By Michel Tielemans, Guido Vanmeulder, Johan Van den Hauwe, Cédric d’Hulst and Michela Fusco, allnex Belgium
Decades ago, allnex pioneered sustainable coating technologies as a foundation for current waterborne, energy-curable, powder and crosslinker product ranges. Gradually, water-based and energy-curable products were merged with the development of novel energy-curable polyurethane dispersions (UVPUD), which combine the benefits of their parent technologies to boost performance and ecology to the next level of requirements. They constitute the fastest-growing product range in the wood coatings market today.
In order to recognize the sustainable attributes of this product range, we must consider three dimensions inspired by Life Cycle Analysis (1).
Composition. Products largely respond to environmental regulations due to their waterborne nature and low level of volatile organic compounds (VOCs). They can make use of renewable feedstock and safe raw materials – banning tin catalyst, volatile organic amines and alkoxylated alkyl phenol emulsifiers.
Performance-in-use. Products demonstrate low viscosity and are easily sprayable. Their minimum film formation temperature (MFFT) is low and does not require the use of additional coalescent materials, increasing air emissions. They keep the high productivity of instantaneous energy curing supported by new developments in low-energy UV-LED lamps.
Lifetime and disposal. Products obtained after curing are characterized by a dense but flexible crosslinking network, resulting in superior substrate protection. They match outdoor applications, where light-fastness and weatherability become essential for durability. Recyclability and biodegradability can further reduce their environmental impact.
Introduction
Fossil resources decreased during the extensive industrialization in recent human history. The estimated reserves are expected to last 30 to 50 years, so their prices will start climbing as they rarify. The primary goal of the industry is to address survival scenarios and to facilitate a new world economy compatible with human wellness. This is imposing a slow but drastic change in the industry, one that we already comprehend with circular economy initiatives.
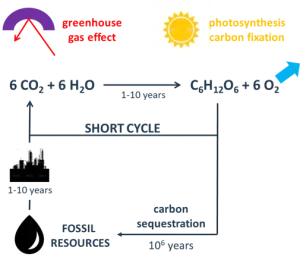
Displacing fossil with renewable carbon feedstock to manufacture new bio-materials is fundamental to this transition. It is particularly relevant when paired with a substrate that is already a bio-material – natural (wood, leather, textile) or synthetic (plastic). This also immediately improves our environmental footprint by reducing the material carbon footprint as a fundamental value proposition for renewable coatings today. Of paramount concern is the massive release of greenhouse gas (such as CO2) in the atmosphere due to human activity. This is resulting in a slow but perceptible rise of the earth’s temperature, affecting life on this planet. There is a strong imbalance in the fossil carbon cycle, considering the rapid transformation of fossil carbon into CO2 (1 to 10 years) and the very slow fixation of this CO2 into fossil carbon (≈106 years). The use of renewable carbon addresses this cycle imbalance with a neutral carbon footprint proposition – considering that the CO2 released in the atmosphere is coming from the same quantity of CO2 fixed by plants during photosynthesis. It is depicted in Figure 1.
Measurement of renewable carbon content and eco-certification
Renewable materials are major components of our ecosphere. They are based on natural resources, which replenish quickly enough through natural biological processes and overcome depletion caused by intensive usage in a human lifetime scale.
The renewable carbon content of an organic material is defined by its weight percentage of the total weight of organic carbon in the material. Bio-based polymers can be certified for their renewable carbon content as a basis for reduced material carbon footprint. This certification is provided after C14 / C12 quantification in the product, according to the dedicated ASTM D6866 standard. It includes distinct test methodologies, but a popular method involves the controlled combustion of the test sample into CO2 and its subsequent catalytic transformation into carbon – that is then introduced in high-energy accelerated mass spectroscopy (AMS) capable of quantifying the two isotopes.
We can quantify the inherent material carbon footprint reduction from the measured renewable carbon content translated in CO2 emission savings (expressed in g/kg of dry product). Importantly, this value excludes the process carbon footprint and does not constitute a full life cycle analysis.
Independent label programs are usually adopted and include, for instance, the Technical Inspection Association (TUV) “OK bio-based” logo, the DIN CERTCO certification organization “Biobasiert Geprüft” logo and the US Department of Agriculture (USDA) “certified bio-based” logo.
In an effort to follow a bio-ethical vision to develop new renewable products, we seek to avoid interference with raw materials sourcing that is in direct competition with the human food chain.
Experimental
The polymer composition, architecture and morphology of ionomeric polyurethane dispersions encompass an extremely wide range of possibilities to target desired performance (2). Our approach was to consider the weighted impact of building blocks constituting the polymer and to address prioritized substitution from renewable feedstock. It sounds like an evidence that the use of bio-sourced acrylic acid is prevalent for an easy drop-in, but unfortunately, its cost-competitive availability is not expected within the next five years. The difficulty then is to stoichiometrically assemble bio-based polyurethane compositions with innovative bio-sourced molecules that preserve a high performance level (crosslinking density) together with possible additional benefits. Typically, raw materials with fixed renewable carbon content follow separate storage and manufacturing routes to guarantee the certification compliance.
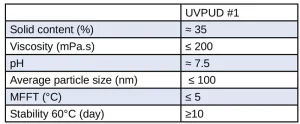
We developed a new green product with high-end performance suitable for clear and white-pigmented wood coatings. The product, referred to as UVPUD #1, has ~22% of bio-carbon content (ASTM D6866) resulting in the material carbon footprint reduction. The product is tin-free and APEO-free. It presents a good colloidal stability with a robust formulation and spray capability. It is physically drying (tack-free) before cure. The low minimum film formation temperature (MFFT) does not require additional co-solvents and dries easily, providing full performance level after energy-cure. The wet product characteristics are summarized in Table 1.
Drying and film formation
The drying efficiency of waterborne polymers is becoming a significant component of sustainability due to its energy impact. The film formation of polymer dispersions occurs in three distinct steps: (1) particles close contact, driven by water evaporation; (2) particles deform, driven by capillary forces; and (3) particles coalescence, driven by temperature – if above MFFT. Only a few protocols have been reported to accurately quantify the overall drying process. An example outside the academic world is the Adaptive Speckle Imaging Interferometry(3) (ASII) by FORMULACTION®, which is limited to ambient temperature.
The drying of a coating is practically governed by time in an oven under controlled conditions of temperature, humidity and air flow. The water release of energy-curable polymer dispersions is often judged by the residual water in the coating during the second and third steps of film formation. Entrapped water may create coating defects, such as undesirable whitening due to the optical anisotropy between the polymer and the numerous nanoclusters of water. The problem can be revealed and fixed for a prolonged period after energy curing. Thus, drying parameters need to be optimized for each product and substrate according to the wet coating thickness.
A novel Near Infrared (NIR) spectroscopy protocol has been developed to investigate the drying of the dispersions. The technique is robust because of its excellent sensitivity to water and its ability to look through the whole coating thickness during the drying operation without interaction with glass.
NIR spectroscopy is an analytical method based on the specific interaction between matter and radiated energy between 4,000 and 12,800 cm-1. The absorption occurring at a defined wavenumber is described by the Beer-Lambert law and provides information on the physico-chemical properties of the sample. It essentially shows overtones and combination bands of transitions between vibrational energy levels of molecules. An overtone is a transition from the ground state to any vibrational level higher than the first level, while a combination band is defined as the combination of two or more fundamental transitions seen as a single absorption at a lower energy than the overtone.
We used the MB-3600 Laboratory FT-NIR Analyser from ABB. The NIR source is a halogen lamp connected to a sample compartment fitted for dynamic transflection measurements and linked to an Indium Gallium Arsenide detector. The data treatment is ensured by a software, Horizon MBTM FT-NIR.
The UVPUD #1 was assessed for drying performance against an internal bio-based reference (REF #1) and an external bio-based benchmark (REF #2; 38% renewable carbon content). The products were formulated with 0.5% BYK® 346 (wetting agent) and 2% UCECOAT® 8460 (rheology modifier). In the case of REF #2, the product had to be formulated with additional Butyl Cellosolve (10%) because of the high MFFT of the dispersion (41°C).
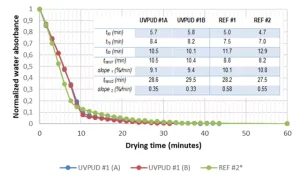
A coating was applied on a glass plate at a wet thickness of ≈200 microns using a stainless steel cylindrical film applicator. The initial spectrum was taken at room temperature by putting the freshly coated glass plate (face down) above the detector surface (fitted with four 2-mm-thick rubber pastilles to prevent contact) and covering it with an NIR-compliant golden mirror for transflection measurements. The coated glass plate was placed in the middle of a Binder FD-53 ventilated oven at 40°C. The coating was taken out after 60 seconds to fit the equipment and take the NIR spectrum (+20 seconds), before starting a new drying cycle (+10 seconds). The measurements were taken every time at the same place of the coated glass plate. The absorbance corresponding to water at 5153 cm-1 and first overtone at 6850 cm-1 were recorded and deducted from the baseline absorbance above 8000 cm-1. The first overtone was selected for its good linear response (no saturation) over the whole experimental water content range and was normalized according to the absorbance of acrylic double bonds at 6164 cm-1 as internal reference; it was normalized a second time based on the residual absorption of the organic background attributed to the absence of water. This resulting absorbance was plotted as a function of residence time at 40°C for two distinct experiments using UVPUD #1 (A/B) as well as for REF #1 and REF #2 (Figure 2).
It is possible to extract from the drying curves some interesting descriptors like the characteristic time required for reaching 50% to 75% to 90% of residual water (t50-75-90). It also is possible to deduct the transition time (ttrans1) attributed tentatively to the transition between the first and the second stage of film formation – corresponding to the strong inflection point in the drying curve. The same can be done for the transition time (ttrans2) between the second and the third stage of film formation – corresponding tentatively to the weak inflection point in the drying curve. These transition points could be obtained precisely by calculating the intercept point from a linear regression of the associated points. Finally, it is worth indicating that residual water (%) at the drying plateau is stable (no evolution after an additional three hours at 80°C).
Very good reproducibility is observed when duplicating the measurements for UVPUD #1 (A/B). All in all, the products show a comparable drying kinetic compatible with application lines, with some possible benefit for the UVPUD #1 during the second stage of film formation which is practically the most relevant for good water release (t90). The drying parameters from the table shed a useful fundamental light to the film formation that is not easily obtained with other techniques. At the end of the drying process, every product is physically drying (tack-free before cure).
Results and discussion
UVPUD #1 was designed to complement the high-performance product portfolio for wood coatings. The product and the two benchmarks were formulated for clear and white coatings according to the Table 2. They were applied on wood, glass, Leneta® or sanded melamine board (as a function of the test protocol) and cured at 5 m/min at 80 W/cm Ga and Hg lamps. The testing was always performed after one week at room temperature.
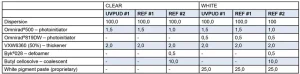
We looked at the Persoz hardness of formulated products in several curing conditions. The coatings were applied with a 120µ wet thickness on a glass plate and dried 10 minutes at 60°C (condition a), followed by 12 days at room temperature (condition b), and finally UV cured at 5 m/min under 80 W/cm Ga lamp and 120 W/cm Hg lamp (condition c). As a comparison, the coatings were similarly dried 10 minutes at 60°C immediately followed by UV curing at 5 m/min under 80 W/cm Ga lamp and 120 W/cm Hg lamp (condition d) and followed by 6 days at room temperature (condition e).
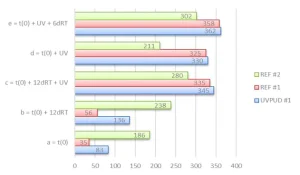
Figure 3 immediately shows a significant difference between UVPUD #1 and REF #1 in comparison with REF #2. The first two products present a low hardness after drying but reach their full hardness potential immediately after UV curing. (Hardness always increases somewhat after several days at room temperature.) The REF #2 immediately starts with a moderate hardness after drying, which increases more significantly after some days at room temperature; in that case, the UV curing does not immediately deliver the full hardness, but it always is required to get a good solvent resistance.
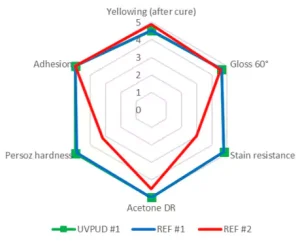
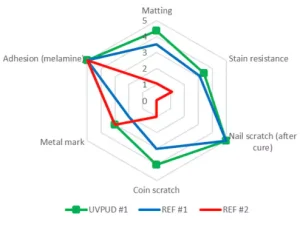
Figure 4 presents the comparative performance of the UVPUD #1 against the two benchmarks in clear formulation. Overall, the products present a balanced set of properties, comprising an excellent adhesion on wood with high gloss, good yellowing after cure and high hardness with superior chemical resistance. UVPUD #1 is close to the internal benchmark REF #1 but outperforms the external benchmark REF #2.
Figure 5 similarly presents the performance in white formulation. UVPUD #1 presents an optimized chemical, mechanical and metal mark resistance in comparison with the internal benchmark REF #1 and is always superior or equal to the external benchmark REF #2. It is worth mentioning that the matting of UVPUD #1 is much improved compared to REF #1 or REF #2 with some specific pigment pastes and that this “self-matting” may be found advantageous for some applications (no matting agents required).
Summary and conclusions
A novel bio-based, energy-curable polyurethane dispersion supported by clear technological differentiation builds on sustainable innovation.
UVPUD#1 (UCECOAT® 7999) contains more than 20% carbon from renewable feedstock (ASTM D6866) and significantly reduces its material carbon footprint.
The product has a low film formation temperature, requiring no co-solvent and provides immediate hardness after cure, along with excellent clear and white coating performance.
The drying kinetics of the coated product were studied using a novel NIR spectroscopy protocol capable of characterizing the film formation steps in a reproducible way.
Selected references
- Sustainable development of new water-based energy-curable PU dispersions for wood. M. Tielemans, G. Vanmeulder and M. Fusco. European Coating Journal 03-2019, 104-109.
- Multiphase coatings from complex radiation curable polyurethane dispersions. M. Tielemans, P. Roose, C. Ngo, R. Lazzaroni and P. Leclère. Progress in Organic Coatings 75 (2012), 560-568.
- Adaptive speckle imaging interferometry (ASII): New technology for advanced drying analysis of coatings. A. Brun, L. Brunel and P. Snabre. Surface Coatings International Part B: Coatings Transactions, September 2006, Volume 89, Issue 3, 251–254.
Michel Tielemans, an associate research fellow at allnex, is based in Drogenbos, Belgium. He occupied several technical and managerial positions in research and development, covering the development of waterborne acrylic and polyurethane polymers for the coating, adhesive and ink markets. He leads global development projects for novel waterborne radiation-curable polymers and supporting coating market segments. He is the author of numerous articles and holds a Ph.D. in organic chemistry from Brussels University.