By Hossein Riazi and K. Michael Peck, Evonik Corporation, USA
Achieving a matte finish in 100% solids energy-curable coatings can be a challenge. Viscosity increases with traditional particle matting agents, and minimal film shrinkage of the binder creates hurdles in efficiently building a suitable matte surface structure. In addition, getting a deep-matte finish in waterbased UV-curable coatings can be challenging as appropriate selection of a matting agent is crucial. This article will discuss the fundamentals of matting agent technology even in low shrinkage systems and explore techniques to optimize performance and achieve the desired finish in UV wood coatings. In addition to 100% solid system, matting mechanism in waterbased UV-curable coatings was investigated to compare the performance of a matting particle in different UV technologies.
Introduction
The use of particles to reduce the gloss of coatings is a well-known practice, with a wide variety of products and technologies available to develop matte wood coating formulations. The use and choice of a specific product often is driven by a variety of factors, but fundamentally, all particle technologies function through a similar mechanism. The particles dispersed in the liquid coating provide a surface roughness after application and drying/curing that serves to scatter light, providing a visual differentiation and reduction in gloss. The effectiveness of the particles is heavily contingent on film shrinkage around them during the drying and curing of the coating, and their utility often is judged based on secondary effects to the coating film, such as rheology, clarity, haptic properties, chemical resistance and resistance to burnish. 1
Deep-matte coatings, where the gloss has been reduced significantly, typically require higher loadings of particles to achieve the necessary surface roughness. These higher loadings often result in greater impact on the secondary effects to the coating film and require far more attention to product selection and formulation to balance the performance needs of the coating. Of particular interest is the aspect of burnish resistance – the increase in gloss caused by the polishing of the finished coating by handling, touching, brushing or other physical contact. Burnishing and reduction of the matting effect can be an issue with all matted coatings but is particularly problematic with deep-matte coatings, as the visual differentiation can be significant. Burnish resistance of a deep-matte coating also is very dependent on the nature and chemistry of the particles themselves, due to the higher concentration needed on the coating surface to achieve the necessary surface roughness. The morphology of the particles, chemical and physical properties, and interaction with the coating film can play a pronounced role in resistance to burnish and is an area of significant interest.
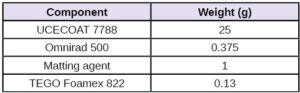
In this work, matting agents for achieving a deep matte-finish with high resistance to burnishing were investigated. While only a snapshot of the broader investigation is reviewed here, the best-in-class products were evaluated in waterbased and 100% solid UV-curable systems, and the results are compared and assessed. Matting agent combinations also are explored, and results suggest synergistic benefits are possible when pairing silica matting agents with organic particles. In addition, results show that matting agent blending is an effective method for adjusting the viscosity of a formulation and improving the clarity of a cured coating.
Waterbased UV-Curable System
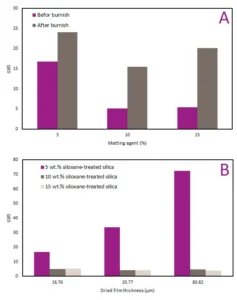
Achieving a deep-matte sheen with a waterbased system is less challenging than with 100% solid UV systems because water evaporation facilitates film shrinkage and increased surface roughness. Selection of a suitable matting agent is expected to be straightforward. In this context, a suitable matting agent is one that has compatibility with the binder. For example, Table 1 shows a formulation in which a treated silica matting agent with an average particle size of 10 microns is used in a UV-curable waterbased aliphatic polyurethane dispersion based on UCECOAT® 7788 (Allnex) binder with a defoamer, TEGO® Foamex 822 (Evonik) and a water soluble photoinitiator, Omnirad 500 (IGM Resins). Three different matting agent loading levels (5 wt.%, 10 wt.% and 15 wt.% of the dry film) were tested. Excellent results in terms of gloss reduction and burnish resistance were obtained, showing a clear relationship between use level and performance. Optimal performance appears to be achieved when approximately 10 wt.% of the matting agent was used. The results for gloss and burnish resistance at the different loading levels are seen in Figure 1-A. The chart shows that 85° gloss after burnish testing is lower for the sample containing 10 wt.% matting agent. Thus, 10 wt.% was selected as the optimum matting agent concentration and coating characterization was conducted at this concentration. In addition, one can conclude that adding more matting agent does not necessary lead to more gloss reduction. In addition to the loading level of the matting agent, film thickness affects the gloss value of the waterbased UV-curable coating. For the sample containing 5 wt.% of the matting agent, significant gloss increase with film thickness is observed. However, gloss is almost constant in a wide range of thicknesses when the loading level of silica is 10 wt.% or 15 wt.%, with respect to dried film. It may be the case that, at higher matting agent concentrations, the coating surface is saturated enough with the silica particles even at a film thickness up to 84 microns. Thus, regardless of film thickness, there are always enough particles on the surface to develop surface roughness and a deep-matte sheen. Figure 1-B shows that adding 10 wt.% of a siloxane-treated silica is enough to get a deep-matte sheen across the wide range of film thicknesses.
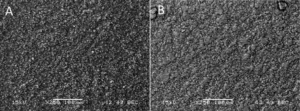
Figure 2 shows SEM microscopy of the surface of the sample containing 10 wt.% siloxane-treated silica and provides a visual comparison of the results shown in Figure 1. The images show the surface roughness created by the matting agent and how the surface remains largely intact even after a burnish test. Limited deformation of the particles and little surface flattening are observed, and it is not extensive enough to change the sheen of the coating significantly. Quantitatively, deep-matte sheen is defined as 0<G60<10 and 0<G85<15.2 In this case, G85 increased from 5 to 15 which means the coating still is in the deep-matte sheen range even after burnish testing.
Although the siloxane-treated silica effectively reduces gloss and shows high burnish resistance, at this high loading level needed to achieve deep matte some negative effects are seen on some secondary properties. One example is the clarity of the coating, which is impacted by the addition of matting agent to the system. Haze and loss of clarity are common problems with particle matting agents. Alternative product selection can help, but balancing effectiveness can be challenging. Particle combinations are a known approach to balance properties, and, if clarity is an important factor, using particle combinations may help to fine tune performance.
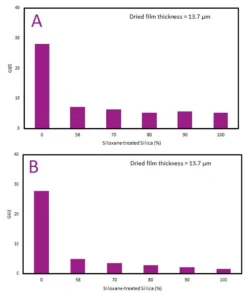
In this specific waterborne UV-curable formulation, the matting effect of the silica is far greater than that of the organic particles. Figure 3 shows six different samples at a 10% total matting agent level across a range of mixture ratio of silica and the organic particle. Figure 3 shows that both 85° and 60° gloss values decrease as the amount of the siloxane-treated silica increases in the system. The same trend is visually observed in surface SEM pictures. The surface roughness decreases by increasing the amount of the polyamide particles in the silica/polyamide matting mixture. As Figure 3 shows, G60 and G85 sharply decrease by increasing the silica content from 0 to 60 wt.%. However, the extent of the change beyond this concentration is not very significant. At the same time, the clarity of the coating using the 60/40 ratio of the silica/polyamide is higher than that using the 100/0 ratio. This means that, by appropriately selecting a ratio of the siloxane-treated silica to the polyamide, a coating that has both low gloss and high clarity can be produced. In other words, the particle blending technique is a viable approach for adjusting secondary properties when trying to decrease the gloss of a coating.
This system was achieving high performance without the need to combine particles, but the work demonstrates the potential improvements and directions that can be achieved. More critical and difficult formulations, such as 100% UV formulations, are of significant interest to understand the function and benefits of particle combinations.
100% Solid UV-Curable Coating
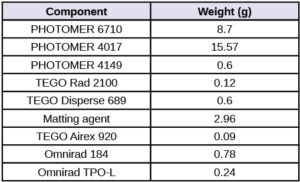
Achieving a deep-matte sheen in 100% solid systems is more challenging than waterborne UV-curable systems, as there is no film shrinkage due to solvent evaporation. To compensate for the lack of solvent evaporation other techniques can be used to provide some film shrinkage during cure but ultimately higher amounts of matting agents often are required. This, however, can lead to problems, particularly a viscosity increase in the formulation. Specialty treated matting agents optimized for UV systems are available and the silica used in this system differs from that in the waterborne work. Here, an acrylate-treated silica which has an average particle size of 5 μm that is specifically designed for 100% solid systems was selected as the benchmark. Table 2 shows the formulation of the 100% solid system used for the evaluation based on PHOTOMER® (IGM Resins) oligomers and monomers and various additives, while Figure 4 shows the viscosity reduction of the formulation that can be achieved by switching from siloxane-treated silica to its acrylate-treated counterpart.
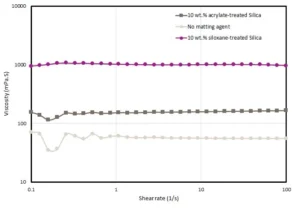
Coatings developed according to Table 2, where the formulation contains 10 wt.% of the matting agent, do not lead to a deep-matte sheen. Increasing the loading level to 15 wt.% is possible in case of the acrylate-treated silica but 15 wt.% of the siloxane-treated silica turns the formulation into a paste. The problem, however, is that even using 15 wt.% of the acrylate-treated silica does not provide a deep-matte sheen. 20°, 60°, and 85° Gloss values of 1, 8, and 69, respectively, were obtained for the coating containing 15 wt.% of the acrylate-treated silica. On the same substrate, those gloss values for the pristine coating without any matting agent were 63, 87 and 92. Comparing these values reveals that the silica particles are effective in gloss reduction at 20° and 60°; however, limited efficiency in gloss reduction at 85° was seen. According to the industry standard2, a deep matte sheen is defined as 0<G60<10 and 0<G85<15. So, it is not feasible to get a deep-matte sheen in this system even by using 15 wt.% of the acrylate-treated silica particles.
In Part 2, the authors will show that in 100% solid UV-curable coatings, film thickness is a key parameter determining the sheen of a coating.
References
- ACEMATT Matting agents for the coatings industry, Technical Overview, Evonik Industries
- The ingredients of paint and their impact on paint properties, The Rohm and Hass, Paint Quality Institute