From glitz and glam to texture and realism, embellishment can provide an added layer of pizzaz to any package. And when competition for the consumer’s attention has never been so fierce, embellishment can be the differentiator that makes a package fly off the shelf – figuratively speaking, that is. Embellishment has not quite yet risen to the level of magic, though what some producers have created is nothing short of remarkable!1 Whether it be Cast and Cure™, cold foil transfer or spot embellishments, often these techniques are achieved with UV… but did you know that they also can accomplished with electron beam?
A popular embellishment, Cast and Cure™ uses a specialty film to emboss a pattern into an overprint varnish (OPV).2 The film temporarily is laminated to the OPV while still wet, allowing the surface of the OPV to conform to the features of the film. Then, the OPV is polymerized with EB, freezing the pattern into the coating. Finally, the film is removed and rewound separately for future use. Using Cast and Cure™ in combination with EB brings a holographic wow to your photoinitiator-free, indirect-food-contact-safe, EB-curable OPVs.
Need a metallic finish? Cold foil transfer is the process of transferring a metallic foil from a carrier web to the packaging substrate.3 A laminating adhesive is applied to the substrate, and the foil nipped to the adhesive. The system is exposed to the electron beam, polymerizing the adhesive and adhering the foil, and finally, the carrier web (with any remaining foil) is removed and rewound separately. Since EB has no trouble penetrating through the opaque foil, the adhesive does not need to be activated before being nipped to the foil. The location of both Cast and Cure™ and cold foil transfer embellishments can be controlled by selective placement of the OPV or laminating adhesive, respectively.
The equipment requirements for both types of embellishment are identical. Each requires a secondary unwind and rewind for the addition and removal of the embossing film or foil carrier web. Moreover, a laminating nip is required before the electron beam entrance, and another adjustable web-guiding roll is needed after exiting the beam to ensure the proper release angle of the secondary web. Any electron beam line with these capabilities is, by default, also capable of laminating and curing coatings (or inks), and thus is considered a four-in-one line. To accommodate the thickness of the secondary web, the maximum accelerating voltage of the EB generally is 150 kV.4 Also, since nitrogen inerting only is required for coatings, the beam can be set up for both inerting and ozone exhaust.5
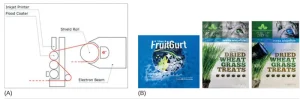
Want an embellishment that can be both visual and tactile? Spot embellishment might be the solution. This broad term encompasses multiple methods to achieve the selective placement of coating or ink. The embellishment can be applied with a patterned flexo plate, or digital inkjet heads can be used so that the embellishment can be changed frame-by-frame to match a digital print. Figure 1 shows an example of the latter method: Indirect gravure was used to flood-coat the HP Indigo-printed substrate with a matte OPV, then clear gloss inkjet ink was patterned over the top in a wet-on-wet process.
The contrast of the gloss between the embellishment and the flood coat is visually appealing, but it also results in a tactile effect from the contrasting coefficients of friction and the additional coat weight of the embellishment. Furthermore, the ink used in this example naturally fluoresces under black light, providing even more creative opportunities. Voltage requirements vary, depending on the thickness of the embellishment, but most often fall between 100 and 125 kV for packaging applications.
In summary, consider the advantages of EB the next time a package calls for embellishment! Whether it’s Cast and Cure™, cold foil transfer, spot embellishment or maybe even a new embellishment technique, EB can help push the bounds of possibility.
Sage Schissel, Ph.D.
Applications Specialist
PCT Ebeam and Integration LLC
sage.schissel@pctebi.com
References
- 2021. FSEA Gold Leaf Awards Celebrate UV Curing. UV+EB Technology. (3).
- DeDonder, M., 2015. Cast and Cure: A Game-Changing Decorative Application Process. UV+EB Technology. (3).
- Embellishments: foil stamping process. https://www.labelsandlabeling.com/label-academy/article/embellishments-foil-stamping-processes
- Schissel, S., 2021. EB Operation 101. UV+EB Tech. (1).
- Schissel, S., 2021. Comparing EB and UV: Common Questions. UV+EB Technology. (2).