Preventive maintenance can be a touchy subject. As suppliers, we know it’s critical. Customers either agree with that premise or, when completely preventable downtime occurs, eventually come to understand its importance.
The idea for this column originated after a conversation with Doctor UV, one of our distributors, about a potential customer. Only one comment (“The lights are on, but nobody is home.”) can be shared in this publication, but the conversation highlights a common problem: Sometimes the customer thinks he or she knows best. In sales, that’s often true… but it’s rarely accurate when it comes to maintenance.
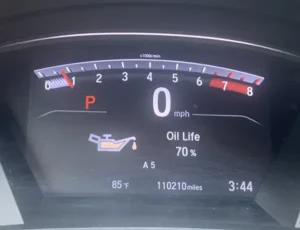
Doctor UV, in addition to selling our UV measurement products for 38 years, also sells a wide variety of UV sources (mercury, LED, spot). The company designs, builds and integrates UV into production lines and has two full-time employees involved in the refurbishment/service of UV sources. The company stocks UV systems and spare parts and also sells related equipment, such as cleaning, surface treatment and inspection products. The company has established relationships with formulators and substrate suppliers in the industry. If Doctor UV cannot provide a solution, the company knows who to call.
The customer mentioned above, although new to UV, refused all our suggestions and combined 75+ years of UV experience.
Suppliers in the UV/EB industry have a vested interest in helping customers succeed. Tom Bodett’s Motel 6 slogan – “We’ll leave the light on for you” – makes a more acceptable title for this column than “The lights are on, but nobody is home.” The Motel 6 slogan also is a great way of saying what the UV industry’s slogan should be: “You’re welcome here, and we want to make sure you’re comfortable.”
Setting a baseline for maintenance
In curing, we want the “light (UV) on,” provided it is the expected/specified-type UV source, intensity/irradiance (W/cm2) and exposure time/energy density (J/cm2). At the same time, we want to address any warning lights or maintenance reminders on the equipment, sources or measurement instruments.
Newer cars have maintenance reminders to suggest when maintenance (oil/filter change, tire rotation, etc.) is needed (Figure 1). Car owners have the option to follow or ignore the reminders based on:
- How do you value your car?
• Do you rely on it to make a living?
• Is breaking down on the side of the road a minor or major thing?
• Do you have a back-up/spare car or buddy to help out?
• If the car breaks down, will you be close to home or far away? - Are you a “fix it yourself” type of person or do you have a trusted mechanic or garage for service? How quickly can they fit you in for repairs? Are parts readily available?
- Are you a cautious driver or do you ‘drive your car like a rental’?
- Do you have the money to pay for the suggested maintenance or will you gamble and pay more for repairs or even a new car later?
Consistently delaying the suggested car maintenance increases the chances of it not working when needed. Long term, ignoring maintenance could impact the car’s value and, ultimately, how long it lasts.
Answer the same questions for your UV system/process:
- How does your business value its UV system(s)?
• Do you rely on the UV system to make a living?
• If the UV system goes down, would the impact be minor or major to your business?
• Do you have a back-up/spare UV system available, another facility with UV or even a competitor that could help?
• If the UV system goes down, will you be late? Upset one customer or lots of customers? - Do you perform your own preventative UV system maintenance or wait until something breaks? Do you have a trusted and reliable company for service? How quickly can that company fit you in for repairs? Are parts readily available?
- How well do you take care of the production equipment? Do you maintain it or abuse it like a rental car?
- Do you have the money to pay for the suggested maintenance or will you gamble and pay more for repairs or even a new UV system later?
Consistently delaying the maintenance on a UV system or radiometer increases the chances of it not working when needed. Long term, ignoring maintenance could impact the value of the UV system/radiometer and, ultimately, how long it lasts.
Assessing instrument performance
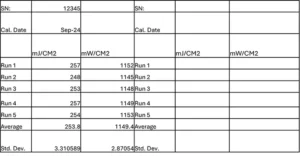
A large part of our job is helping customers “see the invisible light” and understand UV measurement and instrument performance. This requires us to ask questions to understand the situation, so please do not be offended when we ask for the following:
- Serial numbers, instrument settings, source type and your data collection techniques
- Confirmation of the last calibration date and information on who performed the calibration
- At least three runs of data with both Joules and Watts collected in a repeatable consistent manner. Telling us the readings are different or ‘no good’ does not help. In the words of Dr. W. Edwards Deming, “In God we trust, all others bring data” (Figure 2).
Also of interest is whether or not customers have read the instrument manual. This seems like common sense, but sometimes sense is not all that common. For instance, the following interactions are shared below in hopes that readers of this column do not repeat them. Many of these damaged the instrument and voided the warranty.
- The unit was used ‘off-label’ in a manner not supported by the original instrument design. Examples of this include:
- Measurement of a source outside the intended dynamic range of the instrument. We see instruments designed for high-power sources (>100 mW/cm2) used to measure very low-power sources (< 5 mW/cm2).
- Measurement of a source with a different spectral signature than the optical response of the instrument. We often see instruments designed (and scaled) for mercury-based broadband sources used to measure UV LEDs. With one instrument and one LED, it may be possible to get repeatable relative values, but not absolute values. Mix different LEDs, instruments and locations into the equation and it quickly becomes a mess. Establishing a UV source specification or a technical data sheet for a particular formulation with the wrong type of instrument creates a nightmare.
- Using an instrument with electronics designed to measure the output from a ‘continuous’ source on a ‘pulsed’ UV source.
- A complaint was lodged about instrument performance after using it regularly for four years without any service or calibration.
- An instrument was calibrated by a third-party ‘independent’ lab without access to our proprietary procedures, software, tools and components. Sometimes, a ‘correction’ factor is provided which requires additional steps on the production floor. Other times, ‘independent’ labs have damaged the unit by erasing unit firmware when adjusting the unit.
-
Figure 3. Example of radiometer that fell into coating The process window has been set significantly tighter than the listed typical performance of the instrument.
- It is not reasonable to expect +/- 0.25% performance from an instrument that is sold with a typical performance of +/- 5%. Instrument performance does not factor in variations from the process equipment, such as speed controllers, bouncing belts and data-collection techniques.
- The unit has been modified or changed. Examples of this include:
-
Figure 4. The *LB indicates the need to change the radiometer’s replaceable batteries. In-house or third-party repairs to the electronics/optics because of an accidental drop or swan dive into a bucket of ink (Figure 3).
- Replacement of a battery in units designed with a permanent battery
- Accepted solder workmanship standards for electronic components are not followed. (We have seen solder and flux intended for plumbing applications used to make repairs to our printed circuit board. The flux used for electronics soldering is different than the flux used for plumbing.)
-
-
Figure 5. Corrosion on an internal component on a counterfeit unit Warning messages on the instrument are ignored. These include Low Battery (LB), Over Range (OR) and Over Temperature (OT) warnings (Figure 4).
- The unit is a counterfeit unit that may look identical when first purchased (Figure 5). This is happening primarily in China, but some counterfeit units have been exported with equipment lines. Counterfeit units do not have the same performance, values, readings and durability as a genuine unit. Buyer Beware!
UV Source Maintenance
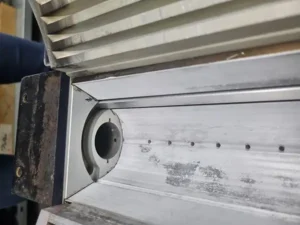
Follow the manufacturers’ recommendations for maintenance on your sources. This includes regular cleaning and replacement of any consumable items, such as reflectors (Figure 6), filters, RF screens and power-supply components. Leave safety shields and guards in place and be sure to follow recommended procedures to lock out equipment if someone is servicing it.
Formulation Storage
Follow the formulators’ recommendations for storage (Figure 7), use and clean-up of UV formulations.
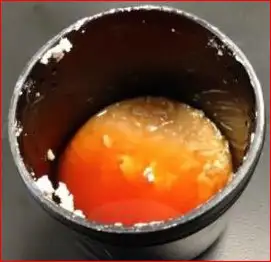
Summary
Use supplier knowledge, experience and guidance to your benefit. Several of our distributors and reps have been involved with UV and UV process control for over 40 years. Use their experience and wisdom to save time, money and frustration. Working together, “We’ll leave the light on for you.”
Parting Shot
Light travels faster than sound. This is why some people appear bright until they speak.
Jim Raymont
Director of Sales
EIT 2.0 LLC
jraymont@eit20.com