By Corey Long and Clémentine Champagne, Arkema
Additive manufacturing generally is considered to be a more environmentally responsible technology by enabling on-demand, local production, with the potential to reduce material waste and minimize the logistic footprint. The key to unlocking its full potential lies in the use of more sustainable raw materials. These innovations are a way that all value chain participants can work together to reduce the overall carbon footprint of the materials used. The authors’ company has been involved in the design, development and supply of biobased (meth) acrylates with traceable bio content. The company now is leveraging this experience to create high-performance photopolymer 3D-printing formulations with high bio-content.
Introduction
3D printing is a production technology that profoundly changes the way the manufacturing of objects is envisioned in many areas. This change in thinking about industrial production simultaneously occurs with societies’ growing awareness of the necessity to reduce its impact on the world. Light-curing additive manufacturing, such as vat photopolymerization (DLP, SLA, LCD) or MultiJet Printing Systems (MJP), is a technology enabling optimization of diverse aspects of sustainability. 1
Use of this technology is an opportunity to minimize material waste, limiting its consumption to what is necessary to create the part and, by consequence, to be more energy efficient. 3D-printing technology also makes it possible to think about supply chains that are better suited to market demand and location. Those opportunities for higher sustainability foster innovation in various sectors. For example, in medical and dental applications, faster solutions customized to the patient can be proposed thanks to 3D-printing processes, supporting better health and well-being.
If opportunities are there, they are accompanied by challenges. To source and develop materials that enable high-performing and durable materials while designed from safe and alternative feedstocks is an objective that is difficult to reach. And downstream in the value chain, the management of the waste when objects are used is a question requiring further research work.
In this work, the authors proposed two approaches to improve the sustainability of materials. The first path is to formulate with raw materials having high bio-based feedstock to obtain material with a variety of mechanical properties, from hard to elastomeric. The second option is to formulate with raw materials made of bio-attributed feedstock.
Materials and Methods
Material
The monomer is isobornyl acrylate (IBOA). The oligomers are a soybean oil epoxy acrylate and two aliphatic urethane acrylates, and the photoinitiator is the ethyl phenyl (2,4,6-trimethylbenzoyl) phosphinate (SpeedCure TPO-L). The monomer and oligomer properties are presented in Table 1.
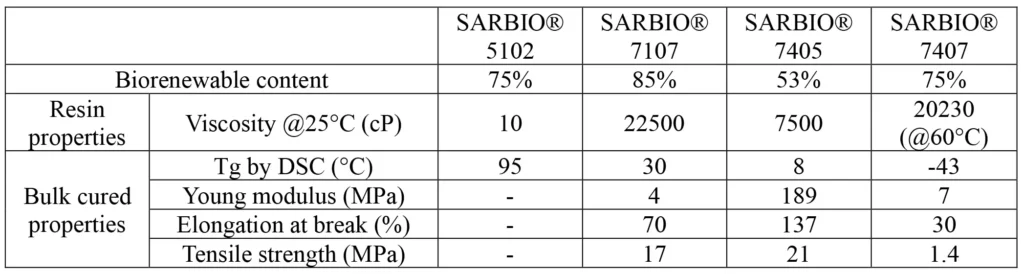
Based on these raw materials, three simple and comparable formulations (with the same content of oligomer and same monomer used) were prepared (Table 2).
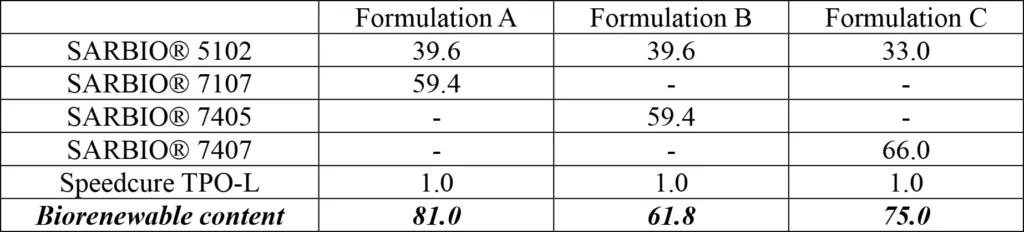
Methods
Material samples were prepared using a tensile test mold for ASTM D638 (Type IV) and using a LED conveyor to cure the materials (395 nm, 3W/cm2 irradiance, four passes). The specimens’ mechanical performance was tested following the procedures laid out in ASTM D638.
Biorenewable content (BRC) is measured based on the ASTM D6866 standard. It is based on 14C analysis.
Results and discussion
Formulating with bio-based feedstock
Materials mechanical performances made of formulation A, B and C are presented in Table 3, and the Stress-Strain curves obtained are drawn in Figure 1.

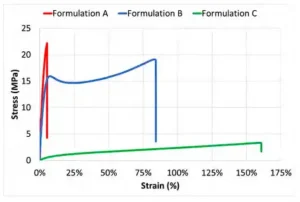
With simple formulations having a significant biorenewable content, from 55% to 75%, it is possible to scan a large spectrum of material performances, from hard and tough materials to elastomers. This is made possible thanks to the oligomers selected for this study, combined with the isobornyl acrylate (IBOA) monomer, as noted in Table 1:
- The soybean oil epoxy acrylate oligomer brings hardness while maintaining a good flexibility.
- The first aliphatic urethane acrylates oligomer brings an excellent balance between hardness and flexibility; it is a toughener oligomer.
- The second aliphatic urethane acrylates oligomer is a highly flexible oligomer for high elastomeric performance.
Formulating with bio-attributed feedstock
If the improvement of the bio-content in 3D-printing UV-cured material is an objective for many, it is not possible today to find relevant bio-based alternatives to all chemical building blocks. Large-volume chemicals, often upstream in the value chain, today are produced thanks to large-volume processes using expensive assets. The duplication of production infrastructures to produce separately (or in a segregated way) a fossil-fuel-based chemical, and its bio-based alternative, often is not economically relevant. The acrylic acid, important in UV-curable market, is an example.
The Mass Balance Approach (MBA) is a solution to transitioning to a more sustainable product. It consists of replacing fossil fuels by renewable feedstocks at the origin of the supply chain, segregating by bookkeeping the quantity of renewable material and “attributing” this quantity to finished products at the end of the chain (see Figure 2). Products leaving the plant are not distinguishable based on their composition or characteristics (ASTM D6866 is not applicable, for example) but are accredited.
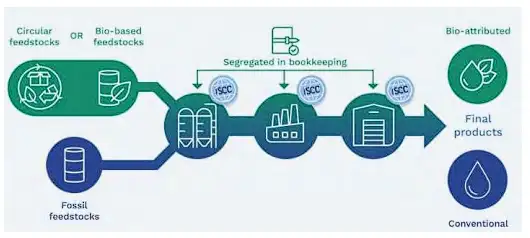
In this case, the authors reference a percentage of bio-attributed feedstock in the final material. It is an alternative pathway to meet the challenge of combining performance, circular sourcing and lower Product Carbon Footprint (PCF).
In Europe, the authors’ company has certified its acrylic supply chain by a third party, according to the International Sustainability and Carbon Certification-PLUS (ISCC+) standards, to ensure the traceability of its “Mass Balance” product offer. 2 From the acrylic acid to monomers and oligomers of Sartomer, the ISSC+ certification of the supply chain ensures that the origin of the renewable sources meets ISCC+ standards for sustainable feedstocks. The acrylated monomers made from this mass balance approach show a reduction of their PCF, as per a cradle-to-gate approach, up to 40%.
Conclusion and perspectives
New raw materials commercially available enable the formulator to develop materials combining high performance and sustainability profile. Raw materials can integrate in their design bio-based feedstock. In parallel and/or in combination, it also is possible to improve the sustainability of materials, thanks to monomer and oligomers made from bio-attributed feedstock.
References
- “Analyzing true sustainability in 3D printing” by Sangmin Simon Lee, 3Dprint.com, August 28, 2023.
- https://www.arkema.com/global/en/resources/post/Webzine%20stories%20CS/mass-balance-solutions-to-accelerate-the-shift-towards-more-circ/