By Noah Menard, Veritas Testing and Consulting; Kevin Menard, Mary Kay Corporation; and Benjamin Menard, Hitachi High-Tech Science
One of the challenges with photocuring systems is understanding the development of the degree of cure and the associated physical properties. Not only do the normally measured properties (glass transitions [Tg], moduli, hardness and strength) vary with the degree of cure, but important, if less obvious, properties (solvent resistance, wear, oxygen permeability, etc.) also follow a similar pattern.1 When one plots the degree of cure against a physical property, the resulting curve shows an inflection point where the material acts more like a solid than the starting liquid. This curve, often called the dog-leg curve, is shown in Figure 1 as an idealized example. The development of the critical properties do not all have their critical value at the same degree of cure. Because of this, and because the various analytical methods do not always agree, a comparison of the ways to measure degree of cure is important.
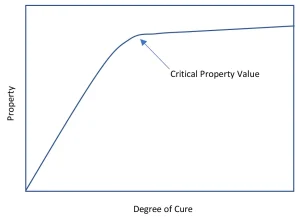
The problems of chemo-rheology agreement and of method-related differences
One of the continuing problems with understanding the curing process is that the chemistry – the change in the components – does not always track linearly with the development of physical properties. When working in thermally cured resin systems, this was true, but the development of high-molecular-weight species (which have implications for viscosity and other rheological properties) is dependent of the mechanism of curing. Because of this, it is possible that different methods give different answers. A classic case in thermally cured systems is certain epoxy resins, where full mechanical properties develop at approximately 88% cure when measured by differential scanning calorimeter (DSC) or infrared spectroscopy (FTIR).
Probably the best example of this is work done by Stansbury2 where the cure of dental-type materials by UV is followed by both near infrared spectroscopy (NIR) and dynamic mechanical analysis (DMA). In many cases, the chemical cure, as measured by the NIR, and the development of the viscosity and modulus, as measured by the DMA, do not track perfectly but instead show differences, particularly in the midranges. Because of these differences, it is important to understand the material, its kinetics and what the testing method measures to obtain the degree of cure. In this article, common methods were reviewed to evaluate what information they give about the changes in the material and relate it to curving.
The second problem is a basic one in analytical chemistry: What does the data mean? Different methods measure different properties of a material and even several thermal methods – all looking at the change of a property as a function of temperature. Yet using the standard methods for calculating the Tg temperature will give different numbers for DSC, TMA, DMA and rheology for the same material. Some of this is instrumental, but some also is due to the Tg being a range of behavior – and different methods measure different parts of the range. A full discussion is outside the scope of this paper, but a lack of perfect agreement actually is to be expected.
Methods: pro and con
Several samples of UV-curable material were tested on a variety of instrumentation. The following instruments were used with associated photocuring attachments: PerkinElmer Spectrum 2 FTIR with diamond ATR, PerkinElmer DSC6000 with Author 1’s photocuring attachment, Anton Paar MCR302 Rheometer, and Hitachi DMA7100. Sample handling varied and is discussed below.
- A commercial light source sold for the curing of nail polish was used. Intensities were calculated using a radiometer. A summary of experimental methods follows to explain how samples were handled.
- For the FTIR, uncured samples were deposited as a drop of uncured material on the ATR and then irradiated. Time-based software allowed tracking of the cure over the exposure time. The cured droplet then could be removed and checked by DSC. Cured samples were placed on the ATR and pressed into contact with the press arm of the ATR.
- DSC pans with quartz lids were used in the DSC8500 with Author 1’s designed curing lid. Approximately 10 mg of uncured material was added, and the instrument was held at a constant temperature while the light source was trigged on and off. Cured samples were crushed into particles and then loaded into an aluminum pan and sealed. They then were heated at 10 CPM under Nitrogen purge.
- The Hitachi DMA7100 is one of the very few DMA that has an optical path into the instrument’s furnace, making it possible to monitor or irradiate the sample. Uncured samples were painted on a strip of paper at ~1.4 mm in the extension geometry and cured by irradiation thru the viewing window while held at a constant temperature. The modulus curve from the paper support was subtracted while the tan delta was used as obtained.
- The MCR302 rheometer performed testing in shear mode using 8 mm parallel plate geometry with a replaceable quartz lower plate in the oscillatory mode. The light was applied to the sample resting on the quartz plate from below, using Anton Parr’s photocuring accessory. Only uncured samples were tested as cured samples were too stiff at room temperature to run.

Data is shown for each method. In DSC (the most common method), the flow of heat in and out of a sample is measured, allowing the authors to determine the Tg (as a shift in the baseline heat flow signal) and the enthalpy of curing (from the peak area). Two different approaches are used (Figure 2). In the first, uncured resin is irradiated in the DSC and the energy of the curve (as the peak area) is measured. As the amount of cure in the sample increases, this area decreases. In the second, a cured sample is heated and the glass transition temperature is measured. Often these are combined into one experiment.
DMA and rheology both look at the development of modulus and the increase in viscosity. As Menard (op cit.) discusses, the difference between the terms (DMA or rheometer) mostly is a marketing decision as both axial and torsional instruments use the same approach. A sinusoidal strain is applied to a sample and the resulting stress and phase lag are used to calculate modulus and viscosity.
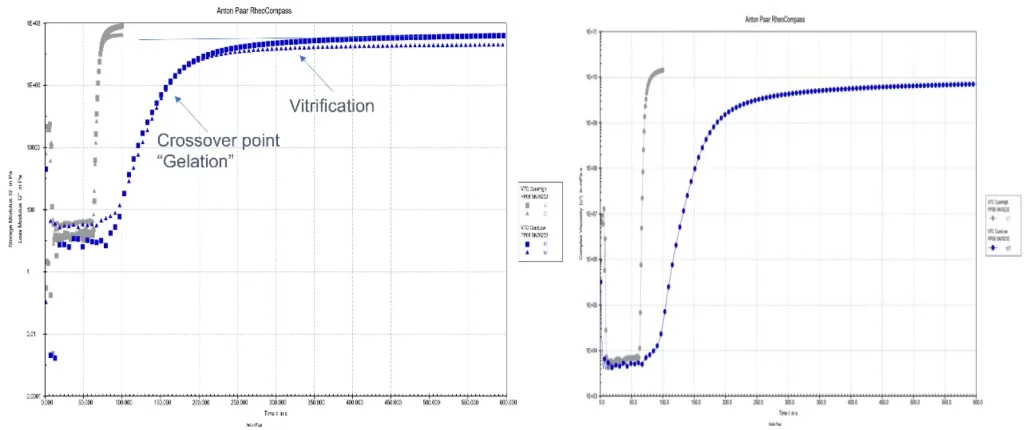
As shown in Figures 3 and 4, both instruments can use the same approaches as in DSC. Either irradiation of a sample or heating of a cured sample are done, and these sometimes are combined in the same experiment. The rheometer tends to be a better choice for uncured samples and the DMA for cured, but both work, and there are advantages to either approach. Some data on the size change on curing can be obtained, but that is best done with thermomechanical analysis (TMA), which is outside the scope of this paper.
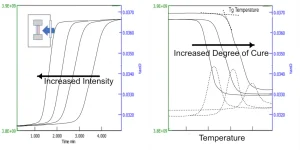
FTIR is but one type of spectroscopic method used for cure study, although it is common. Depending on the chemistry of the curing system, one may need to use FTIR, NIR or Raman. The latter two allow online monitoring (for NIR specifically used to track a sample in the DMA, see Stansbury, op. cit.) but require considerably more investment than FTIR and are more complicated to analyze. Here, the authors focus on FTIR. Figure 5 shows an example of photocuring a commercial nail polish on the ATR.
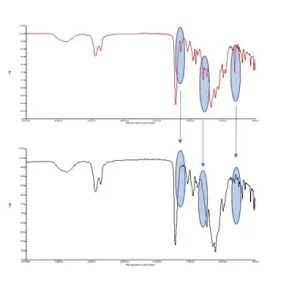
With FTIR, either the decreasing intensity of the starting material peaks or the increasing intensity of the product peaks is tracked. In an ideal system, two distinct peaks that were representative only of the uncured and cured material would be seen. As the cure progressed in said system, one peak would grow in strength and the other shrink, until only the cured peak remains. Unfortunately, many times this is not the case. Several peaks may be tracked, as shown in Figure 5, and a ratio may be used. The exact approach is system-dependent.
Conclusions
Out of the variety of different test methods, no single method of analysis is enough to fully characterize the material, much less determine the exact degree of cure. This is because a complex phenomenon is being examined, and it has many dimensions and often needs to address many concerns. These can include how stiff it gets, when it is self-supporting and at what temperature it will soften. For example, there are differences between the valve for a fully chemical cure from the DSC compared to what degree of cure gives full mechanical strength. Several methods often are needed to develop an understanding of the curing process. Once understood, a simpler method then can be used for monitoring production and quality control.
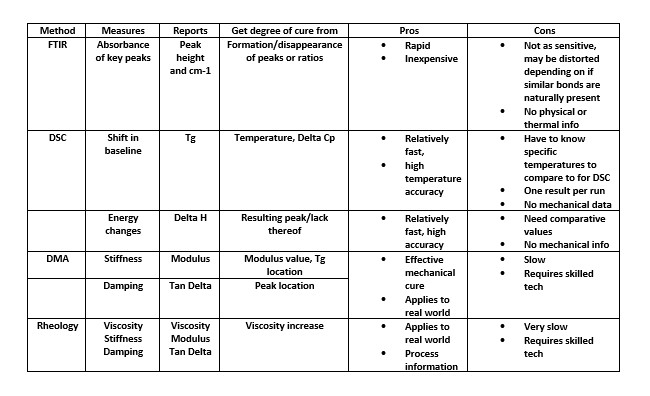
References
- Menard, K. and Menard, N. Dynamic Mechanical Analysis: 3rd Edition, Taylor and Francis, 2020.
- Stansbury, J et al. Measurement and management of stress development in Photopolymer Networks, Radtech Report, Spring 2011.
For more information, contact Noah Menard at noah@veritaslab.com.