Reprinted with permission from Richard Romano, WhatTheyThink.com
At what may well have been the last in-person industry event for a while, professionals in the world of energy-curing technology gathered in Orlando in early March for RadTech’s 2020 UV+EB Technology Conference, three days of sessions devoted to ultraviolet (UV) and electron beam (EB) technologies. UV and EB straddle a number of disparate industries – a prominent one in particular at this year’s conference was the use of UV in healthcare as a disinfecting agent, using UV to kill pathogens that may be living on hospital floors and other surfaces.
Indeed, one highly relevant panel discussion was “UV vs. the Coronavirus: What’s the Situation and What Are We Doing”? Dr. John Boyce of Boyce Consulting gave an overview of the virus in general and the (then) current situation which was exceedingly informative. The session included a video report from Zhiming He of Foshan Comwin Light, who was supposed to have appeared in person but, as he is based near Wuhan, remained in China and gave an update of the situation at “ground zero.” This being a UV conference, the thrust of the session was the extent to which UV might be effective in killing the virus. Obviously, it’s far too soon to draw any solid conclusions, but Dr. Boyce looked at the efficacy of UV on similar pathogens, such as SARS CoV, and cited four studies that found that varying UV exposure times and distances were effective in reducing the prevalence of the virus. “We need more definitive studies on what role UV can play,” said Dr. Boyce.
An interesting further – if disquieting – application was presented by Dr. Art Kreitenberg of Dimer UVC Innovations. He began his presentation with the question, “How often do you think the plane you flew here on is disinfected?” Given the airline I primarily fly, my assumption was never, but as it turns out, no commercial airplane is ever disinfected, as there is no practical way of doing so. At least until now. Dimer UVC Innovations is developing the GermFalcon, a UV-based aircraft disinfection system that is in the process of being tested and is proving to be fast and effective at reducing the germiness of airplane seats and tray tables. It wasn’t designed for COVID-19 in particular, but rather for flu and other common viruses that can be the bane of both passengers and crews. Dimer hopes to have the GermFalcon take flight by the next flu season.
UV and EB have many graphic communications applications, most commonly in energy-curing inks and coatings. Flatbed wide-format and industrial printing, for example, have been completely enabled by UV-curing inks, and packaging is a top application for UV and EB inks. During a lively panel discussion called “Trends in UV + EB Packaging,” the conversation quickly turned to that perennial bugaboo of food packaging: migration. UV and EB inks are used for food packaging, but not on what are called primary surfaces – the part of a package that has direct contact with food – and only on secondary surfaces if the material has the appropriate barrier properties and the ink has low migration tendencies, meaning it won’t permeate through the packaging into the food. This is why corrugated is one of the top applications for UV inks, since it has high barrier characteristics, and food items generally aren’t placed loose in corrugated containers. As for digital printing of packaging, it’s “a cultural shift, especially for large brands,” said James Gill, Fujifilm/Dimatix. “Brands are not ready to change over to digital” despite the fact that, he added, “there is a compelling argument to go digital.”
A topic that came up in this session, as well as at a later one called “Innovative Directions in Flexible Packaging” (full disclosure: I moderated this panel), was sustainability, and the top “innovative directions” that flexible packaging is moving is, according to the panelists – who included representatives from Pepsi, EST (electron beam curing equipment), Comexi (flexo and offset printing systems), and Ashland (chemicals used for inks, coatings, substrates, etc.) – in more sustainable directions. The consensus is that reducing or eliminating plastic in favor of other materials like paper isn’t necessarily the best or even most sustainable strategy, but rather developing more compostable, recyclable and reusable flexible packaging materials will satiate the need for flexible packaging, while at the same time addressing environmental concerns.
3D printing also was a big topic at the event. One panel discussion – “Emerging Applications in Additive Manufacturing/3D Printing” – ran down the veritable “explosion of opportunities” in industries such as healthcare (3D printing prosthetics/orthotics and even implants and organs), entertainment (one of the panelists was from Walt Disney Imagineering, who spoke about how Disney uses 3D printing in sets and costuming for various theme park attractions), to military applications (uniforms, helmets, armor, even weaponry), to a variety of other “consumer industrial” applications. There also was a discussion about digital vs. “analog” manufacturing (3D printing vs. injection molding, for example), which had a familiar ring to those of us who have been witnessing the analog to digital transition in the various segments of our own industry. “3D printing is just another tool in the tool box,” said Michael Brady of 3D Systems. “If you want one million parts all the same, injection molding is the way to go. If you want shorter-run, more customized parts, 3D printing is the way to go.”
This originally appeared on WhatTheyThink.com. Copyright © 2020 WhatTheyThink. All rights reserved. Reprinted with permission. WhatTheyThink is the global printing industry’s leading independent media organization with both print and digital offerings, including WhatTheyThink.com, PrintingNews.com and WhatTheyThink magazine versioned with a Printing News and Wide-Format & Signage edition. Our mission is to provide cogent news and analysis about trends, technologies, operations, and events in all the markets that comprise today’s printing and sign industries including commercial, in-plant, mailing, finishing, sign, display, textile, industrial, finishing, labels, packaging, marketing technology, software and workflow.
RadTech Awards Given for Papers, Posters, Emerging Tech and StartUps
Several awards were presented at RadTech 2020 in Orlando, Florida, held March 9 to 11. Thank you to Molly Hladik, chair of the Radtech Technical Committee, for sharing her comments from the RadTech and IUVA 2020 Awards Dinner, which became the basis for this report.
Best paper awards
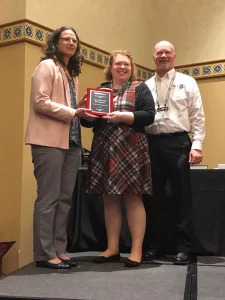
Well over 100 abstracts were received, and all were thoroughly reviewed and discussed by the committee for inclusion in the RadTech 2020 Technical Programs. Committee members included Molly Hladik, Michelman; Julie Jessop, Mississippi State University; Joel Schall, Henkel; Alexander Polykarpov, Sirrus, Inc.; and Susan Bailey, Michelman. Of the 100+ abstracts, more than 70 papers were submitted for review. From those 70+ papers, the technical committee reviewed and selected the best overall paper and the best student paper submitted for the conference. Unique to this year is that both papers awarded focused on the use of electron beam technology.
This year’s Best Paper designation was awarded to Sage Schissel and Karl Swanson for their paper titled, “Attainable Sustainable: Using Electron Beam Technology in Compostable Flexible Packaging.” The Best Student Paper designation was awarded to Nicole Thiher, Erin Peters, Sage M. Schissel and Julie L.P. Jessop (faculty) for a paper titled, “Comparison of UV- and EB-Initiated Polymerizations Based on Equivalent Radical Concentration.”
Student poster competition
For the past few conferences, RadTech has partnered with the Technical Association for the Graphic Arts (TAGA) to request that graphic arts students compete in creating a poster to tout the benefits of energy curable technology. These posters then are voted on for the best representation of the technology. This year’s winner is an IUVA member: Dana Pousty is a student with the Water Research Center, School of Mechanical Engineering, Tel- Aviv University. The second-place winner is Prashant Koktar, a Ph.D. student in Paper and Printing Science at Western Michigan University, doing research in Industrial Inkjet Printing. These honorees received cash awards from RadTech International North America, and the first-place winner’s design is featured on the cover of this issue of UV+EB Technology magazine.
Emerging technology awards
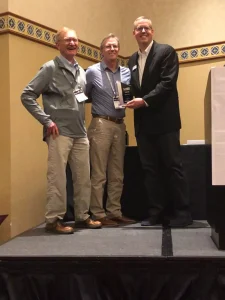
The emerging Technology Awards go to novel, creative and/or impactful uses of curing technologies. This year, the awards were given to a diverse group of end users. Winners included:
Electron Beam Technology for Food Packaging, PepsiCo
As innovative solutions are being sought for the development of a circular economy, PepsiCo is leading the way by working with the flexible packaging supply chain to develop advanced materials and processes for food packaging. As part of these PepsiCo initiatives, the company is exploring electron beam curing, as a fast, clean and energy-saving way to dry inks, coatings and adhesives for PepsiCo’s flexible packaging operations.
Additive Manufacturing of High-Performance Material for Teeth Replacement, Myerson LLC
One of the largest and fastest-growing opportunities in additive manufacturing is the dental market. While the printing of teeth as temporary replacements is feasible, if not yet widely adopted, reaching the very high performance required for long-term tooth replacement has been out of reach. Myerson, LLC (Chicago, Illinois), in collaboration with Hybrid Ceramic (San Francisco, California), has developed a high-performance UV-curable dental material that can be printed and used as long-term teeth replacements. In vitro and in vivo trials are underway.
Surface Treatment of Intraocular Lens Injectors, AST Products, Inc.
LubriMATRIX™ technology has become a “Hidden Champion” for cataract surgery, providing a novel and innovative surface treatment technology specifically developed to enable a safer, simpler and more effective intraocular lens (IOL) delivery. An IOL is an artificial lens made of polymeric or silicone materials, and it is used to replace the patient’s natural lens that has become opaque, a.k.a. cataract. This technology is a patented surface treatment that utilizes an electron-beam-induced grafting method to append a hydrophilic layer onto the surface of an IOL.
UV cured transparent films for Advanced Process Control (APC), Materials Business Unit, Applied Materials
The drive to smaller, faster and more versatile electronic devices such as cellphones has accelerated innovation in state-of-the-art computer chips. To support this innovation, Applied Materials has integrated a high-energy stationary UV cure system to fabricate the UV transparent polymer films. The optical uniformity of the film and time to cure make UV curing a critical technology for these processes.
RadLaunch awards
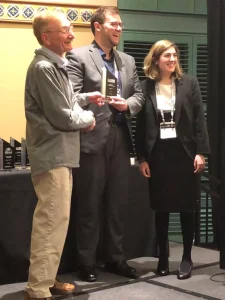
Awards also were presented to students, universities, start-ups or others doing novel work in UV/EB curing.
HARP (High-Area Rapid Printing), Azul 3D
This three-year-old start-up spun out of Northwestern University and is creating a paradigm shift in the plastics manufacturing sector via a revolutionary 3D-printing technology called HARP (High-Area Rapid Printing). HARP enables the use of both oxygen-sensitive and oxygen-insensitive photo-chemistries at rapid speeds, broadening the scope of UV/EB technology for 3D printing.
A Solvent-Free Radical Photopolymerization that Continues its Extensive Post-Conversion in the Dark, University of Colorado
A new photoinitiating system with unprecedented photo-efficiency and extensive post-conversion in the dark has been developed. This innovation allows reduced light exposure times helping to cure irregular surfaces, or thicker samples that might otherwise not work. This discovery promises to increase the scope of photocuring technologies into new application areas. This award goes to a team including Kangmin Kim, Jasmine Sinha, Charles Musgrave and Jeff Stansbury.
Next-Generation Energy Storage with UV Curing of Novel Polymer Electrolyte Materials, The Hosein Research Group, Syracuse University
The ever-increasing demand for Li-ion battery storage solutions soon will present an imminent crisis with the availability of mineral lithium to support the clean energy economy. The challenge with next-generation batteries is developing suitable electrolytes. To this end, polymer electrolytes are an attractive solution owing to their high conductivity, as well as mechanical and thermal conductivity. UV curing may be used to produce both acrylic- and epoxy-based polymer electrolytes, to effectively operate in prototype next-generation batteries.
Bio-based 1,5-Pentanediol: A New Renewable Monomer for the Radcure Industry, Pyran
The vast majority of chemicals are made from nonrenewable and often expensive petroleum (oil) resources. Pyran set out to find a better way and discovered a new pathway to make a chemical called 1,5-pentanediol (1,5-PDO) from renewable resources, such as corncobs. This technology allows the renewable 1,5-PDO to be made at costs that can be 30% to 50% lower than that of similar oil-based chemicals. The 1,5-PDO product is a major component in many ultraviolet (UV) cure coatings.
Real-Time Feedback Controlled Monomer Conversion: A New Paradigm for UV Curing Process Control, Eindhoven University of Technology in The Netherlands
To prepare UV technology for the imminent fourth industrial revolution, a new paradigm is proposed for UV curing process control. The proposal consists of acquiring in-situ measurement data of monomer conversion from a spectrometer to compute a corrective action for the UV light source if needed. This innovation makes UV curing more robust to disturbances and may prove to be an indispensable solution for quality control.
A special RadLaunch University award was presented to Hamidreza Asemani and his professor adviser, Vijay Mannari, from the Coatings Research Institute at Eastern Michigan University for Novel UV-Initiated Dual-Curing Thermoset Materials Suitable for 3D Printing. While 3D printing is fast emerging, one major challenge faced by 3D-printed products is their suboptimum performance due to poor inter-layer adhesion. A team from Eastern Michigan University has designed a 3D printing material that cures by two independent cure mechanisms – one providing rapid green strength development for faster processing, while the second one allows for chemical bonding between the layers – thus significantly enhancing final product performance. The proposed system is enabled by UV curing technology, making it efficient and environmentally responsible.