By Christopher M. Seubert, PhD, Ford Motor Company
RadTech and Ford Motor Company have teamed up to conduct an extensive study to evaluate the longterm performance of UV-curable clearcoats designed for exterior and interior automotive applications. This study is intended to follow up on a 2003 study that included in-depth chemical and physical analyses on what was, at the time, state-of-the-art UV-curable clearcoats to determine if they performed well enough for exterior automotive applications. Cracking/embrittlement during service proved to be a significant issue and demonstrated the limitation of the tested materials. In this new study, coatings from a range of suppliers will be tested to determine if, over the last 15 years, these cracking issues were resolved, if the coatings otherwise degrade in a similar manner and for what type of automotive application (exterior or interior) these coatings are most suited.
To assess the weathering performance of these coatings, some specialized analytical techniques and metrics will be used to quantify the degradation and compare the performance of clearcoat systems. This article will discuss these techniques in detail and review why such techniques are needed to evaluate the performance of not only these, but all exterior and interior clearcoat systems evaluated by Ford Motor Company.
Background and methodology
In order to achieve >90% customer satisfaction at 10 years in service, an automotive coating must be durable for at least eight years of Florida exposure for vehicles sold in the US and at least five years of Florida exposure for vehicles sold in Europe. This is true for both exterior and interior coatings. Types of coating failures that automotive OEMs are trying to avoid include coating delamination, cracking, blistering, significant color change or loss of gloss. Examples of these types of failures are shown in Figure 1.
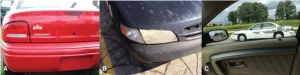
Photooxidation
Weathering failures occur for a variety of reasons, including photooxidation, hydrolysis, additive ineffectiveness, erosion, fracture and adhesion loss. Exposure to sunlight, be it inside or outside the vehicle, can cause chemical composition changes to the coating. When chemical changes become so large that a paint system can no longer cope with mechanical stresses, the paint system fails. To monitor how much a coating changes during weathering, photooxidation is measured using Fourier-transform IR (FTIR) spectroscopy. Transmission FTIR can be used to measure photooxidation within an isolated clearcoat applied to a silicon disc, or photoacoustic FTIR (PAS-FTIR) can be used to measure photooxidation on a sample taken from a coated paint panel.
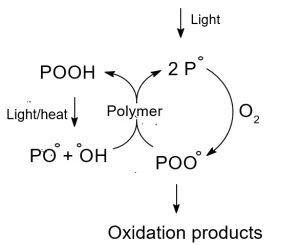
The mechanism of photooxidation is shown in Figure 2, and ideally would be monitored in all layers of the paint system.
Photooxidation is quantified by examining the generic portion of an IR spectrum of the paint layer and measuring the ratio of the (-OH, -NH) area to the (-CH) area, as shown in Figure 3.3 As weathering occurs, the change in this ratio, as shown in Figure 4, gives an indication of how slowly or quickly the coating is chemically degrading. A large change in this ratio could signal that the coating has degraded so significantly that mechanical stresses may lead to a catastrophic failure. How much photooxidation a coating can tolerate before a mechanical failure occurs is
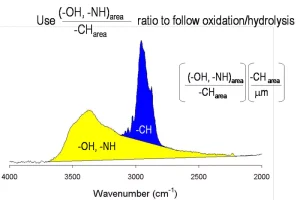
dependent on the specific coating and use case (exterior, interior, etc.).
Fracture energy
While chemical degradation is not the direct cause of mechanical failures within a coating system, it does increase the chances that a mechanical failure will occur. However, once the stress in the coating or at an interface becomes larger than the failure stress, a mechanical failure will result. These stresses arise from mismatches in thermal and moisture expansion coefficients, continued crosslinking of the coatings, and physical aging of the coating below the glass transition temperature (Tg ).
Often it is useful to quantify how susceptible a coating is to mechanical failure, specifically, cracking. One method that can be used to quantify this material property is the fracture energy measurement. By measuring the strain needed to generate cracks within a clearcoated paint panel, and utilizing Equation 1, one can quantify the fracture energy (Gc) of the clearcoat at different stages of the weathering process. The necessary equation and needed material properties are shown below:
In the equation, vf is Poisson’s ratio of the clearcoat, Ef is the modulus of the clearcoat, ɛ0 is the strain to cracking, h is the clearcoat thickness and g(α, β) is a factor related to the modulus mismatch between the clearcoat and the substrate.
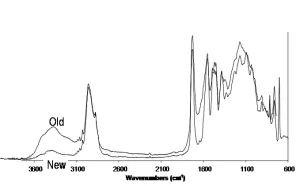
While the absolute value of a coating’s fracture energy is important, where anything below 40 J/m2 would likely crack during typical environmental cycling, the rate at which the fracture energy drops during weathering and/or if the rate of decay starts to slow, or even cease, also is important. This behavior, over time, can be used to predict if the coating will crack in the nearterm or if the chemical changes within the coating have slowed enough to keep the fracture energy above the 40 J/m2 threshold and resist future cracking. These types of tests are of particular importance to UV-curable clearcoats, which have a tendency to embrittle and crack in service due to their high crosslink densities.
Light stabilizers
In addition to measuring chemical and physical changes within the coating system, the presence and loss rate of stabilizers, specifically ultraviolet light absorbers (UVAs) and hindered amine light stabilizers (HALS), are of great importance. The effect of these stabilizers on photooxidation rate and degradation varies among coating systems, so it is important to know how long these additives will provide protection for the base resin. UVA loss rate can be measured using isolated clearcoats and a standard transmission UV/VIS spectrometer3 or through use of a UV microscope.7 HALS are a bit harder to monitor and require the use of an electron spin resonance (ESR) spectrometer, as well as a microtome if depth profiles are desired.8
Accelerated weathering
To monitor the photooxidation, changes in fracture energy and stabilizer loss rate during weathering, a standardized method to weather samples is needed. Natural, outdoor exposure of materials is the most accurate form of weathering. However, to ensure 10-year durability is achieved, one needs to expose the same system that will be used in production for eight to 10 years. Any change to the formulation/material requires the weathering “clock” to be reset.
To reduce the time needed to obtain the necessary exterior durability data, accelerated weathering machines are used. These devices attempt to accurately recreate outdoor weathering conditions. They utilize a high intensity xenon light source and frequent wet/dry cycles to accelerate the weathering process. If the accelerated exposure does not produce the same chemical changes and mechanical stresses that occur during natural weathering, the test’s usefulness is severely limited. Thankfully, significant work has been done to find light filters and environmental cycles that produce accurate degradation and failure modes, all of which were used to create the ASTM D7869 exterior test method.
Materials and coatings designed for use on the interior of a vehicle also are tested using accelerated weathering machines using the Ford Laboratory Test Method BO 116-01 protocol. This test employs cycles similar to those described in the SAE J2412 test protocol but utilizes a glass lantern that surrounds the entire lamp unit to filter out shorter wavelengths of light, similar to the wavelengths filtered out by automotive glazing. This method does employ light and dark cycles, but no water is directly sprayed onto the samples. Materials and coatings must perform over a specified exposure dosage that is dependent on where, within the vehicle, the material or coating will be used in-service.
Materials and samples
For the first part of this study, we talked to a number of material suppliers and requested UV-curable clearcoat formulations that could potentially meet the stringent automotive material specifications for either exterior or interior applications. Eight clearcoat systems were submitted for exterior testing while seven clearcoat systems were submitted for interior testing. Two of the interior formulations were dual-cure systems, while one was a waterborne system. The rest of the submitted systems were monocure. A standard thermoset clearcoat that is commonly used for OEM exterior applications also was obtained and tested. While specific resin chemistry information was not made available, the UV materials are presumed to contain acrylate functional resins and oligomers.
In order to evaluate the rate of photooxidation in each system, a thin layer of clearcoat was applied and cured on an IR transparent silicon disc. Samples for four formulations of each clearcoat system (fully formulated [containing UVA and HALS], UVA only, HALS only and no stabilizers) were made for each submitted system. This is done to determine how each individual stabilizer affects the photooxidation rate of the clearcoat. These samples will be measured using transmission FTIR and will continue to be evaluated as they weather in their respective exterior/interior environments.
Photooxidation also will be measured on samples punched from steel (0.5″ in diameter) primed panels that were coated with each clearcoat system. Again, samples of each of the four formulations were created and measured using PAS-FTIR. This measurement technique allows quantification of the photooxidation state of the top 8 to 12 mm of the clearcoat layer. Again, these samples will continue to be measured to assess the change in photooxidation state as the materials weather.
Primed panels coated with each clearcoat system also were used to assess the fracture energy of each system and formulation. To measure the fracture energy at each exposure time, a full 3×5-inch panel must be destructively measured and analyzed. Due to the large number of panels needed to measure fracture energy of each system and stabilized formulation, only the fully stabilized formulations were measured for each clearcoat system. This allows for a comparison of photooxidation state to brittleness state for the most durable version of each clearcoat system.
To assess the UVA loss rate for each coating system, isolated clearcoats of fully formulated and UVA only formulations were applied to quartz slides and weathered. These samples will be measured using a UV/VIS spectrometer to monitor the absorbance at 340nm over time. If needed, samples taken from the PAS-FTIR punches may be used to track UVA retention using a UV microscope. This study will not include samples to monitor HALS loss rate due to the complexity of the measurement.
Exterior samples will be measured after 750, 1,500, 3,000 and 4,500 hours in the accelerated weathering chamber, which correlates to one, two, four and six years of natural Florida weathering, respectively. Interior samples will be measured after 226 kJ/m2 , 601 kJ/m2 , 977 kJ/m2 , 2406 kJ/m2 and 3609 kJ/m2 , each of which represents threshold exposure values for different locations on the vehicle interior.
Outlook
The analytical techniques discussed here will be used to determine how well current, state-of-the-art UV curable clearcoats perform against automotive OEM coating durability requirements. The results will provide material suppliers much needed data to fine-tune their formulations to create products that can meet the stringent automotive requirements that exist today for both exterior and interior coatings. While some interior UV clearcoats already meet these standards, those that meet the exterior standards are lacking. Preliminary data are being collected on weathered samples, and the results of this work will be presented at a future RadTech conference (likely RadTech 2020) and/or published in a peer-reviewed scientific journal.
References
- Seubert, C. M., Nichols, M. E., Cooper, V. A., & Gerlock, J. L. (2003). The long-term weathering behavior of UV curable clearcoats: I. Bulk chemical and physical analysis. Polymer degradation and stability, 81(1), 103-115.
- Seubert, C. M., Nichols, M. E., & Kucherov, A. V. (2005). Longterm weathering behavior of UV-curable clearcoats: Depth profiling of photooxidation, UVA, and HALS distributions. JCT research, 2(7), 529-538.
- Gerlock, J. L., Smith, C. A., Cooper, V. A., Dusbiber, T. G., & Weber, W. H. (1998). On the use of Fourier transform infrared spectroscopy and ultraviolet spectroscopy to assess the weathering performance of isolated clearcoats from different chemical families. Polymer Degradation and Stability, 62(2), 225-234.
- Gerlock, J.L., Smith, C.A., Nichols, M.E., Tardiff, J.L., Kaberline, S.L., Prater, T.J., Carter, R.O. III, Dusbiber, T.G., Cooper, V.A., and Misovski, T., Proc. 2nd Conference on Service Life Prediction of Organic Coatings, Monterey, CA, ACS, Washington, D.C., November 1999.
- Nichols, M. E., Darr, C. A., Smith, C. A., Thouless, M. D., & Fischer, E. R. (1998). Fracture energy of automotive clearcoats—I. Experimental methods and mechanics. Polymer degradation and stability, 60(2-3), 291-299.
- J.L. Beuth, Int. J. Solids Struct. 29 (1992) 1657.
- Smith, C. A., Gerlock, J. L., & Carter III, R. O. (2001).
Determination of ultraviolet light absorber longevity and distribution in automotive paint systems using ultraviolet micro-spectroscopy.
Polymer degradation and stability, 72(1), 89-97. - Kucherov, A. V., Gerlock, J. L., & Matheson Jr, R. R. (2000).
Determination of active HALS in weathered automotive paint systems: I. Development of ESR based analytical techniques.
Polymer degradation and stability, 69(1), 1-9. - Gerlock, J. L., Kucherov, A. V., & Smith, C. A. (2001).
Determination of active HALS in automotive paint systems II: HALS distribution in weathered clearcoat/basecoat paint systems.
Polymer degradation and stability, 73(2), 201-210. - Misovski, T., Nichols, M. E., & Hardcastle, H. K. (2009). The influence of water on the weathering of automotive paint systems.
In Service Life Prediction of Polymeric Materials (pp. 295-308).
Springer, Boston, MA. - Nichols, M., Misovski, T., Henderson, K., Smith, D., Boisseau, J., Pattison, L., & Quill, J. (2009). Understanding, Optimizing,and Measuring Water in Xenon-Arc Accelerated Weathering for Automotive Exterior Coatings. In 4th European Weathering Symposium: Natural and Artificial Ageing of Polymers,” Publication (No. 11, pp. 189-210).
- Gerlock, J. L., Peters, C. A., Kucherov, A. V., Misovski, T., Seubert, . M., Carter, R. O., & Nichols, M. E. (2003). Testing accelerated weathering tests for appropriate weathering chemistry: ozone filtered xenon arc. Journal of Coatings Technology, 75(936), 35-45.
- Nichols, M., Boisseau, J., Pattison, L., Campbell, D., Quill, J., Zhang, J., … & Misovski, T. (2013). An improved accelerated weathering protocol to anticipate Florida exposure behavior of coatings. Journal of Coatings Technology and Research, 10(2), 153-173.
For nearly 20 years, Christopher M. Seubert has been a research engineer with Ford Motor Company in Dearborn, Michigan. He currently leads research efforts to improve LIDAR reflectivity of automotive coatings and materials to support autonomous vehicle development as well as research to reassess the durability and performance of UV/EB materials used in coatings and 3D-printed parts.