By Liz Stevens, writer, UV+EB Technology
When performing automotive collision repair on auto bodies, it is important to perform certain steps during the pre-paint phase of the repair. One of the most important first steps is to apply an epoxy base layer to the metal area under repair to restore its corrosion resistance to OEM specs and to promote adhesion of subsequent layers of material. That critical first step, however, takes precious time, especially when performed with conventional curing methods such as infrared curing. Properly applying and curing the epoxy coat prevents the formation of destructive rust. Proper application and curing of subsequent layers of fillers and primers eliminates the latent shrinkage of filler material that will ultimately be covered with paint and a clear topcoat.
It is not surprising, but it is shortsighted, for collision repair centers to skip a step or two, call a not-quite-smooth layer “good enough” or rush the job overall. Those shortcuts often come back to bite the repair center owner when unhappy customers return with repairs that require costly re-dos as the consequence of poorly done repair jobs.
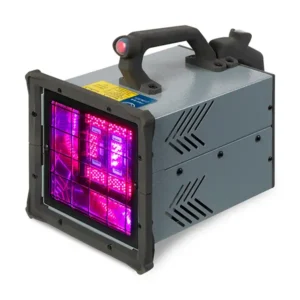
George Smith is inventor/technical specialist at SOCUR Inc., Highland, Utah, his family-owned company that provides UV-curable undercoat materials and UV LED AreaCure (Image 1) lights for auto collision repair. He shared perspectives on the evolution of his products, and how the availability of advanced coatings and UV LED lights has given repair centers the materials and tools to do the job right, the first time, while also slashing repair times.
Can you elaborate on the importance of the epoxy restoration step in auto body repair?
Most collision repair facilities take damaged aluminum or steel panels and do their best to pull the damage. In this metal manipulating process, damage to the layers of coatings is inevitable. And when coatings are removed to weld, grind and shape the metal, the electrophoretically deposited epoxy is removed along with the entire topcoat. Automotive manufacturers require the restoration of the epoxy – an anti-corrosion coating – prior to the application of body filler, however it rarely happens because of the long drying and curing times of conventional epoxies. It takes 12 hours for epoxy to dry and can take two weeks for it to fully cure. Repair shops could use infrared lamps to speed up the drying time, but they hardly ever do.
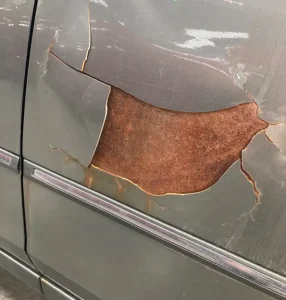
When restoration of the epoxy layer is skipped, which happens frequently, the collision shop gets paid for something that it did not do – namely, provide anti-corrosion treatment. Technically, this is insurance fraud as the vehicle was not repaired to OEM standards. Additionally, the alloys that have been used in the automotive industry for the last 25 to 30 years do not play well with the polyester body fillers of older repair processes. Body filler, for example, that is applied to bare excelite steel will not adhere properly; blistering and/or peeling will almost always occur. Since the collision center is responsible for any structural or cosmetic damage at the repair site for the remaining life of the auto, skipping the epoxy layer step can lead to costly re-dos when a customer returns to the shop, for instance, with the repaired area rusted through (Image 2).
When did you learn about using UV LED light for curing the epoxy layer and other pre-paint fillers/primers?
I’ve been dabbling in UV-cure products for a long time now in automotive refinish, mostly with BASF products. I saw that the conventional large mercury UV lights on stands rarely are used because it is not easy to move them or to use them. Those large light stands end up becoming coat hangers in the repair shop because people refuse to roll them around the shop and wrestle them over the extension cords and air hoses which litter a collision center. While some of the handheld mercury arc lights work well, they generate intense heat and give off UVB/UVC emissions. Also, their warmup time is five minutes for each use and their inherent workplace safety risks are a major turnoff for most owners/managers.
With all of that in mind, I always was looking for a UV LED option. When LEDs became affordable, safer and “instant on,” we developed our own UV-curable coatings and specialty UV LED products. The high intensity of the LED units can instantly cure products properly designed in seconds, without the heat, danger, energy draw and warm-up time of traditional lamps. It is wild how long five minutes seem to last when you’re standing there watching an old UV light warm up, which no one has the patience to do.
What wavelength is used in your UV LED lights, and what is the curing depth?
The wavelength is 365 nm. The curing depth is product-dependent. All of our epoxies, body fillers and primers are engineered to do a specific job. Body filler will cure to about 35 mils, while primer surfacer will only cure to 5 to 6 mils per coat. What most people don’t understand is that these products have incredible inter-coat adhesion, so the film build per coat is not the limitation per repair. For example, if the body filler total depth is 80 mils, we can do that repair in three easy swipes of 27 mils each and quickly cure each layer.
How do these products reduce repair time?
Our products offer repair centers the ability to apply an epoxy primer, cure it and then apply body filler straight to the repair area without sanding. Our other pre-paint coatings can be applied without sanding the prior layer and they cure very rapidly thanks to UV LED technology. Taken together, this practice creates a better repair and also will cycle the car through the repair process faster, thereby increasing gross sales without increasing labor costs or requiring additional square footage for the repair facility. We are successful because we add value by providing a smooth, flawless repair that doesn’t develop rust, blistering, peeling or sand scratch swelling. All of that means faster turnaround, less re-work and more profit for the repair center.
SOCUR offers a full line of UV-curable undercoats such as epoxy, body fillers, primers and specialty products, along with a trio of AreaCure UV LED lights – AreaCure 850 (850 mW, 110V AC), AreaCure 500 (500 mW, powered by rechargeable DeWalt batteries) and MiniCure (AAA batteries). For more information, visit www.socurinc.com.