By Elaine Ruiz, Gabrielle Meehan, Yuhong He, William Schaeffer and Donald Herr, Sartomer Exton, USA
Free-radically cured acrylate coatings are known for their fast cure response and enhanced performance properties when compared to conventional thermoplastic coatings. This is, in part, due to the presence of cross-linking, which has been known to improve properties such as stain resistance, hardness and chemical resistance. Conversely, it also can lead to brittleness and high shrinkage, which can be issues in applications where toughness and flexibility are desired. Traditionally, these issues have been mitigated through the use of lower-functionality monomers and/or oligomers, resulting in cured matrices with clusters of differing cross-link densities.
Another way of potentially mitigating shrinkage and providing more homogeneity to a cured matrix is by adding functionality to the backbone of an acrylate oligomer. This would change the structure from purely telechelic to a more “structured” architecture, with pendant reactive groups in addition to the terminal ones (Figure 1).
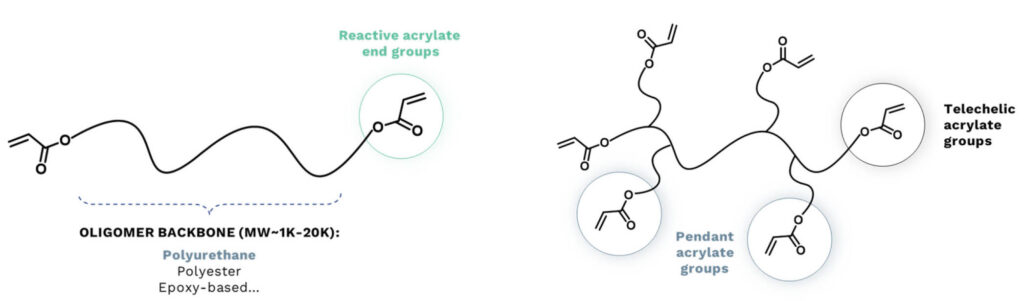
By increasing the functionality of the system via pendant groups vs. terminal groups, the overall cross-link density can be increased more uniformly. The higher molecular weight of the oligomer, and subsequently higher functionality, potentially could impact properties such as degree of cure, toughness and hardness, to name a few.
For the sake of this study, the effect of pendant functionality in urethane acrylates were evaluated in a coating application, specifically as a top coat for luxury vinyl tile. This application demands higher performance properties than traditional floor coatings, which makes these structured urethanes acrylates (SUAs) potential candidates to bridge the gap between hardness and flexibility, which is hard to achieve with telechelic oligomers.
Experimental Methods
In order to better understand the property space that urethane acrylate coatings occupy within the LVT market, a starting point formulation was developed based on an oligomer that has been used in a similar commercial application. The difunctional oligomer (UA) was diluted with a common monomer package, along with an amine synergist and photoinitiator, as shown in Table 1. A modified version of this formulation with a higher concentration of the difunctional monomer was developed to screen the SUAs in order to account for the monomer already present in UA.
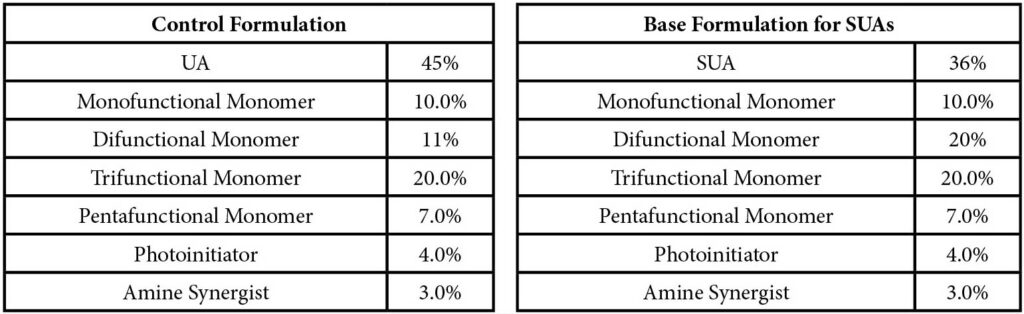
SUAs were provided by the synthesis team and differ in polyol chemistry/molecular weight and pendant group functionality. Pendant groups 2P and 3P were used as the reactive pendant groups, where 2P is difunctional and 3P is trifunctional.
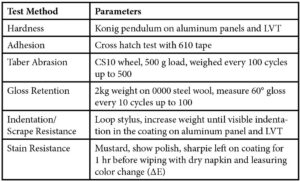
All formulations were coated at 2 mils and cured using two medium-pressure mercury arc lamps at 400 W/in and a belt speed of 42 fpm. PET film was used over the coatings to eliminate the effect of oxygen inhibition while curing. The cured coatings were conditioned for 24 hours before being evaluated in the application test protocol, shown in Table 2.
Results and Discussion
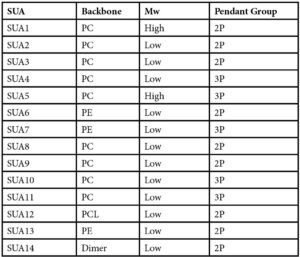
The first set of SUAs evaluated was based on polycarbonate diols with differing molecular weights, reacted with either 2P or 3P. Sample nomenclature is shown in Table 3.
Application test data (see Appendix I) showed that while the formulations with the SUAs were not as hard as the control formulation with UA, they had better taber abrasion and steel wool resistance (gloss retention). The SUAs with low PC diol Mw performed better than those with higher PC diol Mw, which could be due to higher cross-link density. In terms of pendant functionality, SUAs with 2P performed similarly to their higher-functionality counterparts with 3P. All formulations had 100% adhesion to LVT.
In order to rule out the effect of polyol chemistry differences between the control and the SUAs, a new set of SUAs was synthesized using a similar polyester polyol to the control (Appendix II). SUA6 and SUA7 are polyester analogs of SUA2 and SUA4, respectively. Both polyester SUAs performed similarly to the polycarbonate SUAs, with a few notable differences. The PE SUAs had worse taber abrasion resistance compared to their PC diol analogs, and SUA7 (PE polyol, 3P) had the best stain resistance. Additionally, a telechelic control oligomer (TCUA) also was synthesized as a direct control for SUA2; in this case, the SUA oligomer performed better than the control.
When comparing the SUAs across all test methods, the low molecular weight PC diol SUAs (SUA2, SUA3 and SUA4) stood out as the best for balancing both surface and bulk properties. The next step was to increase the concentrations of the reactive pendant groups, 2P and 3P, thereby increasing the overall functionality of the oligomer. SUA8 and SUA9 are higher-functionality SUA analogs of SUA2 (2P), while SUA10 and SUA11 are higher-functionality analogs of SUA4 (3P). All four SUAs outperformed their lower-functionality counterparts in most tests, most notably: steel wool resistance, stain resistance and scrape resistance (Appendix III). It is interesting to note that SUA10 and SUA11 performed similarly to SUA9, which implies that there is an optimum level of pendant functionality since the former two have a higher concentration of pendant groups.
Lastly, a final set of SUAs was synthesized based off SUA9 (best-performing SUA), with different polyol chemistries: SUA12 (polycaprolactone diol), SUA13 (polyester diol) and SUA14 (dimer diol). While these three SUAs performed similarly to SUA9 in terms of hardness, they did not have the same abrasion and stain resistance as their PC diol analog (Appendix IV).
Conclusions and Future Work
The performance data of SUA oligomers has shown that it is possible to increase functionality while maintaining a certain degree of flexibility, which can be useful in applications such as LVT coatings. However, it is to be noted that polyol chemistry and degree of pendant functionality are important factors in optimizing performance. As mentioned above, the best properties were achieved using a combination of high-pendant functionality and a shorter-chain PC diol. These attributes allowed for a higher degree of cross-linking, even as the molecular weight of the oligomer increased due to the addition of the pendant groups.
Although not shown in this study, FTIR (ATR mode) was used to verify that the conversion of SUAs was on par with the telechelic control (TCUA), as it was initially thought that the pendant groups could be sterically hindered from reacting and cross-linking into the network. In terms of future work, Sartomer has begun evaluating the weatherability of SUAs, along with generating neat physical properties for these new oligomers.
Sartomer is a global leader in UV/EB curing and advanced materials. For more information, visit www.sartomer.com.