The upcoming midterm elections in the US, along with the continuous doublespeak from both sides of the political aisle, are the inspiration for this quarter’s column. I no longer wonder why most internet polls rank politicians as one of the least trusted professions. The only campaign promise I have believed was on the button at the top of this page.
Do we “stretch the truth” in our personal lives? Without admitting or denying anything, I allegedly may have used some of these examples in the past: “You look great in that outfit,” “These tools are not new, I’ve had them for a while,” “Wow, you’ve lost weight,” “I was stuck in traffic” or “I only had one drink.”
Do we also “stretch the truth” in UV and create what I call “Little Purple Lies” in these common “truth-stretching” statements below?
Your baby is adorable.
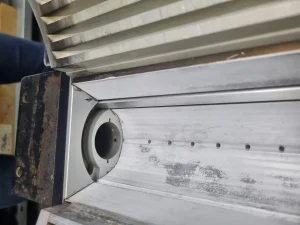
I find all puppies and some babies adorable. Crying, over-tired, spitting up, teething, colicky babies who needed a diaper change two hours ago are not adorable.
We need to adopt this same attitude to address UV systems that are not matched to the process or application. There is nothing adorable about a UV system that is not matched to the application, or that needs maintenance. Is the system well maintained? Is there any wiggle room in the process window? (See Image 2.)
You haven’t changed a bit.
If you last saw me a few weeks ago, I might believe you. Saying this about equipment used in a manufacturing environment is not realistic. Have you documented your process and UV sources when things were curing? Systems and lamps age, or a component or key piece of equipment will malfunction. Reflectors and LED quartz windows can become contaminated. Changes can be made to the equipment settings, many unintentional.
Check with the manufacturer of your radiometer for the recommended service interval. We receive requests to service models of our legacy instruments that were new 16 years ago and have never been back for service. Understand your system and establish an interval for confirming that the key parameters and your radiometer haven’t changed.
I didn’t touch it.
Do you hear this from your kids or coworkers? When a source manufacturer hears that you didn’t touch it, this most likely means that you also didn’t maintain it.
I would never lie to you.

Trust is earned over time and should be a two-way street between a supplier and a customer. It starts when you select the equipment and formulation for your process and continues in the form of support when required. We have had radiometers and sensors returned, with customers insisting the instruments were used within their specified operating range and not exposed to any coatings. (See Image 3.)
It didn’t cost that much.
Many years ago, my dive buddies and I foolishly tried to hide the cost of our underwater cameras by pricing them in BTUs… defined as a “Basic Toy Unit” (not a “British Thermal Unit”), with one BTU equal to $1,000. A camera system costing 3.5 BTUs was $3,500. When we got caught, the BTU doubled in value to $2,000: $1,000 for the camera equipment and $1,000 for things our significant others purchased in retaliation. In the end, our cameras cost twice as much as originally budgeted.
Don’t make foolish mistakes when it comes to determining what it really costs to acquire and maintain UV systems. The cost to buy the right equipment, keep it in peak condition through regular preventative maintenance and measure as needed is much less than the cost of producing unacceptable products, having to rerun a job or scrambling to find a solution when your line is down.
I have no idea where “it” is.
Some common UV “its” that people look for include the following:
- Process documentation: Is your process documented, or is the secret recipe needed to make your process work only known by one person? Documentation could include set-up instructions, equipment settings, troubleshooting guides, maintenance instructions and a maintenance schedule.
- Spare parts: Do you carry stock of common consumable items for your sources, or do you wait until something breaks to place an order? Based on the UV system, your on-hand stock could include bulbs, quartz plates, reflectors and air filters.
- Radiometer and system for organizing the collected data: I also suggest having the radiometer manual and setting a calendar reminder for when service is next due.
- Supplier contacts: Do you have these contacts organized in one place?
I had no way to contact you.
This may have worked 30 years ago (I couldn’t find a pay phone), but today there are multiple ways (cell phone, texting, social media and email) to reach out other than a business phone.
We also have entered an era where newer equipment is able to monitor and provide feedback (Internet of Things) if conditions or equipment performance has changed. Imagine receiving notifications that your power supply or equipment settings have been adjusted or changed.
It’s not you, it’s me.
I fasten my seatbelt when I hear this either in a personal or professional setting. Is this a prelude to a breakup? Most formulators would love to receive a call from a customer stating that the process changed, and this change in the process was the root cause of curing issues – not the formulation.
I’ll respect you in the morning.
If you want me to respect you in the morning, demonstrate that you can establish, monitor and adjust the key parameters of your UV process today and every day.
Jim Raymont
Director of Sales
EIT LLC
jraymont@eit.com