By Michael Kelly, Allied PhotoChemical, Inc., and Michael Bonner, Saint Clair Systems
In this article, we provide a guide comparing the cost of solvent-based and water-based coatings to UV coatings, using a real-life customer example.
The customer is running a return-on-investment analysis of coating costs for a pipe production operation. The goal is to reduce the part cost.
Current operation:
Steel pipe
9.625″ diameter
45′ long
1.0 mils dry film thickness (DFT)
Application needs:
Enhanced corrosion resistance
Reduced part cost
Current production:
2,760 pieces per day
938,400 pieces per year
Case example:
300,000 pieces ROI analysis
Wet film thickness and dry film thickness
Figure 1 illustrates the difference between an 18% solids solvent-based coating, a 27% solids water-based coating and a 100% solids UV coating.
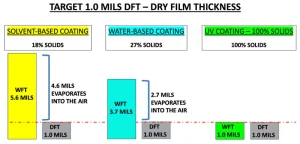
For solvent-based coating at 18% solids, the user needs to spray 5.6 mils WFT to get 1.0 mils DFT.
(Math: 0.18 x 5.6 mils WFT = 1.00 mils DFT)
For water-based coating at 27% solids, the user needs to spray 3.7 mils WFT to get 1.0 mils DFT.
(Math: 0.27 x 3.7 mils WFT = 1.00 mils DFT)
For UV coating with 100% solids, the user needs to spray 1.0 mils WFT to get 1.0 mils DFT.
(Math: 1.00 x 1.00 mils WFT = 1.00 mils DFT)*
*Note: At 1.0 mil, shrinkage in the film is considered negligible.
Coating costs per gallon
The customer currently uses a solvent-based coating system and would like to transition to either water-based or UV coating. The basic question: Which coating costs less?
Solvent-based coating
18% solids
$11.71 per gallon
Water-based coating
27% solids
$15.13 per gallon
UV coating
100% solids
$51.24 per gallon
In reality, cost can be viewed two ways. At first glance, at $11.71 per gallon, the solvent-based coating appears lower in price than the water-based coating, at $15.13 per gallon, or the UV coating, at $51.24 per gallon. While that may be how coatings are purchased, it is certainly not how they are used. Coating in a gallon pail is not the same as coating on a product.
Applied cost per square foot
What the user is really concerned with is how much product can be covered for the lowest possible cost. So it’s important to consider how much product can be covered with each gallon.
First, there is 1,604 sq. ft. at 1 mil thick, in a US gallon of any liquid. Second, consider the percent solids of solvent, water and UV coatings. The solvent-based coating is 18% solids, so effective coverage can be calculated as: 18% x 1,604 square feet x 1.0 mils = 288.7 sq. ft. Cost per sq. ft. is: $11.71/288.7 sq. ft. = $0.0406/sq. ft.
The water-based coating is 27% solids. Using the same approach, the effective coverage can be calculated as follows: 27% x 1,604 sq. ft. x 1.0 mils of film build = 433.1 sq. ft. The cost per sq. ft. is: $15.13/433.1 sq. ft. = $0.0349/sq. ft.
The UV coating, however, is 100% solids. Therefore, its effective coverage will be: 100% x 1,604 sq. ft. x 1 mils = 1,604 sq. ft. The cost per sq. ft. is: $51.24/1,604 sq. ft. = $0.0319/sq. ft.
Therefore, the lowest coverage cost is represented by the UV coating, despite the fact that it has the highest cost per gallon.
So how does this information affect our customer’s application? Does the UV coating really enable the customer to produce at the lowest part cost? To review, the customer is coating steel pipe with the following physical characteristics:
Functional pipe coating model – Linear foot calculation
The measurement centers around linear feet of pipe. Table 1 details the actual linear foot of pipe per gallon of coating for each of the three formulations.
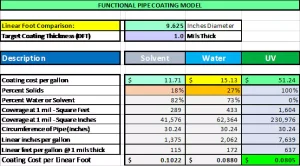
Pieces of 45-foot pipe per gallon
While coverage in feet per gallon is important, in particular, the customer needs to know how many 45-foot lengths can be produced per gallon of coating. Based on the calculations shown in Table 1, the results can be summarized as follows:
- At 115 feet, the 18% solids solvent-based coating will yield 2.55 pieces of 45-foot pipe per gallon.
- At 172 feet, the 27% solids water-based coating will yield 3.83 pieces of 45-foot pipe per gallon.
- At 637 feet, the 100% solids UV coating will yield 14.17 pieces of 45-foot pipe per gallon.
Figure 2 provides a visual comparison of lengths produced per gallon of coating for each of the three formulations.
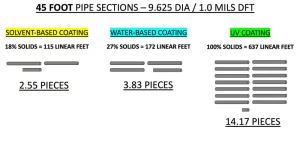
As expected, the UV coating finishes many more lengths of pipe per gallon than the solvent-borne or water-borne coatings. The case continues to be strong for UV coating, so the next comparison is the production cost for each, with 1 gallon of UV coating as the baseline: Cost: $51.24.
As shown in Figure 3, more than 14 lengths of 45-foot pipe can be coated with one gallon of UV coating.
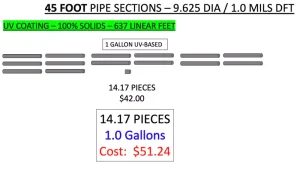
Figure 4 shows that 3.70 gallons of water-based coating would be required to achieve the same level of production as was achieved with UV coating. Cost: $55.98.
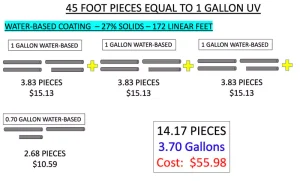
Similarly, Figure 5 shows that achieving the same production level with solvent-based coating as seen with one gallon of UV coating would require 5.56 gallons of solvent-based coating. Cost: $65.07.
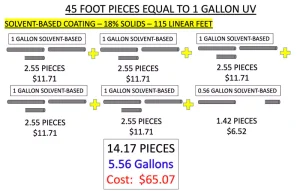
Costing Summary
In a side-by-side comparison (Figure 6), UV offers significant per-part production savings, which add up considerably over time when compared to water-based and solvent-based coating.
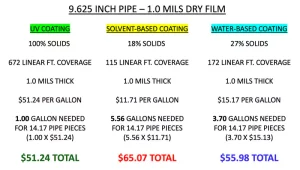
Process Savings
UV coatings applications offer significant process savings as compared to solvent- and water-based applications (see Table 2). Additional benefits and savings can be factored into the overall ROI of the project, including the following:

Faster: Ability to run faster speeds results in greater production output.
Smaller: Equipment footprint for a typical UV line is less than 20 feet, compared to many more linear feet for solvent- and water-based systems.
Quality: UV cure is instant, so no wet or damp coating arrives downstream to result in scrap or compromised product.
Cleaner: No volatile organic compounds (VOCs) or hazardous air pollutants (HAPs) are created.
As outlined above, UV offers significant savings, over time, when compared to both water-based and solvent-based coatings. A case example illustrated in Table 3 shows that UV 100% solids offers savings of more than $101,000 over water-based coating, and UV 100% solids offers savings of more than $292,000 over solvent-based coating.
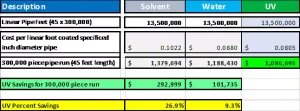
Summary
In short, solvent-based coatings have a low price per gallon, but users are paying for as much as 85% solvent. These high solvent concentrations raise other areas of concern, such as:
- Flammability: Solvents are highly flammable.
- Globally Harmonized System (GHS): Chemical classification and labeling could create issues with in-plant storage.
- Transportation: Transporting hazardous materials requires special consideration and can be costly.
- Air Quality Management District environmental compliance: Most solvents are considered VOCs and are highly regulated. This can result in excess costs for both handling the materials and eliminating the VOCs from the curing process (oven) exhaust.
As the most widely publicized alternative, water-based coatings have a low price per gallon, but users are paying for as much as 80% water. As with solvent-based coatings, these carry other areas of concern, such as:
- Transportation costs: Customers are paying to transport water as part of the coating material.
- Winter shipment: Shipping water-based coatings in extreme cold conditions can create significant issues.
- Storage: As with shipping, water-based coatings cannot be stored at or below 32°F.
- Flammability: Water-based coatings often use co-solvents (such as alcohols) to improve rheology properties and can be flammable.
While perhaps a less publicized alternative due to their higher cost per gallon, with UV coatings users receive 100% of the functional product purchased – no water, solvent or fillers. In addition, they provide a host of other benefits to the operation:
- Significantly improved corrosion protection (per ASTM B117 testing)
- Excellent coating properties in terms of adhesion, non-shrinkage, abrasion resistance, etc.
- Nonflammable
- No winter shipment restrictions
- Can be stored in unheated areas without fear of degradation
- Reduced shipping costs (often >65%) due to lower volumes
- Lower overall applied coating cost per linear foot
In addition to above-mentioned advantages, the following characteristics of the UV process are important.
Smaller equipment footprint
- Small physical footprint of equipment (see Images 1 and 2)
- Significantly less space required: 21 feet versus 100 to 200 feet in length
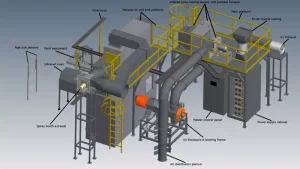
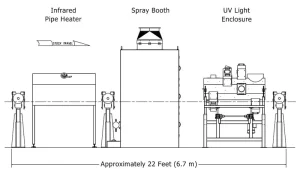
Faster
- Speed: Production line can run faster and produce more pipe feet per minute due to instant cure of coating.
- Coating is fully dry, eliminating sticky, uncured coating that can damage downstream equipment.
Cleaner and Smarter
- Environmentally friendly, with near zero VOC’s and no HAP’s
- No co-solvents
- No emission abatement systems required
- Higher overall quality, with fewer manufacturing rejects
Safer
- Less chance for slippage when handling the pipe due to the reduced lubrication effect of the cured coating
This analysis disproves the concept that UV coating is more expensive than conventional coating based solely on the per-gallon cost. When all factors are considered, it is clear that the UV coating option presents significant quality improvement and lower operating cost for the case study customer and is the best choice for that business.