By Youngsam Kim and Sungseo Cho, Miwon Specialty Chemical; and Rami Awad, Miwon Austria
Abstract
As environmental issues are becoming an industry-wide topic, the interest in water-based systems continues to rise globally. In addition to providing eco-friendly and nonflammable advantages, such systems also can be used in applications such as wood flooring, furniture, PVC flooring and others.
Like their solvent-based counterparts, waterborne systems are required to have chemical resistance and adhesion on wood and plastic substrates. In this study, researchers evaluated key properties of UV polyurethane dispersions (PUDs), such as chemical resistance, scratch resistance and adhesion, especially focusing on physical drying and drying time of water, which are closely related to productivity and energy saving.
Introduction
Polyurethane has been widely developed in various forms. Interest in both industrial and commercial uses is increasing, thanks to the advantages it offers in the synthesis of materials having various forms and physical properties, such as rubber, paint, adhesives, plastics, fiber and the like. Initially, a curing system by evaporation of organic solvent was used, but volatile organic compounds are regulated from the viewpoint of environmental protection, and the method of producing polyurethane using organic solvent gradually is being restricted. For this reason, the demand for waterborne products clearly is growing in the industrial coating market.
This environmentally friendly material often is used in industrial applications, such as wood coatings, organic photovoltaic (OPV), leather and automobile parts. Since the waterborne products are based on water instead of organic solvents, they are nonflammable and less hazardous in the workplace. In addition, the dispersions are easy to handle without requiring the addition of solvents because of the inherently low viscosity.
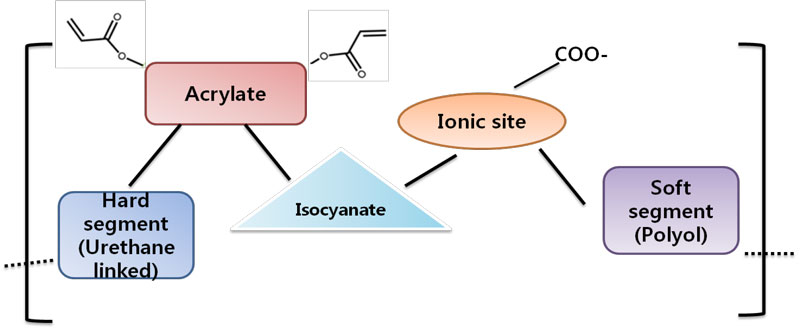

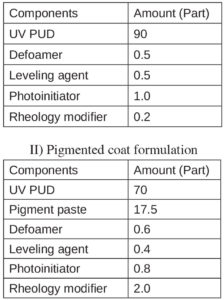
Conventionally, a method of forcibly dispersing by using an emulsifier was used, but the chemical and physical properties tend to degrade in the presence of the emulsifier. Therefore, a different approach has been taken by introducing a hydrophilic group into the polyurethane structure. After preparing the self-emulsifiable resin, it then is added to the water for homogeneous dispersion.
However, use of waterborne polyurethane includes some technical and physical limitations in terms of chemical resistance and scratch resistance. To improve those properties, UV curing is introduced into the resin. A brief explanation of UV PUDs – with the advantage of fast curing (i.e., high productivity) and good coating performance – follows.
The basic chemistry of UV-curable polyurethane dispersion is shown in Figure 1. The structure of UV PUDs generally is divided into two parts: a soft segment and a hard segment. The soft segment is composed of a long-chain polyether or ester having a molecular weight of 1,000 or more. The hard segment has a rigid property that comes from chemical structures such as urea, aromatic rings and urethane.
The hydrophilic group in the structure has a hard segment property, along with an electric force capable of dispersing in water. The electrical repulsion and the van der Waals attraction are known to stabilize the particles in water. The ratio of key attributes – such as hydrophilic group, acid value and degree of neutralization – are very important in helping to form stable particles. Important factors in determining the physical properties are double bonds, cross-linking density, polyol backbone and so on.
It is not difficult to make UV-curable urethane acrylate resin with good performance, but the preparation of UV PUDs has a number of limitations in process design because its dispersion stability is very important and difficult to achieve. The hard segment must be increased and incorporate high functional groups to achieve a high cross-linking ratio, but it may contain unstable particles. This could lead to severe defects in the dispersion process, which may result in poor dispersion stability. In addition, its storage stability could worsen, resulting in deterioration of wetting properties. Optimizing the composition of UV PUDs can help to reduce these defects.
The basic components used to build UV PUDs include polyether, polyester, diisocyanate, aromatic or aliphatic groups, acrylate compounds with double-bond for radiation curing and neutralization bases. A large number of compositions have been tested to obtain stable dispersion, which shows various properties.
In this study, a product was developed with excellent drying speed and physical drying while good chemical resistance and adhesion properties were maintained. Physical drying before UV curing has the advantage in the post-drying dust-brushing process. Drying time is highly related to manufacturing productivity. This means that a shorter drying time could consume less energy, which leads to a significant cost savings.
UV PUD products composed of various isocyanates, polyester polyols and unsaturated alcohols were investigated for performance comparison. Experimental results are summarized in Table 1.
UV PUD formulations for wood and plastic coating
The use of water-based UV systems is growing rapidly in the wood and plastic coating markets, in particular. A major trend is to make a less expensive and less hazardous high-performing product and, more importantly, suitable materials for the coating layer.
According to each application, such as plastic and wood coating, the formulations can be classified as follows. MPUD-E aims to have flexible property for the base and top coat on soft substrates. MPUD-F has good wetting properties on wood, which was designed for primer. The others, MPUD-A through D, were designed for top coat formulation of wood and rigid plastic substrates.
Formulators must understand the physical and chemical properties for successful coating design, review which type of resin best fits these applications and consider use of specific kinds of additives in clear and pigmented systems. Table 2 shows the basic formulations suitable for each coating system. All were later tested in performance.
Beechwood panels were used in testing because of their common use in the wood flooring and furniture markets. Acrylonitrile butadiene styrene (ABS) and polycarbonate (PC) were used as general plastic substrates. All substrates were coated at a wet film with thickness of 60 ~ 100㎛, dried by air at room temperature for five minutes, and then dried in a convection oven at 80°C (176°F) for 10 minutes. The coated film was cured under UV and stored at room temperature for 24 hrs.
Test methods
Chemical Resistance
Chemical resistance was measured using the following procedures:
- Coat MPUD-F on panel at a wet film thickness 60㎛ (0.06mm), air dry 5 min. > 80°C (176°F) dry 10 min
- UV curing (1×10 m/min 600W/in Hg-lamp 75%; total UV energy density: 1,400 mJ/cm²)
- Sanding with #180 sandpaper
- Coat UV PUD(MPUD) on panel at a wet thickness 60㎛ (0.06mm), air dry 5 min > 80°C (176°F) dry 10 min
- UV curing (1×10 m/min 600W/in Hg-lamp 75%; total UV energy density: 1,400 mJ/cm²)
- Stored for 24 hrs after curing
Enough chemical was applied to create a 1~2 cm diameter spot on the test panel. After 16 to 24 hours, the chemical was removed using water/ethanol, and the surface condition of the panel was checked for softening, staining, destruction, etc. Each chemical was rated on a scale of 1 to 5 (1 being no effect on the film and 5 being complete destruction). Chemicals used were coffee, espresso, cola, ketchup, hand cream, ethanol (99%) and mustard.
Scratch Resistance
A steel wool tester was used for scratch resistance. A Leneta card without primer coating was used for the test of scratch resistance. UV PUD was coated on a panel at a wet film thickness 90㎛ (0.09mm), air-dried for five minutes and then oven-dried at 80°C (176°F) for 10 minutes. It was cured with a mercury lamp at 1,400 mJ/cm2 and tested after 24 hours. The coated surface was subjected to a steel wool tester platform. A 1,000g (2.2046 lb) weight was placed on the surface of the coating and slid back and forth at a constant speed for 50 cycles. The weight was removed and loss (%) of gloss (60°) was checked at each 10 cycles.
Coin Scratch
For the coin scratch test, a beechwood panel coated with primer was used. UV PUD was coated on a panel at a wet film thickness 60㎛ (0.06mm) and air-dried for five minutes, then oven-dried at 80°C (176°F) for 10 minutes. The sample was cured with a mercury lamp at 1,400 mJ/cm2 and tested after 24 hours. Testers heavily pushed a coin on the coating surface at a 45° angle and checked the surface condition. Each sample was rated on a scale of 1 to 5 (1 being no effect on the film and 5 being complete destruction or white marks).
Abrasion (Taber)
For the abrasion test, Taber equipment was used. A beechwood panel coated with primer was used. UV PUD was coated on a panel at a wet film thickness 90㎛ (0.09mm) and air-dried for five minutes, then oven-dried at 80°C (176°F) for 10 minutes. The sample was cured with a mercury lamp at 1,400 mJ/cm2 and tested after 24 hours. The coated surface was subjected to a steel wool tester platform. The wheel was used with S33. Abrasion was tested for 200 cycles and weight loss measured by 50 cycles.
Pendulum Hardness (Koenig) Before UV Curing
For the pendulum hardness (Koenig) test, a glass panel was used. UV PUD was coated on a glass panel at a wet film thickness 60 ㎛ (0.06mm) and air dried five minutes, then oven dried at 80°C (176°F) for 10 minutes. After flash-off, testers waited for one hour at ambient temperature before measuring Koenig hardness (sec.).
Pendulum Hardness (Koenig) After UV Curing
A glass panel was used again for this test. UV PUD was coated on the glass panel at a wet film thickness 60㎛ (0.06mm) and dried in air for five minutes, then oven dried at 80°C (176°F) for 10 minutes. It was cured with a mercury lamp at 1,400 mJ/cm2 and tested by measuring Koenig hardness (sec.) after 24 hours.
Pencil Hardness (ASTM D3363-05)
Testers coated UV PUD on a glass panel at a wet film thickness 60㎛ (0.06mm) and air dried five minutes, then oven dried at 80°C (176°F) 10 minutes. It was cured with a mercury lamp at 1,400 mJ/cm2 and tested after 24 hours. Testers started with a dry, clean, well-sanded piece of wood. After removing graphite dust with prepared rubber, pencil hardness was determined as the first pencil that did not scratch the coating surface.
Dry Time
The dry time test determined speed of water flash-off before curing. Testers coated UV PUD on a glass panel at a wet film thickness 60㎛ (0.06mm) with the same solid contents, 35% (blended with water), air dried until tacky or haze phenomenon disappeared, and recorded the time. Measurement was performed at 60°C (100㎛) and 50°C (60㎛) under the same conditions.

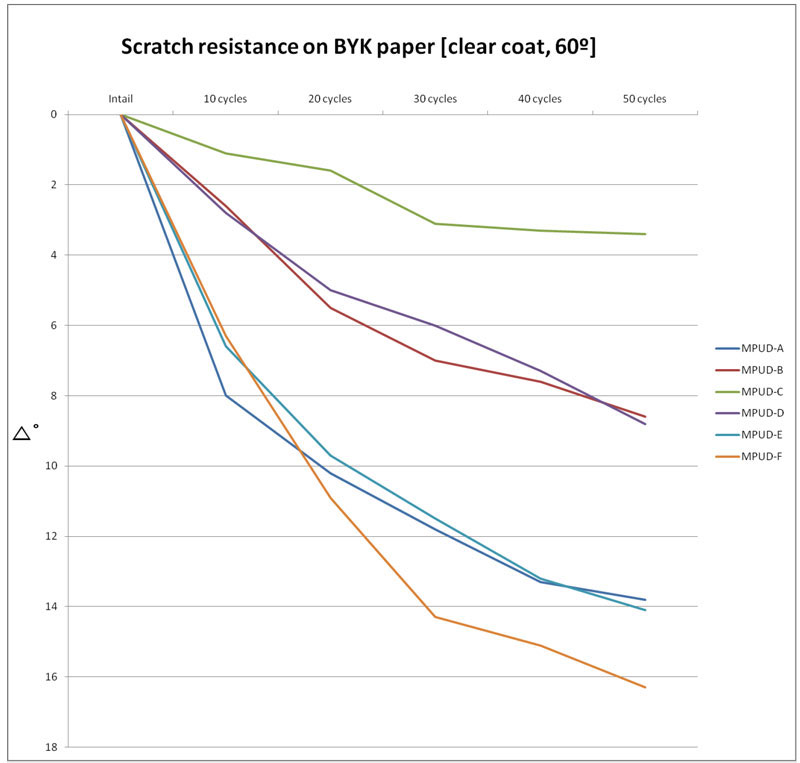
Adhesion
Various corona-treated plastic panels were used for the adhesion test. Testers coated UV PUD on each plastic panel at a wet film thickness 60㎛ (0.06 mm) and air dried five minutes, then dried in the oven at 80°C (176°F) for 10 minutes. The sample was cured with a mercury lamp at 1,400 mJ/ cm2 and tested for cross-hatch adhesion after 24 hours.
Results and discussion
Chemical Resistance on the Beech
Chemical resistance testing was performed on beechwood panels (Figure 2). MPUD-A/B/C showed relatively good chemical resistance, especially for ethanol, espresso and mustard. MPUD-A/B performed better than MPUD-F, which is used for primer. Regarding water, ketchup and hand cream, all samples – including MPUD-F – showed good chemical resistance, but with espresso and ethanol, MPUD-E and MPUD-D samples were weaker than the others.
MPUD-A/B/C incorporated polyester polyol with relatively low molecular weight, whereas MPUD-D used polyether polyol. Polyester polyol used in MPUD-A/B/C, even though it is a soft segment, was selected among many polyester polyols by evaluation of chemical resistance, so that it reacted with diisocyanate to form hard urethane domain, which then leads to good chemical resistance. Weight (%) ratio of hard segment of MPUD-A/B/C would be higher than that of MPUD-D/E, since the molecular weight of polyether polyol used in MPUD-D is much higher than that of polyester polyol used in MPUD-A/B/C. Thus, weaker results of MPUD-D compared to MPUD-A/B/C seem to result. High cross-linking density is the major reason MPUD-A/B/C show better chemical resistance than MPUD-D, depending on the difference in functional groups.
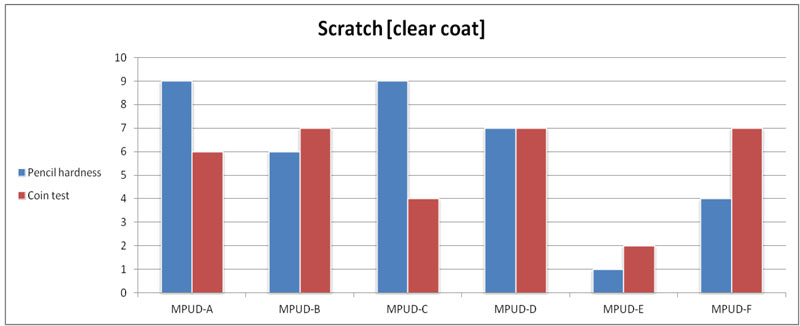
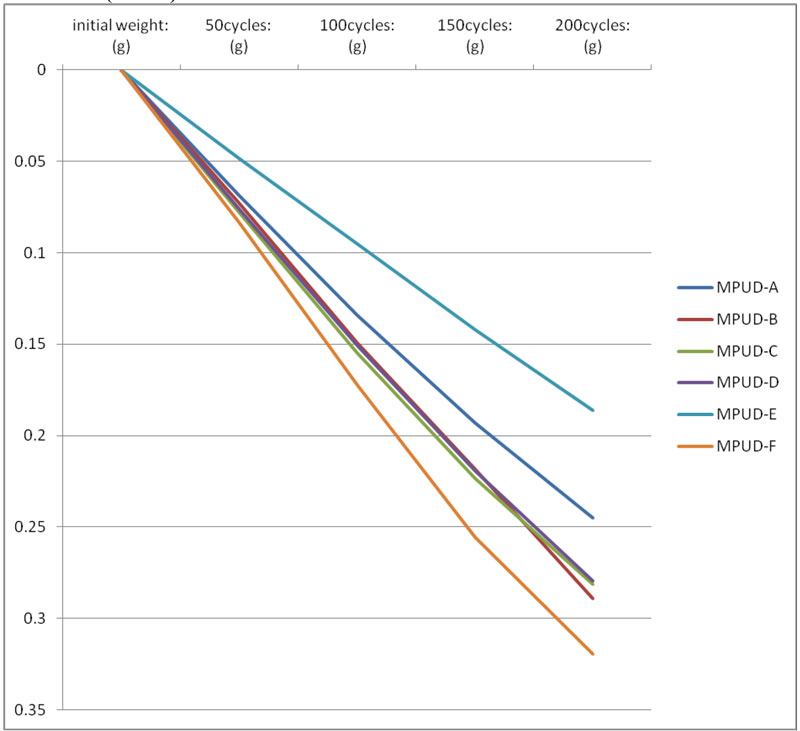
Scratch Resistance
Figure 3 shows the evaluation results for scratch resistance with steel wool. MPUD-B/C/D show much better scratch resistance than MPUD-F, and MPUD-E also shows good scratch resistance. This result is different than that of chemical resistance. Superior scratch resistance of MPUD-C compared to MPUD-F seems to come from high cross-linking density of high-functional acrylate, which can create a dense cross-linked network.
All samples except MPUD-E show good performance in coin scratch resistance. MPUD-E has less cross-linking than the other products. The results of pencil hardness testing for UV PUDs look similar to those of coin scratch testing, overall.
The abrasion test was performed on wood substrates by Taber test equipment, commonly used for industrial coatings. Samples exhibit comparable weight loss overall every cycle – except MPUD-F. In particular, MPUD-A through E showed slower loss, which might come from a good balance of flexible backbone and hard segment. MPUD-F showed a somewhat inferior performance because it originally was developed with a focus on wetting and adhesion for wood.
Adhesion for Plastic
Adhesion on plastic substrates – especially 3C coat application – is considered quite challenging in a water-based system vs. solvent-based systems. Common characteristics of plastic substrates – such as rigid properties and high surface tension – often make adhesion difficult with water-based products when compared to the porous wood substrate.
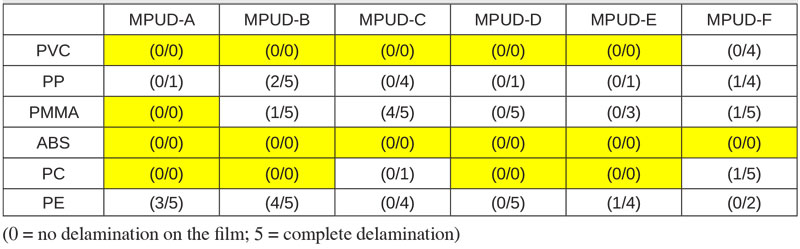
Recently, much effort has been made to solve those issues with the development of various water-based products, including UV PUDs. In this study, researchers have checked adhesion on various plastic substrates using UV PUD products as described in Table 3. Although the result shows all tested samples have poor adhesion on polyethylene (PE) – a difficult substrate – it indicates good results on polypropylene (PP), which often is used for cosmetic cases, as well as on PC and ABS, which are widely used in 3C coat application.
All the samples demonstrate good adhesion on ABS substrate. Especially, MPUD-A is the best performer in adhesion to various plastics because of its high molecular weight and difference in surface tension. The others show similar adhesion performance, except MPUD-F, which is designed for wood primer.
Physical Drying
Physical drying is defined as not being sticky to the touch, an important factor in the field of wood and plastic coating. The design for physical drying-type UV PUDs is influenced by molecular weight and polymer structure.
Table 4 shows the pendulum hardness comparison before and after UV curing. The values from pendulum measurement after UV curing represent the hardness of coated film, as well as elasticity. The values of pendulum hardness before UV curing indicate the measurement just after flash-off. This provides information about physical drying character. In the row “pendulum before UV cure,” MPUD-A and MPUD-B show the highest values, which means they have the best physical drying performance. In comparison, MPUD-F shows the lowest value.
Flash-Off Time
Water drying rate generally is influenced by the particle size and the ambient environment, such as temperature and humidity. One condition for quick water dry is the attraction to water in chemical structure. Figure 6 shows the flash-off times at 50°C and 60°C, respectively (under the same conditions), and shows which product is the fastest drying. Although transparency does not necessarily mean complete elimination of water, it is possible to make a meaningful comparison. Furthermore, the samples were tested in different conditions (temperature and thickness). In addition to checking the coated surface with the naked eye after drying, it was confirmed that fingerprints remained from touching.
These pictures were taken after one minute and four minutes, respectively. If water still is present, a haze-coated surface is visible. By confirming the picture, it can be observed that MPUD-A has a faster drying rate than MPUD-E. The idea was to design a product with better water release by incorporating less hydrogen bonding between urethane/urea and water.

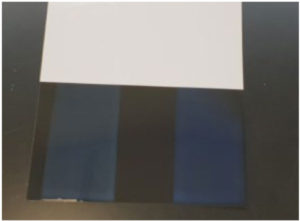
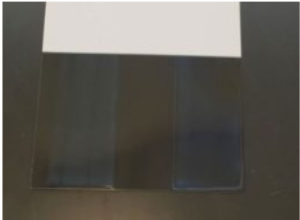
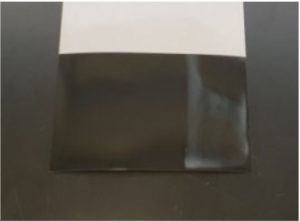

Table 5 shows the drying speed comparison. MPUD-A/B/F have the fastest drying rates, but keep in mind that MPUD-F is a tacky type. In general, the tacky type tends to show a fast drying rate due to the low molecular weight effect. When comparing only tack-free products, it can be seen that MPUD-A/B are excellent products for flash-off properties. Because of its fast drying speed, the MPUD-A/B can be considered the most energy efficient.
Conclusion
A variety of performance testing on UV-curable polyurethane dispersed products, so-called UV PUDs, was completed. Some products showed good wetting on wood substrates and remarkable adhesion results on challenging plastic substrates. Their basic properties met the standards required in general industrial coating. It is worth noting good chemical resistance and scratch resistance for any topcoat and similar applications. The advantage of being able to improve productivity and energy saving effects, thanks to fast drying speed, could be a strong driving force for the development of the technology in the paint industry.
UV-curable polyurethane dispersion will be given a tremendous opportunity in wood and plastic coating markets as various governments and regions strengthen environmental regulations. Therefore, the technology is expected to obtain more support from industrial coating formulators over conventional solvent-based coating products.
References
- Mona Valipour Ebrahimi, Mehdi Barikani, “Synthesis and Properties of Ionic Polyurethane Dispersions: Influence of Polyol MolecularWeight.” Iranian Polymer Journal 15 (4), 2006, 323-330.
- Vanesa Garcı´a-Pacios a, YoshiroIwata “Influence of the solids content on the properties of waterborne polyurethane dispersions obtained with polycarbonate of hexanediol.” International Journal of Adhesion & Adhesives 31 (2011) 787–794.
- Joseph V. Koleske, Radiation Curing of Coatings. ASTM International, 2002, 3-5.
Youngsam Kim earned a bachelor’s degree in chemical engineering at Kyung Hee University, Seoul, South Korea, and has worked in research and development since 2012 at Miwon Specialty Chemical.
Sungseo Cho, who directs research and development at Miwon Specialty Chemical, earned a doctorate in chemistry at the University of Texas at Austin.
Rami Awad earned a doctorate in UV-curable systems at Technical University Graz, Styria, Austria, and has been employed since 2014 as a managing director at Miwon Austria.