By Dr. Kai Yang, Evonik Corporation, USA; Tommy Gu, Evonik Corporation, Singapore
In recent years, matte finish has become one of the very popular finishes for consumer products in the graphic arts industry. Many different matting agents – such as silicas, waxes, organic materials and fillers – have been developed, with different manufacturing processes, treatments and particle sizes to achieve the desired matte effect.1 One of those processes – using UV/EB curing systems – has a challenge in that the amount of matting agent needed to achieve a certain gloss level would be significantly higher than waterborne or solventborne chemistry, due to the lack of film shrinkage.2-4 With the high loading of the matting agent, it is even more important to choose the matting agent(s) with good gloss reduction while maintaining acceptable viscosity for printing presses.
Two principally different process technologies are used for the manufacture of silica: One is the thermal process which leads to pyrogenic silica, while the other is the wet process yielding precipitated silica, silica gel or silica sol. In general, silicas are hydrophilic after formation and could be treated with different chemicals to turn the surface into a different level of hydrophobicity. The most common treating agents are organosilicon compounds.
The focus of the article is to compare a series of products – from matting efficiency and storage stability to viscosity impact and rub resistance – and show the benefit of a novel sphere-shaped silica particle introduced to further improve the performance of the matte coating and increase the block resistance and scratch resistance without too much impact to viscosity.
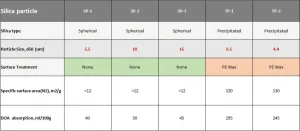
Table 1 outlines the typical physical properties of the spherical particle included in the study. With the novel continuous recirculating reaction, the spherical particle-type silicas have shown unique morphology compared to traditional fumed or precipitated silica matting agents. Other particles used in the study have been listed in Table 1. It can be seen that the specific surface area and oil absorption of these novel spherical particles are significantly lower than traditional matting agents, which minimizes the viscosity impact of particles within the ink and overprint varnish (OPV) formulation.
The matting effect is achieved by the reflection and deflection of the light, where particle size and surface roughness play a very important role. In general, a larger-particle-size matting agent could lead to a lower gloss unit compared to a smaller-particle-size product at the same loading. However, most flexographic and gravure printing with a rapid print speed produce a film thickness as low as 2 to 3 microns. This could lead to a very uneven surface for finished products if the particle size is too large. At the same time, the large particle also could stick at the doctor’s blade, which creates a streaking effect on the product in the printing process. This is one of the key reasons SP-1 and TP-1 were chosen as the main testing products in this study.
Results and discussion
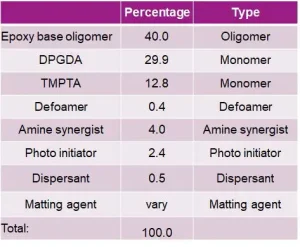
Experiment
Matting agents and novel silica particles are all added at varying levels. Matting efficiency, viscosity impact, rub resistance and stability have been evaluated. The formulation used in the study is noted in Table 2. The OPV film was printed with an RK Proof Coat Instrument’s proofer with 9 um wet film thickness at a speed of 5 onto coated black Leneta chart (initial gloss is 85 at 60°). The drawdown then was cured by mercury lamp at a speed of 7 to 8 meters per minute.
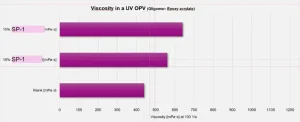
One critical factor in formulating matte UV OPV is the viscosity buildup from the matting agent, especially at a higher level, mainly due to the interaction between the matting agent and the oligomer/monomer in the system. Oil absorption is a detrimental property to consider when choosing the matting agent, and the high viscosity could significantly impact the application and overall appearance of the coating. Figures 1 through 4 review the viscosity impact of silica particles on the coatings. Figure 1 showed the viscosity change with the addition of SP-1, where the minimal impact could be observed even when the loading went as high as 15% wt.
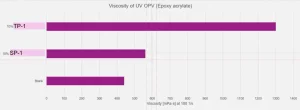
The comparison between SP-1 and TP-1 is reviewed in Figure 2, where the impact of viscosity with TP1 is much higher at 1300 mPa s, which makes the coating much harder to handle. With the graphic arts industry leaning toward the deep matte effect, customers are not satisfied with the gloss unit at 20 anymore. It could be seen from Figure 3 that SP-1 is not able to create the same level of matte effect by itself with the same loading compared to traditional matting additives. Using it alone could be difficult despite minimal viscosity impact.
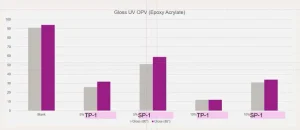
Gloss level and viscosity results summarized in Figure 4 described the use of SP-1 as the matte booster together with TP-1. Even though the gloss unit achieved by 7% TP-1 and 5% SP-1 is only a little bit better than 10% TP-1 by itself, the viscosity is less than half of the single TP-1, which could be a huge benefit for operation.
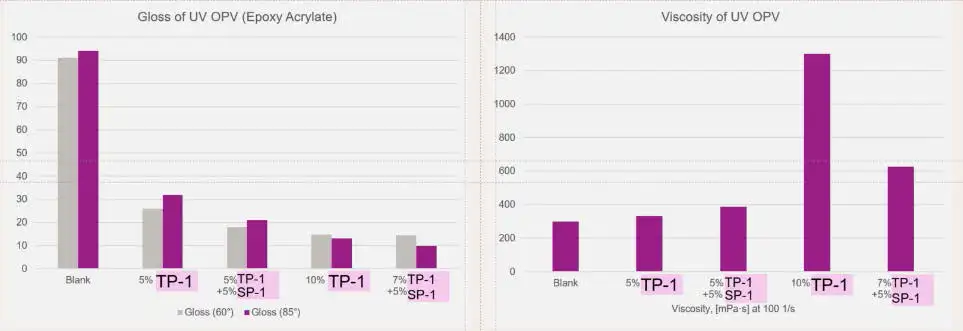
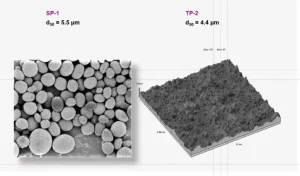
Figure 5 shows the morphology difference between novel silica particle technology and traditional precipitated silica, observed using a scanning electron microscope. One of the main reasons for the poor rub-resistance performance of matte OPV is that the micro-roughening surface easily could be damaged during the surface interaction. The spherical-shape particle could help protect the surface roughness from amorphous silicas, which leads to better rub resistance or burnish resistance. It could be seen from Figure 6 that 7% TP-1 + 5% SP-1 showed better rub resistance with 15um grits polishing paper for 150 rub cycles despite comparable gloss unit.
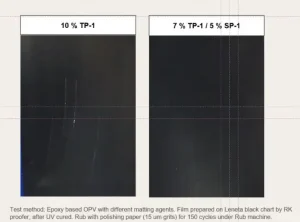
The low oil absorption offers great benefits, such as low viscosity impact and minimal binder absorption; it also impacts the shelf life of the silica suspension in the formulation. After storage for four weeks under ambient temperature, it could be seen from Figure 7 that SP-1 showed the most noticeable phase separation, while both TP-1 and TP-1 + SP-1 continue to show very uniform suspension. This could be explained that amorphous silicas provide enough interaction with the oligomer/monomer to help spherical particles against flocculation and ensure the long-term usability of the coating.
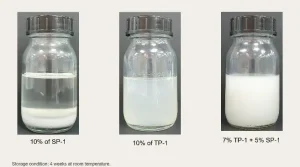
With the globalization trend and rapid growth of market need for food packaging ink, global inventory registration and food contact regulation become more important in the current market. The novel spherical-shape particle offers great food contact compliance with the regulatory entities listed in Figure 8, where it possesses favorable status on most widely used regulation globally.
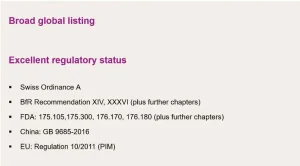
Conclusions
Matting finish is a complicated process with many factors. The end-user result could be impacted by oligomer and monomer usage, initiators, matting agents and other additives, like defoamers/deaerators. The ideal matting agent should provide a good matting effect with acceptable particle size. In UV-/EB-curing formulation, the surface-treated silica is the preferred product, since outstanding stability can be achieved while maintaining a good viscosity for printing applications. The work demonstrated in this article highlights the novel spherical particle represented by SP-1, SP-2 and SP-3 and showed great market potential. SP-1, with its more attractive particle size and stability, provided a new tool for UV/EB formulators in graphic arts to achieve a deep matte finish together with outstanding burnish and scratch resistance.
References
T.E.Fletcher, “A simple model to describe relationships between gloss behaviour, matting agent concentration and the rheology of matted paints and coatings,” Progress in Organic Coatings, Volume 44, Issue 1, March 2002, 25-36
M. Nargiello, “Novel Matting Agent for Low-Gloss UV Coatings,” Paint & Coatings Industry, 2011
Petry, V., Kent, D. “The effect of UV-curable formulations and matting agents on lacquer properties.” Surface Coatings International Part B: Coatings Transactions 87, 103–109 (2004).
I. Calvez, “Low-gloss UV-curable coatings: Light mechanisms, formulations and processes – A review,” Progress in Organic Coatings, Volume 171, 2022, 107039, ISSN 0300-9440.