By Carla Brown, Manager, Corporate Communications – Circular Economy Specialist, Siegwerk Druckfarben AG & Co.
A note from RadTech:
The RadTech Sustainability Committee is embarking on our group’s sustainability journey, and we thank Carla Brown, manager, Corporate Communications – Circular Economy Specialist, Siegwerk Druckfarben AG & Co., for sharing her work in a series of modules UV+EB Technology will publish throughout the year. This is the third installment.
What kind of UV inks should a printer use when printing food packaging?
Why can’t a printer just use standard UV inks?
How can a printer ensure compliance?
These are a few of the questions that will be addressed in this module.
Inks are an essential component of any packaging. When it comes to food packaging, however, they play a particularly important role. Usually, the non-food surface of food packaging is printed for product presentation and to provide information, such as food ingredients and nutrition facts, to the final consumer. However, the fact that the ink on the printed outer surface does not get in direct contact with the foodstuff inside the packaging does not mean that the ink cannot have an impact on the foodstuff. The primary concern is the migration of substances within the inks into the food. This can cause a range of issues, from introducing potentially harmful chemicals into the food to altering the taste or scent of the food.
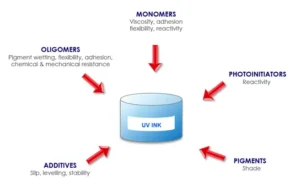
Printers want UV inks that allow the press to run at high speed. UV inks that have excellent adhesion are shrinkable for sleeve applications. Usually, this performance profile is achieved using small, highly reactive components: Monomers, oligomers and photoinitiators (Figure 1).
However, this performance profile comes with a problem when talking about food packaging: The small, reactive components can migrate!
To overcome this problem, low-migration UV ink solutions have been developed. The term ‘low migration’ indicates that the respective raw materials were selected in a way that the printed ink film has less migration potential and the resulting food packaging is able to meet the migration limits, provided that the substrates have sufficient barrier properties and the ink is processed by the converter in a proper way to ensure optimal curing. If the curing is not optimal, there might be an increased migration potential due to the presence of residual uncured photoinitiators. Another source for potential migrants also can be breakdown products of photoinitiators resulting from the curing process.
For selecting the suitable raw materials, a profound knowledge about the underlying characteristics is essential. These include, but are not limited to, the chemistry, compositional information down to trace amounts, toxicological properties and legal evaluation. In any case, the converter should be informed about the potential migrants of the respective inks system in order to perform its own evaluation of the resulting packaging to meet the legal requirements. The ideal instrument to convey this information is in the form of a Statement of Composition (SoC), which contains all relevant information to fulfill this task in an efficient manner.
Can a printer just use a low-migration ink and be compliant?
No. A low-migration system is a prerequisite, but if the printer does not control the process and application of a low-migration system, there may be migration. Just imagine if the film is not fully cured. Set-off of ink components to an upper layer certainly will happen. It is the responsibility of the printer and, ultimately, of the party that brings the product on the market that the entire packaging meets the criteria of low migration.
Note: There may be significant discrepancies between the compositions of low-migration ink systems available on the market. Knowing that one system renders compliant packaging does not necessarily mean that a different low-migration system for the same application also is compliant. Migration needs to be checked first when changing a system.
Is low odor identical to low migration?
Some companies offer low-odor inks. These inks can be low-migration inks, but generally are not. Some components of the standard inks have been replaced by low-smelling components. This usually goes hand in hand with lower migration. However, to meet the migration limits of regulations like Swiss Ordinance, these inks are not necessarily suitable.
How are packaging inks created to ensure food safety?
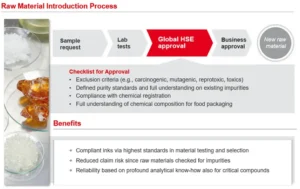
In order to mitigate risk, hazardous chemical substances (such as specific heavy metals, chlorinated hydrocarbons or dioxins) must be excluded, no matter the application. The same holds true for any carcinogenic, mutagen and reprotoxic (CMR) substances. Further, printing inks are manufactured in compliance with various legislations, such as Framework Regulation (EC) No 1935/2004, Plastics Regulation (EU) No 10/2011, Swiss Ordinance 817.023.21 and also voluntary commitments to EuPIA to implement exclusion policy, photoinitiator suitability list, etc., in order to produce the safe and sustainable printing inks (Figure 2).
To ensure food packaging safety, the chemical composition of all raw materials should be known down to trace levels, along with all non-intentionally added substances (NIAS). NIAS are chemical compounds that, in contrast to IAS (intentionally added substances), are present in a material but which have not been added intentionally within the production process. They can be byproducts or impurities of starting substances, for example.
It is the task of the converter to assess all potential risks for the food packaging being printed. As such, it is vital to the converter’s compliance work to know the potential migrants of all relevant packaging components that are being combined – substrates, adhesives, printing inks, overprint lacquers, primers, etc. – including their quantity and regulatory status, migration limits, etc. This information is contained in the Statement of Composition (SoC), as mentioned above.
UV LED – A Good Choice for Printing of Food Packaging
The demand for more environmentally friendly curing has been increasing in recent years, leading to an uptick in UV LED ink use. Interestingly, UV LED lamps do not only consume less energy, but also have a constant output that is an advantage for a controlled printing environment that is needed for printing of food packaging. Low-migration UV LED inks are available on the market, and more and more printers decide for the combination of low migration and LED.