By Jose A. Lafuente, technical manager, Phlex Teknologies
Cationic UV LED cured systems are expanding into a broader array of coatings, composites, adhesives and ink applications where traditional thermoset resin systems such as amine-cured epoxy, urethanes, polyesters and vinyl esters have dominated. Radiation cure technologies are expanding rapidly on an industrial scale, as is interest in cationic photopolymerization. The cationic UV LED curing process presents additional benefits, including the absence of air inhibition, a “dark-curing” reaction, low levels of toxicity and irritation, and lower volume shrinkage during photopolymerization.
UV and LED Cure Mechanism
UV curing is a low-temperature, high-speed, solvent-free photochemical process that uses high-intensity ultraviolet (UV) light to change inks, coatings, adhesives or other photoreactive substances through polymerization into an instantly fixed-in-place solid. “Drying,” by contrast, solidifies chemistry through evaporation or by absorption. Ideally, with UV curing, cured substances securely adhere to the substrates onto which they were applied, with adequate depth of cure without being tacky, sticky or flaky.
UV curing systems use a variety of lamps as UV sources. The most common are mercury-based arc lamps which generate broad spectrum UV. Newer technologies are light emitting diodes (LEDs) that emit only UVA energy, and UVC LEDs are an option where power output and efficiency are much lower. Types of UV curing include spot curing, flood curing, hand-held curing and conveyor curing.
Hg Type Lamps vs. LED
Mercury arc (Hg type) lamps have long been the predominant standard in UV curing and are deployed widely as solutions for printing and other industrial manufacturing processes. While they work well, they have their downsides. Most significant is that they create substantial heat and consume a large amount of energy. Hg lamps also produce ozone, which requires exhaust systems to maintain air quality, and mercury-arc bulbs must be disposed of (at a cost). In addition, mercury-arc bulbs are under regulatory scrutiny due to long-term environmental impact.
LED-based UV curing provides all the advantages of traditional UV curing while adding solutions to many of the problems encountered with heat-set drying. These include instantaneous on/off, fast and uniform drying/curing, low heat emission and low power consumption. Additionally, UV LED’s small-form factor makes those lamps ideal for incorporating into processes or machinery with little available space.
Advantages of Cationic Photocured Cycloaliphatic Epoxy
Cycloaliphatic epoxies are a group of highly ring-strained photopolymerizable resins (a typical cycloaliphatic epoxy resin in Image 1). Unlike acrylics that polymerize through the opening of unsaturated double bonds and the use of free radical photointiators; cycloaliphatic epoxies polymerize via ring-opening and etherification reaction induced by cationic photoacid generators. Due to the unique structure of cycloaliphatic epoxy resins, they are particularity suited for rapidly cured, high-strength and highly chemical-resistant coatings.
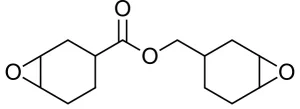
Cure Propagation
When light energy is applied to a cationic system, a strong acid released by the photoinitiator acts as a catalyst and starts the polymerization. This strong acid catalyst can last in a system for days, whereas a free radical lasts only seconds. Also, acid catalysts are not consumed in the reaction whereas free radicals are. The longer lasting acid catalyst allows the reaction to continue to propagate even after the light source is taken away. This is a key difference with UV free radical reactions as they stop as soon as the light source is lost or taken away, and do not continue to propagate.
Cure Speed
Cationic polymerization can be delayed by adding OH functional polyols, which space out the epoxide groups and expands through-cure of the cycloaliphatic epoxy system. Production processes can be regulated by the level of polyol introduced into the system.
Cationic cured cycloaliphatic epoxy systems show appreciable lower levels of shrinkage compared to typical free radical systems. Ether groups are formed during ring opening, thus expanding the molecule and reducing shrinkage during polymerization.
Experimental
PHLEXREZ CER-8000D (hereafter: resin) is 100% solids, UV LED-cured compound based on cycloaliphatic epoxy resin. This resin cures rapidly with lower UV dosages than with many other UV chemistries. It exhibits outstanding adhesion to glass matrices with the proper chemical sizing. The resin exhibits high-temperature physical properties (applications with continuous high strain and application temperatures up to 150° C or higher with certain conditions of use).
High strength and toughness make this material a saturant candidate for glass fiber composites for telecommunication applications. Other typical applications include pultruded rebar, CIPP and Prepreg.
The shelf life in the absence of UV allows catalyzed resin to be heated to temperatures in excess of 70° C for improved speed of fiber wet-out without adverse effects on physical properties or pot life. This thermal stability, coupled with cures which can be achieved in seconds, allow the user to conceive of high-speed production for continuous composites with floor space requirements and capital investment which are less than those required for thermally cured resins.
Properties of the resin in liquid (Table 1) and cured (Table 2) states are shown.
Application Methods
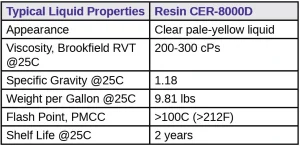
All conventional methods of application can be used to apply the resin. Dip tanks, resin tanks, die application, roll coating or heated spray can be used successfully. The low viscosity allows rapid wet out and saturation. The speed of wet out is dramatically enhanced by heating the resin to as high as 70° C. At 70° C, the resin viscosity is extremely low and wet out can occur in seconds. While there is low volatility on exposure to temperatures as high as 70° C, there is still a small amount of odor. For this reason, good mechanical ventilation is necessary for the extended application of this product at temperatures above 35° C.
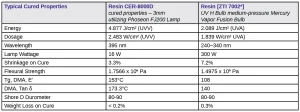
Method of Cure
Cure was achieved with Phoseon FJ200 Lamp 395 nm Energy of 4.877 J/cm² dosage of 2.483 W/cm², measured with an EIT UV Power Puck.
The resin must be exposed to ultraviolet of the proper wavelength to produce cure. This can be done with any number of commercially available LED ultraviolet sources which put out wavelengths of 385 to 405 nanometers 16 watts. The average dose should be 3~5 J/cm² with an intensity of 2.45 W/cm².
Generally, sulfonium or iodonium salts are used for catalysis and photoinitiation.
Activation also can be accomplished with xenon or carbon arc lamps, UV lasers or MPMV lamps. Cured composite thicknesses of 0.250 inches are possible at high speeds of conversion. The resin can be catalyzed to cure by visible light as well as UV. Care must be taken when using this chemistry. Unlike the UV curing catalysts, the visible light curing resins will turn solid under normal ambient lighting conditions.
Conclusion
Cationic-cured cycloacliphatic epoxies are becoming more available and more cost effective. Cationic-cured cycloaliphatic epoxies offer better physical properties than epoxy-acrylate systems, with viscosities that are lower at room temperature. These systems offer a variety of advantages, including continue cure propagation even when the UV source is removed. This means crosslinking continues in shadow areas. Other benefits include excellent chemical and temperature resistance, low shrinkage, reduced odor and tack-free surfaces. UV LED cure offers a number of benefits over medium-pressure mercury vapor lamps. The most significant is the energy – commercial LED lamps are between 16 w to 36 w, Fusion bulbs are 300 w or more. UV LED is in a safer spectrum (385-405 nm) and offers less scatter. Fusion bulbs irradiate UV broadly 200 to 415 nm and need reflectors and cooling units. Another significant advantage of LED over fusion is instant on/off – no need to warm up the bulb. This allows for spot curing, as well as line curing.
Jose A. Lafuente is technical manager for Phlex Teknologies. The company is a unique technology solutions provider to the North American materials sciences sector. Its products are the backbone of many durable goods components, where Phlex Tek’s participation in those segments offer superior performance and novel chemistries. Typical end-use applications include UV/EB cure systems, high-performance composites, coatings, adhesives, elastomers and thermoplastics, plus applications in the energy sector. For more information, email jlafuentes@phlextek.com or visit www.phlextek.com.