By Sage M. Schissel, PCT Ebeam and Integration, LLC
Editor’s Note: In addition, the test results are ongoing for this study. An update will be posted at www.uvebtechnology.com. Due to print space limitations, the article references can be found online in the Article Archive.
In recent years, the packaging industry has experienced a consumer backlash regarding its use of plastics.1-3 In response, companies have made sustainability pledges that include goals such as reducing their plastic consumption, reducing production waste and increasing the amount of recycled plastic in products.4-6 These strides toward a more environment-friendly future are commendable but are not always easily achieved. While consumers call for less single-use packaging waste, their expectations of how packaging performs – that food remains fresh, products remain undamaged and marketing remains eye-catching – have not wavered.
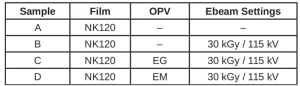
Electron beam (EB) technology is a multifaceted tool that is well suited for aiding the achievement of sustainability goals.7-12 For instance, EB crosslinking can improve mechanical properties, allowing for reduced plastic consumption by down-gauging film. It also can be used to increase compatibility between different polymers, as well as virgin and recycled polymer blends. EB-induced chain scission can be used to recycle materials through degradation. Scrap polytetrafluroethylene (PTFE), for example, is irradiated to create micro-powders that become ingredients in lubricants, inks and coatings.
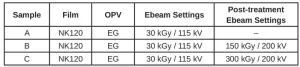
In flexible packaging production, EB is a useful tool in accomplishing one of the industry’s more recent trends – mono-layer and/or mono-material packaging. Traditionally, flexible packaging has relied on multilayer, nonrecyclable structures to achieve the wide array of demands placed on a single pouch, from moisture and oxygen barriers to tear strength and sealability.13,14 Mono-material structures are expected to meet these demands with a single type of plastic so that they can be more easily recycled or composted, but it is an ambitious challenge. One way EB can help meet this challenge is by altering a polymer without any added chemistry. Electron beam crosslinking and chain scission provide property tuning that can be controlled through a selected substrate depth. A common example of this application is crosslinking an outer layer of polyethylene (PE) to increase heat resistance without affecting the sealing temperature of the inner PE layer. Additionally, EB can be used to polymerize inks and overprint varnishes (OPVs) without the need for initiators or solvents and with comparatively little energy.15-18 OPVs are a sustainable alternative to lamination. Because inks and OPVs make up such a small fraction of the overall package, they’ve been shown to not hinder recyclability.19,20
Accompanying the mono-material trend to make flexible packaging recyclable is a movement for compostable flexible packaging. Instead of relying on the ability to effectively repurpose packaging plastics, compostable packaging seeks to optimize the disposal of packaging waste by using biodegradable polymers. EB is less tested as a production solution in compostable packaging; however, there are several ways this technology may benefit the industry. Similar to recyclable packaging, it is expected that EB-cured inks and OPVs can be utilized without impacting the biodegradability of compostable packaging. Furthermore, EB could possibly result in accelerated disintegration if the packaging is exposed to high doses after consumer use.
Molecular weight reduction by chain scission is a known effect of EB irradiation on cellulose, a common compostable material.21 It is hypothesized that this degradation could be leveraged to decrease composting time. As compostable plastic packaging gains popularity, a reduction in the multi-week disintegration process may be imperative for the current infrastructure to keep up with the increasing supply. According to a survey conducted by BioCycle in 2018, of the 185 identified food waste compost centers in the US, only 53 reported the ability to accept compostable plastics.22 In addition, accelerating plastic disintegration should make it a more profitable enterprise; high volume turnover will help offset costs, such as sorting non-compostable plastics out of the feedstock.
In this study, the application of EB in the production and destruction of a mono-material, compostable flexible food packaging structure was investigated. Low doses of EB were used to cure matte and gloss OPVs on the compostable film, which was then tested to determine if the OPV inhibited or impeded compostability. Moreover, high doses of EB were used to induce chain scissioning in the packaging structure (film/ink/EB-cured OPV) to ascertain whether such degradation at the end-of-life could efficiently reduce compost times. Puncture strength was measured as a means of analyzing the EB degradation.
Experimental Materials
The substrate material used in this study was NatureFlex™ NK 120 gauge (NK120, Futamura).23 NK120 is a transparent cellulose film coated with polyvinylidene chloride (PVDC) for moisture and gas barrier properties. It was selected because it is suitable both as a laminate and for mono-layer flexible packaging applications. NK120 is certified as industrial and home compostable. The primer used was DigiPrime® 050 (Michaelman).
The ink used was the CMYK Indigo ElectroInk digital ink set (Hewlett-Packard).20 These digital inks are indirect food-contact-safe and certified as industrial and home compostable.24,25 In addition, the digital printing process has some environmental advantages over analog methods, including less material waste, low energy consumption and no printing plates or cylinders.
The overprint varnishes (OPVs) used in this study were EHG-2601 (EG, DBT Coatings) and EMQ-3710 (EM, DBT Coatings) with high-gloss and matte finishes, respectively.26,27 These EB-curable OPVs were chosen because they are used in the flexible food packaging industry and are formulated to protect and highlight the digital inks. Both OPVs meet ultra-low migration standards, are indirect-food-contact safe and are free of initiators and solvents.
Methods
Sample Preparation
NK120 film was coated with primer and printed using an HP Indigo 20000 digital press. Unprinted NK120 film was used for some samples. Both the printed and unprinted film were then corona treated at 13.8 W/in, OPV was applied with an indirect gravure coater, and the OPV was cured at 30 kGy and 115 kV using a Broadbeam EP electron beam pilot line (PCT Ebeam and Integration). Oxygen levels were kept to < 200 ppm using a flow of 99.999% pure N2 in the beam. The EM OPV was applied using a 5 BCM, 400 line ceramic anilox with a resulting coat weight of approximately 2.0 g/m2. The EG OPV was applied using a 10 BCM, 200 line steel anilox with a resulting coat weight of approximately 3.5 g/m2.
Additionally, some samples were exposed to EB for a second time for a post-treatment, which was intended to reduce composting time through degradation of the cellulose film. The post-treatment was done in air, at 200 kV, 50 ft/min, and at doses ranging from 50 to 400 kGy. To ensure an equal dose distribution through the complete thickness of the film, 200 kV was chosen as an accelerating voltage.
Compostability Testing
To determine the influence of the samples on the composting process, samples were composted by Organic Waste Systems (OWS) following the test method detailed in ISO 16929:2013.28 The pilot-scale aerobic composting test consisted of organic biowaste (a mixture of vegetable, garden and fruit waste) in a 200-L composting bin monitored through temperature and exhaust gas composition for 12 weeks. The mixture was turned by hand every 1 to 2 weeks. In order for the test to be deemed valid, the temperature must remain between 60 and 75°C during the first week and below 65°C thereafter, with the minimum temperature remaining above 40°C for at least four consecutive weeks. Photographs were taken on a weekly basis to visually evaluate the percentage of disintegration the sample material had undergone. Because of this qualitative evaluation metric, the results of this compostability testing serve only as an indicator of whether the sample will pass a quantitative (mass balance) test. The unprinted samples tested for compostability are listed in Table 1 and the printed and post-treated samples are listed in Table 2.
Puncture Testing
Puncture resistance was used as a measure of film strength after EB exposure. Each 6.5-inch square of sample material was held taut in a fiberglass board frame (Micarta) using a rubber O-ring with a 5-inch outer diameter and 0.210-inch width. The frame had a 4-inch diameter circular window exposing the sample. A compressive load was applied to the center of the exposed sample at a rate of approximately 3 to 4 lb/s using a rounded probe with an arc 1.094 inches wide and 0.270 inches high. A broad probe was chosen to gain better resolution of the film strength lost at varying EB doses. The applied load was measured using a Uline platform dial scale (model no. H-176). The recorded value was taken as the maximum load applied before the sample ruptured, and the probe was able to push through the sample. For each sample condition, five repetitions were completed, and the values reported are an average of those repetitions. The error reported is the standard deviation of the five repetitions.
Results and Discussion
The purpose of this study is to establish EB-curable OPVs can be used in the production of compostable flexible food packaging without significantly impeding the compostability of the packaging. Furthermore, EB exposure was investigated as a means of accelerating the disintegration during composting. High doses were used to weaken the compostable film through chain scission.
Packaging Compostability
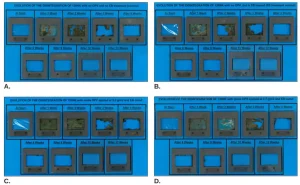
An integral aspect of using EB-cured OPVs in compostable flexible packaging is demonstrating that the OPVs do not inhibit or significantly impede the disintegration of the compostable film. In addition, because EB is well known to interact with cellulose, it is also important to establish what effect an EB curing dose (30 kGy) has on the compostability of the film.21,29 To this end, select samples (Table 1) were composted, and their disintegration progress visually documented (Figure 1).
Comparing the control film (Figure 1A) to a film that has received a curing level dose (1B), the EB dose does not appear to have a significant effect. After two weeks composting, the EB sample (1B) appears to have slightly more disintegration than the control (1A), but those impressions flip after three weeks. After four weeks, both samples are almost completely disintegrated, with only a few small pieces of film still left at the edges of the test frame.
The addition of an EB-cured OPV also does not appear to significantly impact the disintegration time of the film. The majority of both the EM-coated (Figure 1C) and EG-coated (1D) samples was disintegrated after four weeks. Both samples retained slightly more film at the edges of the test frame after four weeks than the control (1A); however, by the end of six weeks (a five-week photo not being included in the test results), the disintegration levels of the OPV-coated samples and the control are visually the same.
Post-treatment of Packaging
With the compostability testing providing positive qualitative results and demonstrating that EB-cured OPVs can be effectively used in the production of compostable flexible food packaging, the potential of EB to affect a package after consumer use was considered. Composting, even on an industrial scale with controlled conditions, is a time-intensive, multi-week process. Accelerating the disintegration of material could allow compost facilities to efficiently convert a higher volume of packaging with little to no change in infrastructure.
Visual Effects
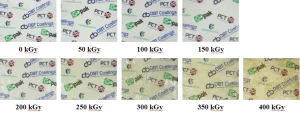
The degradation of the compostable packaging structure (film/print/OPV) caused by EB irradiation was first evaluated visually (Figure 2). Samples exposed to an EB post-treatment dose of 50 to 400 kGy were compared to a control (Figure 2, 0 kGy).
Remarkably, there are no discernible effects of the EB post-treatment until 150 kGy. At 150 kGy, there is some slight discoloration of the film and noticeable cracking of the OPV. As higher post-treatment doses are applied, the yellowing of the film intensifies and the film shrinks and wrinkles.
Puncture Strength Reduction
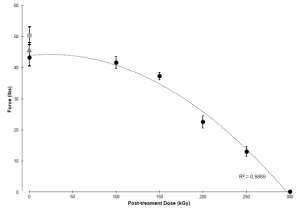
Puncture strength was used as quantitative measure of the scissioning effect caused by high doses of EB. As chain scission increases, the strength of the film is expected to decrease. Figure 3 shows a clear correlation between the puncture resistance of the compostable film and the dose level of the EB post-treatment. Comparing the plain NK120 film to the plain film after receiving a curing-level dose (Figure 3, grey square and triangle, respectively), there is an approximately 5 lb decrease in puncture resistance. Note, there is some overlap of the error in these measures. No significant difference is seen when print and EG OPV is added to the construction (black circle, 0 kGy). As the EB post-treatment dose is increased, the puncture force decreases. The relationship of these two variables follows the trend line of a second order polynomial with an R2 value of 0.9869.
Interestingly, there is almost no loss of puncture resistance between the 0 kGy and 100 kGy post-treatment dose. While EB dose levels are generally kept quite low for curing (~30 kGy), this result, along with the visual results, demonstrates there is potentially a much larger EB operating window than previously thought. The effect of EB on other mechanical properties would need to be investigated to confirm. However, a larger operating window could be a beneficial option for improving ink and coating performance through enhanced crosslinking.
Compost Results
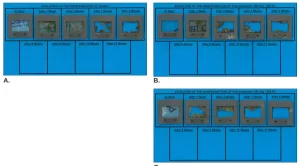
Based on the results of the puncture strength testing, three samples were chosen to test the effect of EB post-treatment on the compost rate of the packaging structure, a control and two different post-treatment doses (Table 2). Currently, the test is ongoing; however, significant differences among the samples already have been observed (Figure 4).
After one week, the control and 150 kGy post-treatment samples turned brown, but no disintegration had yet occurred. Contrastingly, the 300 kGy post-treatment sample had already experienced a significant amount of disintegration. After two weeks, a large portion of the 150 kGy post-treatment sample had disintegrated, while the control sample was still almost completely intact. The compostability test will last 12 weeks, but as of this writing, using a high dose EB post-treatment to increase the rate of disintegration of compostable material looks promising.
Conclusions
In conclusion, a qualitative compostability test was conducted and showed that EB-cured OPV did not make a significant impact on the compost rate of a cellulose film. These results indicate that the reviewed structures would likely pass a quantitative, mass balance test.
Furthermore, a post-treatment EB dose was evaluated as a potential means of increasing the composting rate of the flexible packaging structure. The degradation of the film was confirmed visually as well as by demonstrating that puncture strength decreased as the post-treatment dose was increased. The qualitative compostability testing of these post-treated structures is ongoing; however, after four weeks of testing, high-dose EB post-treatment was shown to positively impact the composting rate.
In addition to quantitative compostability testing, future work in this arena includes broadening the scope of OPVs, inks and compostable substrates investigated. The optimal EB dose necessary to degrade a compostable structure is expected to be dependent on the chemistry of the film and should also be evaluated for a wide variety of compostable material.
The broad applicability of EB was demonstrated by establishing the technology as a tool for both the production of compostable packaging as well as the degradation of it after use. As the packaging industry endeavors toward a more sustainable future, versatile technologies, such as EB, provide companies flexibility in developing new avenues to achieve their recycling and composting targets.
Acknowledgements
The author would like to acknowledge DBT Coatings for initiating and funding the first round of compostability testing and sharing the results (Figure 1). These results provided the impetus for further exploration of electron beam’s role in compostable packaging. The author would also like to acknowledge Futamura for donating the NK120 film and GOpak for donating printing press time and materials.
References
- Crawford, E., 2019. Consumer push-back against plastic will spur manufacturers to seek new packaging in 2019.https://www.foodnavigator-usa.com/Article/2019/01/22/Consumer-push-back-against-plastic-will-spur-manufacturers-to-seek-new-packaging-in-2019
- Pierce, L. M., 2019. Consumers want non-plastic packaging options.https://www.packagingdigest.com/sustainable-packaging/consumers-want-non-plastic-packaging-options-2019-11-14
- Heidbreder, L. M., Bablok, I., Drews, S., Menzel, C., 2019. Tackling the plastic problem: a review on perceptions, behaviors, and interventions. Sci. Total Environ. 668, 1077-1093.
- Nestlé. What is Nestlé doing to tackle plastic packaging waste.https://www.nestle.com/ask-nestle/environment/answers/tackling-packaging-waste-plastic-bottles
- Unilever. Rethinking plastic packaging – towards a circular economy.https://www.unilever.com/sustainable-living/reducing-environmental-impact/waste-and-packaging/rethinking-plastic-packaging/
- Pepsico, 2018. Pepsico’s work to improve recycling in the US.https://www.pepsico.com/docs/album/esg-topics-policies/pepsicoworktoimproverecycling.pdf?sfvrsn=3071b156_12
- Burillo, G., Clough, R. L., Czvikovsky, T., Guven, O., Le Moel, A., Liu, W., Signh, A., Yang, J., Zaharescu, T., 2002. Polymer recycling: potential application of radiation technology. Radiat. Phys. Chem. 64, 41-51.
- Czvikovsky, T., 1995. Reactive recycling of multiphase polymer systems through electron beam. Nucl. Instrum. Meth. B. 105, 233-237.
- Clough, R. L., 2001. High-energy radiation and polymers: a review of commercial processes and emerging applications. Nucl. Instrum. Meth. B. 185, 8-33.
- Mészáros, L., Bárány, T., Czvikovsky, T., 2012. EB-promoted recycling of waste tire rubber with polyolefins. Radiat. Phys. Chem. 81, 1357-1360.
- Navratil, J., Manas, M., Mizera, A., Bednarik, M., Stanek, M., Danek, M., 2015. Recycling of irradiated high-density polyethylene. Radiat. Phys. Chem. 106, 68-72.
- Jamdar, V., Kathalewar, M., Dubey, K. A., Sabnis, A., 2017. Recycling of PET wastes using electron beam radiations and preparation of polyurethane coatings using recycled material. Prog. Org. Coat. 107, 54-63.
- Wagner, J. R. (Ed.), 2016. Multilayer flexible packaging. Elsevier.
- Morris, B. A., 2016. The science and technology of flexible packaging: multilayer films from resin and process to end use. William Andrew.
- Mehnert, R., 1995. Electron beams in research and technology. Nucl. Instrum. Meth. B. 105, 348-358.
- Golden, R., 2012. What’s the score? A method for quantitative estimation of energy use and emission reductions for UV/EB curing. Radtech Report. (3), 44-48.
- Golden, R., 2008. Sustainability advantages of ultraviolet and electron beam curing. Radtech Report. (4), 43-47.
- Sanders, R., 2006. Electron beam: one way to mitigate rising energy costs. Radtech Report. (2), 20-22.
- Korn, D. J., 2005. Recyclability of UV and EB printed and coated paper. Radtech Report. (3), 47-49.
- HP, 2018. HP indigo electroink: frequently asked questions.https://www8.hp.com/h20195/v2/ GetPDF.aspx/4AA7-4166ENW.pdf
- Driscoll, M., Stipanovic, A., Winter, W., Cheng, K., Manning, M., Spiese, J., Galloway, R. A., Cleland, M. R., 2009. Electron beam irradiation of cellulose. Radiat. Phys. Chem. 78, 539-542.
- Goldstein, N., 2018. Quantifying existing food waste composting infrastructure in the US.http://www.biocycle.net/pdf/2019/FoodWasteCompostInfra.pdf
- Futamura. NatureFlex™ NK technical data sheet.
- HP, 2016. HP indigo for food packaging printing: regulatory overview.https://www8.hp.com/h20195/v2/GetPDF.aspx/4AA4-8153ENW.pdf
- Gilbert, N., 2019. HP indigo digital print certified for compostable packaging.https://press.ext.hp.com/us/en/press-releases/2019/hp-indigo-digital-print-certified-for-compostable-packaging.html
- DBT Coatings. Technical data sheet EHG-2601 EB high gloss top coat: low extractables and low migration.
- DBT Coatings. Technical data sheet EMQ-3710 EB low gloss top coat: low extractables and low migration.
- ISO 16929:2013. Plastics – determination of the degree of disintegration of plastic materials under defined composting conditions in a pilot-scale test.https://www.iso.org/standard/62948.html
- Zivanovic, S., 2015. Electron beam processing to improve the functionality of biodegradable food packaging. In: Pillai, S. D., Shayanfar, S. (Eds.), Electron beam pasteurization and complementary food processing technologies. Woodhead Publishing, Boston, pp. 279-294.