By James E. Goodrich, Miwon North America, Inc.
With their distinct advantages, UV LED energy sources continue to move into new applications. And, even with UV LED improvements, there is a distinct need for new and innovative acrylate chemistries to enhance cure while not being detrimental to the overall formulation performance. In this paper, the author will cover the positive and negative effects of changing various backbone structures of an acrylated amine.
Introduction
Acrylated amine oligomers are not a new class of chemistry for UV/EB applications. These oligomers are an upgraded subset of tertiary amines, which are well known to increase the cure response of UV-cured acrylate systems. The acrylated amines combine at least one unsaturated acrylate group and a tertiary amine on the same molecule through a number of different, novel, structures. The acrylated amine oligomers are used in formulations where there are concerns about the mobility of nonreactive, low-molecular-weight, tertiary amines on the final coating’s properties. Also, acrylated amines can participate in the photopolymerization, just like any other acrylate monomer or oligomer that is present.
Traditionally, tertiary amines have been used in graphic art coatings when running at high speeds with thin, low-viscosity coatings. The tertiary amine can serve two purposes in these formulations: First, to act as an abstractable hydrogen site for Norrish Type II photoinitiators to create a highly reactive free radical for initiating polymerization of the acrylate formulation components, and second, the alkyl-amino radical can react with oxygen present in the coating to create a non-propagating peroxy radical. That peroxy radical then can react with more tertiary amines, create another alkyl-amino radical and repeat the cycle1. There is much literature describing this process in more detail.
The well-known formulation strategy of using acrylated amine oligomers with Norrish Type II photoinitiators is common for formulations cured by medium-pressure Hg arc lamps and microwave H lamps. The wavelengths of absorption for benzophenone and its derivatives, for instance, match the output wavelength of those UV sources. But, moving to UV LED sources creates an issue with this formulation strategy.
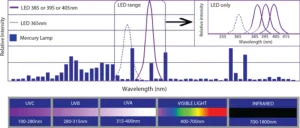
The blue bars in Figure 1 show the spectral output of a medium-pressure Hg arc lamp. Benzophenone, and other Norrish Type II photoinitiators, absorb in the UVB range. But, the UV LED sources currently being used in a wide number of applications have narrow outputs in the UVC range. Usually, their outputs are centered on 385, 395 or 405 nm.2
The UV LED manufacturers have done a great job of increasing the peak irradiance and energy density of their lamp systems. This has allowed for their equipment to be used in many applications that traditionally were the realm of Hg arc and H microwave lamps. There is an acknowledged deficiency of the current chemistry to fully cure with UV LED sources at desired line speeds. The focus of this project and resulting paper was to understand and evaluate the use of novel acrylated amine oligomers to address curing deficiencies in UV LED-cured systems. Secondarily, the project focused on how acrylate amine oligomers can move beyond graphic art coatings to be useful tools to build UV LED-cured industrial coatings with excellent and unchanging performance.
Experimental
To start, the project looked at the structures of the various commercial acrylated amine oligomers produced by Miwon. In general, these oligomers can be split into two classes (Figure 2). Class 1 uses secondary amines that undergo a Michael reaction with the acrylate group to create molecules with at least one unsaturated acrylate and one tertiary amine. The molecular weight (MW) is the MW of the monomer plus that of the secondary amine. These structures will have the lower viscosity of the two classes described here because the structures are not rapidly building MW and result in a very low polydispersity of the final product. Often, Class 1 acrylated amines will have unreacted acrylate monomer left in the commercial product composition. Class 2 uses a primary amine reacted with multifunctional acrylate monomers to create the acrylated amine oligomer. The final Class 2 product builds MW quickly, and the final product is less controlled than that made in Class 1. The reaction tends to create a wider polydispersity and a higher viscosity. Class 2 structures still are very useful, especially when trying to create a final product with very high acrylate functionality for a variety of performance reasons.
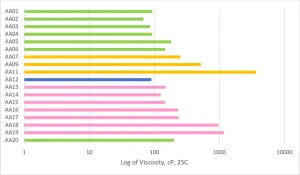
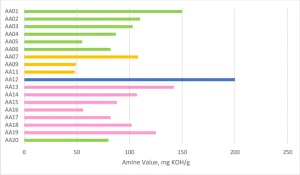
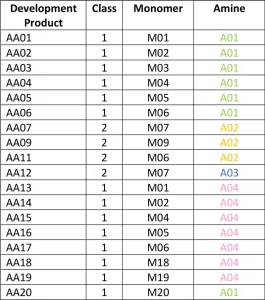
AA01 through AA20 all were made using commercially practiced reaction schemes to produce the acrylated amine oligomers. All products have the same stabilizer system to eliminate differences between products related to stabilization. Because of this, AA08 and AA10 gelled before being used in the study and were excluded. Table 1generally describes the monomer (M) and the amine (A) used to construct the products. Structure property relationships will be examined as the article moves through the project results (Figures 3-5).
The UV LED source for the project was a Phoseon FireJet™ FJ200. The lamp was an air-cooled light array with a peak irradiance of 12W/cm2, centered on 385 nm.3 The lamp was paired with a variable speed belt and set to a distance of 1 cm from the surface. For this project, the lamp was set to 100% output and not varied. Energy delivered to the formulations was varied by changing the line speed.

To test these products in a meaningful manner, a general coating formulation was developed that utilized a high percentage of acrylated amine oligomer to see differences in the structures. The initial formulation work was done using AA02 as the acrylated amine. Through the formulation development, a few key elements were found. The acrylated amine oligomer, trifunctional urethane acrylate diluted with EO TMPTA (PU3600E) and EO HDDA (M202) percentages were set and the TPO (triphenyl phosphine oxide) level evaluated in a ladder study to find the necessary level. The formulation did not cure with less than 6% of TPO in it and maxed out the performance benefit at 8%. It is believed the formulation didn’t cure due to oxygen inhibition and possibly the lack of free radical flux. With this information, the project parameters settled on the 8% loading. To try to increase the surface cure of the formulation, benzophenone – in the amounts of 1%, 2% and then 3% – was added to the formulation with 8% TPO already in it. The 1% benzophenone unexpectedly boosted the line cure speed by 20%. The benzophenone is not absorbing the energy emitted by the UV LED, but it may be excited by the TPO-generated free radicals and accelerate the curing process. The 2% and 3% benzophenone addition did not further increase the line cure speed, so the formulation in Table 2 contains the 1% addition.
To understand the effect of the various acrylated amine oligomers, an AA00 formulation was made where the 50.0% of acrylated amine was replaced with EO TMPTA (M3130). The AA00 gives a formulation with no tertiary amine functionality and shows the real effect of the chemistry change.
One of the main focuses of the project was to achieve commercially viable curing line speeds with the acrylated amine oligomer chemistry. The coatings were applied to Lenetta cards using a #5 wire wound rod for a nominal thickness of 0.5 mils. Surface cure speed was judged by the combination of fingernail scratch and rub resistance by the same trained chemist. The AA00 formulation, without any tertiary amine, was not able to achieve a smear-free surface cured state. The other formulations were fully smudge-free at the line speeds depicted in Figure 6. There are interesting structure property relationships buried in this first set of formulation data. The AA12 formulation has an acrylated amine oligomer with a high amine value, but the final cure speed is one of the lower cure speeds seen in this study. The extra tertiary amine in the formulation apparently was not participating in accelerating the surface cure and actually led to issues that will be discussed in the color change section. The Case 1 oligomers, which generally have a lower number of acrylate groups per molecule, showed cure speed approximately the same as the Case 2 oligomers with higher acrylate functionality. The Case 1 oligomers (represented in the green and pink bars in Figure 6) have a higher amount of tertiary amine value per molecule. This shows that the amine value has a positive effect on increasing the surface cure in this formulation that has a small amount of Norrish Type II PI and cured with a UV LED source.
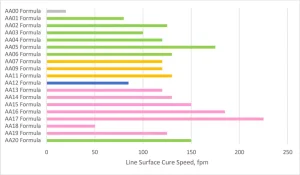
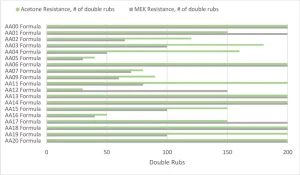
Figure 7 shows the solvent resistance of the various formulations cured at the highest cure speed from Figure 6. The MEK or acetone-soaked cheesecloth was rubbed on the surface with a 1 kg hammer and stopped when breakthrough of the coating could be observed. A water resistance test also was performed that used the same method, but all formulations exceeded 200 double rubs. A more in-depth test for the next level would look at a water soak test to understand the change in properties over time. Before analyzing, it is important to note that the AA00 formulation never fully surface cured but had very good bulk solvent resistance. That means that the AA00 formulation, though showing good solvent resistance, is not a viable commercial coating that can be cured with UV LED.
The crosslink density of the overall system was the key aspect for predicting the MEK and acetone solvent resistance of the formulations. As the MW of the Case 1 acrylated amine oligomers increased from AA01 through AA05, the solvent resistance dropped considerably. The same trend was repeated in the AA13 to AA16 series, even though the modifying amines were different backbones with varying degrees of hydrophobicity. The high acrylate functionality formulations of AA06, AA13, AA14, AA18 and AA20 all had excellent solvent resistance. On the flipside of that, the Case 2 acrylate amine oligomers only had mediocre solvent resistance despite having high acrylate functionality. That functionality is on higher MW backbones, and thus the overall density is lower than the high functionality Case 1 oligomers. And, that cross-link density difference is well exhibited in the solvent resistance testing.
Historically, one of the biggest issues with using acrylated amine oligomers in clear coatings was the color development of the coating after UV cure and more color development as the coating aged on the substrate. In order for this chemistry to be viable in the applications where UV LED curing sources are viable, it needs to exhibit low yellowing after UV cure and low yellowing upon aging. Coatings 0.5 mil thick were applied to Lenetta cards and the L*a*b color of the coating measured by a BYK Gardner spectro2guide, d/8 spectrophotometer with the D65/10 illuminant and d:8° measuring geometry. The coatings then were cured at the maximum surface cure speed in Figure 6 and the color measured. The calculated Delta-E is represented in Figure 8 by the solid bars. The UV-cured coatings then were subjected to 336 hours of 60°C heat aging, the L*a*b color measured and the Delta-E calculated. The Delta-E of the Lenetta card during heat aging was subtracted from the final Delta-E. The patterned bars represent the Delta-E of each formulation after the heat aging. Taken together, they represent the Delta-E of the coating formulation from the liquid state through UV curing and heat aging. The human eye can see a Delta-E of more than 1, though that is just a general rule of thumb and dependent on the colors involved.
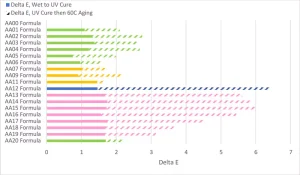
In general, the acrylate amine oligomers built with A01 and A02 amines showed low Delta-E from the liquid state through UV curing. The change would be barely perceptible by the human eye. A significant portion of that increase is likely due to yellowness from the TPO during the curing process. In this study, the authoring company did not work to decouple that color change because the TPO was seen as a critical formulation component and not able to be removed. The acrylated amine oligomers built from A04 showed more Delta-E after UV curing.
The biggest differences among the different amines could be seen after the 336-hour heat aging at 60°C. The AA12 formulation, which used A03 amine, had a very dramatic color increase that could be seen easily by the human eye. This acrylate amine had the highest amine value of all compositions, and that was the main contributor to the change, especially after heat aging. Unfortunately, the A04-based acrylated amines had significant Delta-E values that likely would exclude them from use in many color-sensitive applications. Several of the A04 modified products had color changes that were visible to the human eye. But, on the positive side, the Case 2 acrylated amine oligomers modified with A02 had a minimal Delta-E during the heat aging process, which points to A02 being a very good amine modifier for this performance aspect.
Conclusion
Through this project, several interesting aspects of using acrylated amine oligomers in UV LED-cured applications were further understood. It was shown that clear formulations could be developed with good cure response, even if the traditional formulation strategies had to be adjusted. When all the data – including viscosity, cure speed, solvent resistance and overall Delta-E – were examined, the A01 modification yielded acrylate amine oligomers with the most useful set of properties. Those Class 1 oligomers exhibited low viscosities with good cure speeds and varying degrees of solvent resistance. They also all showed low yellowing after UV cure and after heat aging. AA20 showed itself to have a particularly interesting set of properties and deserved consideration for commercialization. The next step in the project would be an examination of the change in physical properties of the formulations after extensive 80% relative humidity / 60° or 80° C aging.
References
- Stephen C. Lapin, P. a. (2014). Effect of Amine Synergists on the EB-Curing Properties. RadTech Report, 30-34.
- Phoseon Technology. (2020). Phoseon Technology. Retrieved from https://phoseon.com/industrialcuring/technology/led-uv-wavelength/
- Phoseon Technology. (2020). Phoseon Technology. Retrieved from https://phoseon.com/industrialcuring/products/firejet/