Bon Appétit tracks down recipes of special dishes that readers have enjoyed at restaurants. Imagine obtaining the recipe of a decadent chocolate cake. You purchase, measure, sift, mix and blend the ingredients, and when it is ready to go in the oven, the recipe says to “bake for 20 minutes.” Having only the time is not helpful. What is the oven temperature? If the recipe directed you to “bake at 350 degrees” with no time listed, you would be equally puzzled. At a minimum, we expect the recipe to specify both the cook time and oven temperature. A better recipe would also specify the oven type (convection, standard), oven location (top rack, center rack), pan type (glass, metal), layer thickness and possibly any adjustments for altitude.
Like the cake recipe, many UV-curing specifications or data sheets have missing or incomplete information. Like the cake recipe, a UV specification should have both the time (energy density, J/cm2) and power (irradiance, W/cm2) values specified.
Many cure specifications include only a Joule value, which can leave engineers, technicians and operators struggling to establish a process window and achieve proper UV cure. One Watt for One Second = One Joule. Having only Joules, a curing specification of 4 Joules could be achieved by any of the three exposures in Figure 1:
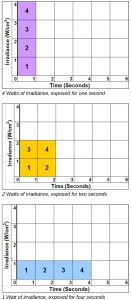
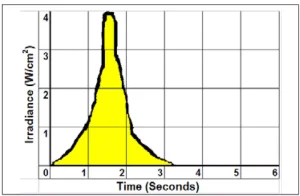
These examples use “whole number” exposures and would lead to different characteristics in the material being cured. In the real world, a 4 Joule exposure does not fit into square blocks and looks more like the example in Figure 2. A radiometer is used to measure the irradiance and energy density.
In order to properly replicate the curing process, a proper UV cure specification should at a minimum include:
- The type of UV source (e.g. 395 nm LED, or iron additive mercury
arc lamp) - The peak irradiance (Watts/cm2)
- The required energy density (Joules/cm2)
With this information, you have a much better chance of replicating the process.
Formulators will argue that they are being cautious and protecting their intellectual property. Establishing a process window requires work based on the specific application. Without a comprehensive specification, achieving proper UV cure is like rolling the dice. But when the stakes are high, leaving proper curing to chance can be a foolish bet.
If available, further information also can be provided or established during tests to define the process window. Information on the UV source can be identified to the brand/model type. Examples include Heraeus 600 W/in. applied power, Light Hammer with “D” bulb or Excelitas 16 Watt 395 nm LED array. Other variables could indicate expected process speeds (e.g., 100 feet per minute), reflector type and/or distance between the substrate and the light source (e.g., a Phoseon LED 385 nm source, rated at 12 Watts, 3″ from the glass.)
When specifying radiometer values, the type of radiometer used also should be specified. This is important because different makes and models of radiometers have different optic responses. A radiometer with a response of 250 to 420 nm will give a different reading than a radiometer with a response of 320 to 390 nm.
A well-crafted specification will contain such information. Here are some examples of good, better and best process specifications:
Good: Cure with 200 mW/cm2 and 1100 mJ/cm2 using a 395 nm LED.
Better: Cure with 200 mW/cm2 and 1100 mJ/cm2 using an Excelitas AC7300-395 UV LED head, rated at 5 W/cm2, 15×300 mm @ 395 nm.
Best: Cure with 200 mW/cm2 and 1100 mJ/cm2 using an Excelitas AC7300-395 UV LED head, rated at 5 W/cm2, 15×300 mm @ 395 nm and 25 fpm. Measured with an EIT L395 LEDCure radiometer.
In addition to differences in optic responses, radiometers also can have differences in dynamic range and suggested operating ranges, sampling rate and cosine response. These can lead to differences in the readings when trying to capture the process (Figure 2).
When it comes to specifications, most of us set the bar too low. Even the Best specification provides only a snapshot of a set of parameters (peak irradiance and energy density) that deliver an acceptable cure. But, it would be even more helpful to know how much latitude this specification provides.
Far too little effort is devoted to testing a “ladder” of settings that will provide good results so that the operators have a process window to work within. This is important since process conditions change over time. These changes sometimes occur naturally. For example, as an arc lamp ages, reflectors deteriorate. Or, over time, the glass on an LED array gets dirty. Other changes might be due to human error. For example, an operator might adjust a conveyor speed inaccurately or fail to properly reposition a lamp.
Just like our cake recipe examples, there are likely to be a range of oven temperatures and cooking times that would produce an acceptable result. We would expect higher temperatures to require less time in the oven, to a point. However, it is unlikely that turning the dial up to 900°F will ever work.
Such process windows have been a standard practice in other forms of curing. For example, a coating can be processed successfully at a number of different settings. This helps the operator to understand the limitations of the process and helps troubleshoot problems when they occur.
It would be great to see more UV formulators and processors work together to develop this kind of process window information. But in the meantime, I will be happy to see more of our customers hone their specifications so that they convey the information needed to make sure things are running properly.
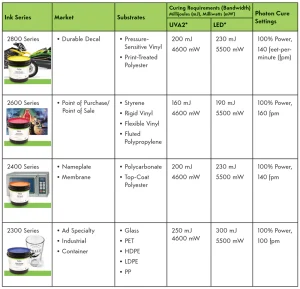
Parting thought: With a proper UV cure specification, you can have your cake and eat it, too.
Jim Raymont
Director of Sales
EIT LLC
jraymont@eit.com