By Lawrence (Larry) Van Iseghem is President/CEO of Van Technologies, Inc.
Over the course of doing business with industrial customers on an international basis, we have addressed an incredible number of questions and have provided many solutions associated with UV-curable coatings. What follows are some of the more frequent questions, and the accompanying answers may provide helpful insight.
1. What are UV-curable coatings?
In the wood finishing industry, there are three main types of UV-curable coatings.
-
- 100% active (sometimes referred to as 100% solids) UV-curable coatings are liquid chemical compositions that do not contain any solvent or water. Upon application, the coating is immediately exposed to UV energy without the need to dry or evaporate prior to cure. The applied coating composition reacts to form a solid surface layer via the reactive process described and appropriately termed photopolymerization. Since there is no evaporation needed before curing, the application and cure process are remarkably efficient and cost effective.
- Waterborne or solvent-borne hybrid UV-curable coatings obviously contain either water or solvent to reduce the active (or solid) content. This reduction in solid content permits greater ease in controlling the applied wet film thickness, and/or in controlling the viscosity of the coating. In use, these UV coatings are applied to wood surfaces through a variety of methods and need to be fully dried prior to UV cure.
- UV-curable powder coatings also are 100% solid compositions and typically are applied to conductive substrates through electrostatic attraction. Once applied, the substrate is heated to melt the powder, which flows out to form a surface film. The coated substrate then can be immediately exposed to UV energy to facilitate cure. The resulting surface film is no longer heat deformable or sensitive.
There are variants of these UV-curable coatings available that contain a secondary cure mechanism (heat activated, moisture reactive, etc) that can provide cure in surface regions that are not exposed to UV energy. These coatings commonly are referred to as dual-cure coatings.
Regardless of the type of UV-curable coating used, the final surface finish or layer provides exceptional quality, durability and resistance properties.
2. How well do UV-curable coatings adhere to different wood species, including oily wood types?
UV-curable coatings exhibit excellent adhesion to most wood species. It is important to make sure that sufficient cure conditions exist to provide through cure and corresponding adhesion to the substrate.
There are certain species that naturally are very oily and may require the application of an adhesion-promoting primer, or “tiecoat.” Van Technologies has performed considerable research and development into adhesion of UV-curable coatings to these wood species. Recent developments include a single UV-curable sealer which prevents oils, sap and pitch from interfering with UV-curable topcoat adhesion.
Alternatively, the oil present on the wood surface can be removed just prior to the coating application by wiping with acetone or another suitable solvent. A lint free, absorbent cloth is first wetted with the solvent and then wiped over the surface of the wood. The surface is allowed to dry and then the UV-curable coating can be applied. The removal of surface oil and other contaminants promotes subsequent adhesion of the applied coating to the wood surface.
3. What type of stains are compatible with UV coatings?
Any of the stains described here can be effectively sealed and top-coated with 100% UV-curable, solvent-reduced UV-curable, waterborne-UV-curable, or UV-curable powder systems. Therefore, there are a number of viable combinations making most any stain in the market suitable for any UV-curable coating. There are, however, certain considerations that are notable to make sure compatibility exists for a quality wood surface finish.
Waterborne Stains and Waterborne-UV-Curable Stains: When applying either 100% UV-curable, solvent-reduced UV-curable or UV-curable powder sealers/topcoats over waterborne stains, it is essential that the stain be fully dry to prevent defects in coating uniformity, including orange peel, fisheyes, cratering, pooling and puddling. Such defects occur due to the low surface tension of the applied coatings relative to the high residual water surface tension from the applied stain.
The application of a waterborne-UV-curable coating, however, generally is more forgiving. The applied stain may exhibit dampness without adverse effects when using certain waterborne-UV-curable sealers/topcoats. Residual moisture or water from the stain application will readily diffuse through the applied waterborne-UV sealer/topcoat during the drying process. It is strongly advised, however, to test any stain and sealer/topcoat combination on a representative test specimen before committing to the actual surface to be finished.
Oil-Based and Solvent-Borne Stains: Although there may exist a system that can be applied to insufficiently dried oil-based or solvent-borne stains, it usually is necessary, and highly recommended, to fully dry these stains before application of any sealer/topcoat. Slow drying stains of these types may require up to 24 to 48 hours (or longer) to achieve full dryness. Again, testing the system on a representative wood surface is advised.
100% UV-Curable Stains: In general, 100% UV-curable coatings exhibit high chemical and water resistance when fully cured. This resistance makes it difficult for subsequently applied coatings to adhere well unless the underlying UV-cured surface is adequately abraded to permit mechanical bonding. Although 100% UV-curable stains that have been designed to be receptive to subsequently applied coatings are offered, most 100% UV-curable stains need to be abraded or partially cured (termed “B” stage or bump curing) to promote intercoat adhesion. “B” staging results in residual reactive sites in the stain layer that will co-react with the applied UV-curable coating as it is subjected to full cure conditions. “B” staging also allows for mild abrading to denib or cut any grain raise that may occur from stain application. Smooth seal or topcoat application will result with excellent intercoat adhesion.
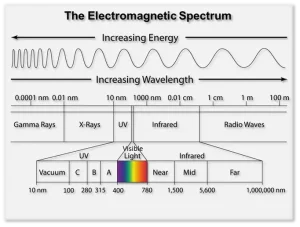
Another concern with 100% UV-curable stains pertains to darker colors. Heavily pigmented stains (and pigmented coatings in general) perform better when using UV lamps that deliver energy closer to the visible light spectrum. Conventional UV lamps doped with gallium in combination with standard mercury lamps are an excellent choice. UV LED lamps that emit 395 nm and/or 405 nm perform better with pigmented systems relative to 365 nm and 385 nm arrays. Furthermore, UV lamp systems that deliver greater UV power (mW/cm2) and energy density (mJ/cm2) promote better cure through the applied stain or pigmented coating layer.
Lastly, as with the other stain systems mentioned above, testing is advised before working with the actual surface to be stained and finished. Be sure before cure!
4. What is the maximum/minimum film build for 100% UV coatings?
UV-curable powder coatings technically are 100% UV-curable coatings, and their applied thickness is limited by the electrostatic forces of attraction that bind the powder to the surface being finished. It is best to seek the advice of the UV powder coatings manufacturer.
Regarding liquid 100% UV-curable coatings, the applied wet film thickness will result in approximately the same dry film thickness after UV cure. Some shrinkage is inevitable but usually it is of minimal consequence. There are, however, highly technical applications that specify very tight or narrow film thickness tolerances. In these circumstances, direct cured film measurement can be performed to correlate wet to dry film thickness.
The final cured thickness that can be achieved will depend on the chemistry of the UV-curable coating and how it is formulated. There are systems available that are engineered to provide very thin film deposits between 0.2 mil – 0.5 mil (5µ – 15µ) and others that can provide thickness in excess of 0.5 inches (12 mm). Typically, UV-cured coatings that have a high cross-link density, such as some urethane acrylate formulations, are not capable of high film thickness in a single applied layer. The degree of shrinkage upon cure will cause severe cracking of the thickly applied coating. A high build or finish thickness still can be achieved using UV-curable coatings of high cross-link density by applying multiple thin layers and either sanding and/or “B” staging between each layer to promote intercoat adhesion.
The reactive curing mechanism of most UV-curable coatings is termed “free radical initiated.” This reactive curing mechanism is susceptible to oxygen in the air which slows or inhibits the speed of cure. This slowing often is referred to as oxygen inhibition and is most important when trying to achieve very thin film thicknesses. In thin films, the surface area to the total volume of applied coating is relatively high when compared to thick film thicknesses. Therefore, thin film thicknesses are much more susceptible to oxygen inhibition and cure very slowly. Often, the surface of the finish remains insufficiently cured and exhibits an oily/greasy feel. To counteract oxygen inhibition, inert gases such as nitrogen and carbon dioxide can be passed over the surface during cure to remove the concentration of oxygen, thus permitting full, rapid cure.
5. How clear is a clear UV coating?
100% UV-curable coatings can exhibit excellent clarity and will rival the best clear coats in the industry. Additionally, when applied to wood, they bring out maximum beauty and depth of image. Of particular interest are various aliphatic urethane acrylate systems that are remarkably clear and colorless when applied to a wide variety of surfaces, including wood. Furthermore, aliphatic polyurethane acrylate coatings are very stable and resist discoloration with age. It is important to point out that low-gloss coatings scatter light much more than gloss coatings and will thereby have lower clarity. Relative to other coating chemistries, however, 100% UV-curable coatings are equal if not superior.
Waterborne-UV-curable coatings available at this time can be formulated to provide exceptional clarity, wood warmth and response to rival the best conventional finish systems. Clarity, gloss, wood response and other functional properties of UV-curable coatings available in the market today are excellent when sourced from quality manufacturers.
6. Are there colored or pigmented UV-curable coatings?
Yes, colored or pigmented coatings are readily available in all types of UV-curable coatings but there are factors to consider for optimum results. The first and most important factor is the fact that certain colors interfere with the ability of UV energy to transmit into, or penetrate, the applied UV-curable coating. The electromagnetic spectrum is illustrated in Image 1, and it can be seen that the visible light spectrum is immediately adjacent to the UV spectrum. The spectrum is a continuum without clear lines (wavelengths) of demarcation. Therefore, one region gradually blends into an adjacent region. Considering the visible light region, there are some scientific claims that it spans from 400 nm to 780 nm, whereas other claims state that it spans from 350 nm to 800 nm. For this discussion, it only matters that we recognize that certain colors can effectively block the transmission of certain wavelengths of UV or radiation.
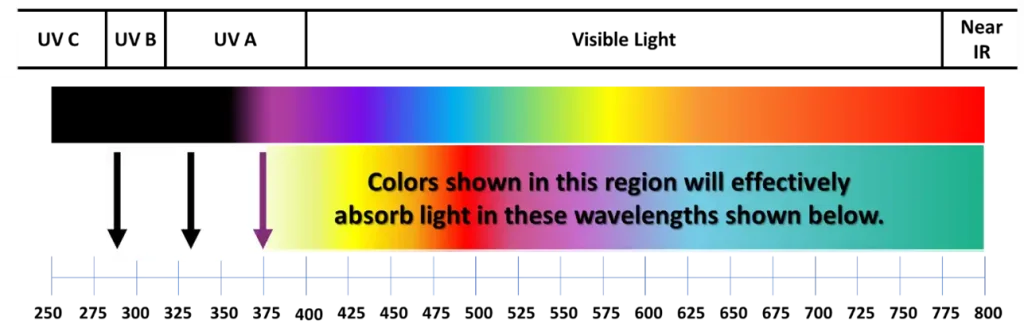
Since the focus is on the UV wavelength or radiation region, let’s explore that region in greater detail. Image 2 shows the relationship between the wavelength of visible light and the corresponding color that is effective in blocking it. It also is important to know that colorants typically span a range of wavelengths such that a red colorant may span a considerable range such that it may partially absorb into the UVA region. Therefore, the colors of greatest concern will span the yellow – orange – red range and these colors can interfere with effective cure.
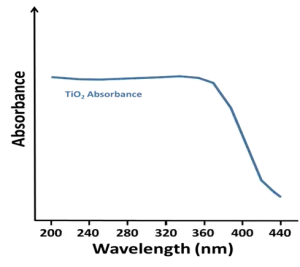
Not only do colorants interfere with UV curing, they also are a consideration when using white pigmented coatings, such as UV-curable primers and topcoat paints. Consider the absorbance spectrum of the white pigment titanium dioxide (TiO2), as shown in Image 3. TiO2 exhibits very strong absorbance throughout the UV region and yet, white, UV-curable coatings are effectively cured. How? The answer resides in careful formulation by the coating developer and manufacturer in concert with the use of the proper UV lamps for cure. The common, conventional UV lamps in use emit energy as illustrated in Image 4.
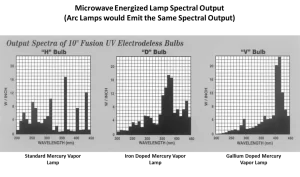
Each lamp illustrated is based on mercury, but by doping the mercury with another metallic element, the emission can shift to other wavelength regions. In the case of TiO2-based, white, UV-curable coatings, the energy delivered by a standard mercury lamp will be effectively blocked. Some of the higher wavelengths delivered can provide cure but the length of time required for full cure may not be practical. By doping a mercury lamp with gallium, however, there is an abundance of energy that is useful in a region not effectively blocked by TiO2. Using a combination of both lamp types, both through cure (using gallium doped) and surface cure (using standard mercury) can be accomplished (Image 5).
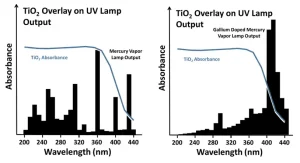
Lastly, colored or pigmented UV-curable coatings need to be formulated using the optimum photoinitiators so that the UV energy – visible light wavelength range being delivered by the lamps – is properly utilized for effective cure.
Other Questions?
In regard to any questions that arise, never hesitate to ask the company’s current or future supplier of coatings, equipment and process control systems. Good answers are available to help make effective, safe and profitable decisions. u
Lawrence (Larry) Van Iseghem is president/CEO of Van Technologies, Inc. Van Technologies has over 30 years of experience in UV-curable coatings, beginning as an R&D company but transformed rapidly into a manufacturer of Application Specific Advanced Coatings™ serving industrial coating facilities worldwide. UV-curable coatings have always been a primary focus, along with other “Green” coating technologies, with the emphasis on performance equal to or surpassing conventional technologies. Van Technologies manufactures the GreenLight Coatings™ brand of industrial coatings according to an ISO-9001:2015 certified quality management system. For more information, visit www.greenlightcoatings.com.