With the announcement of Steel Dynamics’ TruSteel HD™ in September of 2022 1-3 and ArcelorMittal and Beckers’ collaboration in February of 2023, 4-6 the combination of UV-/EB-curable technology and coil coating has been receiving some long-overdue attention. Metal coil coating is a classic example of a conventional solvent-borne, energy-intensive, thermal process that, when converted to a UV/EB process, results in significant VOC reduction and energy savings. 7,8 Yet, these relatively recent converts are not the first to see the value of implementing a UV/EB production line – that distinction goes to Cleveland Steel Container (CSC), which, back in 2014, was the first company in the world to commercially produce coated coil using both UV and EB technologies. 9 To celebrate 10 years of production, let’s take a look at what drove CSC’s decision, the benefits and challenges of switching to UV/EB, and what the future might hold for UV/EB coil coating.
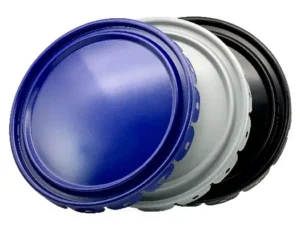
Cleveland Steel Container, one of the largest steel pail manufacturers in the US, was founded in 1963 and has been roll-coating material for steel pails since 1964. In 2012, CSC wanted to improve the production efficiency of the coated steel that was stamped into covers (Figure 1) and bottoms for pails by switching from a sheet-fed process to a roll-to-roll coil process. The steel sheets needed an opaque, colored coating on the outside and a clear coating on the inside. With the sheet-fed process, speeds were limited to 60 to 100 ft/min (18 to 30 m/min) and only one side of the steel could be coated at a time. With a coil-fed line, faster speeds and double-sided coating would be possible. The problem? A traditional thermal-cure coil coating line would not fit in the company’s facility, and it would require additional oxidizer capacity (for VOC capture). These restrictions inspired CSC to investigate UV/EB technology as an alternative possibility, and CSC placed an order later that year for an electron beam and a UV system.
The radiation-curable line was commissioned in early 2014 and features flame treatment to clean the coil; a dual coater; a UV station to cure the clear, inside coating; and an EB to cure the opaque, colored coating that becomes the outside of the pail lid or bottom (Figure 2). The compact line is approximately 100-ft long (30 m) and is estimated to be half the length of a comparable thermal line. The small footprint is due in large part to the instantaneous nature (ms to s) of the polymerization of both EB and UV coatings. Thermal coatings have a dwell time that must be met, either by increasing the oven length or by decreasing the line speed. The combination of UV and EB also saves space. EB requires radiation shielding that would make dual coating with two EBs challenging; 10 by curing one side with UV first, the coil can be articulated easily through the necessary angle changes that make up the beam’s material path. EB was chosen to cure the exterior coating because its colorblindness provided more freedom and less reformulation when curing different colors. 11 Moreover, both UV- and EB-curable coatings are solvent-free, which fulfilled CSC’s objective of preventing added oxidizer investment.
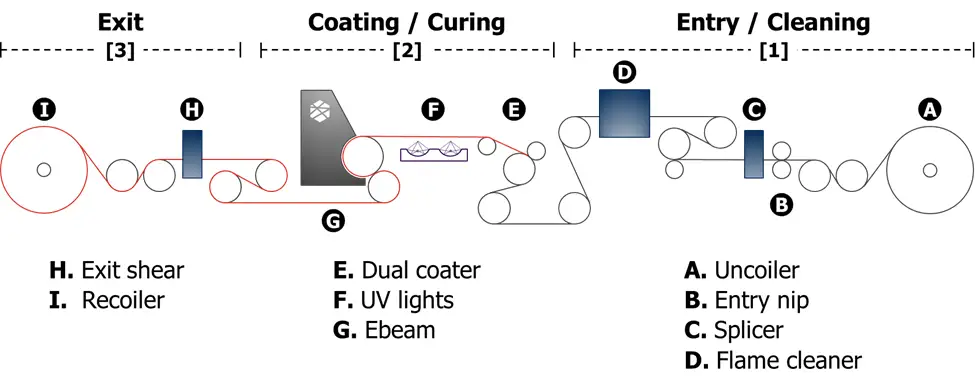
The new line allowed CSC to increase its line speed to 220 ft/min (67 m/min) and condense production into three to four days a week. According to Will Parish, director of Regulatory Affairs for CSC, “The drastic improvement to internal efficiencies (i.e., making more product with less manufacturing effort) has been calculated and is the bulk of the savings we see. The coil coating operation feeds a coil-fed press, which is much faster than the older traditional (sheet-fed) method. The new operation is estimated to be four to six times more efficient than the traditional method. This has reduced overtime and increased production capabilities across the board as resources are easier to plan for customer needs.”
The sustainability benefits of UV/EB technology also compliment CSC’s commitment to sustainability (steel is 100% recyclable!) and contributed to the company’s 2022 EcoVadis Silver sustainability rating. 12 The switch from the conventional, low-solids (~40% solids), thermal-cure coatings to solvent-free UV/EB (100% solids) coatings has eliminated ~700 tons of VOC emissions, equivalent to ~2,000 tons CO2, over the last 10 years. In other words, that is the elimination of 3,500 55-gallon drums of solvent, or the equivalent of removing 40 cars from the road per year for the last 10 years. “Additionally,” said Parish, “the energy requirements [for operating UV/EB] are much lower than heating a natural gas oven to >350° F (177° C) to cure traditional coatings, and the line has much lower regulatory burdens with the state and federal EPA. The reduction in VOCs and the resultant byproducts of combustion have improved our carbon footprint.” CSC has not determined the energy savings for its line compared to a conventional thermal line, but others have estimated that using UV/EB technology could result in an energy savings of up to 98%. 7
While CSC successfully has implemented UV/EB technology in its production, that is not to say the technology doesn’t come with a few challenges. There was an initial learning curve. The tricks that worked with solvent-borne coatings don’t always translate to 100% solids coatings; roll pressures might have to be adjusted or coatings heated to compensate for the increase in viscosity. Maintenance on a UV lamp or an EB is not the same as an oven, and indicators of machine health – effective irradiance measurements or vacuum pressures – are not the same either. Another challenge has been gaining the interest of coating suppliers. A decade ago, only Watson Standard (now acquired by Sherwin Williams) would work with CSC to develop UV/EB coatings to suit the company’s needs. Competition breeds innovation and drives lower prices; without it, it is more difficult to make progress in these areas.
Looking toward the future, UV/EB technology holds much potential for the metal coil industry. In the last couple of years, Sherwin Williams, PPG, Beckers and, most recently, AkzoNobel all announced their support of UV-/EB-curable coatings for industrial metal coil. 13,14 CSC continues its legacy of innovation in coil coating as a great ambassador of UV/EB technology (providing an end-user perspective) and by allowing access to its line to prospective new users of UV/EB for trials, both of which have been instrumental for the expansion of the technology in coil. SDI and ArcelorMittal are beginning to produce UV/EB coated coils for outdoor building and construction applications – a sector that makes up a significant portion of the global coil coating market. With existing infrastructure and proven paint technologies with 40-year warranties, the coil coating industry won’t make the switch overnight, but as the pressure to reduce carbon emissions increases, UV/EB technology is the green alternative building momentum. Thanks, Cleveland Steel Container, for getting us rolling!
References
- Thatcher, S., Steel Dynamics debuts new digitally printed steel that fools the eye. Rollforming Magazine. May 24, 2023. https://rollformingmagazine.com/steel-dynamics-debuts-new-digitally-printed-steel-that-fools-the-eye/
- Clark, A., How Have Tru-Steel HD Digital Prints Impacted the Metal Coating Industry? February, 29, 2024. https://www.truemetalsupply.com/post/tru-steel-hd-digital-prints-impact-on-the-metal-coating-industry
- TruSteel HD from Steel Dynamics. November 16, 2022. https://www.youtube.com/watch?v=i19whCDEr_E
- ArcelorMittal Pioneering Greener Technology for Paint Curing. February 23, 2023. https://construction-osterreich.arcelormittal.com/en/news-details/arcelormittal-pioneering-greener-technology-for-paint-curing
- Beckman, L., Companies Partner to Develop Sustainable Coil Coatings. Products Finishing. January 23, 2024. https://www.pfonline.com/news/companies-partner-to-develop-sustainable-coil-coatings
- Discovering Electron Beam at ArcelorMittal Construction Contrisson. October 2, 2023. https://www.youtube.com/watch?v=6pnAY_qjdvU
- Bonner, M., Bommarito, C., UV/EB Technology as a Sustainable Solution to the Energy Crisis. Paint & Coatings Industry. August 2, 2023. https://www.pcimag.com/articles/111643-uv-eb-technology-as-a-sustainable-solution-to-the-energy-crisis
- Golden, R., What’s the Score? A Method for Quantitative Estimation of Energy Use and Emission Reductions for UV/EB Curing. RadTech Report (3), 2012.
- RadTech Announces 2016 Emerging Technology Award Winners. Ink World. May 12, 2016. https://www.inkworldmagazine.com/contents/view_live-from-shows/2016-05-12/radtech-announces-2016-emerging-technology-award-winners/
- Schissel, S., Radiation Safety for Electron Beams. UV+EB Technology (3), 2021.
- Schissel, S., Colorblind EB. UV+EB Technology (1), 2024.
- https://www.cscpails.com/capabilities/sustainability/
- Swanson, K., Parish, W., The Future of Metal: Electron Beam for Coil Coating. National Coil Coaters Association, Fall Technical Meeting, September 2022.
- AkzoNobel and China’s Wuxi El Pont Explore the Use of Electron Beams. Paint & Coatings Industry. December 11, 2023.
Sage Schissel, Ph.D.
Applications Specialist
PCT Ebeam and Integration LLC
sage.schissel@pctebi.com