A.Over the past few years, 3D printing (also known as additive manufacturing) has increasingly been a topic of discussion. It’s not hard to see why, as technological advances in hardware, process, software and, of course, materials have caused manufacturers to take notice. Moreover, it’s been the applications of those technologies that have really caught the eye, especially as we see more real-world examples of mass-produced, durable, end-use parts using 3D printing. It’s an exciting time for the industry, and UV-curable materials have played a big part in the recent proliferation of 3D printing applications and will continue to do so… but how?
Ultimately, not all 3D printing processes allow for UV curing, but there are a few – namely stereolithography (SLA), digital light processing (DLP) and inkjet 3D printing being the earliest forms of 3D printing methods to use the process. It’s no accident that 3D printing’s popularity, especially within the context of mass manufacturing, is due in part to the benefits of these UV curing-based processes. Traditional UV-curable 3D printing has been around for decades, but advances in systems and hardware have made it easier for 3D printers to control the accuracy and reaction time of the polymerization process.
The result? Increased printing speeds and better part resolution – both incredibly attractive features for manufacturers. Some 3D printing companies that have introduced and adopted UV-curable processes include:
- Carbon, which introduced a new technology called Digital Light Synthesis™, enabled by its proprietary continuous liquid interface production (CLIP™) process that uses digital light projection, oxygen permeable optics and dual-cure resins to print and cure production-quality parts;
- EnvisionTEC, which uses digital light processing and video projector technology to cure each layer in one blast;
- FormLabs, which uses traditional stereolithography (SLA) in its Form 2 printer, drawing and curing each layer of resin using a laser; and
- Stratasys, which uses a process called PolyJet that uses an inkjet-like head to draw each layer on a platform and is cured via a UV unit.
The Role of UV Curing in 3D Printing Materials
Some of the biggest advantages of using UV-cured resins in 3D printing are that it offers the highest level of detail, improved surface finishes and faster printing speeds. Manufacturers need more in the market to leverage all the potential applications, so new UV-curable materials are being introduced all the time. However, to really take this to the next level, we need to consider developing UV-curable materials with the desired application and functional requirements in mind, rather than trying to fit an application to existing materials and UV chemistries.
Below are steps that materials developers, 3D printing customers and engineers can take to shift their thought processes to more of an application-focused approach when developing materials for 3D printing processes that use UV curing:
- It’s important to consider the relationship between chemistry and geometry that ultimately determines part properties. Many properties can be enhanced with changes to part geometry or designs that are not accessible to traditional manufacturing processes. Examples include using latticing to generate lightweight but strong components or replacing multi-part assemblies with a single part.
- Next, it’s a matter of finding a good match of chemistry and properties. For example, the inherent properties of polyurethane elastomers make them a good fit for wear-resistant, high-energy-return midsoles for athletic footwear. Similarly, the excellent chemical and electrical properties of epoxies render them well-suited for applications such as automotive electrical connectors.
- Finally, integrating new chemistries is a big step to developing these materials, and there are always clever ways to integrate diverse chemistries and let them play to their strengths. For instance: turning un-curable materials into UV-curable materials, putting the materials through an additional post-print baking step or integrating them as part of a dual-cure process to best maximize their mechanical properties.
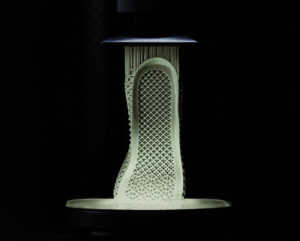
As of now, UV-curable materials in 3D printing have made the biggest headway in dental applications, as they are high-value products that require mass customization. They have found a natural home with indirect bonding trays, aligners, dentures and dental molds, and anti-bruxism splints, to name a few.
Other mass-customized products that have found a natural fit with 3D printed, UV-curable materials include custom hearing aids, anatomical models and guides for pre-surgical planning, and athletic shoe midsoles.
What About Dual-Curing and Post-Processing?
UV curing also has been integral in the post-processing of 3D-printed parts and products which, in many cases, necessitates the addition of a thermal bath or baking process to strengthen the mechanical properties and material performances.
One can cure simply with light (visible spectrum, such as natural sunlight) or UV (such as that used in UV nail salons, DIY cure boxes, etc.) or use both light/UV and heat. Carbon’s CLIP is a dual-cure process, which mixes different complementary materials that then react during the UV curing and heating process to create a material with new mechanical performances and properties.
By combining heat and light/UV, these dual-cure methods offer the ability to incorporate and integrate chemistries and materials into 3D printing that previously wouldn’t have been considered – and that’s where the innovation comes in. In some cases – hybrid dentures and hearing aids – UV chemistry alone may be sufficient to enable a given application. In others, the dual-cure methods can provide the toughness, thermal properties and chemical resistance to find use in demanding environments. Applications such as footwear, electrical connectors, fluid manifolds and more could benefit from dual curing.
What’s Next?
As the 3D printing industry evolves with digital manufacturing, UV-curable materials providers also will be expected to keep pace. This will mean providing more innovative materials that give end users options for additional colorways and manufacturers more options for the performance properties of their parts.
The role of UV curing in 3D printing always has been to take what was designed digitally and help make it a reality. With the industry’s push toward more end-use applications and mass manufacturing, the result will not only be more options, but more safe, consistent, durable, engineering-grade UV-curable materials for those applications. I can’t wait to see what new applications and materials are developed next.