By Liz Stevens, writer, UV+EB Technology
Cypris Materials, Inc., San Leandro, California, is a new RadTech member poised to offer a novel, sustainably oriented alternative to traditional pigments and dyes for matchless coloration in paints, inks and coatings, including UV-curable coatings. In November 2023, Ryan Pearson, CEO and a co-founder of the company, presented “Unlocking the benefits of Structural Color with UV-curable inks and coatings based on novel brush block copolymer technology,” a RadTech webinar on the company’s technology and products. 1 UV+EB Technology talked with Ryan Pearson and Matt Ryan, CTO and a co-founder of the company, to learn more about the nature of the structural color that underpins their patented materials and the status of their endeavor to introduce their unique products to various markets.
A Breakthrough in Precision Polymer Synthesis
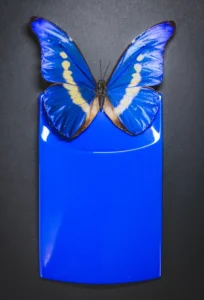
In 2005, the late Robert Grubbs, an American chemist and the Victor and Elizabeth Atkins Professor of Chemistry at the California Institute of Technology (Caltech) in Pasadena, California, was awarded the Nobel Prize in chemistry. Grubbs earned the award for development of the olefin metathesis reaction in organic synthesis, which can be used – among other applications – in precision polymer synthesis via ring opening metathesis polymerization (ROMP). 2 In 2009, Grubbs’s Caltech research group discovered the first rapidly self-assembling brush block copolymer-based photonic crystals, 3 which later would provide the foundation for Cypris Materials’ structural color technology.
Garret Miyake, who performed his post-doctoral studies under Professor Grubbs at Caltech, worked extensively with Grubbs to develop the core science that became the basis for the new technology. When Miyake became an assistant professor at University of Colorado and then later Colorado State University, he was Ph.D. adviser to Ryan Pearson and Matthew Ryan, who earned Ph.D.s there in Polymer Chemistry. And Raymond Weitekamp, a Caltech alum, earned his Ph.D. in Chemistry under Professor Grubbs while developing new materials chemistry and simulating the reflective properties of photonic crystals that would come to benefit the company’s technology.
From 2015 to 2019, those five gentlemen at Caltech and Colorado State were funded (along with researchers at Lawrence Berkeley National Lab) by a Department of Energy Advanced Research Project Agency Energy (ARPA-E) grant to develop paintable reflective coatings for windows. The aim: to reflect near infrared energy and keep buildings cooler in hot weather. As Pearson and Ryan neared graduation in 2019, the quintet – Dr. Raymond Weitekamp, Dr. Ryan Pearson, Dr. Matthew Ryan, Nobel Laureate Prof. Robert Grubbs and Prof. Garret Miyake – focused their attention on structural color coatings, co-founding the company to develop and commercialize aesthetic applications offering a lower environmental footprint.
Traditional Colorants vs. Structural Color
Color abounds in the material world, and almost all of the manmade objects that feature color rely on traditional pigments and dyes. Those colorants, however, are complicated to produce, include harmful precursor ingredients and create toxic byproducts, like polychlorinated biphenyls (PCBs). Production of dyes and pigments also depends upon an enormous supply chain. When the Environmental Protection Agency funded Cypris in 2021 to develop colorant technology without the usual baggage, the company founders asked themselves a transformative question: Why do you need colorants to create color?
They then turned to nature for ideas on a sustainable color alternative and, at the same time, sought to expand the available color gamut for coatings, paints and inks. A close look at the glowing blue seen on the wings of Morpho cypris revealed that the butterfly wings are not actually blue; they are colorless, with tiny scales that use interference to reflect a specific blue wavelength of light. Some bird feathers have similar reflective structural color, as do many butterflies and vibrantly colored beetles. Gemstones, like opal and soap bubble surfaces, also have repeating nano-scale structures that reflect the colors seen in them.
The team tapped into the basics of light interference as an alternative to pigments and dyes which absorb specific wavelengths of light. In mimicking nature, they studied, developed and refined new ways to mix and attain colors – from the entire visible light spectrum. The result: intensely saturated colors and effects that offer beautiful new design choices.
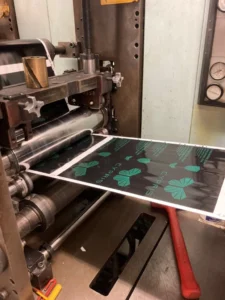
The structural color produced builds on a foundation enabled by Robert Grubbs. “Grubbs’ development of olefin metathesis chemistry in organic synthesis enabled ROMP polymerization,” said CEO Ryan Pearson. “ROMP, in turn, allows for the production of brush block copolymers or comb copolymers with near quantitative grafting density, which eliminates entanglement of the macromonomers. The lack of entanglement enabled by these brush block copolymers allows for self-assembly of our materials in real time.” A key – self-assembly – hinges on minimizing surface energy between two components covalently bound in the same material (i.e. a copolymer). The team designed a brush block copolymer which is more rigid than linear copolymers, keeping the brush bristles from entangling. The copolymers can be made in precise domain sizes to reflect visible light and rapidly self-assemble for industrial use applications.
In these materials, the color that is seen is created from multiple reflections within photonic crystals containing periodic dielectric nanostructures. A nanostructure engineered to a particular wavelength of blue reflects only that blue, per the Bragg equation – nλ = 2d sinΘ. All other wavelengths pass through the nanostructure. By forming Bragg stacks of many paired layers in a lamellar structure, the target wavelength is reflected multiple times – at each interface of layers with different refractive indices – resulting in vivid chromatic intensity. “Our materials are engineered to arrange themselves spontaneously into an ordered structure under the right conditions,” CTO Matt Ryan explained. “In the cross-section of a film or a coating, there might be 50, 70 or 100 repeating copolymer layers contained in one coating application.”
While structural color has been achieved in the past, the company focused on formulating a coating based on polymetric photonic crystals to make structural color more sustainable and accessible to many markets. The company’s photonic crystal material acts as both a binder and colorant, and can be applied via electrostatic and pneumatic spray, and via screen print. One rapidly developing application, direct-to-object digital printing, cannot use traditional structural color due to its associated large particle size. This barrier was overcome with fully soluble copolymers.
Tuning for Color – A Novel Color Process
There is another notable difference between traditional structural color and the company’s approach: only two products are manufactured – a red and a blue, or rather a large and a smaller copolymer – and a unique method for combining those two materials has been created in different ratios to deliver every color in between. “We get what we call wavelength averaging,” Pearson explained. “To my knowledge, there is no other technology that does this. When we combine the large and small copolymers, the weighted average size of the copolymer mixture predicts the reflected color. We have produced a very flexible system that will allow our customers to make any desired hue, without loss in chroma or intensity, from only two materials.”
Matt Ryan elaborated on the novel process. “Wavelength averaging is the term we use to refer to the formulation process of blending together red and blue, for example, to get green,” said Ryan. “It is a new way of thinking about color mixing; the traditional ways are additive and subtractive color mixing.” He explained that the two materials, when combined, form a highly linear relationship. Color formulation is simplified so that tuning for a particular color relies predictably on the ratio of red and blue materials that are mixed. “This really is all about forming the nanostructure, just at different length scales,” Ryan said. “If blue at 400 nm is generated by smaller structures that reflect shorter wavelengths, and red at 700 nm is formed by larger structures that reflect longer wavelengths, then combining blue and red in a 50/50 ratio will produce structures that are formed at a precise intermediate wavelength – 550 nm – reflecting a shade of green.”
Pearson explained that the company has built a flexible color tuning method and has engineered flexibility into who does the tuning, as customers in the printing sector might find the idea of doing their own mixing to be advantageous. “This concept is something that is familiar to press operators, who often pride themselves on being able to color match,” he said. “Mixing our materials is similar but offers greater flexibility than mixing traditional red and blue pigment to make purple. Some customers just want to get a specified color and apply it; we can deliver that. Other customers are more sophisticated and want to mix their own colors; we can deliver that, too.”
Another approach to structural color uses pearlescent pigments, but the pigments can pose problems when used as an ingredient in coatings. Matt Ryan explained: “In comparing the structural color copolymers that we develop to the incumbent pearlescent pigments that are widespread now, pearlescent pigments are composed of discrete particles and their optical effects come from features of those particles.” The company’s material is not particle based; the printed layer is one continuous nanostructure with no particles, yielding a liquid pearl effect with very low scatter. “Low scatter,” said Ryan, “means cleaner flop colors as compared to formulations using pearlescent pigments. And from an application standpoint, pearlescent pigments present a digital printing challenge. Even when ground to a finer size, they quickly block the print nozzle. Our copolymer completely dissolves, removing this limitation.”
Scalability, Compatibility
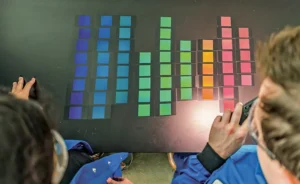
Ryan Pearson described the company’s ability to scale up production for commercial use and the drop-in nature of Cypris materials. “We were focused on scalability as we set out to develop our materials,” he said. “For production, it was important to keep the chemistry simple; all of our polymerization processes are well-established.”
Matt Ryan explained that the company offers a customer-friendly formulation for use under ambient conditions. “We like to call that out,” said Ryan, “because the traditional academic approach to forming polymer-based photonic crystals involves a lot of intense conditions – high temperatures, pressures, highly engineered equipment and long drying times – whereas with our solvent-based system, the copolymer self-assembles as the solvent evaporates. In our UV-curable formulations, self-assembly initiates during mixing and can be cured immediately after application.”
The team also factored in how to roll out new material in the least disruptive way for customers. “We formulated our material to drop into our customers’ existing equipment,” said Pearson. “We do not want our materials to require special equipment or to slow down anyone’s production line speed.” The company initially is gearing toward screen printing and spray applications and will expand the application base rapidly where there is interest.
“There are different ways to deposit our material,” said Matt Ryan. “We have formulations for spray and screen printing now, and we have interest from customers in inkjet since our particle-free technology promises to enable the first jet-able effect colorant.”
A partnership has been entered into with BASF, the European multinational chemical producer, for automotive exterior coating with a product that meets automotive OEM specs for adhesion, windshield bonding, stone chip, humidity and impact resistance. The coating also passes the test for repeatable spray outs and for screen and digital printing.
While working on its solvent-based system, the team learned of market desire for a UV-curable option. This tapped into the company’s quest for sustainability and, in 2022, a UV-curable system was developed. The resin carrier for UV-curable material is more concentrated than the solvent formula, causing the copolymers to begin self-assembly during mixing and show a muted version of the final color. As the material is applied to substrate, final self-organization occurs, revealing the vibrant color. During curing to its final vibrant appearance, a slight color shift occurs as copolymers cross-link and as curing causes some shrinkage of the coating thickness. The company’s photoinitiator package can be adjusted to accommodate all available UV lamps.
On the Horizon
Cypris describes its first-tier target markets as luxury goods and packaging, consumer electronics, automotive and security markings sectors – companies that already are buying its materials for testing and product development. Up next for entry by the company are cosmetics, fast-moving consumer goods packaging, sports equipment, apparel, architectural, and advanced optics and sensing.
Ryan Pearson explained how the company will expand: “We are scaling up production with our manufacturer to reach initial commercial capacity in the first half of 2024. We filed EPA/TSCA regulatory registration documents at the end of 2023 so that we can commercialize in the US market and will follow suit for global markets in 2024.”
In early 2024, the company expects to have production at pilot scale – 100 kg per month of structural color copolymer. The product roadmap calls for commercial UV-curables first, followed by options for solvent-based coatings in 2024 and water-based in 2025. As a next step, the company is ready to engage with formulators and brand owners to begin formulation development and to start line trials for application development.
References
- Ryan Pearson. “Unlocking the benefits of Structural Color with UV curable inks and coatings based on novel brush block copolymer technology.” November 2023. RadTech webinar.
- The Grubbs Group/Research/Polymer Synthesis.
www.grubbsgroup.caltech.edu/index.html@p=19.html - Xia Y, Olsen BD, Kornfield JA, Grubbs RH (2009) Efficient synthesis of narrowly dispersed brush copolymers and study of their assemblies: The importance of side chain arrangement. J Am Chem Soc 131:18525–18532.