By Liz Stevens, writer, UV+EB Technology
Vampire Optical Coatings Inc., Pataskala, Ohio, designs and manufactures coatings and coated films to control light reflectivity, refractive index and static electricity, and also to increase surface hardness and mar resistance and to prolong the life of outdoor plastics. Customers served include integrated circuit manufacturers, touch panel producers, ITO coaters, transit authorities, display manufacturers, and flexible and printed electronics companies. For the medical space, Vampire produces UV-cured multi-layer film products used as tear-away protective sheets for full-face respirators, as well as UV-cured electro-static dissipative coated film used to protect touchscreens.
Vampire’s ProtecTuff™ MLF is the basis for an array of unique multi-layer peel-away PET film products. These products range from multi-layer tear off films for racing helmets and goggles to protective covers for full-face respirators and powered air purifying respirator (PAPR) systems. The beauty of these multi-layer products is that when a full-face respirator’s transparent screen becomes soiled or scratched, the user can simply peel away the topmost protective layer of ProtecTuff™ MLF to quickly restore crystal-clear visibility and expose a new undamaged scratch and abrasion resistant surface. As an example, when used as the protective lens system for sand blasting helmets, ProtecTuff™ multi-layer film delivers improved optics and significantly longer life for each protective layer when compared to the incumbent products in that industry (Table 1).
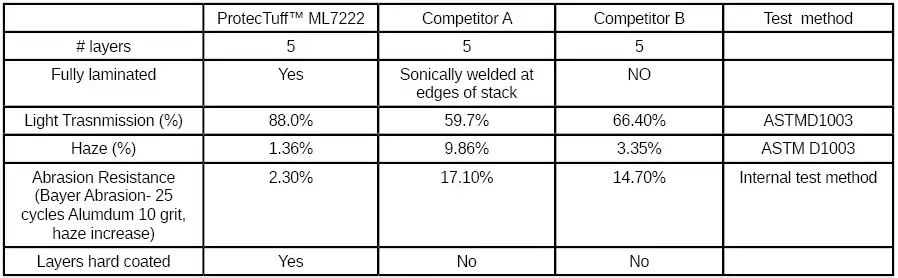
The company’s CEO, Tom Faris, described a key feature of ProtecTuff™ MLF. “The PET films are coated with UV-curable resin,” Faris explained, “laminated while wet and cured together to create a bond between the layers.” The film is pre-treated so that, in a sandwich of many layers of films and resin coatings, the resin bond is stronger toward the film layer below it than to the film layer above it. This allows the topmost layer of resin and film to be easily removed from the layer below.
The impetus for developing ProtecTuff™ MLF came from an effort to design a better anti-graffiti film. “We created the multi-layer product in an attempt to produce a replacement for 3M multi-layer anti-graffiti film,” said Faris. “While 3M’s product requires separate coating steps for pressure-sensitive adhesive application and hard coating, our product accomplishes the same thing in a single, unique, patented step. ProtecTuff™ has no air gaps to collect dirt or reflect light since we bond the films and apply the abrasion resistant coating in a single step.”
ProtecTuff™ MLF is produced using a roll coater with in-line traditional arc UV lamps and comes in 1,000-foot to 1,500-foot rolls. The prime layer of each film is pre-treated via corona discharge and commercial chemical print receptive treatments. “The resin coating,” Faris said, “is applied to the treated side of the PET film. This film then is married to another layer of treated film using pressure lamination, followed by UV curing through the films to effect cure between the films.” The dual layers of film can be stacked and bonded to create up to seven layers of removable protective film, which can be laser cut or diecut into shapes for full-face respirators.
IM-ESD 707 Coated PET is Vampire’s UV-cured electro-static dissipative film product, available in rolls or sheets. It has a permanent non-humidity dependent ESD surface that is abrasion and scratch resistant and is useful for reducing damage to the surface of touchscreens, displays and cleanroom surfaces. This film has three layers – a print treated surface, a 7-mil PET film and an ESD coated surface.
“The ESD coating,” Faris explained, “is an antimony tin oxide nano-particle-filled UV cure coating. The priority is the selection of UV materials/nano-particles to give a coating with enough conductive particles to have 10^5 to 10^9 ohms/sq surface resistivity while remaining clear with high light transmission and low haze.” It is produced via flow coating, dip coating and roll coating, using microwave lamps and traditional arc lamps for UV curing.
Vampire Optical Coatings also manufactures UV-curable anti-fog coatings, traditional UV-cure abrasion-resistant coatings and UV-cure formable hard coatings that allow coated flat sheet products to be formed into motorcycle windshields, UTV windshields and other products that require 3D parts with abrasion and chemical resistant functionality.
For more information, visit www.v-coat.com.