Editor’s Note: The author is no longer with Momentive Performance Materials. For questions, email rickeckberg@nc.rr.com.
By Richard P. Eckberg, Momentive Performance Materials

Silicone (polydimethylsiloxane) polymers are unique materials that are chemically inert and of low polarity that remain fluid at temperatures as low as -120° C and retain useful properties at temperatures > 250° C for extended times. Cross-linked silicone polymers can be bulk solid elastomers, rubbers, gels and low-surface-energy coatings capable of lightly adhering to pressure-sensitive adhesives and then releasing those adhesives without denigration of adhesive tack. Such coatings are known as release coatings. When applied to paper and film substrates as blends of reactive silicones, then cross-linked to a solid abhesive surface, the resultant silicone coating is the key element of a release liner. Self-adhesive pressure-sensitive labels and laminated label structures were first developed by R. Stanton Avery.1,2 The tag and label industry later adopted large-scale use of silicone release liners as a way of packaging labels from time of manufacture to time of application. A familiar example of a release liner is the silicone-coated paper from which self-adhesive postage stamps are detached. Figure 1 depicts the structure of conventional label laminate. Note that the silicone release coating is very thin relative to the rest of the construction.
Catalytic addition of silicon hydrides to olefins and acetylenes is the basis of manufacture of organofunctional silanes and silicones. This hydrosilation reaction in its simplest form can be depicted as:

Numerous transition metal compounds and complexes are known to catalyze this reaction3, but industrial processes mostly utilize silicone-soluble platinum (II) complexes in homogeneous phase because of the speed and anti-Markovnikov stereospecificity afforded by these catalysts. Most silicone release coatings are applied to paper and film sheet as 100 to 500 cstk viscosity reactive fluid blends consisting of vinyl-functional silicone base polymers and hydride-functional silicone cross-linker polymers with hydrosilation catalysts, inhibitors and other additives present.
Karstedt4 type Pt catalyst is a very reactive silicone-miscible Pt(II) complex in common use for thermal processing of silicone release coating agents. It is necessary to include an inhibitor that slows the curing reaction enough at ambient temperatures to permit coating5; useful inhibitors are volatile and are blown out of the silicone coating in high temperature ovens immediately after application, thus permitting cure. Processing of silicone release coatings at very high speeds (> 1000 meter/min) is practiced, but doing so requires sufficient heat to raise substrate and coating temperatures > 150° C, which demoisturizes paper liners and deforms and degrades film and film laminate liners, leading to liners’ dimensional instability after processing.



The mechanism of Karstedt-catalyzed hydrosilation has been well elucidated; the Chalk-Harrod6 mechanism is widely understood to be a good explanation of how silicone addition cure operates at the molecular level.
The Case for Radiation-Triggered Addition Cure Silicone Release Agents
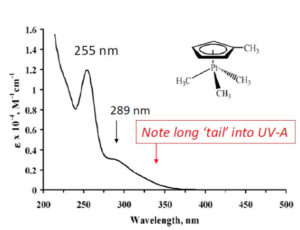
High-speed reliable processing of silicone release liners that takes advantage of Pt(II) catalyzed thermal addition cure chemistry is well established but limits choice of liner substrates to robust paper sheets > 40 lb/ream basis weight that require sufficient heat to reach web temperatures that promote complete cross-linking of reactive silicone polymers. Thermal addition cure chemistry largely rules out use of dimensionally stable thin-gauge polyolefin and PET liners because such substrates degrade and deform at temperatures as low as 110° C. To meet demand for low-temperature curing silicone release coatings, free-radical and cationic type UV-curable acrylate- and cycloaliphatic epoxy-functional silicone polymers and compatible photocatalysts have been developed7,8 and have found commercial specialty market niches. Such coatings require organofunctional silicones that utilize expensive inputs, complex multistep syntheses and silicone-compatible photocatalysts – all of which make these coatings at least twice as expensive as their simple addition cure silicone analogs. In addition, free radical photocure of acrylated silicones runs at commercial speeds only in a rigidly inerted atmosphere (< 50 ppm O2), adding more cost and complexity to processing. To build sufficient reactivity to provide fast photocure into these types of silicone coatings > 15% (w/w) of the polymers consists of polar, reactive non-silicone organofunctionality, which compromises release of aggressive mastic- and acrylic-based pressure-sensitive adhesives. An ideal low-temperature, radiation-curable silicone coating would be a 100% addition curable silicone whose cure is triggered by exposure to UV or EB energy.
UV-Active Hydrosilation Catalysts
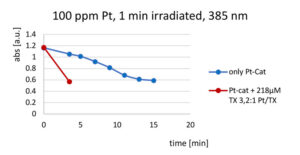
There are numerous accounts of research extant in the literature describing various transition metal compounds and complexes capable of catalyzing hydrosilation reactions upon absorption of incident UV energy3, but the only compounds described that appear fast and efficient enough for possible use in high-speed coating operations for release coatings are certain photo-active Pt(II) and Pt(IV) complexes. Most promising are cyclopentadienyl Pt(IV) compounds. In the 1980s, researchers at 3M patented the use of certain eta-cyclopentadienyl (Cp) platinum (IV) compounds as photocatalysts for hydrosilation9,10 and later expanded the concept to include such Pt (IV) compounds in conjunction with sensitizers to expand the range of input light that could trigger hydrosilation curing reactions11. A subsequent patent describes modified Cp-Pt (IV) compounds that incorporate near UV/VIS light-absorbing functional groups12 with the goal of making an addition cure process amenable to long wavelength UV or visible light activation. Concerns about the volatility of methyl-cyclopentadienyl Pt(IV) trimethyl (MeCpPtMe3) led to attachment of hydrolysable siloxy groups on the Cp ligand13.
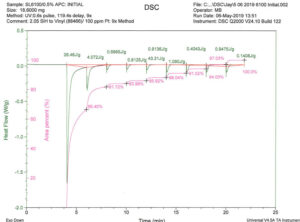
There are three main features of the UV absorption spectrum of MeCpPtMe3: A major UV-C peak centered ~ 255 nm, a secondary shoulder near 289 nm and a long tail extending into UVA region above 350 nm, suggesting that conventional medium pressure mercury vapor UV curing lamps ought to be suitable for photocure of vinylsilicone + hydride-silicone coatings. Given the widespread availability of such lamps and UV cure coating lines equipped with them, as well as the considerable patent literature teaching use of MeCpPtMe3 for photo-hydrosilation, it is surprising that UV-activated addition cure release coatings are not established commercial products. MeCpPtMe3 is used for photo-catalysis of silicone gels and elastomeric conformal coatings,14 but these are thick section slow-curing articles with very low catalyst content requiring long UV exposure times not feasible for high-speed converting operation.
MeCpPtMe3 Photocatalyzed Silicone Processing: Initial Experiments and Observations
Photo-hydrosilation experiments with MeCpPtMe3 were carried out using a model reaction to facilitate analysis15.
ὲ Me3SiOSi(Me)[CH2CH2Si(Me)2OSi(Me)3]OSiMe3
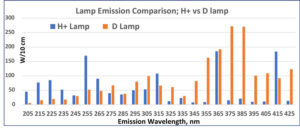
A 2:1 mix of 1,1,1,2,3,3,3 heptamethyltrisiloxane : vinylpentamethyldisiloxane was treated with sufficient MeCpPtMe3 to provide 100ppm Pt, then irradiated with 385 nm LED radiation for 1 minute. The reaction mixture was under N2. Loss of the catalyst 255 nm absorption peak was monitored as a function of irradiance time. The experiment was repeated with sufficient thioxanthone (TX) sensitizer added to provide ~ 30 mole% TX as a function of platinum.
No sensitization effect was observed when this experiment was repeated in the presence of oxygen. When the experiment was conducted tracking the 255 nm catalyst absorption peak after 10 seconds irradiation from a standard medium pressure Hg lamp, rapid initial loss of the absorption occurred followed by a long, slow continuing “dark” reaction. Sensitization was not apparent either inerted or not.
The model study results were consistent with earlier accounts of photo-hydrosilation catalyzed by MeCpPtMe3 but raised concerns that thioxanthones would not be effective sensitizing agents for photocross-linking of reactive silicone polymers in a non-inerted industrial coating operation. Of equal concern was the extent of “dark” reaction that would be considered a “post-cure,” meaning that cross-linking continues long after exposure to UV energy.
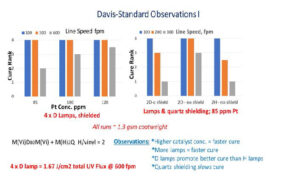
Hydrosilation is an exothermic process with a high heat of reaction of 28 kCal/mol16 so photo-catalyzed hydrosilation is amenable to photo-DSC experimentation. Accordingly, representative coating formulations consisting of vinylsilicone and hydridosilicone polymers were treated with MeCpPtMe3 catalyst, then samples placed in a TA Instruments photo-calorimeter and irradiated with filtered UV energy in the 280 to 400 nm range that includes much of the catalyst absorption range.
Note that the initial exposure results in ~ 66% of total Delta H of available reaction. Five additional UV flashes were required to achieve > 90% cross-linking.
MeCpPtMe3 Photocatalyzed Silicone Processing: Optimization Experiments
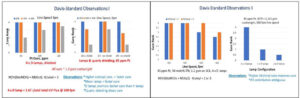
Following the initial lab studies, we began trials of addition cure silicone release coating formulas using a pilot UV processor at Heraeus Noblelight’s experimental facility in Gaithersburg, Maryland. The experiments consisted of making hand drawdowns of candidate catalyzed silicone coatings on sheets of VersoTM SCK paper liner substrate, then passing the coated sheets on a conveyer under one or two focused microwave-fired mercury vapor lamps. Coatings were then evaluated for silicone transfer to, and detackification of, 3M #610 cellophane tape (evidence of incomplete cure), obvious finger smear, and rub-off from the substrate. Cure was defined on an arbitrary scale of 0 to 4, with 0 = no cure (wet) and 4 = well cured (no migration, no smear, good anchorage). Commercial release coating cure of at least “3” is a promising result. Coating variables included catalyst concentration, SiH/vinyl molar coating ratio, anchorage additive, sensitizer content; processing variables included lamp choice, lamp reflector type and conveyer speed. Achieving a cure score of 3 or 4 under one curing lamp at 200 fpm conveyer speed was a goal of these experiments.
There is a significant “red shift” in spectral output of an iron-doped mercury D lamp versus the conventional medium-pressure mercury vapor bulb, so we felt it worthwhile to compare cure response as a function of lamp type, since the absorption spectrum of MeCpPtMe3 trails well into the UVA region. Our results are summarized in Initial Screening Results, page 51.
We were surprised by the significant improvement in cure speed provided by use of a D lamp in place of the H lamp. Additional improvement is provided by use of dichroic reflectors used to filter out IR frequencies. When well cured, all coatings tested OK as release coatings, but quantitative degree of cure could not be assessed.
The next set of experiments was run as coating trials on the five-roll pilot differential coater at the tandem coating lab of Davis-Standard LLC, Fulton, New York. Candidate silicone coating formulas were applied at ~ 1 to 1.3 g/m2 coatweight (~ 1 to 1.3 micron thick) onto Verso SCK paper liner sheet. Vinyl silicone polymers and hydrido silicone cross-linking polymers were mixed with MeCpPtMe3, anchorage additive and isopropylthioxanthone (ITX) sensitizer.
The pilot coating lines at Davis-Standard LLC are equivalent to commercial converting operations in terms of silicone coatweight control, line speed and ability to apply silicone release coating to a wide range of substrates. The observed photocure of hydrosilation cross-linked silicones at near-commercial line speeds was promising, but the requirement of four sets of microwave-fired D lamps delivering a total of 1.7 J/cm2 UV flux (at 600 fpm line speed) to these coatings to overcome an inherent slow activation of MeCpPtMe3 catalyst is an expensive fix. Additional trials at Davis-Standard were subsequently carried out to determine how to further improve photoresponse of the system and to acquire quantitative degree of cure data.
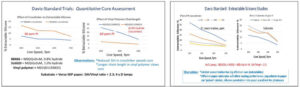
Extractable silicone is a precise determination of uncross-linked silicone extant in a release coating after processing. It is measured by immersing a precisely sized sample of the coated substrate in a precisely measured amount of methyl-isobutyl ketone for > 24 hours, then using AA spectroscopy to measure silicon content of the extractant solvent. The AA result translates to % of uncured silicone extracted. Industry requirement is typically 5% maximum from a liner within a few minutes of cure. Greater than 10% extractable silicone results in backside transfer of silicone on rewind and indicates likely loss of adhesive tack from PSAs laminated to the liner.
Dual Cure: Key to MeCpPtMe3 Photocatalyzed Silicone Release Coatings?
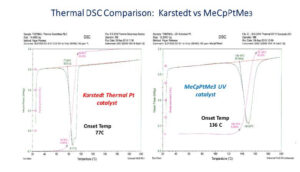
An assumption underlying the project to develop photo-activated addition cure silicone release coatings is that MeCpPtMe3 photocatalyst is strictly a photocatalyst that is stable at ambient conditions in a reactive silicone coating formulation including vinyl- and hydrido-silicone. But thermal DSC traces of identical polymer blends catalyzed by inhibited Karstedt and inhibitor-free MeCpPtMe3 catalysts demonstrate that the photo-active compound also acts as a thermal catalyst for hydrosilation
(Figure 8).
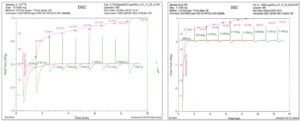
These DSC results show that, while MeCpPtMe3 is a very stable catalyst kept in the dark at 25° C, it will function as a thermally activated hydrosilation catalyst at sufficiently elevated temperature. This observation is consistent with studies of the mechanism of CpPtR3 catalysis of hydrosilation showing that absorption of light leads to breaking a strong sigma bond between Pt and alkyl ligands with loss of alkane to open the Pt coordination sphere17… a slow rate determining step that may account for long post-cure versus Karstedt complex. We next ran simple isothermal photo-DSC studies (as described previously) of the most favorable coating blend per the Davis-Standard trials at different temperatures to see how heating the coating affected photoresponse. Two photo-DSC traces of the same 50 ppm Pt formula irradiated as illustrated in Figure 4 are depicted in Figure 9. Note that initial 0.6 second UV exposure results in < 50% cross-linking at 25° C but provides ~ 85% cross-linking when the coating is heated to 70° C. Repeating this Photo-DSC experiment at intermediate isothermal conditions between 25° C and 70° C confirmed that coating temperature is directly related to speed of cross-linking.
Conclusions and Prospects
Photo-activated hydrosilation of reactive vinylsilicone + hydridosilicone polymers is catalyzed by cyclopentadienyl-Pt(IV) alkyl complexes, most notably MeCpPtMe3, but a UV-curable silicone coating system based on this catalyst requires very high UV flux and optimal substrate selection and may only be suitable for certain specialty silicone release coating applications. Our studies have shown that favorable combinations of vinylsilicone and hydride-functional silicone polymers, coupled with certain types of curing lamps, provide the best performance at realistic catalyst concentration. The next step in this project will be to combine a mild heat stage with UV irradiation. Temperatures in the 75° C to 100° C range will not degrade film or paper substrates if such conditions enable rapid, complete photo-cross-linking on exposure to two banks of lamps on high-speed coating lines – a dual-cure means of manufacturing new types of thinner, dimensionally stable premium release liners will be realized.
References
- S. Avery, US Patent 2,304,787 (12/15/1942)
- S. Avery, US Patent 2,783,172 (2/26/1957)
- R. Hofmann et al, Polymers 2017 (9), 534
- B. Karstedt, US Patent 3,715,334 (2/6/1973)
- R. Eckberg, US Patent 4,256,870 (3/17/1981)
- A. Chalk and J. Harrod, J. Amer. Chem. Soc. 1965 (87), 16
- O. Pinto et al, US Patent 6,548,568 (4/15/2003)
- R. Eckberg et al, US Patent 4,279,717 (7/21/1981)
- T. Drahnak, US Patent 4,510,094 (4/9/1985)
- T. Drahnak, US Patent 4,600,484 (7/15/1986)
- L. Boardman et al, US Patent 4,916,169 (4/10/1990)
- M. Butts, US Patent 6,451,869 (9/17/2002)
- A. Koellnberger US Patent 8,088,878 (1/3/2012)
- SiloprenTM UV Cure Silicone Elastomers (Momentive Performance Materials)
- T. Holzel, Master’s Thesis Universitat Dusseldorf 2016
- Silicone Surfactants, Randal Hill, Ed., Marcel Dekker, New York 1999
- Jakubek and Lees, Inorg. Chem. Comm. 2004 (43), 6869