By Julie Cross and Marina Santos, Domino Printing Sciences
Abstract
The challenges associated with migration when working with low-viscosity inkjet systems for food packaging applications are well understood in the industry. We will discuss the terms “low migration” and “food packaging-compliant” and then will review a migration study completed with a food packaging-compliant ink set with specific focus on set-off migration.
Introduction
The requirement to prevent contamination of food via migration of printing inks through the packaging is well understood. Food packaging materials are covered by the Commission Regulation (European Commission) No 1935/2004, which provides a harmonized legal European Union framework and sets out the general principles of safety and inertness for all food contact materials (FCMs)1.
Significant focus has been put on understanding this issue since the photoinitiator ITX (isopropyl thioxanthone) was found to have migrated from the UV-cured offset ink printed on the outside of the packaging into baby milk in September 20052. In this case, the transfer of the ITX most likely was as a result of set-off migration. Later, in December 2005, ITX also was found to have migrated through the packaging into olive oil and fruit juice3. Following these incidents, significant effort has been put into formulating inks to minimize or prevent migration.
The term “low migration” was introduced to the printing industry more than 15 years ago to refer to inks that were suitable for indirect food packaging applications in that they had been formulated to meet the required migration limits. The term “low migration” only could be used as a relative term, as there is no absolute value associated with it. When the term is used, it usually refers to the fact that the inks are compliant with the Swiss Ordinance and, in some cases, the Nestlé Guidance Notes on Packaging Inks4.
In 2018, the European Printing Ink Association (EuPIA) announced that it would no longer be using this term5 in light of advances that had been made in this field and were reflected in the 2016 revision of the EuPIA Good Manufacturing Practice (GMP) for printing inks used on food contact materials6. This change also has been reflected in the printing industry, and many ink suppliers now are referring to “food packaging-compliant” inks.
Development of a food packaging-compliant ink for inkjet is considerably more difficult compared to analog inks, such as flexo, due to the viscosity requirements of the commercially available printheads. Inkjet printhead technology necessitates use of low-viscosity inks to achieve reliable jetting and, as a consequence, low molecular weight photoinitiators and monomers are required to control the viscosity. The mobility of such molecules is far greater, which makes arresting migration a larger challenge.
Types of migration
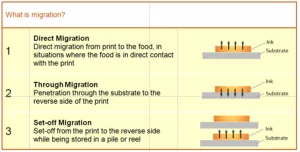
Migration is the transfer of substances from the printing ink into the food. Figure 1 illustrates the different routes that migration can occur.
Direct migration can occur when the printed ink is in direct contact with the food material. Due to the chemical nature of the photoinitiators and monomers/polymers used in inkjet inks, they are not suitable for direct food contact and, as a result, direct migration is not discussed in this paper.
Through migration occurs when components of the printing ink pass from the printed image on the outside through the label and packaging and into the food inside. This can be reduced through careful selection of the label or packaging material, which can act as a barrier. This form of migration is of significant concern for digitally printed labels using inkjet ink.
Set-off migration can occur when prints are stored in a stack or tightly wound roll and when, under pressure, components from the printed surface can migrate to the nonprinted, reverse side of wound labels or stacked sheets, and it is then that this surface comes into contact with food. This form of migration is of less concern when self-adhesive label stock is used, as the label stock usually has a liner that is removed when the label is applied to the packaging. However, for foils, flexible packaging and liner-less substrates, this form of migration must be considered.
Migration analysis methodology
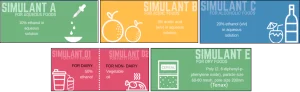
A simulant that mirrors the properties of the foodstuff is used in place of the food sample and is chosen to reflect the product intended to be inside the packaging7,8. Figure 2 provides an explanation of the simulants typically used.
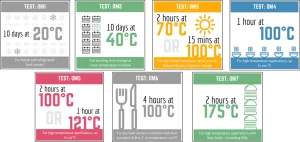
Once the appropriate simulant has been chosen, the testing conditions (temperature and exposure period) are selected, again to represent the environment and time under which the product will be stored9. Figure 3 gives an overview of the standard test conditions that can be employed.
Similar methodology can be used to analyze for through and set-off migration10 and for both, standard stainless-steel migration cells (cell type B of EN 1196-1) are used.
For through migration, the sample is positioned so that the printed surface is in direct contact with the steel plate of the migration cell so that the ink is not in direct contact with the simulant. The migration cell then is closed and filled with the simulant of choice. The cell then is placed in the incubator using one of the standard conditions shown in Figure 3.
For set-off migration, a similar process is used, but instead of placing the printed sample in the cell, a piece of unprinted film that has been in contact with the printed image with a weight on top of both films for 10 days is used. The unprinted sample then is positioned in the cell so the surface that was previously in contact with the printed image is in direct contact with the food simulant. The cell then is filled with the simulant of choice and placed in the incubator.
After the incubation period, the migration cells are cooled to room temperature and the simulant transferred to suitable vials for analysis via liquid chromatography-mass spectrometry (LC-MS).
Migration study
Liquid chromatography-mass spectrometry (LC-MS)
The analysis was carried out using ultra high-performance liquid chromatography (uHPLC)-mass spectrometry (MS). The studies were performed on a Thermo Q Exactive Focus mass spectrometer equipped with a Dionex RS 3000 uHPLC system. The chromatographic separation was performed on an ACE Excel C18 column, 50 x 2.1 mm I.D., 1.7 µm particles. The mobile phase consisted of (A) water/0.1% formic acid and (B) acetonitrile/0.1% formic acid. An increasing linear gradient (v/v) of solvent B was used (t(min), %B): (0, 10), (10, 90), (11-15, 90), (16-20, 10) with a flow rate of 0.25 mL/min and a column temperature of 25oC. The mass spectrometer was operated in electrospray positive ion mode. The capillary voltage was kept at 3.5 kV (positive mode) and the capillary temperature at 320oC. Nitrogen was used for sheath gas (flow rate: 46), aux gas (flow rate: 11) and sweep gas (flow rate: 2).
Formulation and specific migration limits

A simplified set of inks that had been formulated to be food packaging-compliant was used for this migration study. Table 1 shows the acrylate and photoinitiators used in the formulations, along with their specific migration limits.
Sample Preparation
Through migration. Circles consisting of two layers of white
ink (200% coverage) plus one layer of cyan ink (100% coverage) plus one layer of yellow ink (100% coverage) to represent worst case conditions were printed onto PE (82µm, AH941 PE TOP WHITE 1S-85, FassonTM) and PET (45µm, Shrink PET CL 1S-45 UHS, FassonTM) films using the N610i digital printing press at 50m/min, the pinning lamp set to 40% for the white layers and a further pinning lamp set to 80% for the color layers (both
Phoseon FP200 395nm rated at 8W/cm2) and a GEW iron doped mercury NUVA2 lamp (rated at 240W/cm2) set to 50%.
Migration then was investigated for all food types using 10% ethanol (aqueous foods), 4% acetic acid (acidic foods) and 95% ethanol (worse case simulant for fatty foods). Incubation parameters were used to cover usage on food packaging items for long-term storage at room temperature: 50oC for 10 days. In all cases, the ratio was equivalent to 6dm2 per kilogram of food (“EU cube, 10x10x10 cm, 1 kg food”).

Set-off migration. The printed image shown in Figure 4 was used for this part of the study. In this case, the image was printed onto a 50µm PET substrate using the N610i digital printing press at 50m/min, with the pinning lamp (Phoseon FP200 395nm rated at 8W/cm2) set to 100% and a GEW iron doped mercury NUVA2 lamp (rated at 240W/cm power) set to 100%.
Four different samples were prepared to simulate conditions that the prints may experience when printed on a hybrid digital/analog press where several flexo stations may be present after the digital unit:
- No extra treatment
- One extra pass at 50m/min through the iron doped mercury NUVA2 lamp (rated at 240W/cm2 at 95% power)
- Two extra passes at 50m/min through the iron doped mercury NUVA2 lamp (rated at 240W/cm2 at 95% power)
- Three extra passes at 50m/min through the iron doped mercury NUVA2 lamp (rated at 240W/cm2 at 95% power)
The printed image then was put into contact with a 50µm PET unprinted film with a 1Kg weight on top of both films for six days. The film that had previously been in contact with the printed image then was used for the set-off migration test. The chosen simulant was 50% ethanol (dairy foods) and the incubation parameters were 40oC for 10 days.
Results

Through migration. The data in Table 2 show that on PE, when the LC-MS peak areas found from the migration test samples were compared to the peak areas for the standard solution, the HDDA was found to migrate to a level significantly above the specific migration limit for all food simulants tested. No further analysis was therefore carried out for the photoinitiators.
When the substrate was PET, traces of HDDA were found in all simulants, however the two photoinitiators were only found to migrate in the fatty food simulate (95% Ethanol). In each case, when the LC-MS peak areas found from the migration test samples were compared to the peak areas for the standard solutions, the concentration of each was below the specific migration limits.
These results indicate that, even though the simplified inks were formulated to be compliant with the Swiss Ordinance and the Nestlé Guidance Notes to be food packaging-compliant, a functional barrier (in this case 45 µm PET) still was required to prevent through migration above the specific migration limits, when worst-case print coverage (400%) was used.
Set-off migration. The set-off migration samples printed with the simplified inks were analyzed for HDDA, Esacure KIP160 and Omnirad TPO-L. No evidence of set-off migration of Esacure KIP 160 was found in any of the samples.
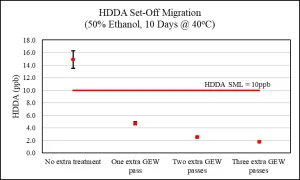
The data in Figures 5 and 6 show that, where no additional passes were made through the iron doped mercury lamp, the concentrations of both the acrylate HDDA and the photoinitiator TPO-L were above the specific migration limits. However, only one additional pass through the lamp was required to reduce the set-off migration in each case to below the specific migration limits, with further reductions in set-off migration being measured with additional passes.
Conclusions
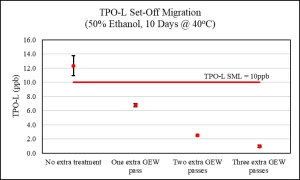
Although the use of the term “low-migration” still is prevalent in the printing industry, it is becoming widely understood that, as there are no absolute values associated with it, it can only be used as a relative term. Because of this, the industry is moving toward using terms such as “food packaging-compliant.”
The data presented show that, even when an inkjet ink set has been formulated to be food packaging-compliant, through migration still can occur when high levels of ink are deposited unless a functional barrier, such as 45µm PET, is present.
Set-off migration also should be taken into account when a liner-less substrate is used and should not be considered safe just because the ink set has been formulated to be food packaging-compliant. The data show that, for some components (in this case the acrylate HDDA and photoinitiator TPO-L), set-off migration above the specific migration limit was measured unless additional passes through a mercury arc lamp were included.
Many printers now are investing in hybrid presses that merge the capabilities of analog and digital printing techniques by integrating a digital press into a flexo line. This typically results in one or more flexo stations being positioned after the digital print engine, allowing the digitally printed image to receive a larger dose of UV to achieve better cure and remove the concern for set-off migration.
Acknowledgements
We would like to acknowledge the work carried out by Axa Romero, from the analytical team of the Marking Materials group in Domino Printing Sciences, who performed the migration testing reported in this paper.
References
- https://ec.europa.eu/food/safety/chemical_safety/food_contact_materials/legislation_en
- Jamnicki and Jamnicki; Migration of ITX (Isopropyl Thioxanthone) from Tetra Pak Bricks into Food, ACTA GRAPHICA 21(2010)1-2. 7-13
- Haglind; Migration of Isopropylthioxanthone (ITX) in fat containing food products, RASFF 2005. 631, 2005, 1-3
- https://www.nestle.com.pe/sites/g/files/pydnoa276/files/nosotros/informacion-proveedores-nestle/documents/actualizacion%202019/guidance%20note%20on%20packaging%20inks%20-%20version%202018.pdf
- https://www.eupia.org/fileadmin/FilesAndTradExtx_edm/181030_EuPIA_Statement_on_Low_migration_Inks.pdf
- https://www.eupia.org/fileadmin/FilesAndTradExtx_edm/2016-03-31-EuPIA_GMP_4th_version_final.pdf
- https://eur-lex.europa.eu/legal-content/EN/ALL/?uri=CELEX%3A32011R0010
- https://www.smithers.com/en-gb/resources/2016/jul/migration-testing-simulants
- https://www.smithers.com/resources/2016/apr/overall-migration-limit-testing-conditions
- https://www.eupia.org/fileadmin/FilesAndTradExtx_edm/181031_EuPIA_Guidance_on_Migration_Test_Methods.pdf
Julie Cross started her career as a formulation scientist for Kodak Limited before becoming a project leader of group developing a proprietary vapor deposition process for applications such as Thin Film Transistors. She joined Domino in 2009 as the Drop On Demand Ink Development Manager. She joined the Digital Printing group within Domino in 2013 as Technical Director and is now responsible for all technical aspects of the Digital Printing products, including product development and customer support.
Dr. Marina Santos is currently a Team Leader within the R&D Analytical Division of Domino Printing Sciences, Cambridgeshire, United Kingdom. She obtained her Ph.D. in chemistry in 2006 from the University of Central Florida. She developed expertise in chromatographic methodologies and trace analysis in pharmaceutical products at Merck & Co., and was later appointed Head of Analytical Development and Process Control at the National Institute of Industrial Technology (INTI) in her home country, Argentina. Since she joined Domino in 2016, she has been pivotal in the development of migration testing methods and the analysis of food packaging printing inks.