By Chloé Paquet, Département des sciences du bois et de la forêt; Jean-François Morin, Département de chimie et Centre de Recherche sur les Matériaux Avancés (CERMA); and Véronic Landry, Département des sciences du bois et de la forêt, industrial research chair NSERC/Canlak; all Université Laval, Québec
Introduction
Abrasion and scratch resistance are amongst the most important properties for interior wood products. To protect wood, UV-curable acrylate coatings are used because of their high reactivity that ensures high factory productivity. Despite the good performance of UV-curable acrylate coatings, scratch formation is unavoidable, as wood is a soft substrate. To ensure scratch repair, extrinsic (vascular- and capsules-based) and intrinsic self-healing technologies were developed1.
Extrinsic technology consists of capsules dispersion or capillaries network inside the material. These capillaries and capsules contain a self-healing agent that is released in the scratch after mechanical aggression. Extrinsic technology is totally autonomous but not repeatable.
Intrinsic technology designates materials with reversible bonds, which create a temporary network. This reversibility, with or without external stimuli, is used to enable material repair1. In contrast to the extrinsic technologies, intrinsic ones are repeatable but not autonomous. Reversible bonds can be carbon covalent bonds in Diels-Alder reaction, hydrogen bonds, interactions or molecular tangles1. During stress, the energy breaks the reversible bond network. Chain mobility allows the reversible network to rebind. In some cases, external stimuli are needed to generate this mobility. Diels-Alder reaction creates covalent bonds between diene and dienophile groups. This reaction occurs at room temperature and retro Diels-Alder upon heating2. Wudl F. et al.3 used Diels-Alder reaction between furan and maleimide to prepare reversible cross-linked polymers. One of the main observations for Diels-Alder-based self-healing materials is that high temperature (100°C to 150°C) is necessary to break covalent bonds. Heating at temperatures higher than 100°C dries and damages wood4,5, which makes this technology inappropriate for wood applications. Molecular tangles occur in materials with high chain mobility, namely soft materials6. UV-curable wood coatings are highly cross-linked, therefore this technology is not applicable. Bond strength and quantity influence the material hardness7. To obtain resistant coatings, one of the strongest non-covalent bonds – the hydrogen bond – was selected to develop resistant intrinsic self-healing coating for wood applications. Several studies on self-healing systems based on hydrogen bonding are presented in the literature. Chen et al.3 developed a polymer with styrene and amide phases. Polyamide phases contain hydrogen bonds ensuring self-healing property. Liu et al.8 used hydrogen bonds in ureido group to prepare oligomers with polyol branches. Stadler et al.9 synthesized several poly(butadiene)s with an assortment of hydrogen bonds. They prove that the temperature needed to generate self-healing is directly proportional to the hydrogen bond. Cortese et al.10 grafted thymine and diaminotriazine onto poly(propylene oxide). In this case, the hydrogen bond depends on thymine and diaminotriazine. This study concludes that polymer crystallinity increases with increasing hydrogen bonds10.
Therefore, increased hydrogen bonding increases material crystallinity as well as the temperature needed to generate self-healing. To obtain resistant coatings for daily life, it is necessary to have hard polymers. However, to ensure that wood is not damaged during heating, it is important that self-healing occurs at low temperature (under 100°C). As a result, the challenge is to obtain a UV-curable coating resistant to ambient conditions that heals under low temperature.
UV-curable self-healing coatings also are presented in literature. Wang Z. et al.11 developed UV-curable polyurethane that is self-healing. The healing property is based on Diels-Alder reaction and thiol-ene click reaction and occurs at 90°C. Saman N.M. et al.12 investigated UV-curable alkyd coating containing capsules to ensure self-healing behavior. Liu J. et al.13 explored hard core – flexible arm structure. They prepared UV-curable polyurethane with hydrogen binding in the flexible part of the material. Thus, the hydrogen bond has been used to study UV-curable self-healing materials, but only with polyurethane coating. In the case of the wood industry, acrylate UV-curable coatings are investigated.
The objective of this work was to develop and evaluate intrinsic self-healing formulations applicable to the wood industry – more specifically – the hydrogen bond. Formulation of UV-curable acrylate coatings creating a hydrogen bond was developed, and their self-healing behavior has been characterized.
Experimental section
Materials
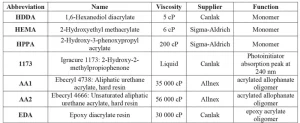
Monomers and oligomers selected for this work are low-toxicity acrylates with alcohol or amide groups providing intermolecular hydrogen interactions. Based on preliminary study of mechanical properties, two monomers and two oligomers were selected to test their self-healing behavior. The two monomers with alcohol groups were HEMA and HPPA, presented in Table 1. The two oligomers selected were acrylated allophanate (AA1, AA2) also presented in Table 1. The reference coating, without hydrogen bond, was prepared with HDDA and EDA. The structures are presented in Figure 114.
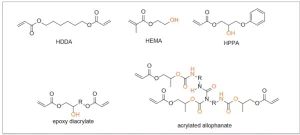
Coating formulation and application procedure
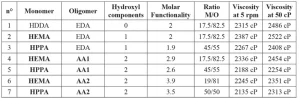
Each formulation was prepared from one monomer, one oligomer and one photoinitiator (1173). The ratio of monomer to oligomer was set to reach a viscosity of 2000 cP. Oligomer, monomer and photoinitiator were added successively in a metallic flask and stirred with a high-speed disperser (Dissolver DISPERMAT LC30) at 600 rpm. Table 2 presents the formulations composition, the viscosity and the molar functionality. The formulations’ molar functionality was calculated using Equation (1)
with f being the functionality and n the mole quantity.
The formulations were applied on several substrates (glass or metallic panel according to tests) with a square applicator film (PA-5353, from BYK) of 100 µm thickness. The films were cured in a UV oven (ATG 160 305 from Ayotte techno gaz) at 150 mW/cm2 200 mJ/cm2. A mercury lamp (UV mac 10 from Nordson) emitting at 200 to 300 nm was used.
Photo-differential scanning calorimetry (Photo-DSC)
Photo-DSC analysis was performed with a Mettler Toledo DSC 822e and the LC5 UV mercury spotlight (from Hamamatsu). The lamp intensity was set to 50 mW/cm² with an emission wavelength ranging from 240 nm to 400 nm. In an open aluminum pan, 1.9 ± 0.1 mg of each formulation was deposited. Samples were irradiated for 1 min. The resulting curve corresponds to the difference of heat flow between the reference (empty pan) and the sample. The measurement was performed at constant temperature (30°C) using the following method: (1) 1 min. without irradiation, (2) 1 min. with UV, (3) 2.5 min. without irradiation, (4) 1 min. with UV and (5) 0.5 min. without irradiation. The first irradiation ensures the photopolymerization, and the second one was performed to measure the irradiation energy as a blank curve. The second irradiation segment was subtracted from the first one. The integration of the resulting curve was calculated. Then, the conversion was estimated by the StarE software from the integration and the theoretical enthalpy. This last parameter was calculated as described by the Equation (2)
with f being the functionality, W the weight fraction, M the molar mass and ΔH acrylate is 86 kJ/mol15.
Dynamic mechanical analysis measurements (DMA)
DMA measurements were performed from 30°C (or 0°C for low glass transition temperature (Tg) coating) until Tg + 70°C at 3°C/min. The parameters selected were the following: 125% of force track, preload at 0.1 N and 0.2% of strain. Samples measuring 2.5 x 0.5 cm were cut using a CO2 laser LMC-2000 (laser machine center, from Beam Dynamic). Information obtained by DMA are the loss modulus, the storage modulus and the tan (δ) curves depending on temperature. The maximum of loss modulus represents the Tg. The minimum of storage modulus was used to calculate the cross-linking density following Equation (3)
Where E′ is the storage modulus in the rubbery plateau at Tg + 50°C, R is the gas constant and T is the temperature at Tg + 50°C.
Self-healing characterization
Scratch resistance experiments
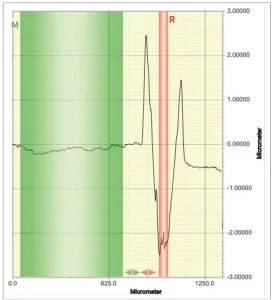
Coatings were applied on Q-panels R-36. Scratches were performed using a multi-finger scratch/mar tester (Model 710 from Taber Company), using a 10 N weight and a spherico-conical tip of 1 mm radius. The Dektak 150 contact profilometer (from Veeco) was used to measure scratch depth. Three coatings were prepared from each formulation. Two scratches were prepared on each coating, and three profilometer measurements were performed per scratch. Profilometry measurements were realized using a 2.5 µm radius tip and a 1 mg weight. The profilometer measurement was 2,500 µm in length and 20 s in duration. The software was set on “high and valley” profile at a resolution of 524 µm. From the scratch profile (Figure 2), the software measures the scratch depth following Equation (4).
Scratch depth before and after healing was used to calculate self-healing efficiency Equation (5). Healing was performed by placing the sample in an oven at 80°C for 2 h.
Color measurements
As abrasion creates a white color on the coating, color measurements were used to characterize self-healing property. Coatings were applied on black glass panels (#3720 from BYK) following the application procedure described previously. Abrasion was performed with the abrasion and washability tester from Elcometer (#1720), using a Scotch Brite hand pad 7447 (from 3M) as abrasion pads. Five cycles of abrasion were performed at a speed of 37 cycles/min. Then, samples were heated at 80°C for 2 hrs in the oven. Color measurements were performed before and after abrasion tests and after heating. Coatings’ color was measured using a X-rite Ci6x spectrophotometer. L*, a*, b* values were retrieved from the colorIQ software. The color difference ΔE (before and after healing) was calculated in CIELab system as described in Equation (6):
Results and discussion
Photo-DSC
The photo-DSC measures the enthalpy of photopolymerization to calculate the conversion yield of the acrylate formulation. Table 3 presents the results of photo-DSC measurements.
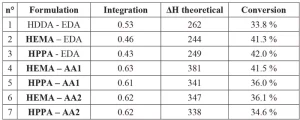
Photo-DSC results indicate conversion yields between 35% and 42%. These rather low yields can be attributed to the low lamp intensity of 50 mW/cm2 (the maximum of the lamp), instead of the 150 mW/cm2 generally used for the irradiation for these acrylate coatings photopolymerization. To ensure this point, UV cured films were characterized by FTIR spectroscopy, and the results are published in Coatings Journal14. Also, these coatings are the sealer layer, which does not need to be 100% polymerized to ensure good interlayer adhesion. It is notable that the reference coating (n°1) has the lowest conversion yield due to the highly reactive monomer. The higher the formulation reactivity, the lower the conversion yield, as the network will cross-link and stiffen faster. For the same reason, the lower the formulation functionality, the higher the conversion yield16. This explains the high conversion yield of the coatings n°2 and 3, which have functionality of 2 and 1.9, respectively. Conversion yield will be compared with the self-healing results in the following sections.
Dynamic mechanical analysis (DMA)
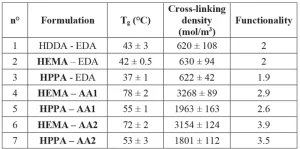
DMA measurements were used to characterize the Tg of the coatings and their cross-linking density. Results are presented in Table 4.
It is notable that the Tg follows the same pattern as the cross-linking density. The Tg represents the temperature at which the material changes from glass to rubber state. In the glass state, the polymer chains have low mobility, but above the Tg polymeric chains have enough thermal energy to ensure mobility. High cross-linking implies low chain mobility, which means that more thermal energy is necessary to ensure chain movements. This explains the relation between Tg and cross-linking density. For the same reason, high formulation functionality induces high cross-linking density and high Tg.
The results indicate that coatings with HEMA monomer and acrylated allophanate oligomers (n°4, 6) have high cross-linking density and Tg values. Also, reference coating HDDA – EDA (n°1) has quite a low Tg and cross-linking density. The results can be explained by the average coating functionality.
Self-healing characterization by scratch depth
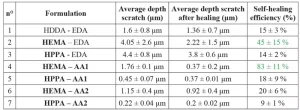
Self-healing property was characterized using contact profilometry. Scratch depth before and after healing was measured. The resulting self-healing efficiency is presented in Table 5.
The coating HEMA – AA1 (n°4) presents the highest self-healing efficiency. Also, the coating HEMA – EDA (n°2) shows self-healing property.
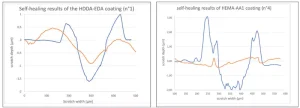
The coating n°2 has only one component with hydroxyl groups, leading to a low concentration of hydrogen bonds. This explains the lower healing efficiency compared to coating n°4. The reference coating (n°1) does not have a reversible bond. The 15% of scratch depth measured is due to its elasticity. In fact, the heating at 80°C releases elastic stress of the material induced by the scratch. Thus, the low healing efficiency is considered as the elastic part of the stress. The contact profilometry results are presented in Figure 3 and indicate the scratch profiles of these coatings. It is notable that HPPA monomer and AA2 oligomer do not provide self-healing. This could be due to steric hindrance, as HPPA monomer contains an aryl group.
According to this study, two coatings (n°2 and 4) show self-healing behavior. HEMA monomer provides a self-healing property. Also, the higher the hydrogen bonds quantity, the higher the self-healing efficiency. It is notable that the self-healing coatings also are the ones with the highest conversion. These results show that UV-curable coatings can have enough chain mobility to repair even when they are highly cross-linked. Other self-healing characterization by scratch depth measurement were performed on ductile scratches14.
Self-healing characterization by color measurements
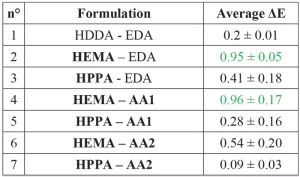
A new method is used to characterize self-healing property. As scratches’ formation on transparent coatings leads to whitening (due to light diffusion on roughness), color measurements can be used to measure healing efficiency. If the coating is self-healing, it normally should revert to transparent after heating. ΔE is the color change of the coating after abrasion, before and after heating. Low ΔE means that the coating does not change during heating, so no healing occurs. High ΔE means that the color of the coating changed, in this case reverted to transparent. Coatings with high ΔE thus have high self-healing efficiency behavior. The results are presented in Table 6.
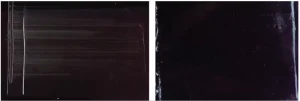
The coatings HEMA – EDA (n°2) and HEMA – AA1 (n°4) show higher self-healing efficiency. This result coincides with results obtained for the self-healing scratch study. The values of ΔE are relatively low, as the white aspect of abrasion could be due to light scattering on roughness. The color measurement proceeded without surrounding light, so there is no light scattering. This can explain the low ΔE values. Theoretically ΔE less than 1 indicates that the difference between the two colors is not noticeable by the observer. To see the difference between two colors, the value of ΔE must be greater than 217. To take in account the light scattering, gloss measurements were performed to evaluate self-healing14. Photographs of the coatings on a black glass panel in Figure 4 indicate that the reference coating HDDA-EDA (n°1) still has abrasion after 2h heating at 80°C. At the opposite, the coating HEMA-AA1 (n°4) is completely repaired.
Conclusion
The challenge was to obtain resistant UV-curable coatings with intrinsic self-healing properties applicable to the wood industry. Coatings must be highly cross-linked but also must have enough chain mobility to allow healing. Results indicate that HEMA monomer and AA1 oligomer provide good self-healing behavior as well as good mechanical properties. Also, the quantity of hydrogen bonds impacts self-healing efficiency. DMA and photo-DSC measurements show that self-healing coatings (n°2 and 4) are highly cross-linked and one of the most polymerized. This innovation presents hydrogen-based self-healing behavior on UV-curable acrylate coatings. Moreover, the healing occurs at 80°C. In conclusion, this system is self-healing, highly cross-linked and applicable to the wood industry as a sealer in the finish system.
Chloé PAQUET received a BS in chemistry and master’s degree in materials chemistry and physical chemistry from Université de Bordeaux (France). She currently is pursuing her PhD at the Wood Science Department of Laval University, Québec, Canada, with Dr. Véronic Landry. Her research focuses on self-healing UV-curable acrylate coatings for wood flooring.
Dr. Jean-Francois Morin has been a professor in the Department of Chemistry at Université Laval since 2006. His research interests include carbon nanomaterials synthesis for field-effect transistors as well as organic semiconducting materials and dendrimers for theranostics.
Dr. Véronic Landry, the NSERC/Canlak Industrial Research Chair in interior wood-product finishes, has been an associate professor in the Department of Wood and Forest Science, Faculty of Forestry, Geography and Geomatics (FFGG), at Laval University since April 2017. Her team develops indoor wood products for mechanical performance, fire resistance and aesthetics.
References
- Blaiszik BJ, Kramer SLB, Olugebefola SC, Moore JS, Sottos NR, White SR. Self-Healing Polymers and Composites. Annu Rev Mater Res. 2010;40(1):179-211. doi:10.1146/annurev-matsci-070909-104532
- Dewar MJS, Pierini AB. Mechanism of the Diels-Alder reaction. Studies of the addition of maleic anhydride to furan and methylfurans. J Am Chem Soc. 1984;106(1):203-208. doi:10.1021/ja00313a041
- Chen X, Dam MA, Ono K, et al. A thermally re-mendable cross-linked polymeric material. Science. 2002;295(5560):1698-1702. doi:10.1126/science.1065879
- White SR, Sottos NR, Geubelle PH, et al. Autonomic healing of polymer composites. Nature. 2001;409(6822):794-797. doi:10.1038/35057232
- Wilson GO, Porter KA, Weissman H, White SR, Sottos NR, Moore JS. Stability of second generation grubbs’ alkylidenes to primary amines: Formation of novel ruthenium-amine complexes. Adv Synth Catal. 2009;351(11-12):1817-1825. doi:10.1002/adsc.200900134
- Meng H, Xiao P, Gu J, et al. Self-healable macro-/microscopic shape memory hydrogels based on supramolecular interactions. Chem Commun. 2014;50(82):12277-12280. doi:10.1039/C4CC04760E
- Boyer DB, Chalkley Y, Chan KC. Correlation between strength of bonding to enamel and mechanical properties of dental composites. J Biomed Mater Res. 1982;16(6):775-783. doi:10.1002/jbm.820160604
- Liu R, Yang X, Yuan Y, Liu J, Liu X. Synthesis and properties of UV-curable self-healing oligomer. Prog Org Coat. 2016;101:122-129. doi:10.1016/j.porgcoat.2016.08.006
- Hilger C, Stadler R. Cooperative structure formation by combination of covalent and association chain polymers: 4. Designing functional groups for supramolecular structure formation. Polymer. 1991;32(17):3244-3249. doi:10.1016/0032-3861(91)90148-C
- Cortese J, Soulié-Ziakovic C, Tencé-Girault S, Leibler L. Suppression of Mesoscopic Order by Complementary Interactions in Supramolecular Polymers. J Am Chem Soc. 2012;134(8):3671-3674. doi:10.1021/ja2119496
- Wang Z, Liang H, Yang H, et al. UV-curable self-healing polyurethane coating based on thiol-ene and Diels-Alder double click reactions. Prog Org Coat. 2019;137:105282. doi:10.1016/j.porgcoat.2019.105282
- Saman NM, Ang DT-C, Shahabudin N, Gan SN, Basirun WJ. UV-curable alkyd coating with self-healing ability. J Coat Technol Res. 2019;16(2):465-476. doi:10.1007/s11998-018-0124-x
- Liu J, Cao J, Zhou Z, Liu R, Yuan Y, Liu X. Stiff Self-Healing Coating Based on UV-Curable Polyurethane with a “Hard Core, Flexible Arm” Structure. ACS Omega. 2018;3(9):11128-11135. doi:10.1021/acsomega.8b00925
- Paquet C, Schmitt T, Klemberg-Sapieha JE, Morin J-F, Landry V. Self-Healing UV Curable Acrylate Coatings for Wood Finishing System, Part 1: Impact of the Formulation on Self-Healing Efficiency. Coatings. 2020;10(8):770. doi:10.3390/coatings10080770
- Lee TY, Guymon CA, Jönsson ES, Hoyle CE. The effect of monomer structure on oxygen inhibition of (meth)acrylates photopolymerization. Polymer. 2004;45(18):6155-6162. doi:10.1016/j.polymer.2004.06.060
- M. Braithwaite SD. Chemistry & Technology of Uv & Eb Formulation for Coatings, Inks & Paints, Volume 4: Formulation. SITA Technology; 1991. Accessed February 12, 2020. https://www.biblio.com/book/chemistry-technology-uv-eb-formulation-coatings/d/1248824156
- Mokrzycki W, Tatol M. colour difference ΔE – a survey.October 8, 2012.