The proverb “if the shoe fits” first appeared as “if the cap fits” in a poem by Daniel Defoe in 1705. The expression evolved by the late 18th century and eventually became associated with the glass slipper in the fairy tale, “Cinderella.”
Cinderella is a fairy tale with a happy, predictable ending. This column is a real-world tale and is best described as a work-in-progress by the customer, with real-world values and images that are not pretty. The ending of this story still is being written.
Shoe Production and UV
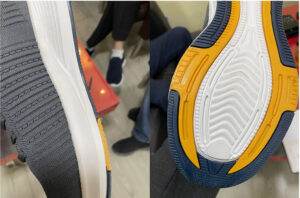
UV is used to produce the soles of shoes, primarily in Brazil, India and Vietnam. The customer produces 120,000 pairs of soles per day, which equals 5.6 million pairs per month and 43 million pairs per year (Images 1 and 2). The soles in this facility are produced on 17 different UV lines.
The customer has maintained a “we have always done it that way” approach. (Refer to the Q2 2024 UV+EB Technology column, “The Seven Dirty Words,” for more information.) The customer has a policy to measure each of its 17 lines once every two hours. Two different radiometers are used, which equates to each radiometer taking over 3,000 measurements per month.
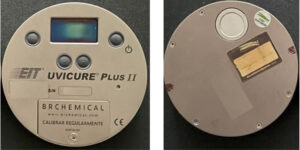
The facility has significant staff turnover, and our guidelines for proper care of our radiometers are not always followed. Units sent for service/calibration often show excessive wear and exposure to heat of both the cases and optics (Images 3-6).
The changes are not just to the appearance of the instrument housing. The optics window, which is like a lens on a camera or cell phone, also has been damaged by the customer through improper cleaning (Images 7-10).
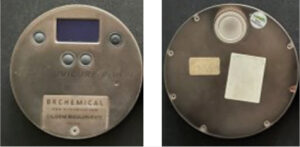
As a result of improper optics cleaning and the types of damage shown in Images 7-10, customer units frequently are received outside of the expected +/- 10% performance tolerance. Units received read up to 55% high due to customer-induced damage to the optics.
Customer data for the EIT UV-A (320-390 nm) band is shown in Table 1 for units both recently calibrated and units approximately 60 days after calibration. The readings on Serial numbers 17593 and 19498 have increased tremendously because of customer abuse.
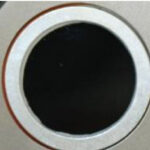
Other hidden issues observed by our authorized service and calibration facility in Brazil include the following:
- Broken battery clips because of the instrument being physically dropped
- Damaged displays because of the unit being used upside down with the numerical display frequently exposed to the UV sources
- Damaged electronics and leaking batteries because of repeated exposures to heat far above the recommended temperature limits of the units
Summary
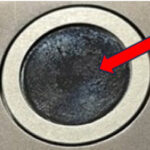
Most of our customers follow proper use, care and cleaning guidelines and experience much better results, with many EIT instruments lasting more than 15 years with regular service. The instrument performance shown in this column is outside of expectations. The root cause is extreme instrument abuse at the customer facility.
EIT 2.0 and BRCHEMICAL have worked to proactively educate the customer by:
- Providing multiple education seminars on how to use, handle, clean and care for the instruments,
-
Image 9: This is an image of a damaged EIT optic window. The customer used a solvent other than isopropyl alcohol (IPA) to clean adhesive off the optic window. The solvent damaged the optic window and created a damaged “ring” on the optics. Offering detailed reports when units are received out of tolerance,
- And asking why the customer feels the need to measure each of its production UV lines every two hours.
The customer does better for periods of time, but frequent staff turnover and lack of a formal training program make consistent performance and a happy fairy-tale ending difficult. Only the customer, with sustained and substantial changes to its internal processes, can change the ending to this tale.
The next time you slip into your shoes, thank UV.
Acknowledgments
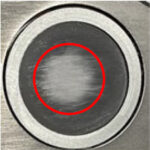
Special thanks to BRCHEMICAL (www.brchemical.com) in Brazil for sharing the images and working to break the “we have always done it that way” mentality of this customer. Images 3-10 are courtesy of BRCHEMICAL Brazil.
Parting Thought
If Cinderella’s shoe fit perfectly, then why did it fall off?
Jim Raymont
Director of Sales
EIT 2.0 LLC
jraymont@eit20.com