By Vanessa Maurin, David Engberg, Stefan Lundmark, Pia Wennerberg and Martin Olofsson, Perstorp AB, and Guillaume Bano, Céline Croutxé-Barghorn and Xavier Allonas, Laboratory of Macromolecular Photochemistry and Engineering
Cationic UV curing brings clear benefits, such as low shrinkage and excellent adhesion, to difficult substrates like as plastic, metal and glass. Cationic UV formulations are not sensitive to oxygen and benefit from the dark-cure living polymerization, offering full-cure possibilities. Despite these benefits, the use of cationic curing still is very limited today, mainly due to the cost and limitation of available raw materials. In this article, the advantages of using oxetanes, such as TMPO and Di-TMPO, in cationic-coating formulations are discussed. Experiments have been conducted to evaluate different formulations using both traditional mercury as well as LED lights. The use of TMPO and Di-TMPO to aid dispersion of additives and their use in 3D-printing formulations also are discussed. Finally, the necessity to consider sustainability for cationic raw materials will be reviewed.
Introduction to Cationic UV Curing
Cationic photo-induced polymerization was developed in the late 1970s by Dr James V. Crivello, working at the General Electric Corporate Research and Development Center in New York. He was tasked with finding an alternative to the traditional thermally cured, solvent-based, electrically insulating enamel that had been used in the production of transformer-generator cores. The primary goal of the project was to eliminate solvents. Free radical UV coatings already were under development at this time, but when it was concluded that a curing unit with 20 mercury arc lamps and nitrogen purging system would be required, it was deemed too expensive and alternatives were needed. This led to the development of onium salt photoinitiators for cationic polymerization and the first successful application with photocurable epoxy generator core plate enamel. 1 As the oxonium ion and carbocation are inactive to oxygen, there was no need for any nitrogen-purging step.
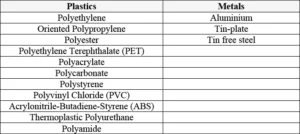
Not being inhibited by oxygen is, however, not the only advantage of utilizing the photocurable cationic reaction. Other major advantages are the low shrinkage and excellent adhesion to various materials, thanks to the inherent stress-relief ring-opening effect of the photopolymerization reaction. This enables cationic UV-curable inks and coatings to have superior adhesion on especially difficult substrates, such as metal, glass and plastics, when compared to traditional free radical systems suffering from potential shrinkage and limited adhesion after curing. In Table 1, examples of difficult substrates are shown where cationic inks and coatings have been proven to have very good adhesion.
Other advantages of the cationic reaction are that the reaction is only initiated by the exposure to UV light, and that the “living polymerization” (often referred to as “dark cure”) continues even after the exposure illumination. This enables the reaction to reach full cure in thick and/or shaded parts and contributes to the high adhesion and also minimizes problems (e.g. migration) in sensitive applications. Although cationic UV curing has a long history and evident advantages, the market today is very limited due to availability and the high price of the key raw materials.
Oxetanes to Boost Cationic UV Curing
Most often, cationic UV curable formulations are based on one main ingredient, which is a cycloaliphatic epoxy resin: 3,4-epoxycyclohexylmethyl-3’,4’-epoxycyclohexane carboxylate (ECC). While some studies indicate a fast curing for ECC when cured under Hg UV bulb, the finished films often are very brittle due to a high Tg.2 Conversion of ECC alone in standard conditions are usually in the range of 40-60%. 3, 4 Therefore both brittleness and a low conversion degree often make ECC unsuitable to be used alone for industrial applications. In order to find the right balance between high curing speed, high conversion level and limited brittleness, it is required to blend ECC with other ingredients.
To achieve this, different components can be considered such as: 1) Other epoxy resins with a longer chain backbone, such as bis (3,4-epoxycyclohexyl) adipate, which will show high curing speed and increased flexibility 2 ; 2) Other epoxy resins with a simpler structure, such as a monofunctional epoxy, as the cyclohexene oxide, which could cure very fast and reach high conversion level 5 ; 3) Polyols, which will react through chain transfer and therefore influence the reaction speed as well as bringing flexibility to the cross-linked system. These polyols could possibly have a polyester core. Dendrimers or hyperbranched polyols also are of interest and would be fully part of the formed polymer networks as reacting through the chain transfer mechanism in a similar way as the polyols 2, 6, 7 ; 4) Vinyl ethers and 5) Oxetanes, both well known as efficient reactive diluents and therefore allowing to adjust the viscosity of the formulations while participating to the photopolymerization process. Some studies also report the benefits of blending epoxy with oxetanes and that such systems do copolymerize well 5, 6, 8, 9 ; 6) Another possibility is to blend cationic systems with free radical systems to form so-called interpenetrating networks (IPN), sometimes also referred as hybrid formulations. 4
Oxetanes Benefits
Similar to epoxy, oxetanes react through a ring opening mechanism. Oxetane rings possess a slightly lower ring strain energy than epoxy/oxirane rings, while they show higher basicity of the heterocyclic oxygen, therefore making them have comparable reactivities. The photopolymerization mechanism of oxetanes as well as their benefits have been well investigated in various studies. For example, the monofunctional oxetane TMPO and the difunctional oxetane Di-TMPO are two efficient reactive diluents that can allow significant reduction of the viscosity of epoxy-based formulations while ensuring high reactivity in the cationic photopolymerization process. 5, 6, 9 These effects will be further discussed in this article. Lowering the viscosity of the formulations can increase mobility of the reactive species during the photopolymerization process and higher conversion degrees could be achieved when blending epoxy and oxetanes together. Lower viscosity also can be beneficial when applying coating or ink formulations on the desired substrates, this often resulting in a good visual appearance of the cured films. In 3D printing, viscosity also is a key parameter; high viscosity often is undesirable as objects would lack details.
Experimental Part I: Effect of TMPO and Di-TMPO on the Reactivity of Cationic Systems using Traditional Hg Light
Materials
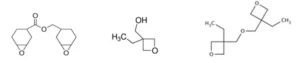
The following monomers/oligomers were used: 3,4-epoxycyclohexylmethyl-3’,4’-epoxycyclohexane carboxylate resin (ECC, UviCure S105) from Lambson; 3-ethyl-3-oxetanemethanol (TMPO, CuraliteTM Ox) from Perstorp AB; 3-ethyl-3-oxetanemethanol (Di-TMPO, CuraliteTM OxPlus) from Perstorp AB. As can be seen in Figure 1, ECC is a difunctional epoxy resin. TMPO is a monofunctional oxetane but also possesses a hydroxyl group, while Di-TMPO is a difunctional oxetane resin. UVI 6992 is a mixture of triarylsulfonium hexafluoroantimonate salts in propylene carbonate from Dow and was used as cationic photoinitiator. BYK 307 is a silicone-based surface additive from BYK and was added in very small amount to the formulations in order to reduce surface tension and ensure good surface film formation.
Formulations and Testing
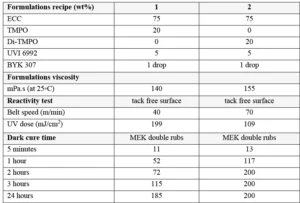
The ingredients were blended according to the recipes presented in Table 2, and films have been applied on Al Q-panels using a 6 μm K-bar. Since cationic photopolymerization is sensitive to moisture, the experiments were performed on the same day to avoid variation due to different environment conditions.
The reactivity test was performed under a UV conveyor (Efsen Engineering) using a Fusion lamp (Fusion F600, Hg-bulb, max power of 240 W/cm) for which its intensity was set to 55%. The surface cure was checked by gently drawing a cotton stick over the film surface after its irradiation and is reported the highest belt speed for which there was no mark on the surface (when the surface film is tack free). A high belt speed corresponds then to a low UV dose.
A second test was run in order to follow the living polymerization in the dark. For this test, the 6 μm films were first cured with 2 passes at 5 m/min under the UV conveyor and the lamp intensity set to 55% (2 J/cm2). Then the film surface was rubbed with a cotton stick previously soaked into methyl ethyl ketone (MEK) . The cotton sticks were replaced every 50 double rubs. The double rubs were performed manually, and an approximate weight of 0,5 kg was applied when rubbing the coatings. When some defects were visible, the number of double rubs is reported. A high cross-linked coating manages 200 MEK double rubs without any damage.
Results
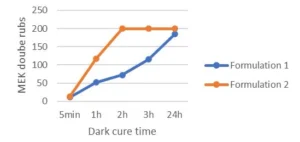
Looking at Table 2, it can be concluded that the use of the difunctional oxetane allows to get a tack free surface working with a faster conveyor speed/lower UV dose, this suggests that Di-TMPO has a higher propagation rate than TMPO, thanks to a higher oxetane functionality. As illustrated by Figure 2, it also is possible to reach a high chemical resistance of 200 MEK double rubs after only two hours of dark curing. The system based on Di-TMPO, therefore, seems more reactive, and the cross-linking network is built in a shorter time.
The monofunctional oxetane TMPO requires an increased UV dose to complete surface curing, meaning that the polymerization rate is somehow slower than for Di-TMPO. This is confirmed by the dark cure results where it can be see, that 200 MEK double rubs only are reached after 24 hours of dark cure. The system still presents some mobility after illumination is stopped, allowing the reactive species to continue to react until full cross-linking is completed and then ensuring high chemical resistance to the system. In theory, the presence of the hydroxyl group on TMPO should promote a chain transfer mechanism that should contribute to fasten the overall reaction speed, but this is not observed in the present experiments. The authors still assume that the hydroxyl group is reacting to some extent and bringing some flexibility to the system. This possibly could be verified by FTIR/DMA experiments.
Experimental Part II: Effect of TMPO and Di-TMPO on the Final Coatings Properties using Traditional Hg Light
Formulations and Testing
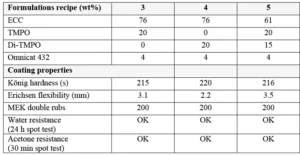
Formulations were prepared using similar monomers/oligomers as in the previous sections. But another sulfonium salt was used as cationic photoinitiator in this study: Omnicat 432, which is a mixture of triarylsulfonium hexafluorophosphate salts in propylene carbonate from IGM Resins. While TMPO and Di-TMPO have both in common to act as efficient reactive diluents in cationic epoxy formulations, they also each have distinct properties. For this study, formulations have been prepared by blending ECC with TMPO and/or Di-TMPO as presented in Table 3. For the last formulation, it was of interest to use oxetanes to compensate a larger reduction of the ECC amount; there a blend of 20 wt% TMPO with 15 wt% Di-TMPO was used.
For the evaluation of hardness and flexibility, formulations were applied on glass and Al respectively, using a 40 μm K-bar – while for testing the MEK resistance, films were applied on Al Q-panel using a 12 μm K-bar. All coatings were cured with two passes at 5 m/min under the UV conveyor with the lamp intensity set to 55% (2 J/cm2). The curing of these formulations was performed the same day to avoid variation due to different environment conditions. Cured coatings were stored in a constant room (50% relative humidity and 23° C) for three days prior to the evaluation of hardness and flexibility and up to eight days for the water and acetone resistance tests.
Results
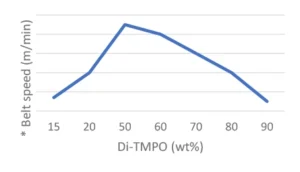
Final coatings properties are presented in Table 3. All formulations show good reactivity and cured coatings properties, but TMPO is especially of interest if a flexible coating is desired. Since Di-TMPO allows faster curing speed, a combination of TMPO and Di-TMPO seems to be of the best interest if a combination of fast curing speed, high hardness but also some flexibility is targeted. The amount of ECC is significantly reduced in Formulation 5 using a mixture of TMPO and Di-TMPO. The effect of using a higher amount of Di-TMPO has been studied. As illustrated by Figure 3, the conclusion is that there is an optimum around 50 wt% of Di-TMPO to achieve best benefits.
Moisture Sensitivity
It is well known that cationic photopolymerization is sensitive to environmental humidity as this could possibly lead to some inhibition of the reaction. Therefore, moisture should be well controlled in the working environment to minimize the risk of inhibition but also to ensure no variation in the curing results. While this could be relatively well controlled in small scale or experiments run the same day to avoid variation from environmental humidity, it can be a challenge on an industrial scale.
From the literature, it can be noted that a small amount of water could be beneficial acting as a proton carrier and chain transfer agent in the cationic photoinitiation and propagation processes, while an excess of water will capture and terminate the propagating cationic species.
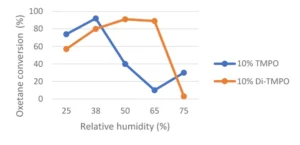
To counterbalance the negative effect of a too-high humidity during cationic photopolymerization, the use of components acting as humidity blockers has been described in the literature. Different approaches have been described, such as: 1) The use of hydrophobic materials, which are less negatively affected by humidity variation; 2) An optimal amount of hydroxy-functional components to enhance conversion through chain transfer mechanism. In such scenarios, the use of TMPO could be beneficial. However, in high-humidity environments, conversion will tend to decrease; 3) It has been shown that the conversion of the difunctional oxetane Di-TMPO could reach a maximum at much higher humidity level than TMPO as illustrated by Figure 4, which is based on a study by Chen & Co. 3 This could be explained by the fact that Di-TMPO is less hydrophilic than TMPO, and that a higher humidity level, in that case, could be allowed to reach an optimum hydroxyl concentration for an efficient cationic photopolymerization.
Experimental Part III: Cationic Photopolymerization of ECC/Oxetanes under LED 395 nm
Formulations and Testing
The reactivity of ECC/oxetanes blends was studied under LED 395 nm. Formulations were prepared using similar monomers/oligomers, as in the previous sections. A different photoinitiator system was selected in order to ensure good absorption at this wavelength. Omnicat 440, which is a bis(4-methylphenyl)iodonium hexafluorophosphate, was used as photoacid generator. However, as it does not absorb at 395 nm, 2-isopropylthioxanthone (ITX) was used as photosensitizer. Direct interaction of iodonium salts with the triplet state of ITX produces H+, and that can initiate the cationic polymerization. In addition, benzyl alcohol was used in order to generate an aryl radical, which is oxidized by the iodonium salt to generate reactive cation species. 4
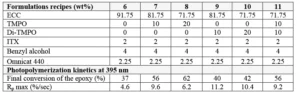
The reactivity study of the formulations was investigated by Real-Time Fourier Transform Infrared spectroscopy (RT FTIR) using a Vertex 70 from Bruker, coupled with a LED 395 nm (Ufiber) from Uwave, and an intensity of 29 mW/cm2 or 78 mW/cm2. The formulations were deposited on a KBr pellet using a calibrated bar coater (40 μm). Conversions were calculated by following the epoxide band at 910 cm-1. It is to be noted that oxetanes don’t absorb at this wavenumber. The epoxide conversion vs. time was calculated according to Formula 1 where A0 is the initial absorption band area before exposure (at time t0) and At is the absorption band area after various times of light irradiation (at time t). The maximum rate of polymerization (Rp max) was calculated from the maximum of the first derivative of the conversion vs time curves. Experiments were carried out in similar environmental conditions with a humidity of 35-40%. All experiments were repeated three times to ensure good repeatability, and the values presented in Table 4 are the average values.
Results
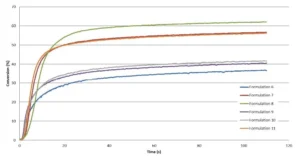
A preliminary study of a formulation containing only ECC and no oxetanes was carried out on the Vertex 70 in order to investigate the effect of different intensities on the epoxy conversion. From 29 mW/cm2 to 78 mW/cm2, no significant difference was observed, and the conversion was about 40%. A curing trial under a conveyor equipped with a LED 395 nm (Firejet) from Phoseon was conducted as well, in which significantly higher intensity was delivered up to 160 mW/cm2. However, this did not contribute to increase the epoxy conversion. Most likely, the Tg of the cycloaliphatic epoxy resin limits the chains mobility and, by consequence, the final conversion. Table 4 presents the recipes of the different formulations, which have been studied by RT-FTIR under LED 395 nm with an intensity of 29 mW/cm2. The kinetics are presented in Figure 5 and a zoom in the very first seconds is shown in Figure 6.
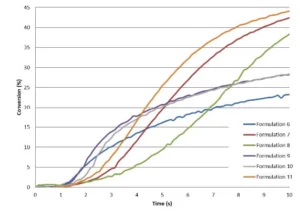
From these results, it can be concluded that TMPO allows significant increase of both the polymerization rate and final conversion of the epoxy. TMPO possessing a hydroxyl group, there is a possibility for TMPO to also react through chain transfer mechanism, this allowing it to reach higher Rp. However, in presence of TMPO, a slight delay in the starting reaction is observed during the very first seconds of irradiation.
To reduce the induction period, it is possible to further work on an optimal ratio between oxirane/oxetane, as described previously in literature. However, the induction period still would exist. Another approach is to work with other epoxide compounds, such as limonene dioxide, used in smaller amount as presented by Crivello in his “kick-starting” oxetane photopolymerization studies where it is possible to reduce significantly the induction period. Such systems are described to not be sensitive to variation in ratio oxirane/oxetane but instead sensitive to variations in photoinitiator concentration and light intensity. 9
As illustrated by Table 4 and Figure 5, Di-TMPO contributes to an important increase in the polymerization rate but a limited improvement of the final conversion of the epoxy. Due to higher oxetane functionality, the reaction starts faster but it seems that the system rapidly reaches a gel state where the reactive species have limited mobility to further react. Based on these results, it indicates that a blend of TMPO and Di-TMPO with optimized ratio could offer several possibilities to various applications, such as coatings, inks, adhesives and 3D printing.
Solving Problems in Challenging Applications
General
Despite its advantages, cationic UV curing seldom is used in comparison to free-radical UV curing and still only addresses few application areas. It is well understood that there is a clear need to develop new materials for cationic photopolymerization – new monomers, oligomers and also photoinitiators – in order to offer a broader components toolbox to the formulators. Therefore, industrials should continue to work hand in hand with academics to further develop and broaden the possibilities for cationic UV photopolymerization.
However, there are examples of challenging applications where cationic UV curing already has demonstrated its potential, such as in the field of graphic arts, thanks to very good adhesion on difficult substrates like polyolefins (PE, PP, OPP)6, but also in the area of 3D printing/stereolithography (SLA) where IPN systems often are offering several advantages, such as complete curing and dimensional stability of the printed objects. Another example where cationic UV systems bring potential is in the adhesives field (e.g. to produce smart card/tag modules). 2 It is the authors’ knowledge that cationic UV can offer excellent adhesion to metals such as Aluminium, Tin-plate and Tin free steel. Making it suitable for applications like coil-, can- and metal decorative coatings. It is the authors’ belief that cationic UV curing can have even further potential in these applications and in other areas as well.
IPN systems also have been studied for the preparation of low-gloss coatings. Most often, UV-curable coatings possess very high gloss, and therefore the use of matting agents is required to produce matte coatings, which could be of interest for example for interior finishing and wood flooring applications. However, high concentration of matting agent is required to get a low gloss, and this could lead to significant increase of the formulation’s viscosity. The use of reactive diluents, such as TMPO and Di-TMPO, could be very beneficial to help dispersing the matting agent, controlling the overall viscosity of the system, while still ensuring possible migration of the matting agent during the photopolymerization mechanism so it could reach the coating surface and create the desired topography. In the study from Calvez et al, another approach is described that eliminates the use of the matting agent, but instead works with a two-phase or multiphase polymer system where different components are thermodynamically incompatible. This self-matting approach allows to control the gloss based on the formation of a phase-separated morphology. Formulating with IPN, where two distinct multi-functional polymers are interlaced but are not covalently bonded, could be a solution to control the coating surface morphology and, as a consequence, the gloss level. 10
Sangermano et al published an overview of the use of cationic UV curing in the field of coatings, composites, adhesives and inks. Within the coatings industry, there is a strong demand for functionalization of the coatings and, in many cases, this could only be achieved by incorporation of specific organic or inorganic particles. This review highlights the different possibilities to further functionalize cationic UV-curable coatings with fillers and additives (as some examples: clays, carbon nanotube, siloxane functionalized materials, metallic nanoparticles, fluorinated components, polymer particles, TiO2). 8 When incorporating fillers and additives, viscosity and overall reactivity often could be affected, and the use of reactive diluents such as TMPO and Di-TMPO could, in most cases, help to counterbalance these effects.
3D Printing
As mentioned earlier, there are several benefits to working with IPN systems in the area of 3D printing, especially for stereolithography (SLA).
Though 3D printing always is followed by a post-curing stage, the cationic part of the IPN systems can allow for a complete curing of thick and complex shapes with fine details, thanks to the dark-cure phenomenon of the cationic photopolymerization. Contrary to pure free radical systems, there is no or less issue of shrinkage, therefore reducing stress and defects in the printed models. As a result of low shrinkage and dark-cure phenomenon, the final prints often have high resolution and high dimensional stability. 11
As for coatings and inks applications, the use of oxetanes as reactive diluents allows monitoring of the overall viscosity of the 3D resin and contributes to the cross-linking network formation. The authors observed that both TMPO and Di-TMPO work well in 3D IPN resins, and the best results were obtained using a combination of both the mono- and di-functional oxetanes. Finished and post-cured 3D-printed parts exhibited good hardness and impact resistance, as well as high resolution. While impact resistance was increased, it was possible to maintain acceptable HDT values. The resistance towards water also was greatly improved in presence of Di-TMPO; this is in agreement with the findings from the study from Bagheri et al. 12
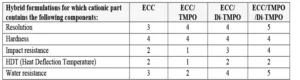
These effects are summarized in Table 5, where the properties are assessed using a scale from 0 to 5, where 0 is the lowest result and 5 is the highest result.
These days, 3D printing is more and more considered and accepted for production purposes and not only for prototyping. There is a strong interest in developing functionalized materials and, therefore, the incorporation of fillers and additives once again could be required. As an example, the authors have tested the incorporation of high molecular weight components into 3D IPN resins and were able to demonstrate that a specific ratio of TMPO/Di-TMPO was beneficial to ensure efficient blending and stability.
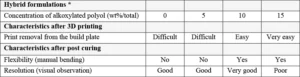
If some flexibility is desired in the printed parts, the addition of alkoxylated polyols reacting through chain transfer mechanism would help to modify the structure of the cross-linking network with the tendency to build more flexible chains. As can be seen in Table 6, the use of alkoxylated polyols is beneficial to ensure an easy removal of the printed objects from the printing platform (the green parts). This removal step needs to be performed carefully in order to not generate defects in the object. Especially if the printing procedure is performed without specific support structure. As for coatings and inks formulations, the ratio between oxirane/oxetane and hydroxyl functions must be well balanced to get the best performance results.
The table also shows that there is an optimum concentration of alkoxylated polyol to use to achieve good flexibility and resolution. If too much polyol is used, certain properties might be negatively affected, as shown in Table 6 where 15 wt% alkoxylated polyol led to a poor resolution. The polyol used for this study was a tetra-functional polyol which contains ethoxylated chains; it has an approximate viscosity of 300-600 mPa.s and a hydroxyl value of 270-310 mg KOH/g.
Sustainable Raw Materials for a Sustainable Technology
There is a strong drive throughout all industries and applications to strive towards more sustainable solutions, reducing the carbon footprint throughout the product’s lifecycle. Industry as well as consumers continuously become more aware of their own footprint and actively search for more sustainable alternatives. Cationic radiation curing already is in itself a sustainable technology compared to traditional solvent-borne technologies, but that does not mean that there is no possibility to further improve the sustainability of the technology by considering alternative raw materials.
Replacing traditional cycloaliphatic epoxy´s like ECC with epoxidized vegetable oils (EVOs) was evaluated and reported already in 1992 by Crivello and Narayan. In this work, soybean, safflower, sunflower, canola, crambe, lesquerella, rapeseed, meadowfoam and linseed oils were epoxidized. Since then, several more studies have been conducted on the subject focusing on the ones that seem viable from both performance and commercial aspect (epoxidized soybean, sunflower, corn and linseed oils). Also, systems combining EVOs with petroleum-based epoxy have been evaluated. However, in general, the systems based on EVOs show lower reactivity and struggle to meet the same mechanical properties as petroleum-based epoxy. More work and studies are required to further develop and optimize the systems based on EVOs. 13
Work to improve the sustainability of diluting monomers, such as oxetanes, has been done. Today, there are commercial bio-attributed oxetanes available derived from bio-based raw materials using a mass-balance concept. The mass-balance concept is a certification system that allows producers utilizing existing production units to gradually transition into renewable raw materials using a certification system, similar to what was adopted many years ago for electricity. An independent third party, such as ISCC, then is used to ensure the amount of bio-based raw material consumed each year corresponds to the amount of bio-attributed product produced. The mass-balance concept allows a producer to attribute the green molecule to a chosen product but with full chemical and physical traceability, allowing the green shift progress in an easier and sustainable way.

The most commonly used oxetane for cationic curing, TMPO, traditionally is derived from natural gas, propylene and methanol. However today, there are alternatives by using bio-methane, propylene from bio-nafta and bio-methanol instead. This results in a partially or even fully renewable TMPO with a considerably lower carbon footprint compared to the traditional petroleum-based one. The authors have calculated the potential savings that partly renewable TMPO/Di-TMPO could bring in comparison to purely fossil-based TMPO/Di-TMPO. Results are presented in Table 7. For this, a lifecycle assessment (LCA) analysis has been conducted, where the emissions from each step in the production chain are included, from the extractions of the raw materials, by processing, energy use and transports to the production of the final products. The user phase and the end-life phase are estimated as well. The functional unit in the study is 1 kg of TMPO or Di-TMPO.
It is of great interest to see that the use of, for example, a 50% renewable TMPO could contribute to save 1.1 CO2e/kg. In a formulation where TMPO is used up to 20 wt% of the total formulation, this would result in a saving of 0.22 CO2e/kg. Reducing CO2 emissions is one of the important approaches to meet sustainability targets, and basing the production on raw materials through, for instance, the mass-balance methodology is a promising way.
Conclusion
Performance requirements for radiation-curing systems constantly are sharpening, and the conventional free radical technology comes with limitations that could affect this performance (e.g. adhesion, flexibility and oxygen inhibition). These key properties potentially can be addressed by cationic UV curing. Most often, the cationic UV-curable formulations in the industry are based on ECC as the main ingredient. However, both brittleness and low-conversion degree often make ECC unsuitable to be used alone for industrial applications. Experiments presented in this article confirm that oxetanes such as TMPO and Di-TMPO can lower viscosity as well as increase reactivity in cationic formulations cured with the use of traditional mercury and LED lights. Di-TMPO is shown to be superior in terms of increased reactivity, but TMPO especially is of interest if some flexibility is desired. Hence, a combination of TMPO and Di-TMPO seems to be desired if a combination of fast curing speed, high hardness and some flexibility is targeted.
As sustainability is high on the agenda in all industries today, there is a demand for biobased raw materials within cationic UV curing. More development is required to improve the performance of oil-based epoxies. However, already today there is access to established raw materials, like oxetanes available in bio-attributed versions using the mass-balance concept.
References
- The Discovery and Development of Onium Salt Cationic Photoinitiators; J. V. Crivello; J. Polym. Sci. Part A: Polym. Chem.: Vol. 37 (1999)
- UV Cationic Systems for Smart Card/Tag Applications; H. Murray and E. Ledwidge; Conference proceeding from IEEE conference on Polymers & adhesives in microelectronics and photonics (2001)
- A “Humidity” Blocker Approach to Overcoming the Humidity Interference with Cationic Photopolymerization; Z. Chen, Y. Zhang, B. Chisholm, D.C. Webster; Journal of Polymer Science Part A Polymer Chemistry 46 (13):4344-4351 (2008)
- Influence of actinic wavelength on properties of light-cured interpenetrating polymer networks; F. Karasu, C. Rocco, M. Lecompère, C. Croutxé-Barghorn, X. Allonas, Y. Zhang, A.C.C. Esteves, L. G. J. van der Ven, R. A. T. M. van Benthem, G. de With; J. Polym. Sci. : Part A : Polym. Chem., 54, 1378-90 (2016)
- Photopolymerization of oxetane based systems; M. Sangermano, G. Maluceeli, R. Bongiovanni, A. Priola; European Polymer Journal 40, 353-358 (2004)
- Cationic UV Cure on Polyolefins; D. James, P. Appelkvist, E. Gustavssson; Conference proceeding from RadTech Europe (2005)
- Synthesis and Characterization of a Hyperbranched Polyol with Long Flexible Chains and Its Application in Cationic UV Curing; X. Hong, Q. Chen, Y. Zhang, G. Liu; Journal of Applied Polymer Science, Vol. 77, 1353-1356 (2000)
- Cationic UV-Curing: Technology and Applications; M. Sangermano, N. Razza, J. Crivello; Macromol. Mater. Eng. (2014), 299, 775-793
- Investigations of the Reactivity of “Kick-Started” Oxetanes in Photoinitiated Cationic Polymerization; J.V. Crivello; Journal of Polymer Science, Part A: Polymer Chemistry 2015, 53, 586-293
- Influence of photoinitiator content on phase separation and microstructure of free-radical/cationic hybrid system and its application for low-gloss UV-curable coatings; I. Calvez, C. Szczepanski, V. Landry; Conference proceeding from European Coatings Conference (2021)
- Photo-curing 3D printing technique and its challenges; H. Quan, T. Zhang, H. Xu, S. Luo, J. Nie, X. Zhu; Bioactive Materials 5 (2020) 110-115
- Photopolymerization in 3D Printing; A. Bagheri, J. Jin; ACS Appl. Polym. Mater. 2019, 1, 593-611
- Cationic UV-Curing of Epoxidized Biobased Resins; C. Noè, M. Hakkarainen, M. Sangermano; Polymers 2021, 13, 89.