By Darryl A. Boyd, Colin C. Baker, Jason D. Myers, Vinh Q. Nguyen, Woohong Ki and Jasbinder S. Sanghera, Optical Sciences Division, Naval Research Laboratory and Collin C. McClain and Christopher G. Brown, University Research Foundation, Greenbelt, Maryland
Note from the Editor: The polymers described in the following proceeding are being developed for use as infrared (IR) transmitting materials to replace costlier, heavier and more difficult-to-process IR-transmitting materials currently on the market. These ‘ORMOCHALC’ polymers have been shown to transmit from the red-visible range all the way into the mid-wave IR.
Abstract
Polymers containing the chalcogens sulfur and selenium show great promise as infrared transmissive materials. The chalcogen-based materials are synthesized using a process known as inverse vulcanization. Through this process, sulfur and selenium-rich polymers are fabricated, and these polymers possess unusually high refractive indices while also being transmissive far beyond the typical transmission range of most polymers. The results of this work highlight the value of sulfur-based reactions in the development of cost-efficient and useful optical materials.
Introduction
Sulfur is an earth-abundant element that has several inherent beneficial qualities for the development of functional materials.1,2 ORganically MOdified CHALCogenide (ORMOCHALC) polymers are sulfur-rich materials that can be synthesized via inverse vulcanization.3 Inverse vulcanization is a recently developed process in which sulfur-based polymers can be synthesized through the use of elemental sulfur and carbon-rich crosslinkers.4 First, sulfur, which exists as an eight-membered ring structure compound (i.e. S8), is heated to open the ring structure and make a linear sulfur chain. Upon ring-opening, radicals are revealed at either end of the sulfur chain. The radicals at the ends of the sulfur chain then can be reacted with crosslinking/branching agents to produce stable ORMOCHALC polymers. The ORMOCHALC polymers fabricated using this process have valuable optical characteristics and have also found use in dye-sensitized solar cells,5 as well as in cathode materials for lithium sulfur batteries.4,6,7
Sulfur has elemental similarities with selenium, which sits just below sulfur in the periodic table of the elements. Due to their similarities,8,9 it is possible to combine the two elements and use this combination as an ORMOCHALC precursor material. The addition of selenium to the backbone of ORMOCHALC polymers has a direct and pronounced effect on the optical properties of the polymers produced. Most notable are the extension of the infrared transmission profile further into the mid-wave infrared region3 and the increased refractive indices of this class of polymers.10 The reported work presents the synthesis and optical characterization of ORMOCHALC polymers.
Materials and methods
Materials: Sulfur and selenium were purchased from All-Chemie Ltd. and distilled four times each. 1,3-diisopropenyl benzene (DIB) was purchased from TCI America and used as received. All polymers were fabricated with a “S-Se precursor” to “DIB comonomer” weight ratio of 70 to 30.
Analysis Instrumentation: FT-IR data was obtained using an Analect Diamond-20 FT-IR. SWIR images of polymers were taken using an FJW Industries FIND-R-SCOPE.
Preparation of crystalline sulfur-selenium compounds: Purified elemental sulfur (S) and purified elemental selenium (Se) were combined as previously described.3 Data presented are based on an S to Se ratio of 95:5.
Fabrication of poly(SxSey–r-DIB) ORMOCHALC polymers: In a fume hood, a beaker containing a magnetic stir bar and crystalline S-Se compound was placed in a silicon oil bath that was preheated to ~180°C, covered with a watch glass and stirred on a magnetic stir plate. After the S-Se compound completely melted, DIB was added to the beaker and the mixture stirred until it became viscous and red in color. The viscous material was poured from the beaker into a mold, and the mold was then placed into a furnace that was preheated to 200°C and allowed to vitrify for 1 hour. The polymer was allowed to cool to room temperature and removed from its mold. Polymers in this study were made with 30 wt% DIB comonomer, while the subscript values given for sulfur and selenium within the precursor compounds represent atomic percentages.
Results and discussion
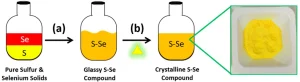
The blending of the elements sulfur and selenium together to form a uniform precursor material (Figure 1) is a nontrivial, but useful, process that allows for the synthesis of sulfur-selenium ORMOCHALC polymers.3 These multi-chalcogen precursors are used as comonomers and can be combined with a variety of crosslinking comonomers.6,11-13 In the work outlined, the crosslinking comonomer is 1,3-diisopropenyl benzene (DIB). The resulting polymers are generically named as poly(SxSey–r-DIB), where S represents sulfur, Se represents selenium, DIB represents the comonomer, r represents the random nature of the crosslinking and the subscripts x and y represent the ratio of sulfur to selenium in the precursor, respectively.
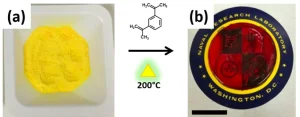
Elemental sulfur is typically yellow in color. Upon addition of selenium, the sulfur-selenium precursor becomes increasingly orange in color as the percentage of selenium increases. Once the solid precursor is heated to 120°C, it begins to melt and get darker in color (i.e. from yellow/orange to deep red) as the temperature approaches 200°C. The change in color is accompanied by an increase in viscosity, with the material becoming solid-like at 200°C. In the absence of a crosslinking comonomer, the sulfur-selenium precursor will return to a yellow/orange, solid material. The addition of the DIB crosslinker at elevated temperatures prevents the sulfur-selenium compound from turning back into a yellow/orange material, leaving behind a red, solid ORMOCHALC polymer (Figure 2b).
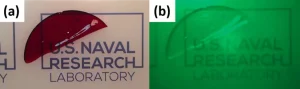
Despite the red color of the ORMOCHALC polymers, they still are translucent to the naked eye (Figure 3a). When visualized in the short-wave infrared (SWIR) region of the electromagnetic spectrum, the polymers appear transparent, like clear glass (Figure 3b), demonstrating the useful infrared transmission character of these polymers.
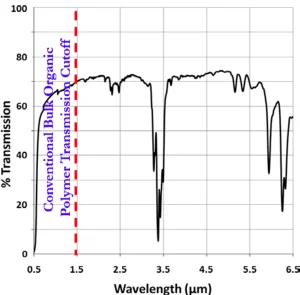
In agreement with what can be seen through a SWIR viewer (Figure 3b), FT-IR analysis demonstrates that the ORMOCHALC polymers indeed have broad optical transmission into the mid-wave infrared (MWIR) region of light (3 to 6 μm) (Figure 4). This transmission only is interrupted by the –CH absorbance bands that arise from the presence of the DIB comonomer within the ORMOCHALCs. Most polymers are incapable of transmitting light at high transmission percentages far into the infrared region, making ORMOCHALC polymers particularly valuable as possible replacements for costlier, heavier and more difficult to process IR-transmissive glasses.
Conclusions
Sulfur and selenium-rich materials, termed ORMOCHALC polymers, can be fabricated via the inverse vulcanization process. A major benefit to ORMOCHALC research is that it offers an alternative use for the large stores of excess sulfur that exist on the planet, and – with the proper crosslinkers – can lead to the development of useful materials using completely renewable resources.14 Though red in color to the human eye, these materials provide transparency into the MWIR region of the electromagnetic spectrum, far beyond the typical transmission of most common organic polymers. Finally, the unique optical characteristics of these polymers can be further enhanced by increasing the amount of selenium present in the polymer backbone.
References
- Boyd, D. A. Angewandte Chemie International Edition 2016, 55, 15486.
- Boyd, D. A. Angewandte Chemie 2016, 128, 15712.
- Boyd, D. A.; Baker, C. C.; Myers, J. D.; Nguyen, V. Q.; Drake, G. A.; McClain, C. C.; Kung, F. H.; Bowman, S. R.; Kim, W.; Sanghera, J. S. Chemical Communications 2017.
- Chung, W. J.; Griebel, J. J.; Kim, E. T.; Yoon, H.; Simmonds, A. G.; Ji, H. J.; Dirlam, P. T.; Glass, R. S.; Wie, J. J.; Nguyen, N. A.; Guralnick, B. W.; Park, J.; SomogyiÁrpád; Theato, P.; Mackay, M. E.; Sung, Y.-E.; Char, K.; Pyun, J. Nat Chem 2013, 5, 518.
- Liu, P.; Kloo, L.; Gardner, J. M. ChemPhotoChem 2017, 1, 363.
- Dirlam, P. T.; Simmonds, A. G.; Kleine, T. S.; Nguyen, N. A.; Anderson, L. E.; Klever, A. O.; Florian, A.; Costanzo, P. J.; Theato, P.; Mackay, M. E.; Glass, R. S.; Char, K.; Pyun, J. RSC Advances 2015, 5, 24718.
- Gomez, I.; Mantione, D.; Leonet, O.; Blazquez, J. A.; Mecerreyes, D. ChemElectroChem 2018, 5, 260.
- Eisenberg, A.; Tobolsky, A. V. Journal of Polymer Science 1960, 46, 19.
- Tobolsky, A. V.; Eisenberg, A. Journal of the American Chemical Society 1959, 81, 780.
- Anderson, L. E.; Kleine, T. S.; Zhang, Y.; Phan, D. D.; Namnabat, S.; LaVilla, E. A.; Konopka, K. M.; Ruiz Diaz, L.; Manchester, M. S.; Schwiegerling, J.; Glass, R. S.; Mackay, M. E.; Char, K.; Norwood, R. A.; Pyun, J. ACS Macro Letters 2017, 6, 500.
- Crockett, M. P.; Evans, A. M.; Worthington, M. J. H.; Albuquerque, I. S.; Slattery, A. D.; Gibson, C. T.; Campbell, J. A.; Lewis, D. A.; Bernardes, G. J. L.; Chalker, J. M. Angewandte Chemie International Edition 2016, 55, 1714.
- Arslan, M.; Kiskan, B.; Yagci, Y. Macromolecules 2016, 49, 767.
- Salman, M. K.; Karabay, B.; Karabay, L. C.; Cihaner, A. Journal of Applied Polymer Science 2016, 133, n/a.
- Worthington, M. J. H.; Kucera, R. L.; Chalker, J. M. Green Chemistry 2017, 19, 2748.