The Late Night (NBC: 1982-1993) and Late Show (CBS: 1993-2015) with David Letterman aired on two different television networks for over 6,000 episodes. (Note to my editor: This is my 20th column, and I will not reach 6,000). Letterman’s shows had two signature segments: The “Top 10 List,” which aired most nights and “Stupid Pet/Human Tricks,” which aired periodically. In this quarter’s column, I have combined Letterman’s two signature segments to create “Jim’s Top 10 Stupid UV Tricks List.”
Live from the EIT 2.0 Home Office in Leesburg, Virginia…
10. Failure to Learn
I have the privilege of interacting with a wide variety of extremely intelligent suppliers and end users who are working on new, unique and creative UV applications. More than occasionally, I come across a situation that requires me to review the basics of UV curing. The educational aspect of my job comes with the territory and most UV suppliers embrace it, especially with someone new to the UV industry.
Unfortunately, I frequently find companies or people that jump into the UV industry unprepared. Use industry resources like this publication, suppliers, supplier websites, blogs and trade associations/shows like RadTech to start, enhance or continue your learning.
9. Penny Wise: Dollar Foolish
Watching pennies can lead to the loss of dollars if you are not careful. Purchasing teams often receive compensation based on their ability to lower the cost of purchased materials. In some cases, this can save the company money. In other cases, the purchasing team does not understand the importance of an item to your process and their decisions can wind up costing more.
Replacement components such as bulbs, reflectors and quartz plates need to be thoroughly evaluated. Do you get the same number of useful hours? Same spectral output? If a quartz plate, is it the same quality with the same transmission characteristics after 1,000 or 2,000 hours?
Does a less costly LED array have the needed irradiance (W/cm2), energy density (J/cm2), spectral distribution, uniformity, and lifetime? EIT instruments have been counterfeited in Asia. The counterfeit units do not perform as a genuine EIT unit.
8. “Not All Those Who Wander Are Lost”
This saying from J. R. R. Tolkien (“The Riddle of Strider” from The Fellowship of the Ring) makes an interesting travel philosophy, although I prefer the Beach Boys’ “Get there fast and take it slow” philosophy from the song, “Kokomo.” Apply “wandering” to travel but not your UV process. Establish a process window and document the conditions that produce acceptable products. I have seen many companies wander around aimlessly, lost when it comes to having a documented UV process.
7. “Ch-ch-changes”
David Bowie famously sang this in his song, “Changes.” When customers call because they are not getting “expected” readings, we ask them to check and confirm that their physical settings have not changed since the previous measurement. The checklist of changes includes:
- Applied Power Setting: Did the power level go up or down? Confirm with the manufacturer if the UV source will have the same spectral output at 25 or 50% as it does at 100%.
- Exposure Time: Was data collected at a different process speed (feet or meters/minute) or exposure time?
- Source Height: Did the height of the source change in relationship to the measurement point?
Also see numbers five, four and two in the list below for other things that might have changed.
6. Equipment Selection
Matching the UV source to the application and formulation is much easier than trying to force your process to work with equipment that you had available or is not suited for the application. Do the sources in your R&D lab approximate what is available on your production line? If you have a mercury-based source, do you have a similar source and bulb type in both R&D and the planned production location? If you have an LED, does the spectral output (wavelength, irradiance and energy density) match between arrays in R&D and production?
5. Equipment Maintenance
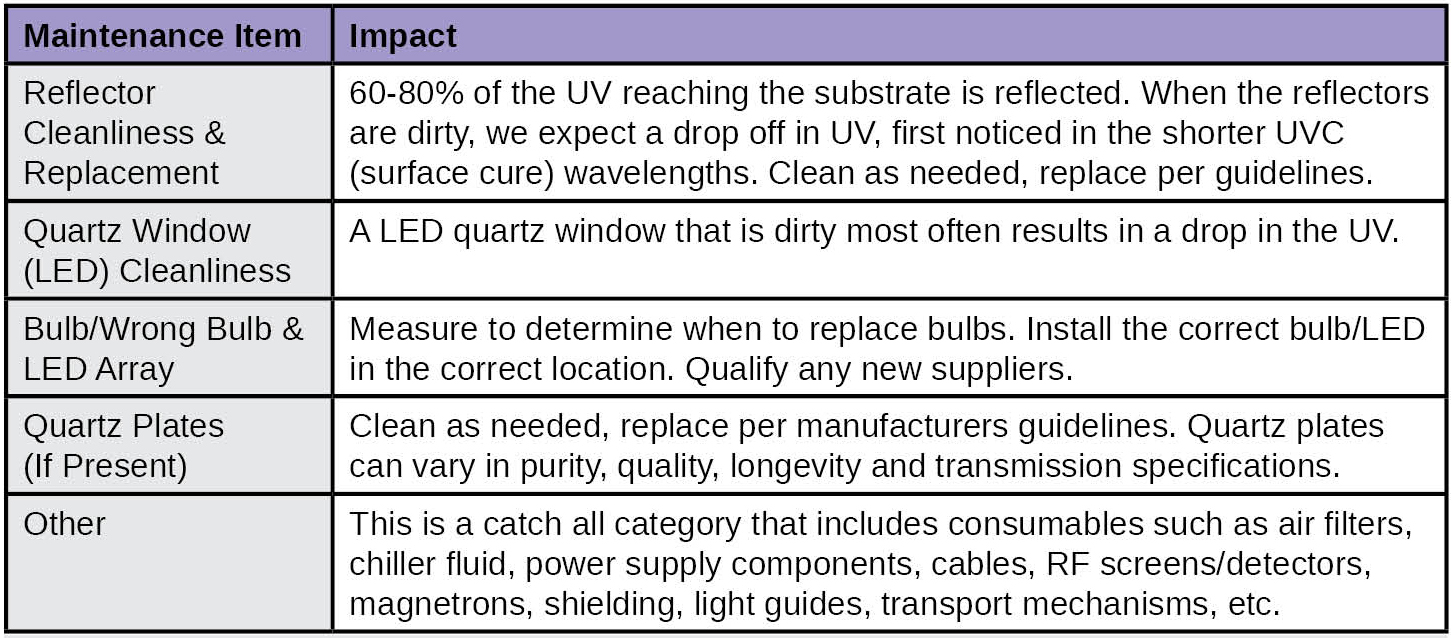
UV sources require maintenance to perform best. Work with your equipment suppliers to establish both a preventative and planned maintenance schedule. Look over Table 1 and decide what is important for your sources and the needed maintenance frequency.
4. Instrument Selection and Maintenance
Imagine the two scenarios below:
- In the first scenario, the end user elects not to measure their UV and takes a chance that the process works. This user is willing to accept the risks and potential costs (money, time, liability) with the production of poor-quality products.
-
Table 2. In the second scenario, the end user has an instrument that is mismatched to the process and may not have the optimal optical response or dynamic range. The user-adjustable settings, including sample rate, may be set wrong. Has the instrument been maintained, serviced or cleaned following the manufacturers’ recommendations? This user has a false sense of security and may have more issues than the user in the first scenario. The instrument provides a ‘number’ that may or may not reflect the actual UV conditions. Communication (see number 1) could be compromised. Using an instrument not optimized for the UV source can result in misleading values. In Table 2, a broadband instrument with EIT UV-A and UV-V was used to measure a 395 nm LED. An instrument with a response (L-395) also was used to measure the LED. The values as measured by the L-395 band are more representative of the true values.
3. “Useless but Important Information”
Jimmy Buffett and Mac McAnally wrote a song with this title. Enjoy and listen to it but do not follow it when it comes to your UV data. We consider all information from our radiometers to be useful and important. Record, document and organize it. While some customers are content to collect only Joule values, we want to have as much information as possible available when helping customers to understand their UV systems. We want to see both the Joule and the Watt values. We also ask for three sets of consistently (see number 2) collected data when trying to understand a customer issue. The three sets of data allow us to identify source/conveyor stability as well as instrument performance.
Multi-band (UV-A, UV-B, UV-C, UV-V) instruments for broadband (mercury) sources provide more information than an instrument with a single-band (narrow or wide) response. By looking at the ratio of the UV bands in a multi-band radiometer, the user can identify:
- The source type (mercury, mercury-iron, mercury-gallium).
- Aging in the source. A mercury-gallium arc lamp eventually will age and look more like a mercury source. Is that after 750, 1,000, 1,500 or 2,000 hours?
- When your UV reflectors need maintenance. Track the ratio of UV-A:UV-C. If the UV-A values are okay and holding steady and the UV-C drops, it is time to clean your reflectors.
If your radiometer can generate an irradiance profile (Watts/cm2 as a function of time), we review that file to identify the system focus conditions. By comparing files collected at different times, we can quickly see changes to the speed, power levels, bulb types and focus. This is especially important on lines with multiple sources.
Confirming or documenting ‘other’ variables in your process often goes a long way to solving issues.
2. Data Collection Techniques
Number two on my Top 10 List is Data Collection Techniques. Getting consistent data requires consistent data collection techniques by all people collecting the data. As a reminder:
- Let your source warm up and stabilize.
- Decide the settings on your UV source and process equipment.
- Turn off or avoid application/dispensing stations and thermal/IR ovens.
- Decide instrument settings, including the sample rate.
- Establish the measurement locations and orientation of the unit so the optics are in the same location each time.
- Check to make sure the instrument optics are clean.
- Carefully record the data after the readings.
1. “What We’ve Got Here is a Failure to Communicate”
This line, from the movie Cool Hand Luke, is number one on my list of “Top Ten Stupid UV Tricks.”
Failure to communicate often leads to either a breakdown in the UV process or running at less than optimal conditions. Communication needs to happen:
- Within a company facility between R&D, production, adjacent manufacturing lines, different shifts, purchasing and your maintenance teams.
- Between company facilities in different locations. Include everyone listed above and pay special attention if the process is going from an R&D pilot line in one location to a production line in another location.
- Be sure to understand any language differences between locations and communicate (document) what you need.
- What happens if the pilot and production lines are different?
- Within your supply chain, which can include any or all of the following:
- Formulators
- Substrate suppliers
- UV equipment suppliers
- Machine integrators/builders
- Measurement companies
- End users
Parting Thought:
From a bumper sticker: “I have managed to successfully weigh a rainbow. It turns out it was pretty light.” Happy Holidays.
Jim Raymont
Director of Sales
EIT 2.0 LLC
jraymont@eit20.com