By Liz Stevens, writer, UV+EB Technology
Like most in healthcare industry, dentistry is adopting new technologies to work better, faster and more economically. Orthodontics is no exception: there are improved methods emerging for straightening teeth. Vitro3D, a startup in Boulder, Colorado, is leading the charge to finetune and commercialize the use of volumetric 3D printing to help the dental industry make advances, initially applying its technology to the dental aligner market. Dental aligners are an alternative to braces that substitute custom-molded clear plastic mouthpieces for metal brackets and wire.
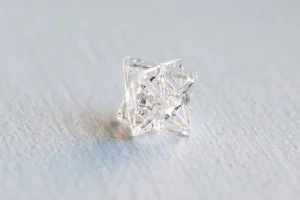
While an intraoral scan still is required for determining the contours of a patient’s mouth, gums and teeth, rather than using the scan to create a mold, around which braces or a traditional plastic dental aligner would be formed, Vitro3D avoids the mold-creation step and translates the scan details directly into coordinates for a 3D-printed photopolymer aligner. The company earned a RadTech 2022 RadLaunch Award for its new methodology and its proprietary printer. Vitro3D describes its method as a form of UV photopolymerization that is more sustainable, 100 times faster than the traditional method and which produces more accurate or higher-resolution aligners (read: better patient comfort). UV+EB Technology spoke with Dr. Camila Uzcategui, Vitro3D co-founder and CEO.
The backstory
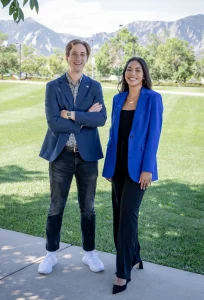
Dr. Uzcategui earned her PhD at the University of Colorado Boulder where she focused on 3D printing for life science applications and, specifically, for tissue engineering and regeneration with Dr. Stephanie Bryant and Dr. Robert McCleod. “Dr. McCleod’s lab started a collaboration with Lawrence Livermore National Labs and the University of California Berkeley,” said Uzcategui, “where they had just developed this new type of 3D printing called volumetric 3D printing.” While exploring the new technology, Uzcategui also developed an interest in entrepreneurship and commercializing technologies out of the laboratory. She and co-founder Dr. Johnny Hergert conducted customer discovery interviews to identify potential life science industries where volumetric 3D printing would fill a need. “After 130 interviews,” she explained, “we were considering 3D printing organoids for drug testing and evaluating medical devices. But at a conference in November of 2021, we were approached by folks in the dental industry.”
Uzcategui subsequently discovered a big need for new technology for dental aligners. “The dental aligner industry is the biggest user of light-based 3D printing in the world,” she said, “and the traditional process is multi-step and quite cumbersome.” In reviewing the typical scan-mold-thermoform process for aligners, the team had an inspiration: Why not directly 3D print the aligner rather than going through this multi-step process? Volumetric 3D printing could output a better-fitting aligner faster, with less steps and for a lower cost; those features and the range of materials available signaled a good fit for aligners.
The method and the technology
Volumetric 3D printing, as described in the engineering.com article, “Volumetric 3D Printing is Becoming a Reality,”1 is unlike most other 3D methods since a printed object is not created layer by layer. “Instead, the object’s pattern is repeatedly projected into a transparent liquid resin. Like the opposite of a CT scan, light images are continuously applied into the resin from various angles. This repetition rapidly solidifies the object in the resin tank.”
Traditional 3D printing methods rely on interior scans of objects to reconstruct a model layer by layer. Volumetric 3D printing projects a pattern with lasers to create a model with instantly-curing, intersecting points – an object created simultaneously in all three dimensions without the need for support structures. Fast print speed is a key feature, along with smoother surfaces, a wider range of usable materials with higher viscosities than those traditionally used in 3D printing, and the ability to print around pre-existing structures.
Uzcategui described Vitro3D’s volumetric 3D printing in additional detail. “We take a scanned 3D image of a patient and deconstruct it into the different angles required to reconstruct a 3D object,” she said. “Our software then uses a patented algorithm to guide reconstruction of the object. We use a liquid photopolymer resin-filled volume which can be a cylinder or, as in our case, a cartridge. While the cartridge is rotated, we project in the images at the different angles that we generated with the algorithm. During rotation, all of the intensities from the different projected angles add up and then the entire volume polymerizes at once.”
Vitro3D uses its own custom-designed 405 nm laser printer with a new volumetric 3D printing geometry that allows for larger print sizes while maintaining high resolution. Post-processing for this method is similar to that of other resin-based 3D printing, although it does not include separation of printed objects from their support structures since volumetric 3D printing does not require those structures. Uzcategui noted that printer design is one of the main hurdles in this project. “In terms of technical challenges,” she said, “it is getting the right form factor that we are going after; we still are working on that. We have a form factor right now that is a little larger than we would like, so we are working on making it smaller, to be more of a desktop-type printer.”
Commercialization
Vitro3D envisions having a product ready for launch next year. “We are in the early stage,” she said, “so we still are working out the kinks and hoping to have a product on the market by late 2023. We are seeing the early versions of the printer working well with the partners we have identified so far.”
In describing the company’s success in forging partnerships to bring its method and product to market, Uzcategui credits the team’s extensive customer discovery process and also cites the big RadTech boost. “The RadTech award and being featured in the magazine for getting the RadLaunch award was very helpful,” she said.
As the team finishes finetuning the printer design, it also has plans for the next iteration of the printer. “The next generation of our printer will have internal post-processing capabilities,” said Uzcategui. “All of the washing and post-curing will happen in the printer, inside of the cartridge.”
Vitro3D’s future
“As a small startup with limited resources,” said Uzcategui, “we wanted to be able to get to market quickly. 3D printing in tissue engineering and other spaces that require regulatory hurdles creates a long pathway to commercialize any product that will go into the body or be used as some sort of implant to the body.” Recognizing this reality, Vitro3D chose to first concentrate on the dental and orthodontics arena. “Rather than seeing this as a change in our plans, we see it as a change of timing. We see ourselves going into the tissue engineering market in the future since our printer will be applicable to that market’s needs as well; all that will vary is the material that we use inside the cartridges.”
The future possibilities, Uzcategui continued, are wide open. “We see ourselves having a huge opportunity to disrupt different industries. We are starting with dentistry, and we see ourselves going into tissue engineering and other life science applications, but we are open to other applications that maybe we haven’t even thought of or scratched the surface on.”
References
Heimgartner, Jeffrey, “Volumetric 3D Printing Is Becoming a Reality,” engineering.com. February 9, 2022. www.engineering.com/story/volumetric-3d-printing-is-becoming-a-reality