By Mike Toth, BYK USA
In modern wood coatings, UV-curable technologies are growing worldwide. High-quality aqueous, solvent-borne and solvent-free UV coatings exist to protect consumer wood (and non-wood) products, such as hardwood flooring, kitchen cabinets, millwork, store fixtures, LVT flooring, and office and residential furniture. Traditionally formulated for clear systems with typical gloss ranges from satin to high-gloss coatings, recent consumer wood coating trends have gravitated toward much deeper – in some instances, ultra-low – matte finishes. In today’s market, some consumers seek the appearance of bare wood with deeply matted finishes, but simultaneously demand superior surface durability and optical appearance that only high-quality finishes can provide. Can formulators provide a flawless surface with the scratch, stain, chemical and UV fade resistance properties that consumers desire in a low matte finish? The answer is yes, if the coating is:
- Properly formulated with dispersing additives that are efficient at reducing processing viscosity and enabling Newtonian flow behavior, while accepting the addition of heavy silica or matting agent loading, and
- Able to incorporate compatible technologies such as wax dispersions, mixed mineral technology (MMT) clays or synthetic clays to compliment silica-based matting agents, resulting in an improved surface finish.
Dispersant requirements to achieve low gloss stability and improved flow
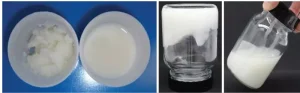
To attain deeper matte radiation-curable wood coatings, the efficient “wetting” of broad pigment varieties is of paramount importance to achieve the lowest gloss and best “hiding” power possible. These dispersants must be compatible in a broad range of commonly used solvents, co-solvents, monomers and oligomers and with a variety of treated and untreated grades of silica(s). To address these demands, advancements in dispersant technology have led to improvements in particle wetting, pigment stabilization and flow in UV coating systems containing silica-based matting agents (Figure 1). Commercially available hyper-branched co-polymer dispersants with pigment affinic groups enable heavy loading of matting agents while enabling Newtonian flow behavior in the coating during both production and application.
How hyper-branched co-polymer dispersants work
Ordinary high molecular weight dispersants (i.e. linear AB block co-polymers) typically provide a defined number of functional groups that support absorption onto the pigment or matting agent particles. However, these high molecular weight linear AB block co-polymer dispersants can be difficult to use in 100% UV or solvent-free coatings because the higher viscosity, associated with the high molecular weight linear structures, can make the dispersants difficult to pour and handle in the manufacturing process. In contrast, the spherical design, with the benefit of additional functional tails of the high molecular weight hyper-branched dispersants, is very well suited for 100% UV and solvent-free systems because it optimizes absorption onto matting agent particles, providing lower processing viscosities and improved Newtonian flow characteristics.
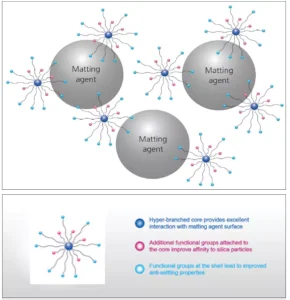
Customized hyper-branched co-polymers with pigment affinic groups work to de-flocculate matting agents by means of steric stabilization (Figure 2A). Steric stabilization can be described as a 3D network of weak intermolecular attractions and repulsions. The anti-flocculation “effect” of the dispersant helps to reduce pigment settling, thereby improving the storage stability of the coating, often mitigating the despised “hard-pack” settling outcome of matting agents left to the natural forces of time, temperature and gravity. Undoubtedly, the most beneficial result of this chemical interaction between dispersant and the de-flocculated matting agents is a Newtonian flow behavior of the now heavily matted coating. Enabling for Newtonian flow provides a significant reduction in processing viscosity and can help to improve the surface leveling characteristics and pigment orientation of the matting agent present in the coating’s film (Figure 2B). These custom hyper-branched dispersant technologies often share the same active ingredient, but whose delivery form (carrier) is modified for use in different coating technologies, such as aqueous, solvent-borne or solvent-free coating systems.
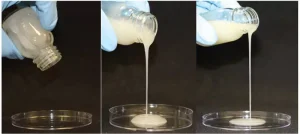
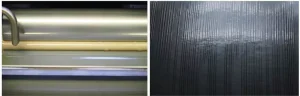
Additionally, during roll-coat application (Figure 3) with heavily matted UV coatings, the use of a hyper-branch co-polymer dispersant can improve silica orientation and flow, which helps to eliminate roller marks or “roping” issues caused by poor flow behavior and leveling on the applicator roll. “Roping” on the applicator roller is detrimental to finish quality, as it transfers to the coated part.
Advantages/disadvantages of silica-based matting agents
UV coatings, especially higher solid and solvent-free UV systems, can be difficult to matte. The higher the resulting shrinkage during film formation, the better the matting efficiency. Therefore, aqueous or solvent-based technologies, like nitrocellulose lacquers or low solids acrylic aqueous emulsions, often are easier to matte. In contrast, high solids, solvent-free and 100% solids UV coating systems can be a challenge to matte due to the very minimal-to-no film shrinkage that occurs during the expedient curing process with UV lamps. Silica-based matting agents are no doubt very effective with matting; however, silica-based matting agents (especially fumed silica) typically are more difficult to handle in manufacturing environments than other matting agent options.
During the manufacturing process, the addition of a silica can cause significant clouds of “dusting” particulates, which can require extra housekeeping and can be a challenge to ensure all silica particles reach their desired location – the manufacturing vessel. Furthermore, as processing viscosities rise, the addition of silica can cause the coating to have a tendency to “climb” up the vertical shaft of the mixer, complicating the dispersion and particle “wetting” process. Additionally, due to the “fluffy,” less dense nature of silica-based matting agents, significant processing time may be required for the addition of powdered silica into manufacturing batches to ensure sufficient particle wetting. Another challenge with low-matte coating formulations that contain surface-treated silica matting agents can be the generation of excessive foam, which may require a higher dosage of defoamer, air release and/or surface additives to correct and may existentially impact the total cost of the formulation.
Other desirable performance characteristics for UV coating
Beyond achieving low gloss stability and improved flow, the heavy pigment loading and rapid cure times associated with UV coatings can present additional challenges to formulators that seek to optimize these coatings. Additional formulary considerations to help address market demands for superior UV coatings may require improved clarity; scratch and abrasion resistance; soft feel effect (haptics); stable defoaming action (during production and application); and superior chemical and stain resistance qualities. In order to meet these special requirements, other additive technologies – like wax dispersions and micronized waxes, and/or mixed mineral technology (MMT) clays – can be used in conjunction with different silica types and hyper-branched co-polymer dispersants to achieve high-quality results.
Considerations for wax dispersions and micronized waxes
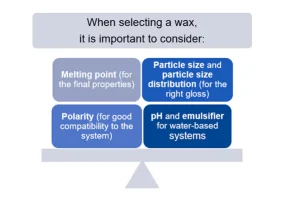
As previously mentioned, silica-based matting agents are excellent for obtaining matting efficiency in ultra- and lower-matte coatings but generally have inferior surface performance characteristics for scratch, mar, stain and chemical resistance when compared to wax dispersions or micronized wax additives. Particle size, polarity and melting point are key factors for the surface performance of a wax. Alternate technologies, such as a liquid wax dispersion or micronized (powder form) wax exist as viable
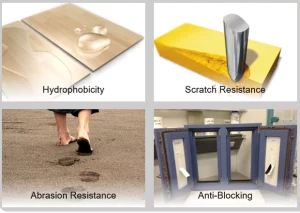
options to complement silica-based matting agents commonly used in UV formulations. These wax additives can provide some additional matting effect, but more importantly, can help significantly to improve mechanical resistance, chemical resistance, scratch resistance, abrasion resistance, water repellency and anti-blocking of a coating by being active at the air/surface interface. It is important to consider the final properties to be achieved (Figures 4A and 4B). Fine particle size micronized waxes in the 5 to 10 micron range that can match those particle sizes of common silica-based matting agents will help contribute to the desired lower optical matting properties.
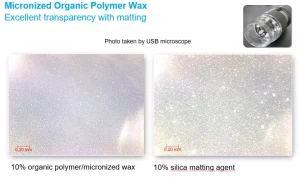
Friendlier “green” technologies and select grades of micronized biodegradable and bio-renewable organic polymer additives exist. The use of “green” organic polymers can be marketed as such, while reducing negative impacts to the environment. Since improved distinction of image (DOI) and optical clarity are desirable features to consumers of wood coatings, new advances in micronized wax technology can help provide superior clarity in coating films when compared side-by-side to silica-based matting agents (Figures 5A, 5B and 5C).
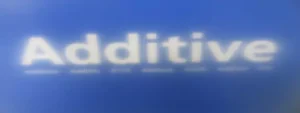
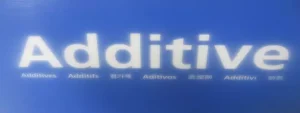
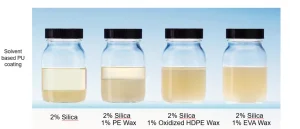
Another common wax-based chemistry for micronized wax products is PTFE (Teflon® containing) wax. Recent European regulatory concerns regarding a substance known as PFOA (perfluorooctanoic acid), which can be present as a processing aid or “emulsifier” in PTFE waxes, currently is listed as a substance of concern. The more PFOA a PTFE wax contains, the easier it is to incorporate. To address regulatory concerns, PFOA-compliant versions now are commercially available. Micronized waxes create a microstructure on the film’s surface that mechanically lowers the CoF (coefficient of friction), improving mechanical resistance and becoming less likely to mar or “burnish.” PTFE waxes provide a strong reduction to the CoF, offering remarkable mechanical and chemical resistance at lower dosages. Taber testing cycles for wear resistance generally are improved. If additional “slip” is not desired (i.e. hardwood flooring applications), larger particle size texturing grades exist. Waxes can impart hydrophobic properties to the film, which ultimately can hinder the ability of stains to penetrate. This hydrophobic benefit ultimately can lead to improved surface resistance to common household stain reagents, such as mustard, red wine, iodine, food dye and permanent markers. Another benefit of micronized wax additives is their ease of incorporation into batches (usually with low to moderate shear forces), with little to no effect on viscosity. Certain grades can produce highly transparent coatings.
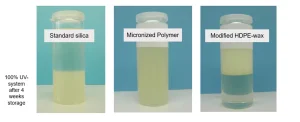
Often polyethylene (PE) and ethylene vinyl acetate (EVA) co-polymer wax additives can help improve and delay the settling tendencies of a coating by keeping the silica from accumulating on the bottom of the container (Figure 6A). Many commercially available rheological (PE) or (EVA) wax dispersions help to improve the orientation of pigments, which positively contributes to the matting efficiency of silica-based matting agents. In summary, wax additives can be a highly effective partner to silica-based matting agents, providing improved surface, matting and rheological control properties (Figure 6B).
Benefits of mixed mineral technology clays for UV coatings
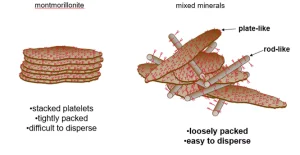
Another matting consideration that helps to provide rheological benefits for use in UV coatings is to incorporate a mixed mineral technology (MMT) additive, sometimes also referred to as a semi-synthetic clay or mixed mineral thixotrope (Figure 7). MMT clays typically have a good performance-to-price ratio, have an affinity for matting and promote a pseudoplastic flow behavior in the coating. Pseudoplastic flow promotes sag resistance and anti-settling in coatings, viscosity in the low shear range and quick recovery from shear forces that deform the fluid’s structure.
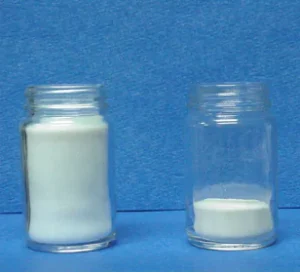
One additional, but very important, feature of MMT clays is the reduction in bulk density as compared to traditional silica matting agents (Figure 8). Due to the heavier particle size density of MMT clays compared to fumed silica, they provide for less “dusting,” which results in improved productivity and increased manufacturing efficiency of a solvent-free coating. Moreover, the use of MMT clays, in comparison to traditional montmorillonite organoclays, offers added performance improvements:
- They do not require a polar activator.
- They allow for easier activation due to the loosely packed platelets.
- They help improve pigment orientation.
- They help to control the flooding and floating of pigments.
MMT clay technology options exist across the polarity spectrum for non-, low-, mid- and highly polar coating systems, and synthetic clay derivatives exist for use in aqueous, solvent-borne and solvent-free UV coatings. MMT clays are chemically stable in coating formulations, as an inert and inorganic material. Furthermore, MMT clays typically provide long lasting viscosity control, as long as other liquid materials contained in the coating (i.e. binders, monomers) do not interfere with the rheological network building process. Interference from other ingredients with MMT clays is rare. However, as best practice, performing a comprehensive ladder study always is recommended when evaluating rheology and/or other additives.
Conclusion
The ongoing advancements to hyper-branched co-polymer dispersant additive technologies play an integral role in the successful development of ultra-low matte UV radiation cure coatings. The ability to achieve and retain Newtonian flow properties throughout the manufacturing process with addition of silica-based or other type matting agents is paramount to achieving low matte coatings. The considerable reduction in viscosity is achieved by means of incorporating hyper-branched co-polymer dispersant technology, which allows for heavier pigment loading of silica-based matting agents. Thus, formulators can achieve low to ultra-low matte coatings with decreased processing viscosities that are capable of being applied using common industrial wood application methods, such as roll-coat or spray-applied finishes.
The performance trade-off in the use of silica is that other matting agent options, like waxes and clays, tend to compromise matting efficiency but do offer other tangible benefits that silica alone cannot provide. Surface enhancement is the operating window where wax additives really shine. Used in conjunction with silica-based matting agents, wax additives help contribute to a matting effect while providing the benefit of improved surface characteristics and manufacturability. Additional considerations for the incorporation of MMT clays in conjunction with the use of silica-based matting agents should be explored in order to optimize the coatings surface and rheological performance properties. To further achieve extraordinary surface characteristics, the use of high-quality defoaming, air-release and surface additives in conjunction with a modern dispersant, wax dispersion, micronized wax, MMT clay or synthetic rheological additive undoubtedly produces a world-class, high-performance UV wood coating. High-performance wood coatings in all sheen variations are aesthetically pleasing to consumers; provide durability, character and uniqueness to wood products; and, most of all, result in customers who are delighted with their purchase – achieving the formulator’s goal.
Mike Toth is the USMCA regional end use manager for Wood Coatings at BYK USA and has management responsibility for the BYK Wood Technical Service Lab in Wallingford, Connecticut. He has 25 years of diverse industry experience in wood coatings and paint additives. Before joining BYK in 2017, he held several management positions at a leading wood coating manufacturer located in High Point, North Carolina. Additionally, he has several years of experience working in a wood coatings laboratory as part of a commercialization team specifically focused on testing and application work for UV radiation curable coatings. For more information, visit www.byk.com.