
By Namgoo Kang, Ph.D.; Ken Myers; Mark Adams; Andrew Sandt and William C. Miles, Ph.D., Penn Color, Inc.
The adhesion of energy-curable coatings is a subject of great interest, particularly for substrates that are low energy (i.e. plastics) or in the joining of substrates with different surface energies.1 Advantages of energy-curable coatings are that they often are very durable, can be rapidly applied, provide high scratch and mar resistance and do not contain volatile organic compounds (VOCs). The challenges associated with energy-curable coatings often are ones of adhesion. Often, one formulation cannot work for multiple substrates, which means that formulators are left to design systems that work for a specific substrate.2
Sometimes pre-treatment is required to get the energy-curable coating to bond, adding capital and processing costs.3 Additionally, lamination of surfaces after coating with an energy-curable coating can be a significant challenge, much more significantly than with a solvent or water-based coating that has much more thermoplastic character and so can contribute to bond strength between the laminated layers.4 Adhesion is a complex mixture of physical and chemical forces, the understanding of which can lead to failure or success of a coating. Additionally, the components of the coating can impact performance as shrinkage rates, photoinitiator wavelength of activation and ductility of the film can play key roles in whether a film can withstand the rigors of the application for which it is designed.4
Typically, adhesion issues are addressed in three main ways. First, the surface is cleaned to ensure that there is a uniform surface for which the coating will be applied. Often this is done through a plasma or corona pre-treatment. The advantages of this is that the surface is uniform every time the coating is applied. The disadvantage is that the treatment adds costs, both from a capital expense but also from a processing standpoint.5
The second way to address adhesion issues is to increase the interaction of a formulation with the surface. This is typically done by adding a surfactant to match the surface tension of the substrate, allowing the maximum amount of surface contact between the substrate and the formulation prior to cure. The advantage of this method is that it can be designed specifically for the substrate, though that is also a disadvantage in that it is not always applicable to each substrate.6
The third way to address adhesion issues is to incorporate an adhesion promoter into the formulation. Adhesion promoters typically work by forming a chemical bridge between the coating and the substrate, the idea being that surfactants and pre-treatment address maximizing surface area while the adhesion promoter addresses actually getting the material to stick. Often these materials work very well, but again there are limitations based on the type of substrate for any one adhesion promoter.7
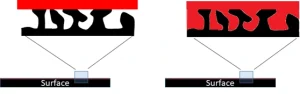
One way that often is talked about to enhance adhesion but not often quantified is the mechanical interlocking of the curable coating with the substrate. Every substrate – no matter how smooth – has some degree of surface roughness. If the coating can be driven down into the pores of the substrate, the surface area of the coating/substrate interface can be maximized, as shown in Figure 1. Additionally, shrinkage of the coating then should aid adhesion rather than being a detriment, as the film would tighten at the interlocking points rather than pulling away from the substrate.
The issue with designing systems that utilize this interlocking mechanism is that there are opposing capillary forces that prevent coatings from infiltrating these “pores” fully.8 Surfactants can be added to aid this infiltration, but often this isn’t enough, even with precise rheological control of the film. It certainly is not universal as a surfactant is specific to the surface energy of the substrate.
The work in this paper shows a different mechanism for providing this interlocking mechanism. Here, the authors present evidence that it is possible to develop a polymeric material that will increase infiltration into various substrates based solely on the polymer architecture and design. The authors further present evidence that the force imparted by the polymer design is surface agnostic – i.e., it does not rely on surface energy or cleanliness to force its way into the pores of the substrate – and so gives a formulator significant latitude to make formulations that give good adhesion on multiple substrates.
Experimental
Synthesis
The synthesis of functional copolymers was carried out according to US patent (US 9,441,123 B2).9 The synthesis method can be tailored to give brush-like copolymers with diverse functional groups in the polymer backbones and side chains. Different concentrations of the monomers were added to control the functionality in the resulting copolymers. The copolymers examined in this study consisted of ratios of 13.5% and 27% branching to backbone by weight. The composition of the backbone used in these experiments was predominantly vinyl alcohol, with alcohol-based functional groups used to attach the branches, mostly made up of acrylic functionality.
Surface Force Characterization
Surface tension and contact angle measurements were conducted using an Attension Theta surface tensiometer. Surface tension measurements were conducted using the pendant drop method with a Teflon pipette tip to minimize any surface interactions between the solution and the tip. Contact angle measurements were conducted on injection-molded polyethylene terephthalate (PET) chips, with the results reported an average of measurements of droplets at three different locations. Figure 2 shows the surface tension and contact angle of the branched polymers in emulsion form compared to a linear polymer with amine functionality at a similar ratio.
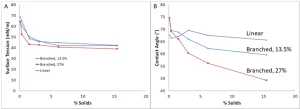
Figure 2 shows that the surface tensions of the branched polymers and linear polymer are virtually identical as the polymer concentration in water is changed. However, there is a marked difference between the contact angles of each of these components when deposited onto PET chips. Because surface tension is a physical property measurement, while contact angle is an application-specific measurement, this suggests that there is a difference between the way the resins act with themselves and when they are put on a surface, with the branched polymers more adept at wetting out a surface. Indeed, one observation made during the surface tension measurements was that when using a polypropylene tip for the measurements, the branched polymers would not form a droplet, but would rather migrate up the pipette tip. That was the reasoning for using a Teflon tip for the measurements and suggests that there is a non-surface tension-related force generated by the branching.
Emulsion Application Testing
While not energy-curable specific, application testing of these materials as emulsions does give some insight to their versatility as well as the properties brought to bear by the branched architecture. For the first of these tests, emulsions were mixed with a paraffin wax containing a carbon black colorant above the melt temperature of the wax (130° C). The 13.5% branched polymer and the linear polymer were incorporated into the wax at 10 weight percent solids and the water was evaporated off. The wax then was cast into a writing utensil and the resulting samples were compared to wax containing no polymer.
Figure 3 shows the difference in efficacy between the control, linear polymer and branched polymer samples when rubbed on both polypropyelene and PET. This same effect was seen on steel, glass, high density polyethylene, an energy-cured substrate and other smooth surfaces.
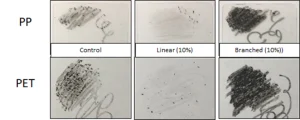
The control deposited on most surfaces decently, but then rubbed itself off as the sample was pressed into the surface with more force. The sample containing the linear polymer did not deposit on any surface well at all and rubbed off easily when more force was applied. The sample containing the branched polymer not only deposited on all of the surfaces easily, but it became darker as more pressure was applied.
This suggests that the polymer may be helping the wax adhere to the smooth surface, allowing it to build over time rather than being rubbed off with additional force. An interesting observation is that this adhesion appears to be surface agnostic. Because the effect is seen with all surfaces, this again suggests this isn’t a surface energy phenomenon, but rather something specific to the polymer being used. This further was confirmed by adding the branched polymer (13.5%) to a polyvinyl alcohol adhesive at 10% solids loading. The same mass of adhesive with and without the branched polymer was applied to a glass slide and then an injection-molded polypropylene chip was pressed on top of the glass at a controlled pressure for 24 hours.
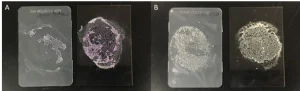
Figure 4 shows that the control sample had an adhesive failure, as after the samples are pulled apart, the majority of the adhesive is only on the glass slide. However, the incorporation of the branched polymer to the adhesive changes that to a cohesive failure where the actual glue is failing, rather than the adhesion to the substrate. This is clearly illustrated by the adhesive remaining on both the polypropylene and glass surfaces.
Energy-Curable Application Testing
The powder version of the branched polymer was incorporated into energy-curable formulations to test adhesion to various substrates, specifically PET and a previously cured UV coating. Solubility of the powder was limited (<1%) in various common energy-curable components unless it first was solubilized in a low molecular weight monomer such as butyl methacrylate (BMA, 99.9%, TCI America) or 1,6-hexanediol diacrylate (HDODA, technical grade 80%, Millipore Sigma). Once the material was solubilized into these monomers, it easily could be incorporated into various formulations in excess of 15 weight percent.
In the first example, the branched polymer was put into a proprietary UV-curable formula consisting of 15 wt% branched polymer. The proprietary formula does contain a difunctional urethane acrylate, which was substituted out for the branched polymer. The formulation was tinted with a red UV-compatible pigment dispersion to enhance the ability to see the effect of the polymer in the application tests. A blend of phenylketone and benzophenone initiators (3.5 weight percent) was used as the primary initiator in the formulation, with a phosphine oxide (1.5 weight percent) used as the second initiator.
Films of the formulas – a control without the polymer and a sample containing the polymer – were drawn-down onto PET films using a number 26 wet film applicator rod. The film then was UV-cured by passing through a mercury arc lamp with a primary emission wavelength at 365 nm, with secondary emission peaks at 315 and 440 nm at 40 fpm five times. The maximum intensity range for the UV stations was between 300 and 500 watts per inch. The resulting films were shiny and hard, with no material transfer or tackiness upon touching. The films then were tested using crosshatch tests, following the methods described in ASTM D3359.
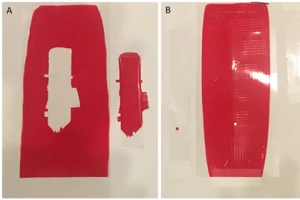
Figure 5 shows the crosshatch results from these tests and the enhancement of the adhesion with the branched polymer added. There is complete adhesive failure of the film that does not contain the branched polymer powder. However, the performance with the branched polymer is considerably better, only having one small square removed from the
PET film.
The films then were examined after being cross-sectioned using a Zeiss Axio Imager.A2m optical microscope with an Axiocam 305 color camera at 200X magnification. Following cross-sectioning, the films were stood on-end and clamped in place to get a full view of the interface between the film and the surface. Figure 6 shows these cross-sections, and what is apparent is that there is delamination of the coatings from the PET film in both situations (the black space between the white film and the red coating). However, for the sample containing the branched polymer, there are places where delamination did not take place. Additionally, that sample has a much more variable interface than the control sample. This suggests that the branched polymer may be enhancing adhesion through the mechanical interlocking mechanism discussed above.
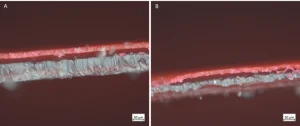
The branched polymer then was added at 1.8 wt % to a proprietary black UV-curable formulation. This coating needed to be able to stick to a previously cured UV coating containing a silicone acrylate to increase slip. In this case, a white coating was used to ensure high levels of contrast.
The white coating was drawn down on a glass substrate using a number 26 wet film applicator rod. The coating then was UV-cured exactly as described above in the previous example. The resulting coatings were shiny and hard, with no material transfer or tackiness upon touching. The black coating was applied in the same fashion after the white film was completely cured. Here, the black coating used a phosphine oxide-type initiator at 3 weight percent in conjunction with a phenyl ketone initiator at 2 weight percent.
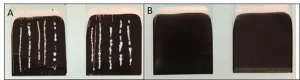
Figure 7 shows the effect of adding the branched polymer to the formulation, even at a small percentage. The cured black film shown in Figure 7A scratched easily with the H hardness pencil, uncovering the white coating underneath and sometimes even removing the white from the glass directly. The cured black film shown in Figure 7B containing the branched polymer did not show any failures at the same H hardness level.
Conclusions
It has been shown that adhesion can be increased on multiple substrates for multiple formulations just through the incorporation of a branched polymer. The structure of the polymer and the degree of branching all play a role in the degree and ability of the polymer to aid adhesion. This increased adhesion has been seen from both a water-based emulsion of the polymer as well as the isolated polymer powder.
There is evidence that the material causes wetting in a way that is surface-tension independent, meaning that there is a force imparted by the polymer that aids wetting and surface roughness penetration regardless of the substrate. This allows the branched polymer to be utilized for both high and low energy substrates, and potentially to join surfaces with large surface energy differentials. Because of this – and microscopic evidence – the authors believe this increase in adhesion may be due to increased mechanical interlocking at the surface.
Particularly for energy-curable coatings, there is visual evidence that cured films have more roughness when cross-sections are examined, indicating that the film has much more intimate contact than a typical energy-curable coating. This provides a different mechanism for increasing adhesion than improved wetting through surfactants or chemical bonding through the addition of an adhesion promoter. This could be a powerful addition to a formulator’s toolbox given the ability to take a formulation that fails catastrophically and make it perform to a potential customer’s specifications.
For more details, contact Nicolas Rivollet at nrivollet@penncolor.com.
References
- “How to improve adhesion to a substrate.” 2020, https://adhesives.specialchem.com/selection-guide/adhesion-promoters-adhesives-sealants.
- Stecher and Mills, “Improving the adhesion of UV liquid and powder coatings using plasma treatment.” UV+EB Technology, 2015, https://uvebtech.com/articles/2015/improving-the-adhesion-of-uv-liquid-and-powder-coatings-using-plasma-treatment/.
- Gururaj, Subasri, Raju and Padmanabham, “Effect of plasma pretreatment on adhesion and mechanical properties of UV-curable coatings on plastics.” Applied Surface Science, 257 (9), 4360-4364.
- Nunez, McMinn and Vitas, “Barriers to the use of radiation-curable adhesives in the coated and laminated substrate manufacturing industry.” Journal of Hazardous Materials 45 (1996), 59-78.
- Weissberg, “Achieving adhesion of UV and EB cured materials to plastics.” RadTech Application Note, 2006.
- Rebros, Fleming and Joyce, “UV-Inks, substrates and wetting.” Proceedings of the 2006 TAPPI Coating and Graphic Arts Conference, April 24-27, 2006, Atlanta, GA.
- Banton, Casey, Maus, and Carroll, “Adhesion promotion for UV coatings and inks onto difficult plastic substrates.” Coatings World, 2018, https://www.coatingsworld.com/issues/2018-07-01/view_features/adhesion-promotion-for-uv-coatings-and-inks-onto-difficult-plastic-substrates/.
- Jang, Sun, and Santamarina, “Capillary pressure across a pore throat in the presence of surfactants.” Water Resources Research, 52 (2016), 9586-9599.
- Spiegel and Rybny, “Cationic water based polymers for ink, coating, and film applications.” US9441123B2, Granted September 2016.