By Zhijia Du, Oak Ridge National Laboratory, and Sage Schissel, PCT Ebeam and Integration, LLC
It is no secret batteries have become intrinsic to everyday life. Batteries have made mobile technology possible – from the flashlight to the Walkman to the cell phone – and, in turn, technology has demanded battery development keep pace. As batteries become more compact, powerful and flexible, technology already has designs to use those improvements to produce smaller, longer-lasting wearable devices or electric vehicles with increased range and faster recharging. Thus, it likely is no surprise that battery production has only increased over the last century. Lithium-ion batteries alone have experienced exponential growth, increasing globally from 0.5 gigawatt-hours (GWh) in 2010 to over 500 GWh in 2021.1
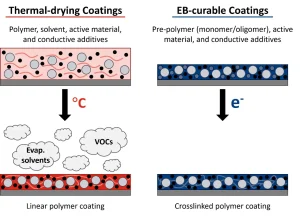
However, while battery production grows, so too does its environmental impact. Conventional manufacturing for lithium-ion batteries, for example, uses the organic solvent NMP (N-methyl-2-pyrrolidone).2 The components of the electrodes – active materials, conductive additives and polymer binders – are mixed with the solvent to form a slurry that can be coated onto a metal foil (Figure 1). The NMP then must be evaporated using a thermal oven. Solvent evaporation is well known to be an energy-intensive process with production speeds limited by oven length and required dwell time.3 Solvent recovery also is necessary to reduce the volatile organic compounds (VOCs) released into the environment. Even the environmental impact of shipping the solvent must be considered. In addition, restrictions on the use of NMP recently have been implemented in the European Union (EU) due to its effects on human health, including reprotoxicity.4
Of course, the costs associated with solvent usage are not only environmental but also monetary. Eliminating NMP would reduce material costs (from $1.50 up to $3.00/L) as well as energy consumption; the latter contributing to an estimated 2x reduction in electrode production cost if NMP is replaced with water.5,6 Dry room space is a substantial cost in lithium-ion battery manufacturing. Minimizing the process footprint by replacing thermal ovens with a more compact technology also helps minimize cost. Furthermore, increasing production speeds without increasing the process footprint improves on the cost per unit. Cost reduction is an important aspect of consumer accessibility. In the case of electric vehicles (EVs), for instance, costs have been cut from $1,200/kWh in 2010 to $132/kWh in 2021; however, the battery price point at which it is estimated EVs become comparable in price to internal combustion vehicles is ≤ $100/kWh.7
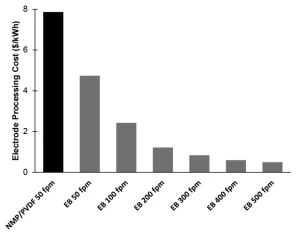
The elimination of solvent, reduced energy consumption, smaller footprint and faster processing speeds are all achievable with the incorporation of ultraviolet (UV) or electron beam (EB) technology in battery manufacturing.2,8,9 The conventional polymer binder (typically polyvinylidene difluoride, PVDF) needs to be dissolved with a solvent (NMP) to be properly mixed with the active materials and conductive additives that form an electrode. In contrast, radiation-curable pre-polymer resins generally are liquid, which allows for mixing, and are polymerized instantaneously (as fast as < 1s) and solvent-free (Figure 1). Figure 2 shows the cost reduction benefit when electron-beam curing is used to replace the NMP drying/recovering process in electrode manufacturing.3,6,10 When a similar line speed (50 fpm) is used, EB processing can save approximately 40% of the cost. Yet, when the instantaneous nature of EB polymerization is taken advantage of and the faster speed of 500 fpm is used, the cost can be decreased to as little as 6% of the NMP-based process. Furthermore, the energy consumption for NMP/PVDF processing is ~151 MJ/kWh, while EB processing only requires ~27 MJ/kWh. This energy reduction translates into much lower greenhouse gas emissions – the NMP/PVDF process generates ~93 lbs CO2/kWh vs. ~17 lbs CO2/kWh generated by the EB process.
The method of replacing PVDF electrode binders with EB-curable resin is presented in Du, et al. (2019).2 Here, cathode coatings were prepared with a low molecular weight, acrylated polyurethane dispersion, irradiated via EB at 500 fpm and made into pouch cell stacks. The performance of these cell stacks then was compared to cell stacks made with the conventional PVDF binder. Overall, when high polymer conversions were achieved, the EB cell stacks showed cycling rate performance and capacity retention similar to that of the PVDF cell stacks. As with other EB-curing applications, nitrogen inertization proved to be vital.11,12 Samples that experienced oxygen inhibition did not fully cure and battery performance suffered as a result.
While both EB and UV technology can be successful in this application, EB was chosen because of several advantages. Electrodes contain carbon black and other optically opaque materials which restrict light penetration, and thus, UV-cured electrodes are limited in thickness.12 EB penetration is independent of material opacity and is instead governed by the material density and the accelerating voltage of the electrons. Du, et al. reports 250 g/m2-thick electrodes EB-polymerized at 275 kV compared to UV-cured electrodes at just 60 g/m2.2 Thicker electrodes allow for batteries with higher energy densities. Additionally, photopolymerization requires photoinitiator where EB polymerization does not. Although the photoinitiator generally is only a small fraction of a formulation, this fraction can be dedicated in an EB-curable electrode to increasing the active materials.
While nascent to battery manufacturing, an advantage of both UV and EB is that these technologies are well established in other industries. Both have decades of success in packaging, architectural products and adhesives. Although the existing UV/EB knowledge base may not always directly translate to this new application, the foundation is solid, and the basic principles that encourage adoption (i.e., low energy consumption, instant, solvent-free, etc.) remain unchanged.
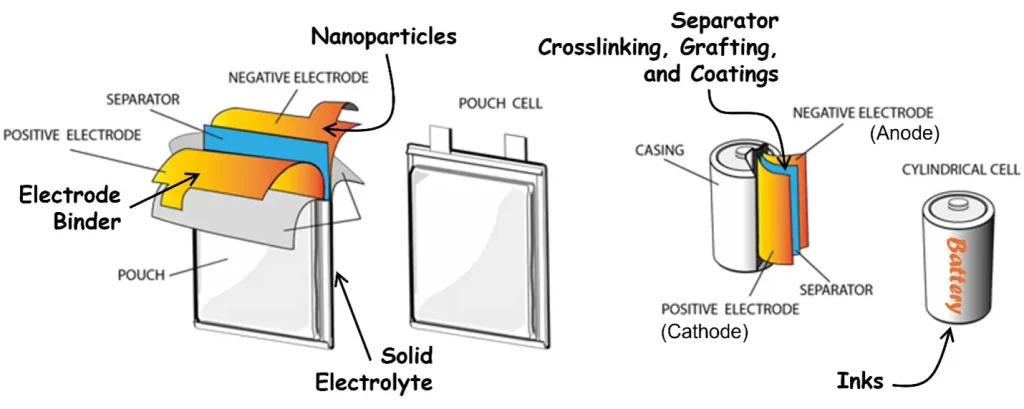
Moreover, manufacturers should consider the diversity of available opportunities to incorporate UV/EB technology into battery production (Figure 3). In addition to electrode binders, there is potential to make use of UV/EB on just about every component – grafting, coating and/or crosslinking the separator for robustness, heat resistance and better Li ion mass transport14-19; synthesis of nanoparticles to coat the electrodes for improved electrochemical performance20-23; formation of a solid electrolyte for safer batteries24,25; and even polymerization of the inks on the casing for an eye-catching battery. Adoption of most new technology in an existing industry is arduous, but, in the case of UV/EB, the investment in time, effort and equipment can be distributed over multiple promising avenues.
Currently, there still is much progress to be made for UV/EB technology in the battery industry. These innovations exist primarily in academic literature, and it will not be trivial to implement them on the production floor. Specifically, in the case of the EB-curable binder, the reported attempts still needed the addition of water and isopropanol to make a liquid, coatable slurry.2 Future endeavors will attempt dry or high-solid-loading paste coating to further eliminate solvent and thermal drying26, but it is unlikely to be the last challenge EB battery processing will face.
Despite these obstacles left to conquer, adoption of UV/EB technology in battery manufacturing holds great promise for the industry. Lower costs, faster processing and reduced environmental impact are needs that UV/EB can deliver upon in leaps and bounds. With demand for lithium-ion batteries expected to soar to an astounding 9,300 GWh by 20301, now is the time to consider how these technologies can support the production of greener, better performing batteries.
References
- Bullard, N., 2020. This is the Dawning of the Age of the Battery. Bloomberg. https://www.bloomberg.com/news/articles/2020-12-17/this-is-the-dawning-of-the-age-of-the-battery?srnd=green#xj4y7vzkg
- Du, Z., Janke, C. J., Li, J., Wood, D. L., 2019. High-speed electron beam curing of thick electrode for high energy density Li-ion batteries. Green Energy Environ.4, 375-381.
- Wood, D. L., Quass, J. D., Li, J., Ahmed, S., Ventola, D., Daniel, C., 2018. Technical and economic analysis of solvent-based lithium-ion electrode drying with water and NMP. Drying Tech. 36 (2), 234-244.
- Sherwood, J., Farmer, T. J., Clark, J. H., 2018. Catalyst: Possible Consequences of the N-Methyl Pryrolidone REACH Restriction. Chem. 4 (9), 2010-2012.
- Li, J., Du, Z., Ruther, R. E., An, S. J., David, L. A., Hays, K., Wood, M., Phillip, N. D., Sheng, Y., Mao, C., Kalnaus, S., Daniel, C., Wood, D. L., 2017. Toward Low-Cost, High-Energy Density, and High-Power Density Lithium-Ion Batteries. JOM. 69, 1484-1496.
- Ahmed, S., Nelson, P. A., Gallagher, K. G., Dees, D. W., 2016. Energy impact of cathode drying and solvent recovery during lithium-ion battery manufacturing. J. Power Sources. 322, 169-178.
- Henze, V., 2021. Battery Pack Prices Fall to an Average of $132/kWh, But Rising Commodity Prices Start to Bite. https://about.bnef.com/blog/battery-pack-prices-fall-to-an-average-of-132-kwh-but-rising-commodity-prices-start-to-bite/
- Odian, G., 2004. Principles of Polymerization. 4th Ed.
- Mehnert, R., Pincus, A., Janorsky, I., Stowe, R., Berejka, A., 1998. UV & EB Curing Technology & Equipment Volume 1. Wiley.
- Batteries 2020 Annual Progress Report. U.S. Department of Energy. https://www1.eere.energy.gov/vehiclesandfuels/downloads/VTO_2020_APR_Batteries_compliant_.pdf
- Schissel, S.M., 2021. Comparing EB and UV: Common Questions. UV+EB Tech. (2), 14-15.
- Thiher, N. L. K., Schissel, S. M., Jessop, J. L. P., 2020. Quantifying UV/EB dual cure for successful mitigation of oxygen inhibition and light attenuation. Prog. Org. Coat. 138, 105378.
- Barnett Technical Services. Anisotropic Thermal Conductivity and Diffusivity Measurements of Li-ion Battery Structures. https://barnett-technical.com/steves-solutions/hot-disk-battery-anisotropy/
- Berejka, A., 2004. Electron beam grafting of polymers. Advances in radiation chemistry of polymers. IAEA. 85-90.
- Jiang, X., Zhu, X., Ai, X., Yang, H., Cao, Y., 2017. Novel Ceramic-Grafted Separator with Highly Thermal Stability for Safe Lithium-Ion Batteries. ACS Appl. Mater. Interfaces. 31 (9), 25970-25975.
- Sheng, L. Song, L., Gong, H., Pan, J., Bai, Y., Song, S., Liu, G., Wang, T., Huang, X., He, J., 2020. Polyethylene separator grafting with polar monomer for enhancing the lithium-ion transport property. J. Power Sources. 479 (15), 228812.
- Sohn, J. Y., Gwon, S. J., Choi, J. H., Shin, J., Nho, Y. C., 2008. Preparation of polymer-coated separators using an electron beam irradiation. Nucl. Instrum. Methods Phys. Res. B. 266 (23), 4994-5000.
- Choi, Y., Kim, J. I., Moon, J., Jeong, J., Park, J. H., 2018. Electron beam induced strong organic/inorganic grafting for thermally stable lithium-ion battery separators. Appl. Surf. Sci. 444, 339-344.
- Kim, K. L., Park, M. S., Yim, T., Yu, J. S., Kim, Y. J., 2014. Electron-beam-irradiated polyethylene membrane with improved electrochemical and thermal properties for lithium-ion batteries. J. Appl. Electrochem. 44, 345-352.
- Kang, H. S., Kim, B., Park, J. H., Kim, H. W., Koo, Y. H., Bae, H. B., Park, C. M., Lee, B. C., 2013. Size Control Technology of Silver Nanoparticles Using Electron Beam Irradiation. Bull. Korean Chem. Soc. 34 (12), 3899.
- De Freitas, L. F., Varca, G. H. C., Batista, J. G. D. S., Lugao, A. B., 2018. An Overview of the Synthesis of Gold Nanoparticles Using Radiation Technologies. Nanomaterials. 8 (11), 939.
- Bindumadhavan, K., Chang, P. Y., Doong, R. A., 2017. Silver nanoparticles embedded boron-doped reduced graphene oxide as anode material for high performance lithium ion battery. Electrochim. Acta. 243, 282-290.
- Yin, S., Qing, J., Zuo, X., et. al., 2018. Silicon lithium-ion battery anode with enhanced performance: Multiple effects of silver nanoparticles. J. Mater. Sci. Technol. 34 (10), 1902-1911.
- Hou, J., Park, I. K., Cha, W. J., Lee, C. H., 2021. A Gel Polymer Electrolyte Reinforced Membrane for Lithium-ion Batteries via the Simultaneous-Irradiation of the Electron Beam. Membranes. 11 (3), 219.
- Sakakibara, T., Kitamura, M., Honma, T., Kohno, H., Uno, T., Kubo, M., Imanishi, N., Takeda, Y., Itoh, T., 2019. Cross-linked polymer electrolyte and its application to lithium polymer battery. Electrochin. Acta. 296, 1018-1026.
- Hawley, W. B., Li, J., 2019. Electrode manufacturing for lithium-ion batteries – Analysis of current and next generation processing. J. Energy Storage. 25, 100862.