Whytneigh R. Duffie; Kevin D. Barz; Tsvetanka S. Filipova; Katrina J. Donovan; Timothy M. Brenza; and Travis W. Walker, South Dakota School of Mines & Technology
Several groups have studied the application of water-soluble resin formulations for 3D printing of materials4, with a common concern being the swelling of the polymer matrix during the dissolution process. In this work, a synthesis protocol was developed to produce unique surface eroding methacrylic-anhydride-based oligomers that later react to form crosslinked networks during the 3D-printing process. Chemical degradation leads to surface erosion of the crosslinked network after 3D printing, which provides ample opportunity for a wide array of applications where swelling of the polymer matrix has previously been a significant drawback in the functionality of water-susceptible 3D-printed parts.
Introduction
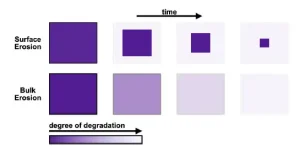
Development of 3D printable thermosets that chemically degrade in the presence of water in a controlled, predictive manner has been postulated as a novel strategy to engineer a number of advanced composites, including biomaterials (e.g., drug delivery, fracture fixation, tissue sealants), disposable single-use medical devices, and advanced transient sensor technologies.1,2 Previous efforts to incorporate surface-eroding oligomers into resin formulations have been further limited by the commercial availability of surface-eroding constituents that are suitable for use in light-based 3D printing. Incorporation of the surface-eroding oligomers into novel resin formulations enables high-resolution, 3D-printable, acrylic-based resins that chemically degrade in the presence of water. Multiple avenues have been identified for development that allow for local photopolymerization of surface-eroding, anhydride-based formulations via 3D digital light processing (DLP). Hydrolysis of the anhydride bonds in the presence of water yields the diacid monomer and poly(methacrylic acid) via a surface-erosion mechanism.1 Surface erosion occurs when chemical degradation and subsequent mass loss is limited to the outermost layer of the crosslinked product (Figure 1).
Bulk erosion occurs when chemical degradation and mass loss occur throughout the entire volume of the material (Figure 1). Surface erosion leads to higher retention of mechanical properties, less water uptake and swelling, and a more controlled degradation rate.3
Methods and materials

Photopolymer resin(s) were prepared with novel synthesized methacrylated-anhydride-based oligomers, reactive diluents and photoinitiators. The synthesized oligomers were characterized using FTIR for functional group confirmation (16 scans), 1HNMR for structural confirmation and determination of molecular weight (300MHz, 1024 scans, CDCl3), 13CNMR for structural confirmation (300MHz, 8192 scans, CDCl3) and Dept-135 NMR for confirmation of peak assignments (300MHz, 8192 scans, CDCl3).
Crosslinked cylindrical disks (15 mm diameter and 1.85 mm height) were produced using an Anycubic Photon LCD printer (Figure 2, left). Printed samples were dried with a lint-free towel and cured in a B9Creations UV cure unit. Degradation studies of formulations containing a reactive diluent with equivalent weight percentages of three different oligomers were performed in triplicate using PBS buffer solution at a fixed agitation of 60 RPM and a temperature of 37° C. After the degraded samples were allowed to dry completely, the disks were massed to calculate the rate of degradation of the disks.
An Anycubic Photon printer was modified in this work to minimize the volume that is required for printing novel formulations to less than 1 mL (Figure 2, right). The modifications to the Anycubic Photon printer included a vat insert with a new area for loading the film, an additional part that was added to the original build plate to serve as the new build area, a 3D-printed sensor piece and an upper-limit switch with 3D-printed housing. The vat insert included a tapered cylindrical cavity at a reduced volume. The cavity that was created to hold the liquid resin included a slight tapering of the inner channel to create turbulence as well as a mixing effect given the dynamics of the printing process. The vat insert was secured with epoxy adhesive around the edges to avoid issues of the build plate lifting the insert during the printing process. Empty cavities were created on the bottom side of the vat insert to reduce the overall weight of the part. The FEP film insert with a smaller area was created with the same general idea as the original vat. The maximum volume that the new vat can hold is approximately 5 mL. Resin is added and removed from the vat using a disposable pipette.
A cylinder was attached to the original build plate using a set screw, and it can be removed at any time with the correct tool. The current cylinder has a diameter of approximately 25.25 mm, and a height of approximately 35.90 mm. The 3D-printed sensor piece has the same shape as the original metal piece that was provided with the Photon; however, the new piece is longer to accommodate for the length of the cylinder that was added to the build plate. The sensor length (55 mm) was chosen to allow for the (z = 0) position to be set slightly lower than the home position without the sensor piece ramming into the bottom of the printer.
Results and discussion
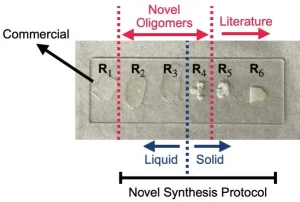
To date, the novel synthesis route has enabled the invention of three previously unobtainable oligomers. Percent yields for all synthesized oligomers were over 70%, and oligomers that were chosen for further evaluation were limited to an ‘n’ value of two, where ‘n’ represents the average repeat of the anhydride oligomer. These lower-molecular-weight starting materials, available in both solid and liquid states at room temperature, allow for a wide array of applications, including 3D DLP (Figure 3).
Oligomers existing in the solid state at room temperature are suitable materials for DLP upon dissolution in light-sensitive liquid crosslinking agents. Thus, solid-state oligomers that are loaded at specific weight fractions into the crosslinking agent undergo co-polymerization upon exposure to light with the addition of a photoinitiator. Several groups have demonstrated the successful copolymerization of solid-liquid mixtures by utilizing methacrylated sebacic anhydride, which is available via a single-stage synthesis route, and loading it into commercially available methacrylic anhydride.2,3 While methacrylic anhydride is the only commercially available liquid bi-functional anhydride, literature suggests that when choosing homopolymerization of liquid methacrylic anhydride, limitations exist that are a result of limited radical diffusion. The long timeframes that are needed to crosslink the material at small volumes are unsuitable for most applications. While the addition of methacrylated sebacic anhydride was found to improve these exposure limitations, the increase in hydrophobicity of the backbone composition and decrease in crosslink density led to decreased erosion rates and decreased mechanical performance of the material.3 Thus, constituents that are suitable for loading into methacrylic anhydride are both promising and worthy of investigation for applications that require increased erosion rates and improved mechanical performance. The additional availability of the products from the novel oligomeric synthesis allows the opportunity to further establish a trend of faster degradation rates and increased mechanical integrity as the length between methacrylated-anhydride functional groups decreases.
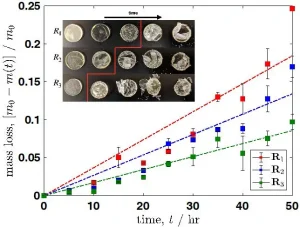
Disks that were 3D printed exhibited linear rates of degradation and shrinkage along only the surface, based on the observation of surface cracking. These results indicate that the crosslinked products were, in fact, surface degrading. The degradation studies suggested that, at a constant value of ‘n,’ a decrease in the length of the R-group in the formulation resulted in an increase in the rate of mass loss (Figure 4). In other words, the rate of degradation was found to increase as the hydrophilicity of the R-group increased, as found in the literature.2,3 Controlled degradation rates provide the opportunity for commercialization in countless applications.
Next steps
By utilizing novel methacrylated-anhydride oligomers that are available solely through an innovative synthesis route, formulation development has shown great promise in providing expanded physical properties of degradable thermoset materials that are suitable for 3D printing. Given that the materials are surface eroding, it is hypothesized in future experiments that the modulus with respect to the thickness of a sample will exhibit very little change over most of the material lifetime. Toward the end of the material lifetime, the thickness of the sample approaches the same order of magnitude as the thickness of the erosion zone on the outer surface of the material. In this case, the modulus with respect to the thickness of the sample rapidly will decline.
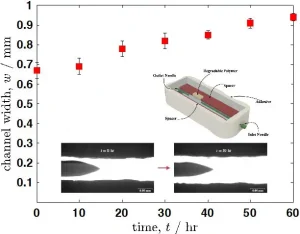
Standard characterization techniques provide limited information about the degradation kinetics and mechanism of erosion. Therefore, a frugal microfluidic device has been developed to further access the kinetics and mechanism of surface-eroding polymer degradation (Figure 5). Liquid is introduced into the channel at a constant flow rate and temperature.
Polymer degradation can be assessed readily via image analysis by evaluating the erosion over time with respect to material formulation, polymerization conditions and sample environments. In-depth analysis of the degradation rates and erosion mechanisms with the novel and adaptable flow apparatus can be coupled with previously explored methods of analysis to give insight into the complex mechanisms that take place during erosion. An increase in the number of crosslinks or in the hydrophobicity of the backbone should result in a decreased rate of degradation.
Acknowledgements
The authors would like to thank the South Dakota Board of Regents Competitive Research Grant and the NSF EPSCoR 2DBest Graduate Student seed grant for funding. This material is based upon work that was supported by the National Science Foundation Research Traineeship program under award number 1828462. The authors also would like to thank Christen V. Gauker and Jacob P. Fyffe for their assistance, as well as B9Creations, LLC for its support of the project overall. Two invention disclosures have been submitted in relation to this work, with a provisional patent application being finalized.
References
- Kristi S Anseth and Deborah J Quick. Polymerizations of multifunctional anhydride monomers to form highly crosslinked degradable networks. Macromolecular Rapid Communications, 22(8):564–572, 2001.
- Andrew W Watkins and Kristi S Anseth. Copolymerization of photocrosslinkable anhydride monomers for use as a biodegradable bone cement. Journal of Biomaterials Science, Polymer Edition, 14(3):267–278, 2003.
- Jennifer S Young, Kelly D Gonzales, and Kristi S Anseth. Photopolymers in orthopedics: characterization of novel crosslinked polyanhydrides. Biomaterials, 21(11):1181–1188, 2000.
- Robert Liska, Florian Schwager, Christine Maier, Rafael Cano‐Vives, and Jürgen Stampfl. Water‐soluble photopolymers for rapid prototyping of cellular materials. Journal of applied polymer science, 97(6):2286–2298, 2005.