By Liz Stevens, writer, UV+EB Technology
Elixe SRL, Trento, Italy, has designed and now produces a turnkey, automated industrial equipment system, including patented technology and proprietary photopolymer materials, for preparing, coating and curing the interior of steel tubes, pipes and cylindrical products that are used for pressurized liquids and gases.
The Elixe production line preps, primes, coats, cures and performs quality control on pipes and cylinders from 1″ to 10″ in diameter and as long as 3 to 12 meters. The coating protects the metal products themselves from corrosion and scratches, facilitates flow through the products, protects the flowing material from contamination, and protects people and the environment from leaks from the tubes, pipes and vessels.
In the first stage of the production line, pipes or cylinders are prepped with shotblasting, during which the interior surfaces are treated with mechanical abrasion to remove oxidation, clean them and impart a rough texture. In the second stage, lances are inserted into the pipes or cylinders to deliver and cure two layers of coating. The product interiors receive a coat of proprietary primer, applied by the company’s patented airless microturbine and cured with its UV LED lamp, which was engineered for maximum curing effectiveness and efficiency. The next stage adds a proprietary topcoat to the interior surfaces, also applied via airless microturbine and cured with Elixe’s UV LED energy system. Quality is ensured through a multi-step process that includes irradiation intensity output control, visual inspection, electrostatic control and nIR spectroscopic imaging.
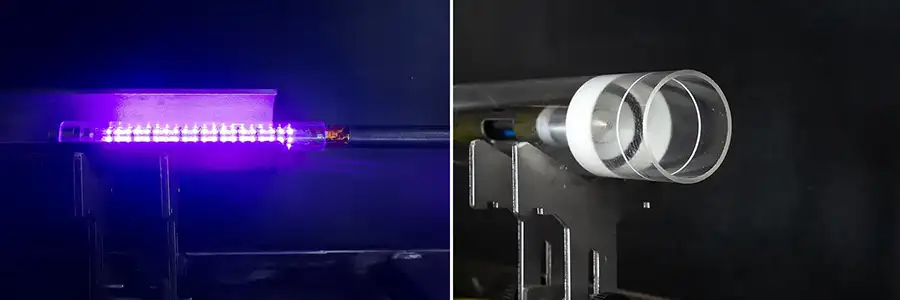
Elixe, in conjunction with University of Trento and Polytechnic University of Turin, researched and developed chemistries to be environmentally friendly photopolymer coatings which can be rapidly cured with Elixe’s UV-LED equipment, offering an alternative to conventional coating chemistry that contains VOCs and must be cured via a slow, heated-oven technique. Alessandro Condini, Elixe owner/CEO and a PhD researcher at University of Trento, described the company’s collaboration with Italian academic institutions: “We have a cooperation agreement with University of Trento (specialized in the study of metals) for the characterization of a new steel protective coating and with Polytechnic of Turin (specialized in the study of photopolymers) for scientific support to the development of a new UV protective coating.”
The main challenges in engineering the photopolymer coating chemistries, said Condini, “were obtaining a tack-free surface in the presence of oxygen with a single-wavelength, low-intensity lamp while ensuring the high-tier performance of steel protective coatings for oil and gas applications. These problems were overcome by combining photoinitiators and a primer topcoat system, allowing perfect adhesion and surface cure.” Elixe has developed several UV-curable coatings, some of which currently are patent-pending.
With UV LED, curing time for the coatings is 60 seconds with no post-processing required, yielding a dramatically reduced production cycle time. “The same protective coating with thermal curing takes two to three hours at 80 to 100° C,” said Condini, “which means at least 120 minutes, compared with one minute using UV curing.” UV LED curing technology also reconfigures the industrial footprint for this stage of the process. Instead of putting a pipe inside an oven to be cured, Elixe puts UV LEDs inside the pipe.
Elixe went to great lengths to design and engineer optimal UV source geometry for its UV LED lamp system. “Starting from the required UV intensity derived from laboratory tests, the required number of LEDs of nominal power per surface unit were selected,” Condini said. “Then, MATLAB [a programming and numeric computing platform] was used to evaluate the best disposition of LEDs to achieve a uniform light output at a selected distance from the source, both radially and along the main axis. Different simulations were performed using various geometries (hexagonal, octagonal, etc.), varying the LED relative distance within the array and the distance from the surface to be irradiated.” Elixe found that the hexagonal section was the optimal solution for obtaining uniform light intensity across the internal surface of 1″ to 4″ pipe. The values obtained via simulations then were confirmed by measuring real intensity output with a radiometer.
The UV LEDs are single 1 W LEDs arranged in arrays to form a patented lamp system delivering UV at 395 nm. Heat output from the lamp system, said Condini, is removed efficiently using a water-cooling system (Figure 1). “The internal structure of the cylinder housing the LED arrays,” he explained, “was studied in terms of computational fluid dynamics to maximize heat exchange. A control on water temperature is performed to avoid moisture condensation on electronics.”
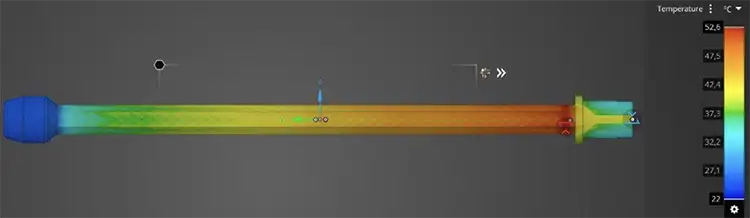
The system includes several quality control features. “In our system, the UV intensity needed to achieve a coating with optimal performance,” said Condini, “is ensured by monitoring the UV lamp intensity output with a radiometer before the lamp enters a pipe. This way, discontinuities due to the end of life of LED or damage can be quickly determined and corrected before curing each pipe.” Another quality control pass takes place after coating and curing, using a continuity test. “This test checks for electrical conductivity along the coated pipe,” he explained. “The pipe is connected to the ground while instruments with a probing electrode are passed along the surface; if the coating has porosities or damages, these expose the conductive metal below the probe, allowing it to create a circuit with the ground and generate an electrical signal.”
An additional quality inspection, nIR spectroscopy imaging, is used to detect any points or sections of the coated pipe that were not adequately cured. “We use nIR spectroscopy as a control system to evaluate the progression of the crosslinking reaction inside the coating,” said Condini. “This method allows us to read the chemical conversion that has taken place and compare it with setpoint values required for optimal mechanical properties. The reading is performed using miniaturized devices that fit inside the pipes and provide conversion values at different points along the pipe to isolate sections in which the cure has not properly occurred.” In the case of incomplete cure, another pass of the UV LED lamp system completes the curing process.
Elixe’s first production system is designed for use in a permanent, industrial-based plant location, and the company has plans for a mobile version that also will provide coating to protect steel from hydrogen embrittlement. “Right now, we have developed our equipment for an industrial, highly efficient, compact and sustainable process,” said Condini. “As a next step, in fall of 2023, we will start development of a CIPP [cured in place pipe] solution featuring flexible movement of the coating and curing equipment, and the ability to work in bended pipes. This project will include a hydrogen barrier coating made with photopolymers that can be applied to existing gas pipelines.”
Elixe’s innovations earned a Special Academic Award in the RadLaunch 2022 competition. For more information, visit www.elixe.com.