By Dianna Brodine, managing editor, UV+EB Technology
Supply chain constraints have impacted every market segment, and those utilizing UV- and EB-curable chemistries are no exception. Reduced global manufacturing capacity and output due to COVID-19 have reduced component availability; weather impacts have further tightened chemical supply concerns; and infrastructure issues in shipping, rail and trucking transportation have created massive congestion. In a plot twist that normally would be good news, unforeseen increases in consumer demand have strained the supply chain further.
It’s not possible to put a Pollyanna spin on this – the global economy is facing challenges due to manufacturing’s inability to meet current demand. However, there’s also no need for panic. Everyone is in the same boat (and the joke could be made that the boat is waiting at a port somewhere). There’s an opportunity here to develop deeper relationships with supply partners and to acknowledge issues that could have an American-made solution. Perhaps this is the moment where the many links in the UV- and EB-curing circularity begin to remove some dependence on single-source supply?
Global Supply Chain in Flux
“Most companies, like allnex, have contingencies in place to get through some level of disruption,” said Chris Puccio, RADCURE Business Directors Americas, allnex. “This current situation is like nothing we have ever seen. Typically, the global supply chain can absorb some of the issues we have seen – weather delay, force majeures, production delay, mechanical issues, port delays and carrier availability. What we saw was all these issues occurring in a similar time frame, along with strong demand and very low inventories. There was just no buffer to absorb the impact.”
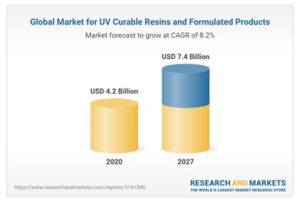
The collision of these multiple factors has caused ripples – or earthquakes – in typical purchasing habits. Joe Chiaramonte, vice president, Sales and Marketing for Coatings & Adhesives Corporation, said, “Our purchasing philosophy has always been to align with suppliers that could offer three main criteria: sustainable source of supply, quality and timely service, and pricing in line with market conditions. These shortages we are currently working through have caused customers to question purchasing habits, and many are now talking about expanding and diversifying their purchasing decisions for consumables.”
Details abound as pundits scramble to explain the current supply chain situation ahead of a holiday season that will ensure all consumers are paying attention. The following factors all are in play:
Infrastructure. Shipping is a global issue for supply chain delivery, but the United States has additional challenges in that its infrastructure of ports, railways and trucking companies is a patchwork of many private companies, resulting in a system that is not linked and does not share data. As far back as 2015, congestion already was being reported at ports and in the intermodal systems. As fall 2020 arrived, these issues were compounded. “COVID-19 caused large shifts in demand and capacity that has resulted in massive supply delays throughout the world’s supply chains, most evident at ports – particularly on the US West Coast, but also in Asia and, to a lesser extent, Europe,” said Michael Gould, technical key account manager, EnergyCuring USA, RAHN USA Corp. ”Moves to classify many UV raw materials as Dangerous Goods for international transportation (usually Class 9) have made vessel booking even more difficult, with some lines refusing to transport such goods.” And, with demand skyrocketing, shipping costs have followed. “Shipping rates on some routes have gone up fivefold as companies scramble for space on available vessels,” said Gould.
COVID-19. In late 2019, COVID-19 emerged in China, causing factories there to slow or idle as the virus spread from region to region. The initial impact was a shortage of imported goods from those factories. In 2020, as the virus spread, factories around the world slowed production, switched to producing new items or idled completely both as a reaction to uncertainty and an impact of short staffing.
Increased consumer demand. After an initial demand surge (such as the panic over toilet paper), the expectation was that consumers would tighten spending. Instead, the opposite occurred. In fact, US durable goods spending is up nearly 32% since Quarter 1 2020, according to data from the US Bureau of Economic Analysis. Normally, an increase in consumer spending is good news – but this surge began after many suppliers and manufacturers had slowed production, and now they are scrambling to catch up.
Natural disasters. In February of 2021, a devastating winter storm rolled into Texas and Louisiana. “The February storm that hit Texas severely disrupted the US domestic supply chain, hitting feedstock supply hard,” explained Gould. “Supply issues have been prolonged due to extremely high demand (from all markets) for these basic building blocks, driven by bounce-back in demand fueled by government stimulus programs. As the supply of basic raw materials – like propylene, epichlorohydrin, Bisphenol A, trimethylolpropane and other alcohols, isocyanates, etc. – began to tighten, downstream manufactured products such as monomers and oligomers were under allocation, and some were subject to Force Majeure.” Hurricane Ida in August 2021 added to the monomer supply problems.
“Supply allocations are challenging the ability to manufacture and supply customers in a timely fashion,” summarized an ink manufacturer. “The evening news describes the supply chain issues at the major seaports. The Gulf Coast still is vulnerable since hurricanes can last until November. Many Chinese chemical manufacturers are under government policy shutdowns due to energy consumption policy. And the Winter Olympics and Chinese New Year will further shut down chemical manufacturing in China.”
UV/EB Supply Chain Working to Mitigate the Constraints
So, that’s all the unfortunate news. These challenges aren’t a surprise to anyone taking part in the production process. The questions become, “Where is the relief?” and “What’s next?”
Communication and planning
“From the start of this situation I have taken the stance that it is important to be transparent,” said allnex’s Puccio. “We have regular discussions with our commercial teams and our customers to keep the information flowing. We are in this together, and the only way out is to work together. We feel that in these tough times our proactive discussions with our customers have further strengthened our relationships.”
Rahn USA is taking the same approach, said Gould. “Regular, open and frank communication is the key to ensure that our clients can make the best decisions they can for their customers. We have daily conversations with customers to understand the scope and timing of their needs, and we do our very best to provide a realistic response to their inquiries.”
Chiaramonte explained, “Many of our customers print time-sensitive, on-demand product. We understand their needs and are trying to provide product to them to enable them to meet their customers’ needs. This becomes more difficult when materials are not readily available. We are requesting longer than usual lead times that are unprecedented previously in our industry while communicating the status of individual orders from the order point to delivery. We are working diligently and tirelessly to work around these setbacks to provide customers with quality product and expediently as possibly.”
These conversations allow the supplier and the customer to plan effective solutions to the current constraints. “The best strategy is to work with customers to accurately gauge their needs and to schedule as far in advance as possible to meet those needs,” said Gould. “Companies that have made accurate material forecasts consistent with purchasing history or projected growth and established strong security stocks have best weathered the crisis so far. Just-in-time purchasing has not worked well at all.”
Alternative materials
The traditional response to material shortages is to source alternate material potentials. “Our procurement team works continuously on options while balancing local and imported materials,” said Puccio. “In addition to leveraging our global footprint, we continue to add staff to support demand.”
Gould agreed but cautioned that testing out new options isn’t an immediate solution, and shortages felt by one supplier are likely to be felt by others. “Alternate materials often are the first/best option,” he said. “However, even products with the same CAS number cannot necessarily be substituted for one another as drop-in replacements without customer validation. Validation studies take time, and during the current crisis, there is little or no time for purchasing and technical staff to make critical decisions. The product that is available today to meet a customer’s demand might be gone by the time a validation study is completed. The ability of suppliers to mitigate these challenges decreases by the week.”
Some customers may consider alternate production methods in light of current shortages. “The members of our customer base are considering changing their purchasing decisions and product use,” explained Chiaramonte. “The customers that have choices are considering a shift from using UV-curable coatings to waterbased, where possible. Our supplier base is naive to the graphic arts print market cost, use and the ease of transitioning from UV use to waterbased coatings. Many pressroom configurations will allow the seamless transition from UV to water if faced with continued shortages and long lead times, coupled with continued rising prices.”
Coatings, however, are only a small part of the constraints facing the graphics arts market. An ink manufacturer pointed to the all-encompassing nature of the current supply issues. “Customers are faced with supply issues on paper, board and film,” the manufacturer said. “Inks and coatings are a minor contribution.” In addition, a process change requires time and testing. Frustrations exist in every direction, but some light is on the horizon.
A return to “normal”
All those interviewed for this article agree that supply chain resolutions will begin to appear by Spring or Summer of 2022, and the upcoming holiday season will be challenging. “The global supply chain needs to get past the New Year and the China Olympics and have time to absorb the backlog,” said Puccio.
Gould added, “Basic raw materials still are in tight supply, and that situation will only improve slowly, over several months. The China ‘Blue Skies’ initiative is due to run through February so the critical photoinitiator sector is unlikely to see relief until late Q2.”
But ‘relief’ is not ‘normal,’ said Chiaramonte. “A return to normal will not occur. The shortages we are facing today that will hopefully ebb in later 2022 will have long-lasting changes in purchasing and service expectations.”
One positive result of the live ‘supply chain stress test’ that is occurring is a heightened awareness of the dangers of depending on a single supply source. “The supply situation for UV/EB monomers, oligomers and photoinitiators is fragile,” said the ink manufacturer interviewed for this article. “Any small change has huge repercussions in the industry.”
In particular, Gould added, “China’s ‘Blue Skies’ directive has created great uncertainty for all UV products and raw materials sourced there. This has highlighted a major weakness that the UV market needs to address: Too high of a percentage of the key photoinitiator product group comes from a country with very high exposure to rapid and frequent disruption.”
The positive result is that manufacturers and their component and chemistry suppliers are thinking differently about what will constitute ‘normal’ in the future and how to create a supply chain that can endure unforeseen stressors. Gould continued, “The one saving grace in this supply chain collapse is that every link in the chain wants to return to normal business conditions. So, while we broaden our supply base, those product manufacturers broaden theirs (for more basic raw materials), and customers broaden their network of suppliers. Every company in the value chain is making critical decisions to manage the crisis, and this will pay off in future with a more robust supply chain for the key raw materials.”
Predicted demand ultimately is good news
Increased demand, while a complicating factor at the moment, will be a long-term factor in the success of those involved with UV/EB curing. An early 2020 release from Research and Markets indicated significant future growth. “Over the years, the level of demand for UV-curable resin has increased due to growth of wood coatings, plastic coatings and metal coatings,” it said. “UV-curable resin is used for a variety of end use industries, such as industrial coatings, graphic arts, electronics and others and is forecast to grow at a CAGR of 5.5%. The major growth drivers for this market are the growth of end-use industries, demand for green coatings, an increase in demand for materials with faster cure time, and stringent emission laws.”
In April 2021, Research and Markets released an updated report entitled “UV Curable Resins & Formulated Products – Global Market Trajectory & Analytics.” It upwardly revised market growth for UV-curable resins and formulated products (Chart 1), saying, “Amid the COVID-19 crisis, the global market for UV Curable Resins and Formulated Products estimated at $4.2 billion in the year 2020, is projected to reach a revised size of $7.4 billion by 2027, growing at a CAGR of 8.2% over the analysis period 2020-2027. Oligomers, one of the segments analyzed in the report, is projected to record a 9.1% CAGR and reach $2.5 billion by the end of the analysis period. After an early analysis of the business implications of the pandemic and its induced economic crisis, growth in the Monomers segment is readjusted to a revised 8.1% CAGR for the next seven-year period.”
Global photoinitiator segments growth is estimated at 7.1% CAGR, growing a combined market size of $759 million in the year 2020 to a projected size of $1.2 billion by the close of the analysis period, according to the report. China will remain among the fastest growing but countries such as Australia, India and South Korea also are expected to contribute.
“For the UV/EB industry, the most critical asset in working through the next six to eight months will be patience,” said Gould. “There are multiple reasons why energy curing technology is a favorite for particular established applications and a growing favorite in other emerging markets. Those reasons aren’t going to change, and moving away from energy curing would eventually bring new problems to light that could precipitate an entirely new crisis.”