By Jake Staples, technical manager, Wausau Coated Products, Inc.
Identifying the point at which a coating is cured is important to maintain consistent physical properties and performance, but it becomes even more critical when potential migration of uncured components is a consideration. Migration testing by extraction can be expensive, and the results are only reliable for coatings which have the same level of cure or greater. Easy and reproducible test methods for determining good cure are essential for quality control and peace of mind regarding migration of components for food packaging or Prop 65 concerns.
The first step in ensuring cured coatings is to practice good maintenance of UV-, LED- and EB-curing equipment. LED and EB units are low maintenance, but they are not “no maintenance.” It is important to follow manufacturer instructions on proper preventive maintenance. UV lamps are high maintenance and have multiple areas that could negatively impact curing efficiency. Old bulbs, dirty reflectors or quartz windows, a substrate web that is out of focus and/or poorly functioning power supplies all can contribute to reduced UV energy output, which in turn results in under-cured coatings, inks and/or adhesives.
Other considerations include the following:
- Cure exposure/dose is inversely proportional to coater or press line speed. Slower line speed increases cure exposure/dose for the UV/EB/LED unit power setting, and higher line speed decreases cure.
- Settings and maintenance of coating application equipment can affect the amount of ink or coating applied to the surface. Too much or too little coating can change the physical properties/performance of inks and coatings and could negatively affect the cure.
- Substrates with high porosity can absorb inks and coatings, which may decrease the cure for components within the material where light can’t reach. This primarily is an issue for UV and LED inks and coatings as EB energy has significantly higher penetration depth.
- For coatings and inks that require nitrogen-inerted systems, the amount of oxygen present at the surface of the coating or ink has a detrimental effect on curing. Best results are achieved by using a nitrogen air knife to strip oxygen off the boundary layer on the surface of the coating or ink, followed by a chamber with low ppm of oxygen where the UV/EB/LED curing occurs. The degree of cure can change within the range of <10 to 200 ppm oxygen.
For testing of good cure, there are three methods I like to use.
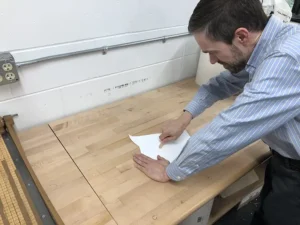
Mar test. With the mar test, a wooden craft stick is held at approximately a 45° angle and rubbed against the coating surface with moderate pressure and then any changes in the appearance of the coating surface are observed. A well-cured coating should not change appearance. Gloss coatings should not dull, and matte coatings shouldn’t burnish (become glossy). While not “analytical,” this test is quick, cheap, robust and reproducible. Small changes in the angle or pressure do not have a significant impact on the test results. This test works well for most coatings, but some may be too soft or burnish too easily for this method. The feasibility of this technique can be evaluated by testing at different cure exposures/doses (based on the UV/EB/LED power and line speed). If a minimum cure exposure/dose is found where the test results do not change, this method is validated.
MEK double-rub ball peen hammer test. The round head of a ball peen hammer is wrapped in cheesecloth and soaked with MEK solvent. The soaked cheesecloth is rubbed across the surface of the coating such that only the weight of the hammer head is putting pressure on the surface. Each back-and-forth movement is counted as one double-rub, and the result is the number of double-rubs before the coating surface breaks. The tester needs to evaluate the number of double rubs for a good cure of each coating initially since the results depend on the solvent and abrasion resistance of the cured chemistry. Once the baseline double-rub count is determined, the test provides a pass/fail result as under-curing the coating reduces the number of double-rubs before failure. This method is very reproducible as the amount of pressure applied by the tester is consistent.
FTIR cure analysis. Fourier-transform infrared spectroscopy (FTIR) is used to scan a coating, and a calculation can be used to determine the degree of cure based on the shift of key peaks in the spectrum. This is a truly analytical test, but it requires a calibration curve to be developed for each coating as significant changes in the chemistry alter the spectrum. The calibration curve is established by scanning the coating at different cure exposures/doses ranging from 0% (liquid and completely uncured) to 100% (extremely over-cured). A macro program can be developed from this data to easily measure and report the degree of cure. It then is important to identify the pass/fail point for “good cure” based on physical properties/performance and migration. From experience, that can be somewhere in the range of 75% to 95%.
Other tests exist, including the thumb twist and marker reticulation, but I prefer these three methods for accuracy, precision and ease of use.
Jake Staples is the technical manager at Wausau Coated Products, Inc. He can be reached at 715.348.2390 or jastaples@wausaucoated.com.